Technology Maintenance Safety Conference 2024
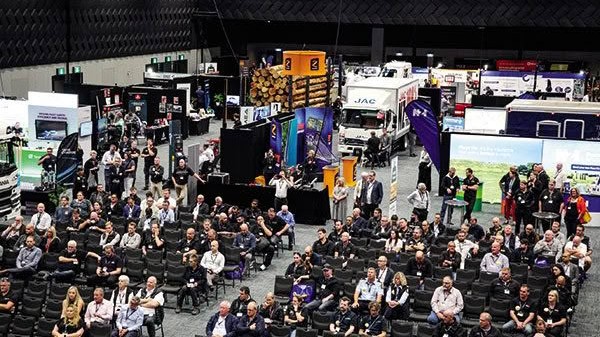
The Teletrac Navman Technology Maintenance Safety Conference and Exhibition was held at Te Pae Christchurch on 13 and 14 March and promised a refreshed format to the usual standard of conferences and exhibitions. Organised by the New Zealand Trucking and National Road Carriers associations, it was designed to engage delegates and inspire conversation with more than 50 exhibitors and eight conference sessions.
Improving Productivity – Roading and permitting
Peter Brown, national manager – maintenance and operations, at Waka Kotahi NZTA, gave delegates good news: the agency has money to spend on roads and a plan for the future.
“The current state-highway network is generously described as fragile. Significantly, there has been underinvestment in rehabilitation and resurfacing of our state highway network over the past decade.”
Brown said that while cars consume road capacity, trucks consume the asset. One 10-tonne axle is equal to 10,000 cars.
“If we accept a greater freight task and heavier freight loads that will consume the roads faster, we have to strengthen the state highway network, focus on drainage, because water is not our friend, and use treatments such as deeper pavements instead of chipseal, foam bitumen (three times the cost of chip), and structural asphalt (four times the cost).”
Brown outlines the task. “Over the next 10 years, we need an increasing programme of maintenance renewal. We have to stay in the available funding envelope provided by the National Land Transport Fund, and that’s to return the network to an acceptable level of service, comparable to what it was like in 2014. How? The first step is the draft Government Policy Statement that says the government intends to reform the system through a national infrastructure agency, which will take a 30-year view, reform how we fund transport infrastructure and have a 10-year investment plan and funding pipeline, which is really important.
“The part of the draft GPS that really spins my wheels is ‘maintenance and resilience’, focusing on resealing, rehabilitation and drainage over the next 10 years. The government is signalling to NZTA to take a more proactive approach. The targets set expect 2% of the network to be rehabilitated per year. Currently we achieve 0.7% of the network.”
Brown says NZTA is looking at a new maintenance delivery model that will give it more say in what’s delivered by providing contractors with a blueprint for what it wants, and also looking at Tier 2 and Tier 3 regional providers to grow the capacity. “We will take control of the asset management – we own it.”
He said catalogued designs that can be modified depending on location, instead of individualised designs per site, will be used. “That requires NZTA to take more risk, but it’ll be more efficient to get the process moving and contractors delivering on the volume of improvement needed,” he said.
“Over the last decade, we’ve been guilty of patching up what we can afford at the time – which is not efficient or effective. We’re going to have longer and more secure planning cycles, 10-year pipelines for funding. It will require significant upfront cost and we need to shift thinking to whole-of-life costs; over time, it’ll mean a lower maintenance cost over the life of the network – and less disruption.
“We’re on the way.”
Brown was joined by Geoff Taylor, regulatory manager at Waka Kotahi NZTA, who spoke about oversight and permitting.
He said an increase in applications for 54-tonne HPMV permits indicated people are stretching existing gear to improve capacity across the sector.
He said the agency is:
- Working on ways to do compliance checking as part of renewals of higher mass permits more efficiently to reduce the admin burden on operators.
The agency has:
- Removed attribute sheets for overlength, 50MAX and HPMV.
- Applications for high-mass permits can now be done on the VIN, shortening the time for a vehicle to hit the road.
- Extended the number of combinations to 10 per application, initially with 50MAX.
- Agreed on policy for over-width loads on HPMV, responding to industry concerns.
The agency will:
• Canvas industry groups about extending the validity of permits across the board for HPMV and 50MAX.
• Roll out a centralised permitting system by mid-year.
Navigating a Slowing Economy – Understanding your business costs
Addressing the challenges of a slowing economy, James Smith, GM Policy & Advocacy, National Road Carriers, and David Boyce, CEO New Zealand Trucking Association, discussed the importance of understanding business costs and the advantages of cost modelling. They were joined by Gareth Kiernan, chief forecaster at Infometrics, who talks about the Customisable Cost Index.
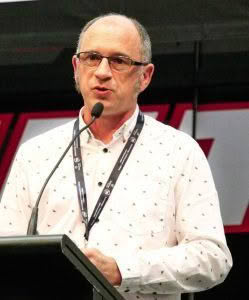
Infometrics worked with National Road Carriers to identify the main costs that go into a transport business. Kiernan said the problem is that each of those costs moves very differently.
“You look at the variation in fuel, for example, and you’ll know that it goes up and down, all over the place, from any one month to the next. Diesel prices have gone up on average by 28% a year,” he said. “Yet on the other end of the spectrum, you’ve got RUC, which hasn’t changed since 2020. It’s been up and down, and now it’s back at that pre-Covid level. Costs such as labour and other overheads have risen more rapidly than we’ve seen in the past, but still nothing compared to fuel.”
Kiernan said the Customisable Cost Index enabled businesses to identify proportions of each different cost and how they fed into the overall cost structure.
“You can then use that with the index, which is available online, to see how costs have changed for your specific business.” Kiernan then discussed where costs may go over the next 12 months.
“Market forecasts suggest that diesel prices should gradually drift down. But there are risks around that – world events can impact international shipping costs, and there’s the availability of oil coming out of the Middle East,” he said.
Kiernan said it was certainly not a done deal in terms of interest rates. “It could be some time before interest rates start to be cut by the bank. Our view is that probably from August this year, interest rates could start to be cut, but it may be a little bit longer than that before it comes through.”
The current unemployment rate of 4% was an improvement from a business point of view in terms of the availability and supply of labour, Kiernan says. “Some of those critical staff and skill shortages, which businesses were screaming out about through 2022, have become much less acute, and we are expecting to see that feed through into less wage inflation and less pressure on labour costs.
“The other point to bear in mind around the labour market is that we’ve had really strong net migration through 2023, and the rate of job creation is not keeping pace with the number of people coming into the country now. So that suggests that this sort of pressure will continue to ease. Add in the fact that the new government is lifting the minimum wage at a much slower rate than the previous government, which will take some of the pressure off at the lower end of the market.”
