Turning up the heat
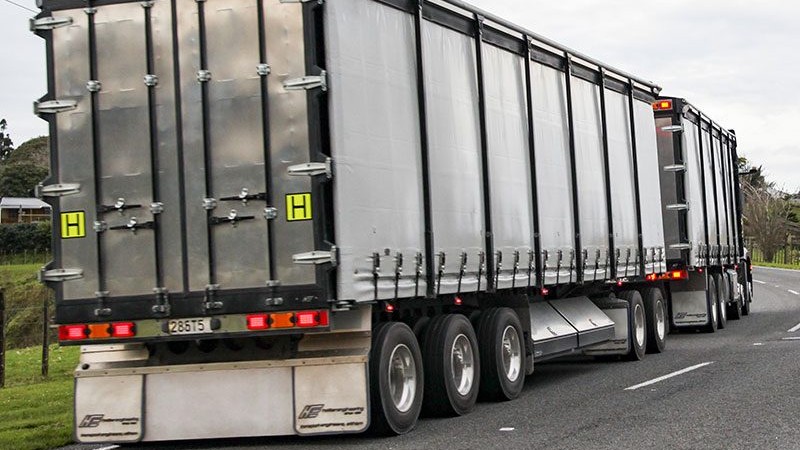
With a history steeped in product development and innovation, Russell Hotter and his Eltham-based business Hotter Engineering are no strangers to working at the sharp end of the industry. So, when the opportunity came across Russell’s desk to build a 22.88m, 80-tonne GCM tipping curtainsider nine-axle truck and trailer unit for Mike Fale, it was game on.
Hotter, a well-established general engineering company with a worldwide reputation for exporting rotary milking systems, was looking to diversify into transport engineering. It was a true opportunity to showcase its already well-honed, digitally driven production skills.
A new basket
“Transport engineering is quite new for us,” explains Russell Hotter, managing director. “We made the jump into the sector in 2018. Our game was rotary milking sheds. We were manufacturing them here in Eltham and sending them worldwide. It was Covid that screwed us – we lost our export market overnight; 90% of what we made all went overseas. We were sending a 40ft container out once a week. At one stage, we were the largest user of steel in Taranaki. When Covid hit, we had 27 platform projects on order. However, with all the global lockdowns, we only ever completed two out of 27.
“We realised before the pandemic that we had all our eggs in one basket, so we were already looking at diversifying. The opportunity to move into transport engineering arose because Bruce Nickel of Nickel Engineering just down the road in Normanby, was looking to move away from transport. Taranaki is a small place, especially South Taranaki, and I always had this unwritten rule that you do not stand on each other’s toes. Bruce was doing transport, so we didn’t go there – and vice versa, we did cowsheds, so Bruce stayed away from those. There was mutual respect; it worked really well.
“I went to see Bruce and said, ‘If you are not doing this anymore, do you mind if we do?’ and he said, ‘No, not at all – fill your boots. Good luck, it’s not as easy as it looks.’ And I have to agree with him now – currently, the margins just aren’t there, but it gave us a new direction and that was motivating.”
Pushing boundaries
On Mike’s project, Hotter Engineering worked alongside Chris Ward from TransTech Dynamics out of Dunedin. Chris was asked to jump on board and provide a design.
“We had worked with Chris before on other projects. He has an extensive knowledge of the industry and is extremely innovative with his ideas, pushing the boundaries to look for solutions,” Russell says of Chris. “I find our thinking is very similar – always looking to push the envelope in search of improvements and efficiencies.”
Russell continues: “All the years manufacturing rotary cowsheds, we were heavily involved in design and innovation, always seeking to perfect the products that we were exporting overseas by implementing new technologies and procedures. Our history with the production of rotary cowsheds meant working with CAD, and 3D digital modelling was commonplace.
“What was interesting was when the 3D digital model was sent through to us from Chris, our more recently employed transport engineering staff had never really worked off a 3D digital model. They had mostly worked with basic drawings or drawings from a certifier, and that is a completely different world to a 3D model from a designer.”
At first, Russell printed off about 40 different views of the model for the fabricators to envisage exactly what they were building. But eventually, they would instead go straight to Russell to bring up the model on screen. “The ability to hide different layers of the build so that you could see how various parts interfaced with each other made it so easy to understand. The ease of point-to-point measurements removed the guesswork. The boys were just blown away by how simple it was to use.”
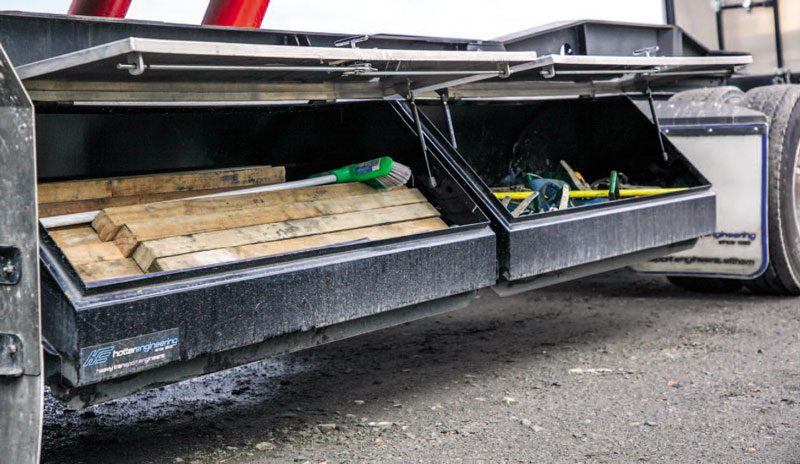
Efficient accuracy
Every part of Chris’ design (except the likes of bushes, etc) is formed from flat high- tensile Bisalloy steel, which is laser-cut and folded, with all the parts designed to tab into each other. This greatly speeds up the fabrication time. “In effect, you could build the entire chassis of the trailer without a tape measure – that is the magic of integrated design, where all the parts come together and, by design, perfectly align and lock into one another,” Russell comments.
This meticulous approach to fabrication also plays into the hands of another area of advanced engineering. “It was back in 2000 when we invested in our first robot welder. We learnt early on that self-jigging by design was the best way forward. The robot was our best quality-control guy on the factory floor; if it welded in the wrong place, it wasn’t the robot that was wrong, it was the material that was incorrectly located. So, getting our interlocking and self-jigging designs of items that needed welding spot on was critical. This way, the part could never be fitted incorrectly and meant perfect placement and connection every time.”
The ability to use the tools and technology at hand allows the team to design and configure rapid and 3D prototyping, which quickly presents accurate answers, says Russell. “Accurate answers are where you find efficiencies.”
Russell is proud that the whole build for MC Fale Transport, including fabrication, blast and paint, assembly, hydraulics and electrics was completed in house. The build is a true example of using technology and automation within transport engineering to take accuracy, fit and finish to the next level. The trailer and body for Mike’s build are a complex design. However, using technology the way the team at Hotter Engineering has, made it extremely easy to put together.
“It literally clicked into place,” says Russell. “When the wheel-alignment contractor scanned his lasers over the unit, the most extreme misalignment on any of the axles was only 0.4°. His tolerance is 2°.”
You couldn’t ask for much more than that in a build, and it’s fair to say that the Hotter Engineering team’s fresh thinking and technology-based approach to transport engineering will definitely turn the thermostat up a notch within the industry.