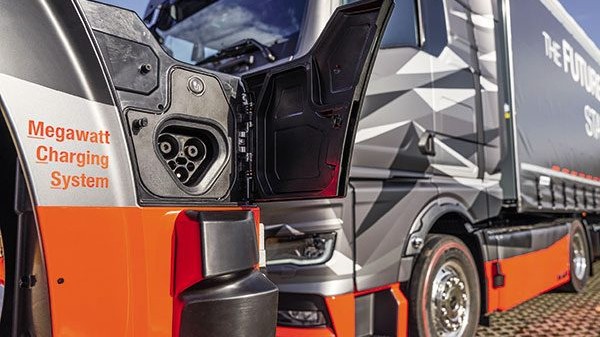
We have seen the MAN eTruck and the battery that powers it. The elephant in the global room of battery electric mobility is, however, charging. Assuming regulators can get us the power, here’s how MAN – and its peers – plan on getting it to their trucks.
We are on the frontier of history in terms of alternative propulsion, awoken from our complacent and convenient fossil fuel slumber by the need to reduce carbon, and carbon dioxide emissions. A propulsive force that’s given us vast levels of scalability and flexibility, we’ve built an entire civilisation around internal combustion. It’s not surprising then, that its more constrained alternatives are causing a complete reinvention of how we move both ourselves and the things we need moved.
In the alternatively fuelled world, one of the key gaps is refuelling time. Yes, we will get better and faster, but for now the rethink has penetrated to the core of the supply chain to maintain the required DIFOTIS (Delivered In Full On Time In Spec), and find blocks of time to patiently replenish batteries.
Notwithstanding charge-in-motion technologies, for BEV, the answer currently is bigger, faster, gruntier chargers in the form of Megawatt Charging Systems (MCS). The delicate balance here is speed, stress on the battery and heat (read into that noise) and, of course, the safety.
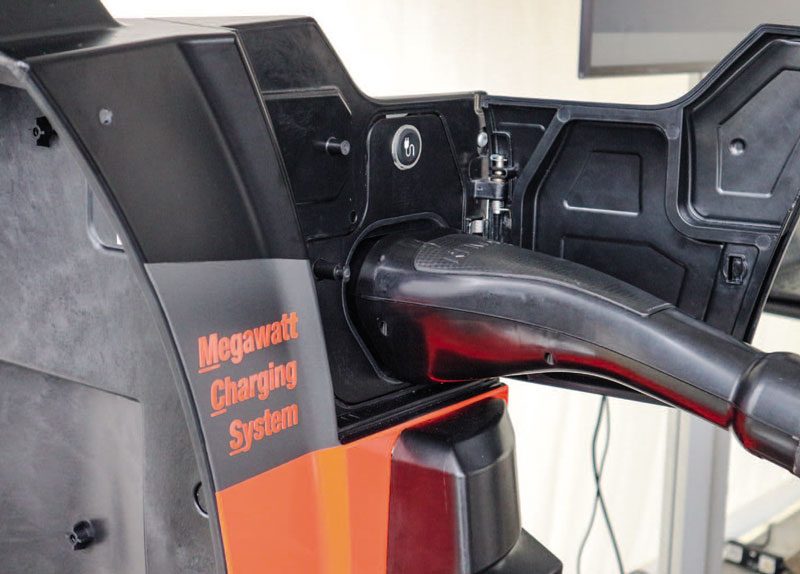
At MAN’s eTruck drive day and media event in Munich late last year, we were given a fascinating insight on Megawatt Charging. Bernd Hofmann, systems engineer for MCS Truck System Development at MAN, hosted the MCS module.
“There’s variation in charging standards around the world; the current (whether AC or DC), safety mechanisms and communication protocols. There are fundamental issues that have needed addressing. For instance, who does the conversion from AC to DC? Is it the vehicle or the charging station? OEMs are reluctant to add any more weight to the vehicles.
“MAN and Traton are actively involved in the current industry group CHARIN, working through the creation of a holistic MCS standard. The work is due to be completed in 2024 synchronising with eTruck’s release to market.”
Hofmann said any standard needed to have redundancy built in for the future. Currently 800kW is as high as is used, but we’re looking at something that will be able to serve 3.75MW, 3000 Amp, and 1250V. “We’ve had 3000 Amp units operating in test.”