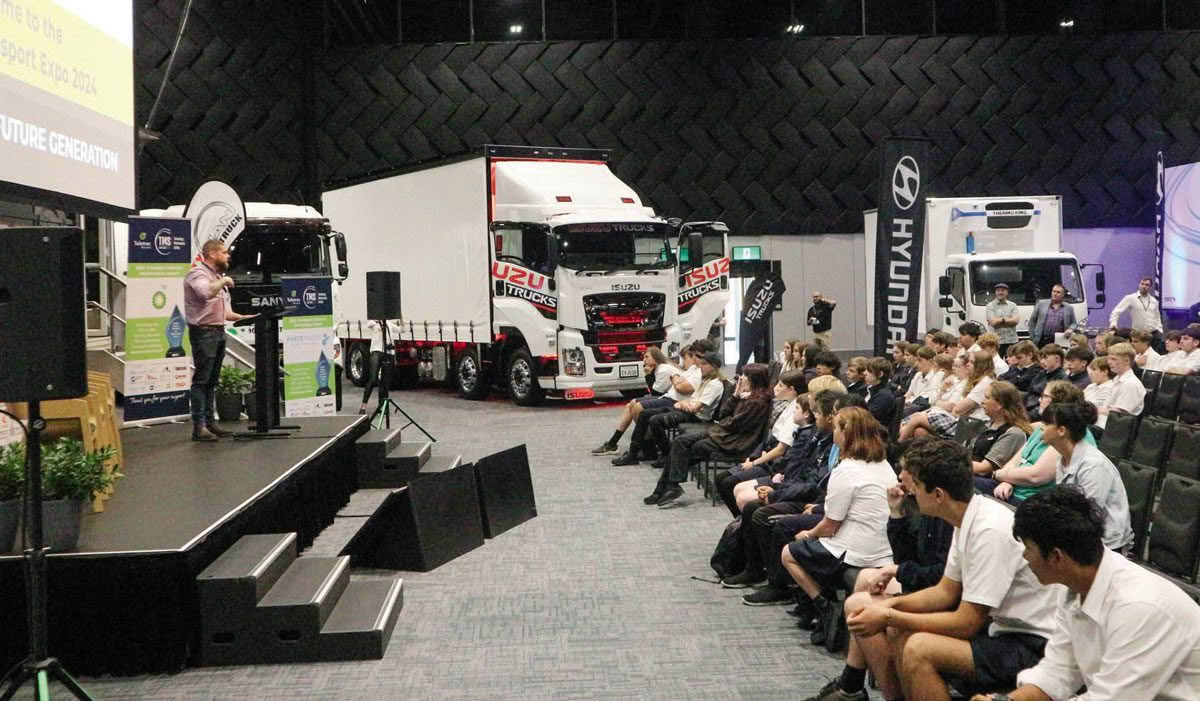
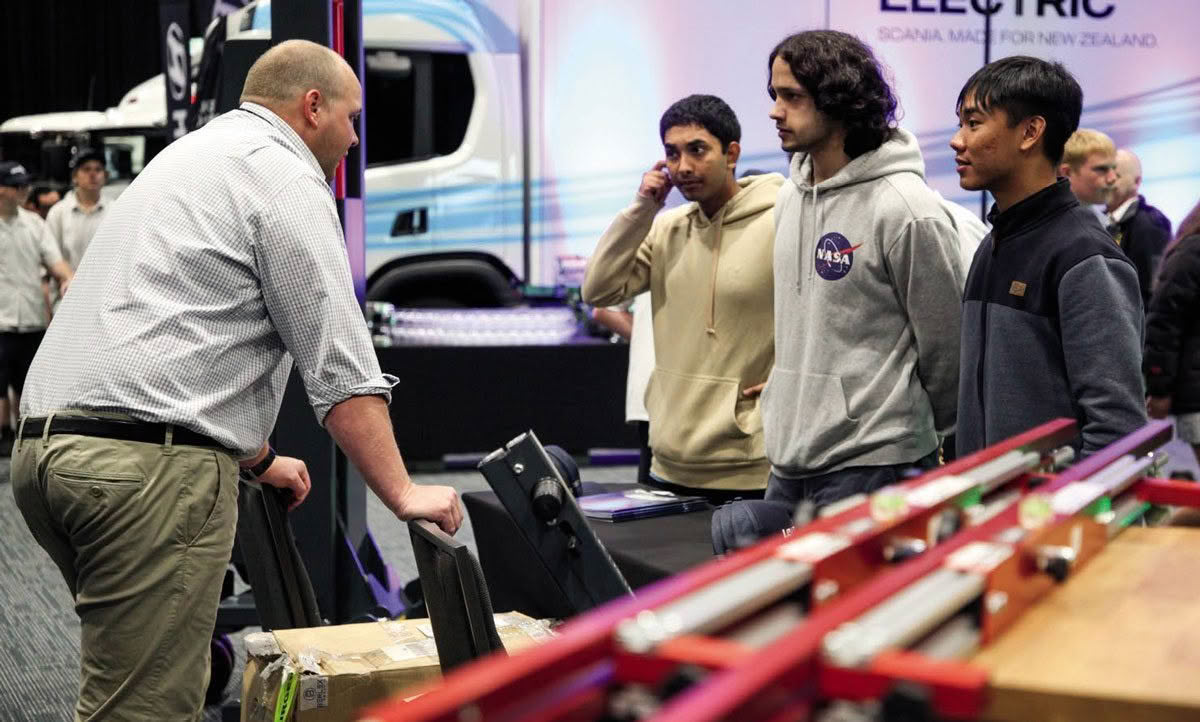
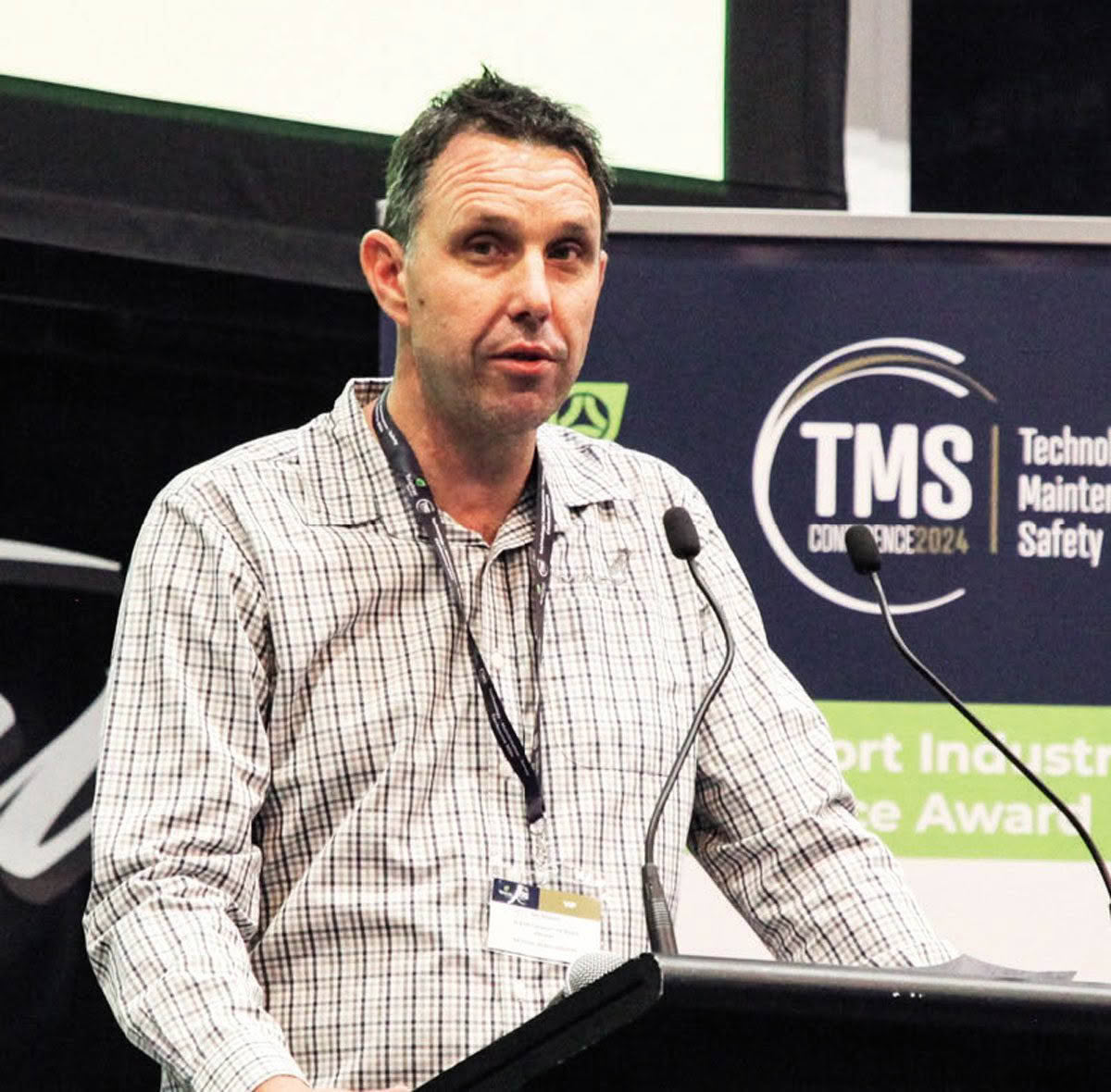
Ian Newey.
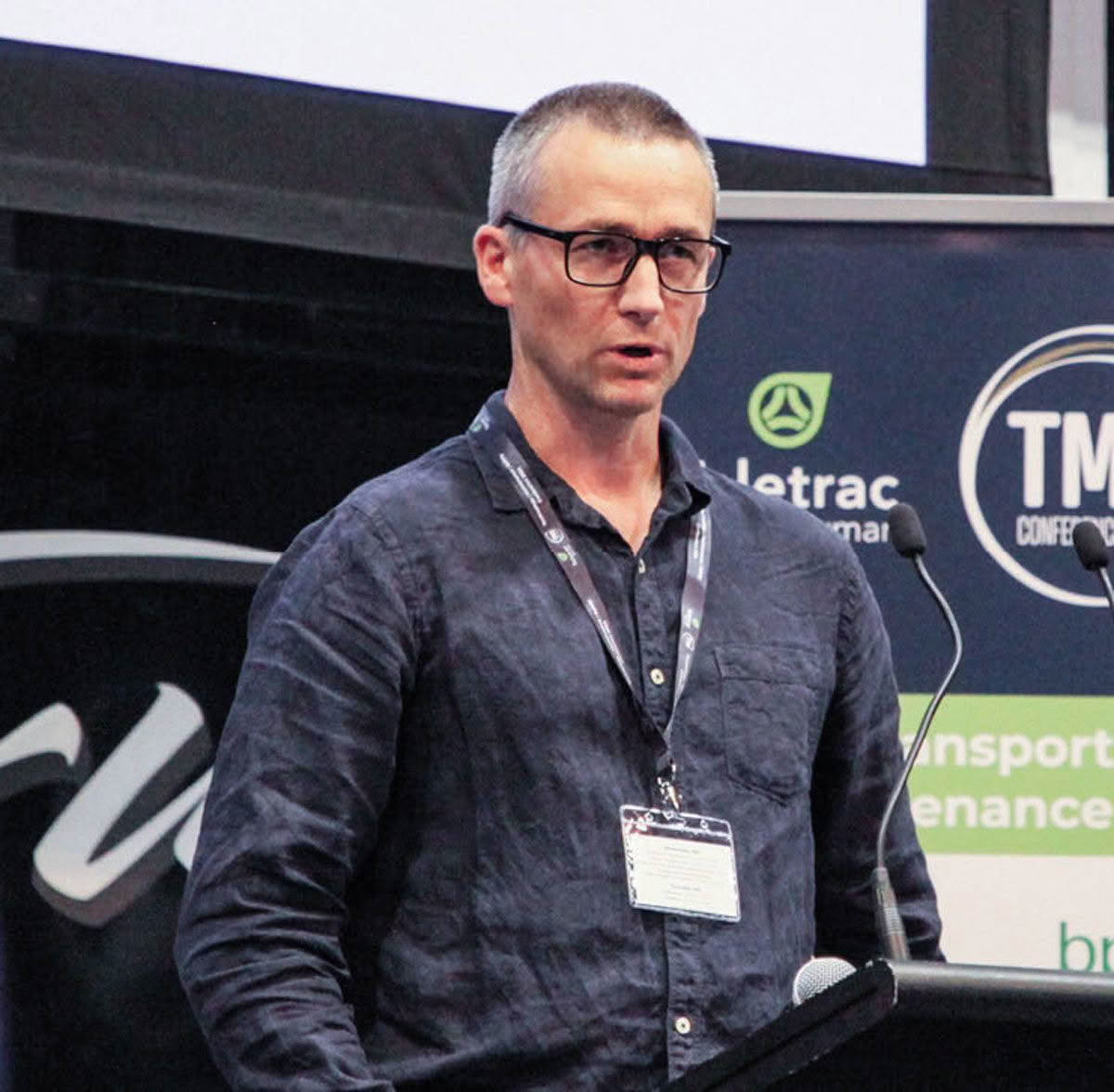
Adam Norman.