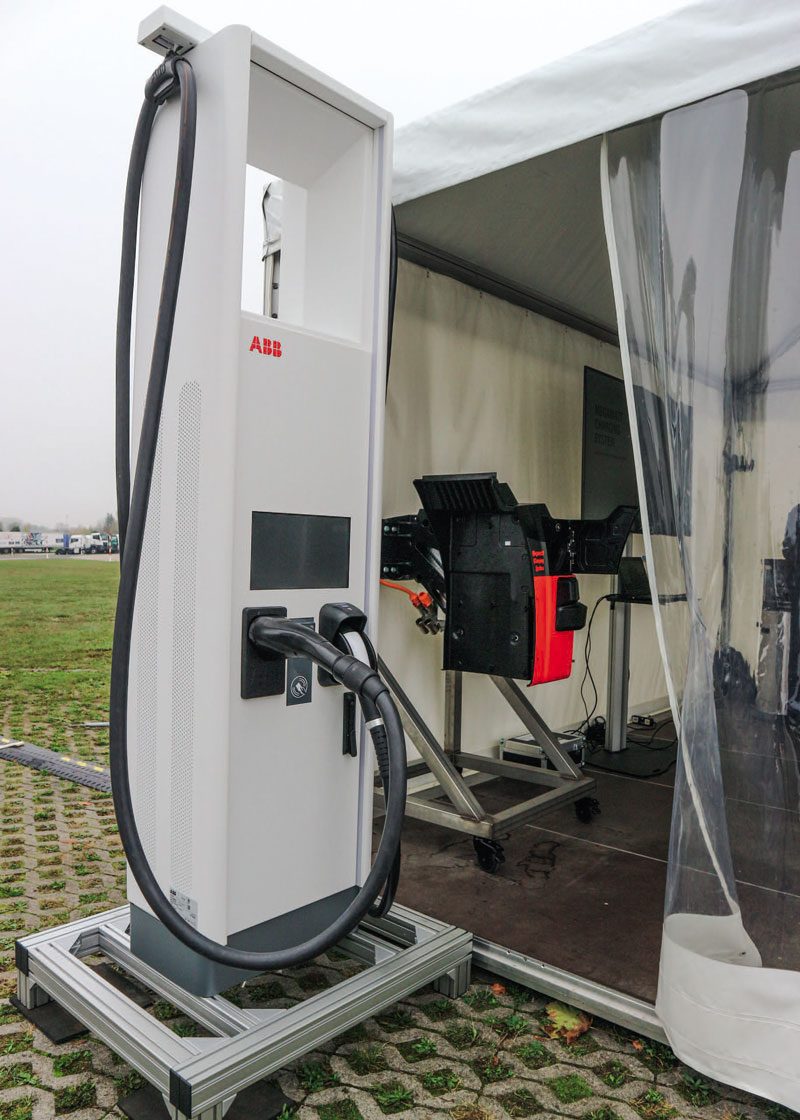
With those numbers safety becomes a key priority, as does dissipating heat. OEMs are reaching agreement on the unified placement of contact points on trucks to facilitate automatic connection in the future. This has the added benefits of streamlined component manufacture as well as helping to standardise charging station construction.
Significant work is also being undertaken on cooling fan noise in both the charging station and the vehicle while the charging process is active.
“We don’t want to incur the anger of the communities with vehicles charging in the early mornings, for instance. We have to keep noise under control.”
And the heat issue is no small matter. Every doubling of current results in a four-fold increase in loss in the form of heat. The total heat to be dissipated at the truck is about 30kW at 1000Amp, and to put that into perspective the average “wood oven” (the term quoted by Hofmann) is 7–10kW. Hofman said the batteries themselves also played a significant role, with cooling capacity per cell at around 15–20W, and the balance facilitated via the truck’s own systems. Demonstration rig showing the plug-in point on the truck.
The good news is we do have a starting point, and in some ways, the ‘wheel’ has already been partially invented. We just need a bigger and better ‘wheel’.
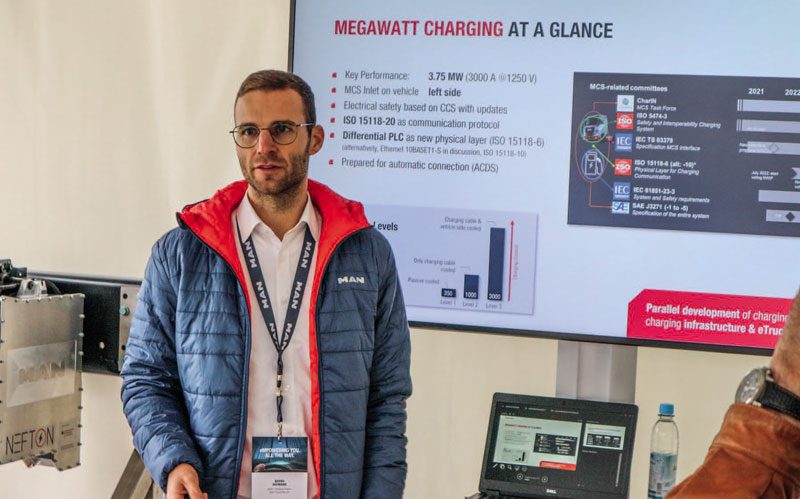
“The Combined Charging System (CCS) standard has been a safe, reliable, and robust one in the lighter capacity charging environment.”
While it gives a great starting point, there are key issues that need addressing:
• The communication protocols need more protection from the increased artifact and electrical fields generated. The level of protection built into the CCS will not be adequate for MCS.
• Data security. The intention here is no human interface and all the necessary handshake gateways – including payment – to occur automatically at connect and disconnect.
• Batteries can create incredibly high short circuit currents. Hofmann said consideration needed to be given to fuse structure and the charging path, and that semiconductors might even be the ultimate solution.