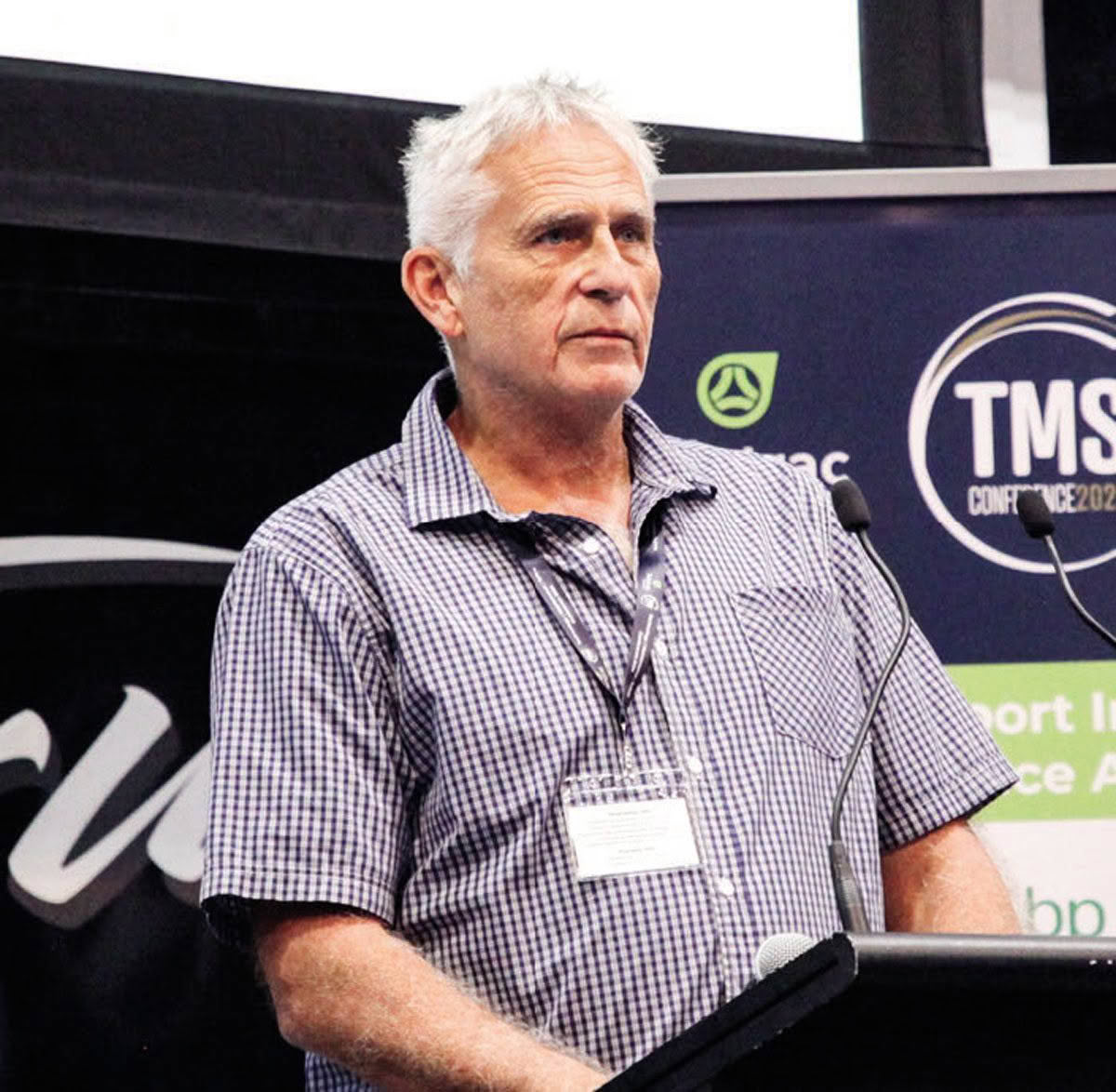
Don Wilson.
Operator Views Across Industry Sectors
Ian Newey, MD of Newey Transport, said innovation was at the heart of logging. “As a sector, a lot of what we’re seeing today has come out of the Log Transport Safety Council’s desire to push the envelope on stability, load height and technology. In the past five or six years, we’ve seen a steep increase in innovation in log trailers.
“The curve is at a point where you think, ‘How much further can we design these things?’ But EVs and hydrogen-powered vehicles will bring in the opportunity to redesign again.
“The VDAM rule is going to have to be modified so we are not compromising the safety gains made with low and long vehicles to offset emissions gains.” Newey suggested fleet standardisation to make maintenance programmes a lot easier. “We understand the trucks, front to back, and as many truck owners will be aware, if you have an issue with one truck, typically you’ll have that with all of the same model.” He said the company had found AMT was the way to go, “especially when older drivers extend their careers because of it”.
Newey said community engagement was key. “In the logging sector, we’re always looking for permission from the community to operate. That public support from the rural sectors is really important.” He said engagement had been advanced through the nationwide Wood is Good programme.
Adam Norman, GM of Normans Transport, spoke about running a family owned provincial carrier. “One thing we’re trying to change in our business is to turn our energy to the people that are helping us deliver day-to-day. They are the ones helping us be successful and deserving of our attention.”
He said recent psychometric assessments for the management team had led to real gains for the company. “It helped us understand how we all operate and how to manage different people, what their strong points are and where to get people internally or externally to fill the gaps.”
He spoke about managing staff levels for business continuity and growth. “There are fantastic operators who are hard to replace. We try run a lean operation but also spend a fair bit of time on succession planning.”
Norman spoke about the company’s focus on technology. “Investing in a transport management system, especially if you’re coming from a paper system, is a whole new way of living. Embracing technology as a tool to help automation of administrative tasks is a focus for us; punching in jobs is not a great use of time.
“So, my key learning is to attract and retain talent that allows me to play to my strengths as a leader, and overall as a team, so we can achieve the outcomes we strive for.”
Don Wilson, owner of OnRoad Transport, said livestock transport was one of the most demanding sectors in the transport industry, but its importance was huge. “It contributes $6.2 billion to the economy (2.2% GDP). Beef and lamb exports alone are worth $5 billion. The sector contributes $2 billion to household income. He said the industry included about 250 operators running approximately 2500 crates.
He said infringement notices were a real challenge for the industry despite the amount of compliance. “These normally go to the transporter and not the farmers, when they are often the ones responsible. Our sector is too weak. Compliance agencies need to reward hard-working transporters more than they do.”
He said taking advantage of future opportunities required each player to take ownership of the outcome. “We do our utmost to provide quality service to the farmer and meat processing plants. Understanding each other’s difficulties and issues will lead to better solutions. Enforcement should be geared to enabling the export sector to thrive.
He said there were a lot of initiatives involving the livestock transport industry, but a change of attitude was needed. “The people we deal with need to start realising how important our sector is. All the players in the chain need to understand our issues and start applying ‘how can I help’ rather than ‘that’s not my problem’.”
Grant Lowe of consulting firm Glow 45, discussed the work of the South Island Port User Group, “However, there are a lot of common challenges throughout New Zealand,” he said.
“Ports need to manage space well. It’s difficult and expensive to build more space. Peaks present challenges, and they have to keep containers moving. Processing takes seven to eight minutes per container, it’s important for efficiency at the ports that we start finding ways of transporters just taking the top containers.”
He said wind events presented big challenges. “Restacking in heavy winds can require between 100 and 500 moves, at seven to eight minutes per move, creating backlogs. These events are happening about 12 times a year and growing.”
He said the South Island Port User Working Group aimed to promote the key values of health and safety, productivity and chain of responsibility compliance for all South Island port companies and their users; to focus on and prioritise issues of concern affecting South Island road freight operators utilising port facilities; and to improve communication and accountability between all stakeholders involved in the South Island supply chain.
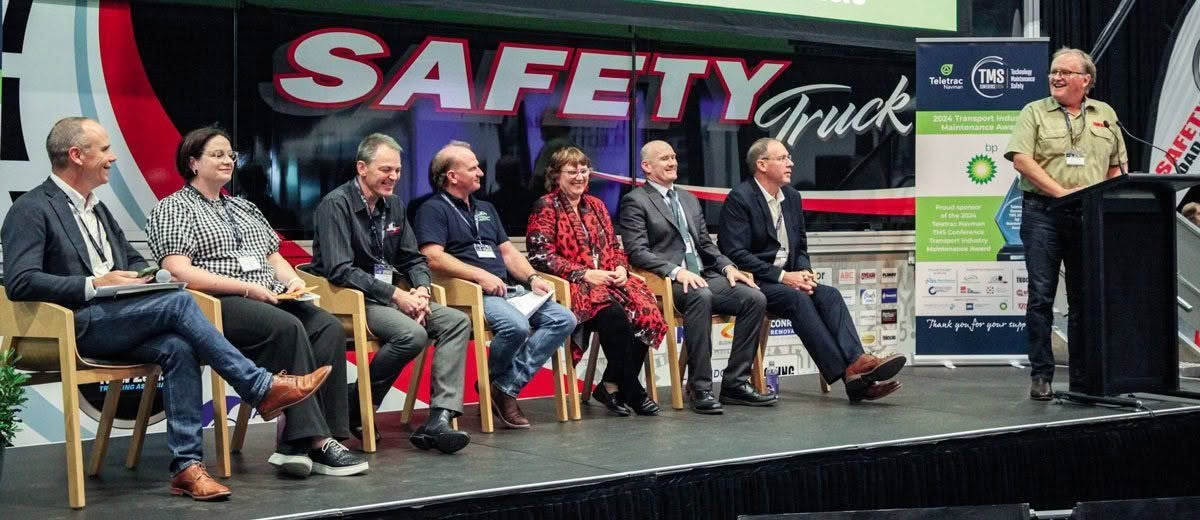
The Voices of Industry – In conversation with association leaders
“This is an incredible sector in the way it all hangs together – the innovation, coordination and hard work. We tend to undersell ourselves and we must recognise the great work that gets done. In some ways, the sector is its own worst enemy; it’s so efficient that the decision-makers take it for granted.” – Justin Tighe-Umbers, National Road Carriers Association CEO.
“Dealing with government depends on the response you get … The approach we’re taking now as opposed to the previous government is very different.
“The ministers are across numerous portfolios, so relationships with their aids is very important. They want to be seen as successful in their role, so how can we work with them, so everyone gets what they want?” – Sarah Toase, CEO, Crane Association of NZ.
Should there be some form of practical competency audit for class 2 pilots?
Yes, you can do that, but it’s optional. We appreciate there is a benefit to doing it. Once you have your certification, it’s for life. We would say at least every five years, you should reapply. Ideally, practical assessments are something we want to move to.” – Jonathan Bhana-Thomson, CE, Heavy Haulage Association.
“Years ago, we’d go to Parliament, but the previous government really didn’t want to know what we had to say. We were involved with primary industry, dirty dairy, synthetic fertilising, fossil fuels to drive our trucks, we’re all bad people … I didn’t lose a lot of sleep over it.” – Simon Pedersen, chair, Groundspread NZ.
“The real problem is the fact we have a three-year government cycle. Long-term planning happens, and two years later, someone else comes in and changes it. Unless the government decides to take infrastructure seriously, the whole multi-modal supply chain is going to be affected.” – Diane Edwards, NZ president, CILT.
“There are opportunities and challenges with all governments. They have their agenda, and we have to work out how that fits in with our agenda … But governments change. Don’t underestimate the value of having friends in Parliament who are sympathetic, and understand the industry. A champion to rely on is worth their weight in gold.” – Mathew Munro, CEO Australian Trucking Association.
“The No.1 issue facing the broader supply chain is our licence to operate with the community, taking ownership of our own safety and walking the talk instead of making it someone else’s problem … We need to lead by example and do the right thing.” – David Boyce, CEO New Zealand Trucking Association.
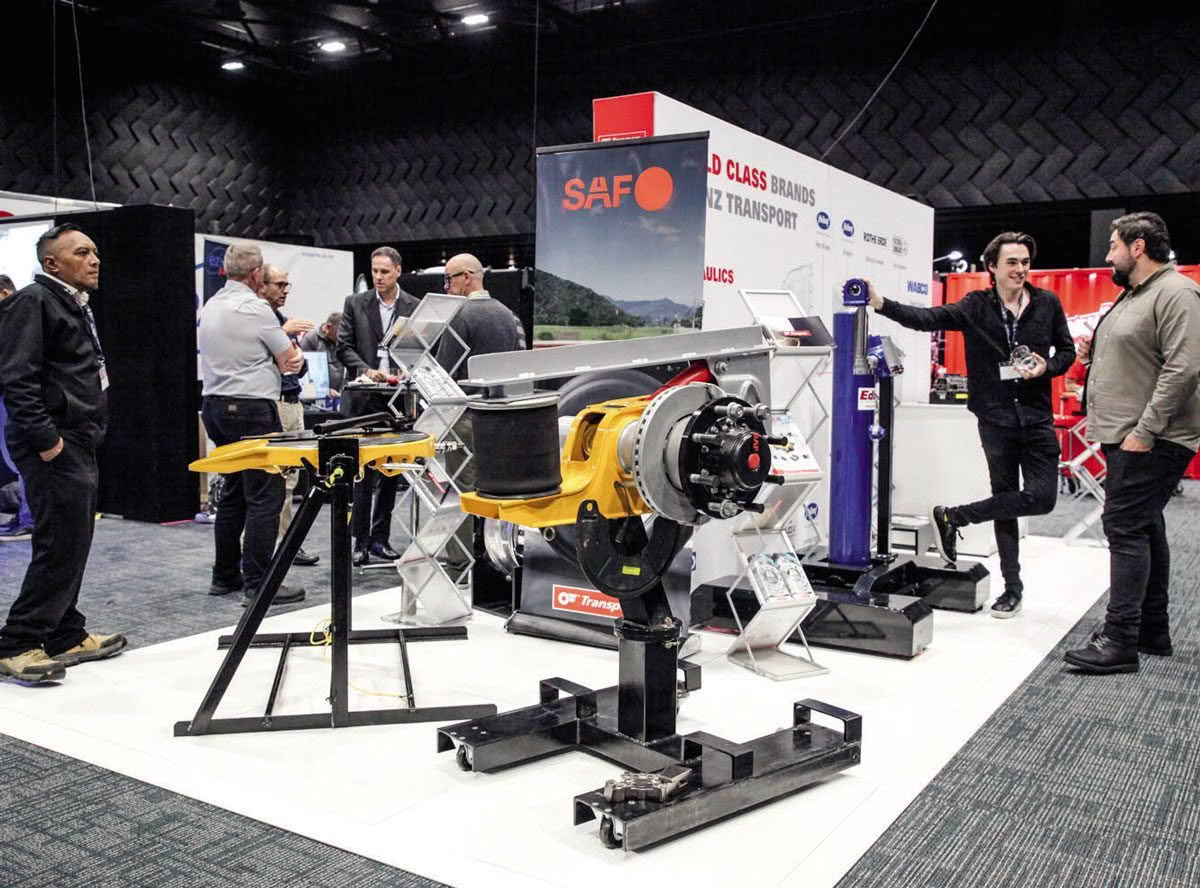
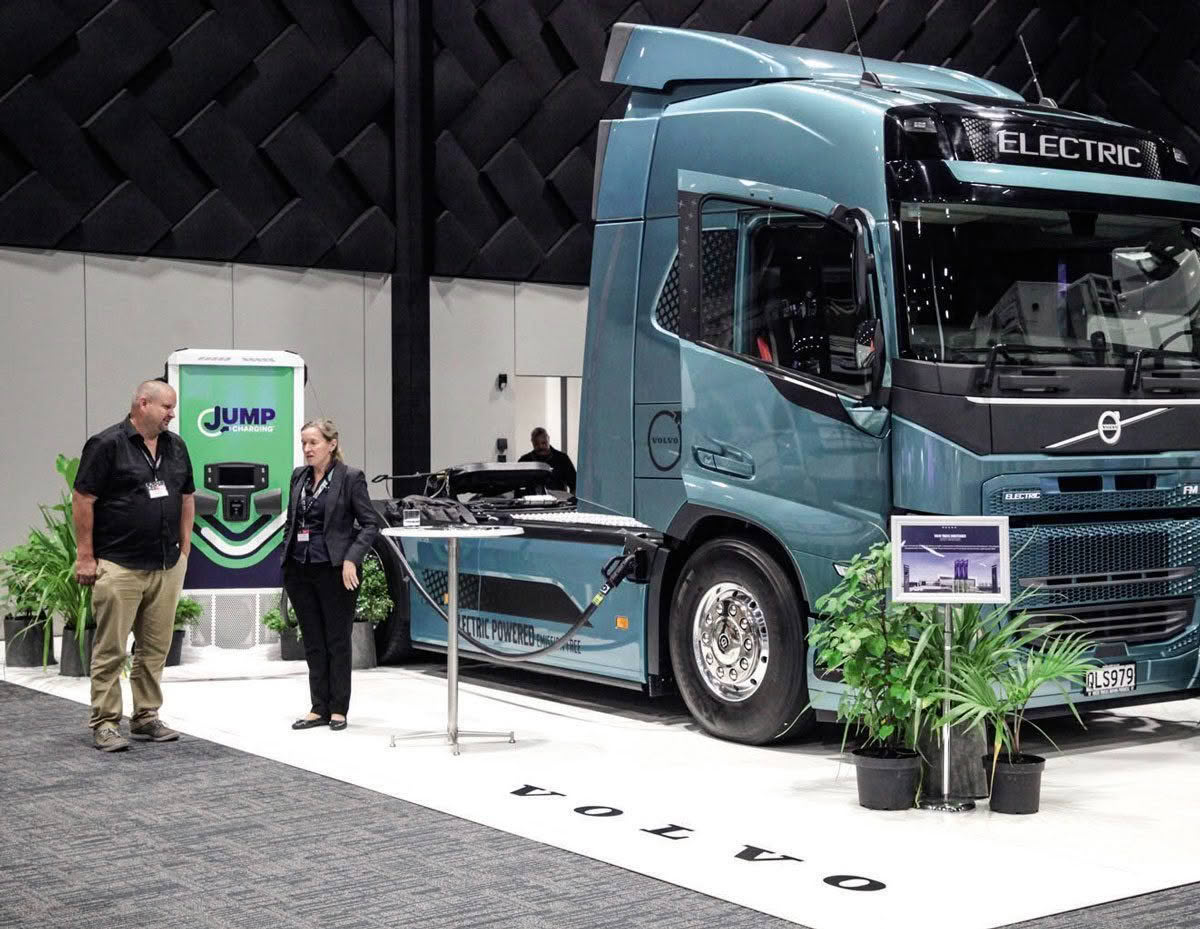
Unleashing Technology – The role of AI
Bede Cammock-Elliott, founder of seedigital, shared some insights on how AI is shaping the future of health and safety in the transport sector.
“This industry deals in danger. Transport operators have no doubt worked tirelessly designing and identifying critical risks and creating controls around them,” he said.