• The physical cables will need to be bigger and more robust, meaning heavier and less flexible. Currently a CCS cable is about 1.14kg/m, and a 1000W MCS cable would be 1.77kg/m. Copper buzz- bars are being investigated as replacements for future large capacity charges.
In terms of human safety beyond the interactive elements, Hofman said that in the DC space, the challenges were more mechanical as there were not the issues around electrical fields. Otherwise, there were existing stringent protocols around electrical fields that must be met when designing and manufacturing such equipment, including the provision of safe areas.
“You can’t change physics,” said Hoffmann. “The faster you charge, you’ll always incur an ageing on the batteries. It’s a trade-off between cost, life, stability and performance.”
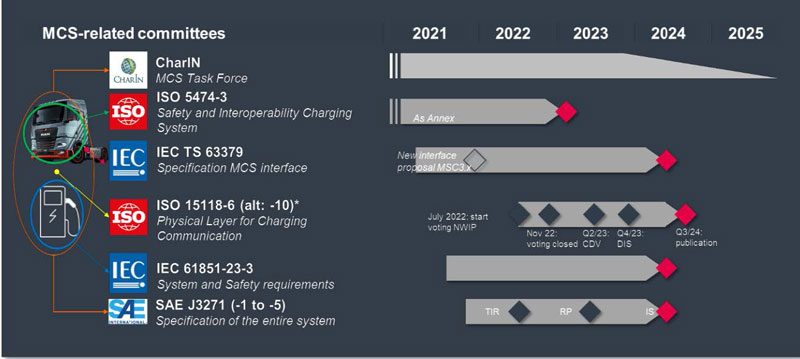
Infrastructure
While this is a European perspective, many issues under the microscope appear to be replicated globally. OEMs are producing the product, but will they be of any use?
Hofmann said Europe currently accounted for about 10% of total global electricity consumption. By 2030, he said there was predicted to be 270,000 BEV trucks requiring a regular and reliable charging network in Europe.
MCS will not be needed every time a truck charges. Currently 35% of all truck stopping events last eight hours or more. When laid over, they can be charged at slower rates using traditional CCS. Charging can also be planned into driver breaks and the rate of charge optimised to that. However, autonomous vehicles will increase the need for speed and capacity as they will only be stopping to charge. Any time over the minimum required will be productivity lost.
Additionally, the spread of charging points will not be even throughout Europe.
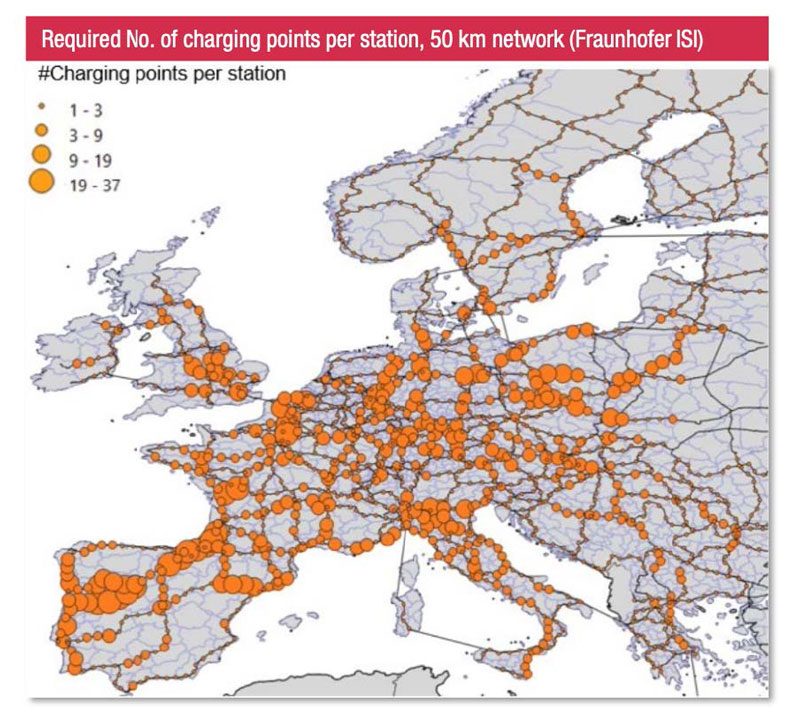
The relationship between the grid and users will need to become more of a dynamic relationship, and Hofman said MAN’s eTruck contributed to this via dynamic control of how much power the truck took from external sources, bi-directional and grid-friendly charging, as well as power scheduling capabilities.
As we know, Traton, Daimler, and Volvo have the Milence joint venture, a network of 1700 high-capacity chargers over the next five years at a cost of €500 million. As impressive as it sounds, both Hofman, and Andreas Gorman at the Daimler roundtable in Hanover the month before, said it was only a drop in the ocean and the key to the future was in the hands of central law makers and regulators.
Read more
Road to Zero Isuzu styles
0 Comments6 Minutes
Ready for the harvest
0 Comments12 Minutes
VGA introduces electric
0 Comments8 Minutes
Celling’ the future
0 Comments14 Minutes