“A huge challenge for all of us is how do we know that these efforts actually make a difference without waiting for harm to occur? And in a world where we are awash with data when it comes to health and safety, we can often suffer from a complete lack of it,” he said.
“That’s the central promise of AI, to know about pre-harm behaviours, know how your environment may be unwittingly contributing to unsafe behaviour: employees knowing how their behaviour might be putting themselves at grave risk and knowing if your efforts to change are actually making a difference.”
Seedigital developed a solution called seeo, an AI-driven video analysis service as a system offering that tracks workplace safety and hygiene compliance.
“No one comes to work with the intention of doing a crappy job or being harmed,” he said. “What AI shows the people doing the work is how they put themselves in harm’s way unconsciously.
“AI takes you from a reactive stance into a proactive, pre-harm stance,” he said. “Solutions like seeo enable you to become proactive in mitigating risks by knowing about the extent of your risk before someone gets hurt.”
Leigh Farrow, transport solutions specialist at Teletrac Navman, discussed the role of video telematics and AI in modern fleet management.
“Telematics and AI enables businesses to automate administrative tasks that slow down improvement. And with a driver app and real-time notifications, you can keep your team engaged and focused on optimising performance,” he said.
“There are multi camera options available, but driver-facing cameras are a really important video solution because they provide status monitoring. Cameras use algorithms to detect whether something has gone wrong – for example, the driver is on the phone or there has been eye closure for a number of seconds. The solution gives the driver a warning via an alert that says, you’re getting a bit distracted, you need to change the behaviour, or pull over and take a break, get refreshed. All those things that are really important to keeping it safe.”
Farrow said most of the cameras were fully connected so that camera data fed into a business’ telematics platform.
“You can use tracking data for other purposes or other compliance tools, so your electronic diaries and other things are all connected together. It becomes a one-stop-shop where you can view all of that data together.”
Farrow said transport operators needed to encourage drivers to understand that cameras were not the enemy.
“They’re there to gain an insight of what might have happened on the road,” he said. “Be transparent. Have a company policy about how you’re going to use the data, so drivers know that when something happens, here’s how the business is going to manage it.
“Some cameras analyse every minute of driving time and give the driver a score, which businesses can use to incentivise good driving behaviour. Use the data to accelerate your driver improvement, to incentivise drivers to perform.
“Technology alone is not the silver bullet. It’s only good if you use it. You need to get the most out of the solution.”
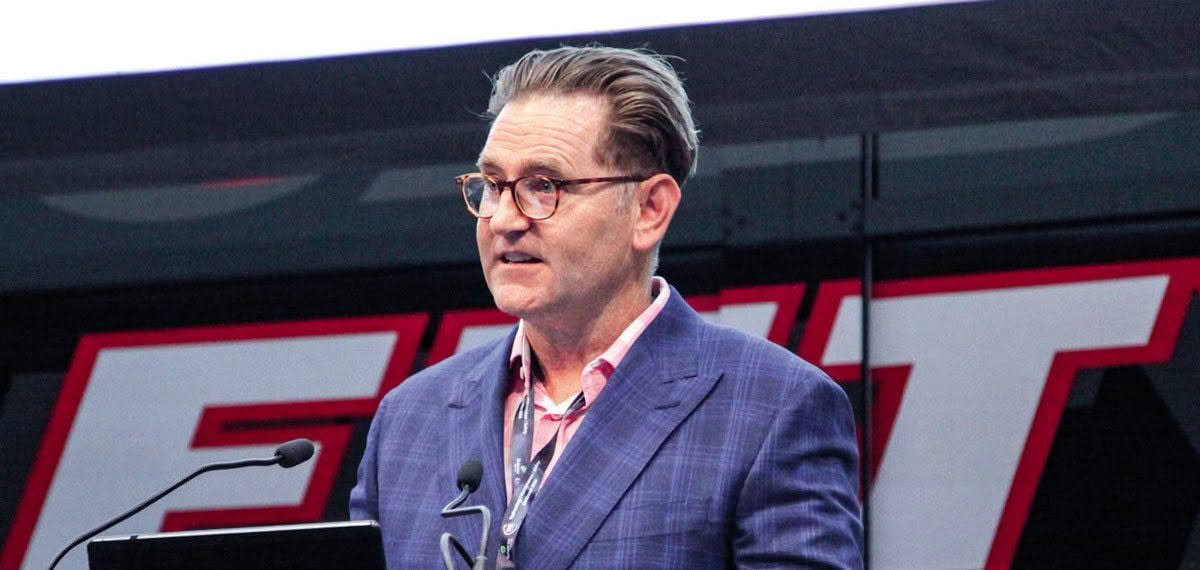
Bede Cammock-Elliott.
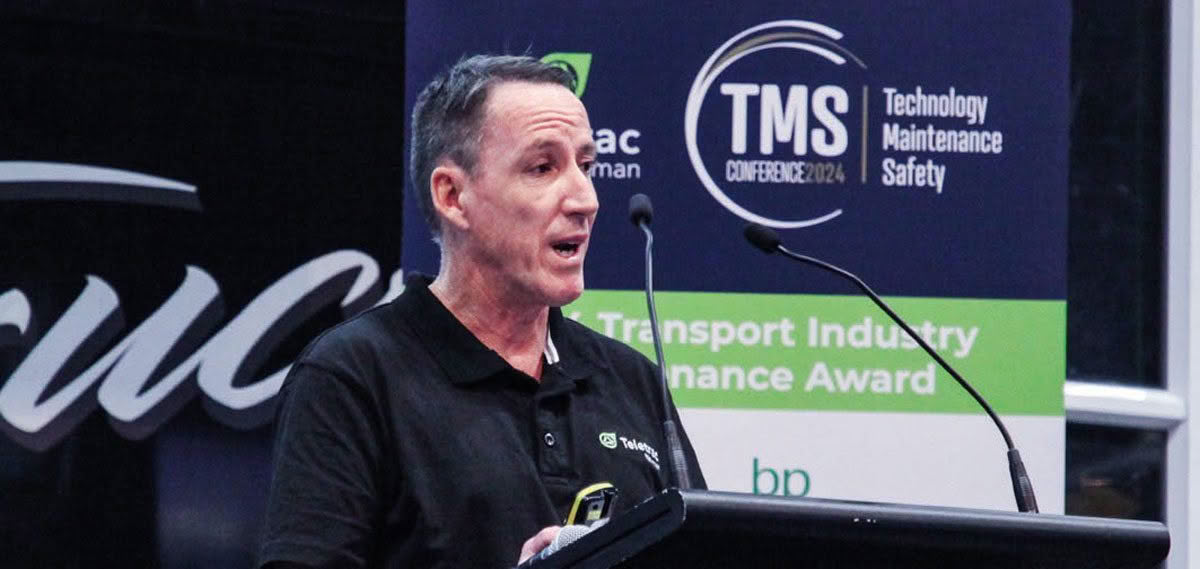
Leigh Farrow.
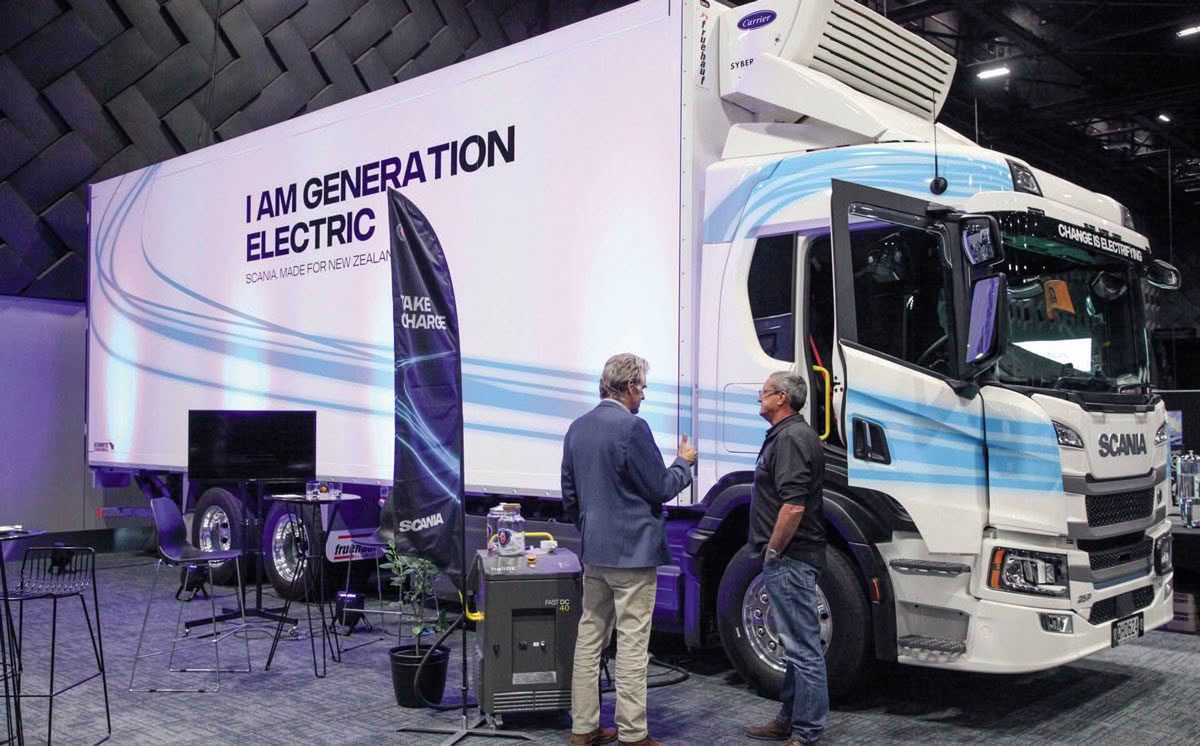
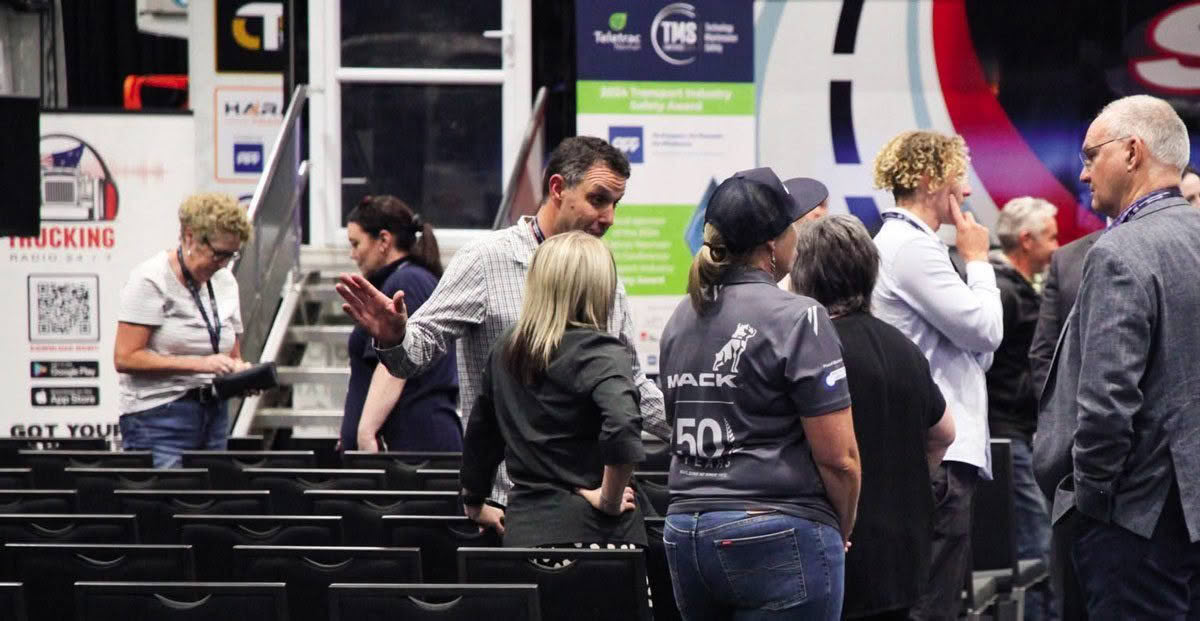
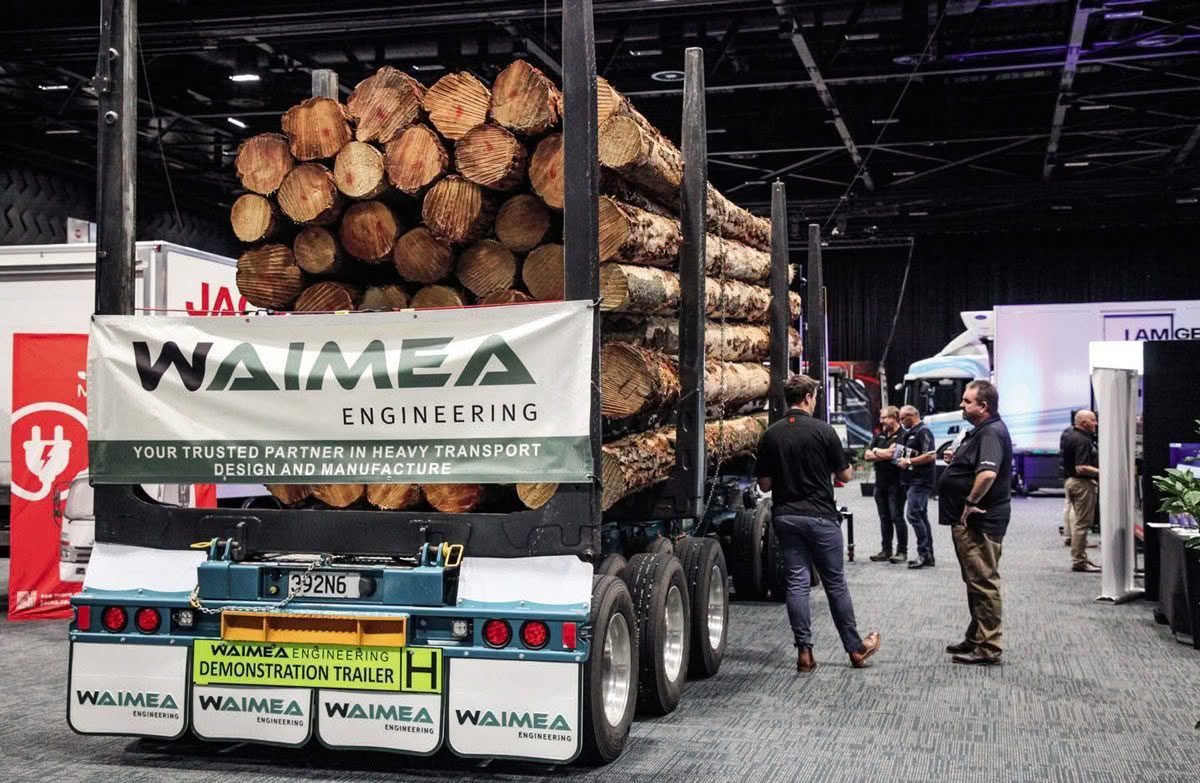
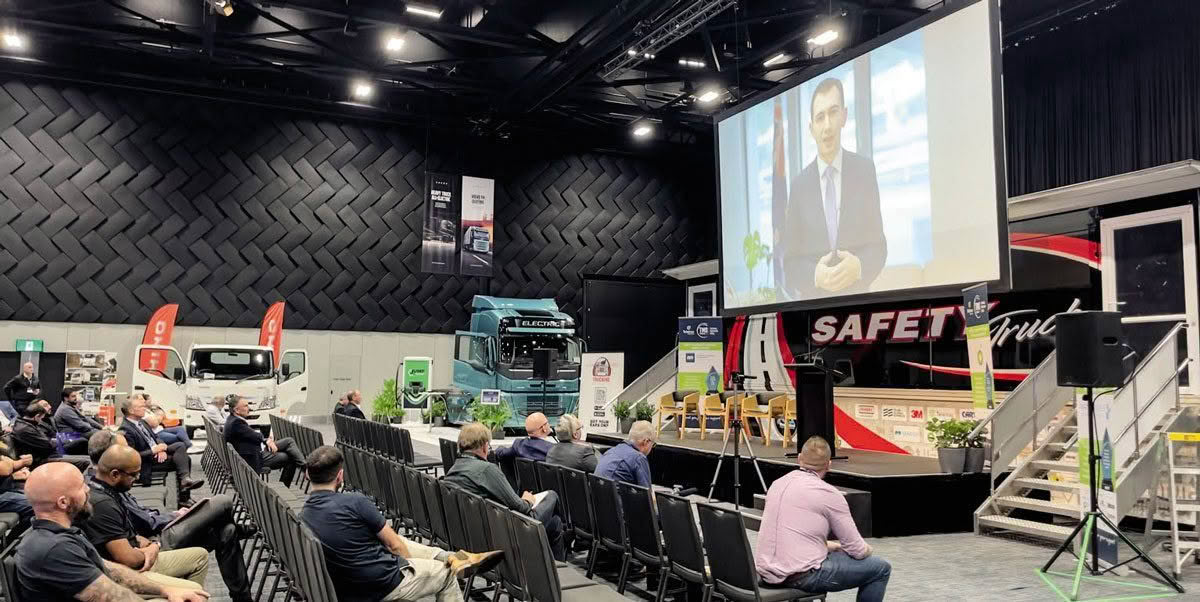
TMS Awards
Three awards were introduced at the 2024 Teletrac Navman TMS Conference
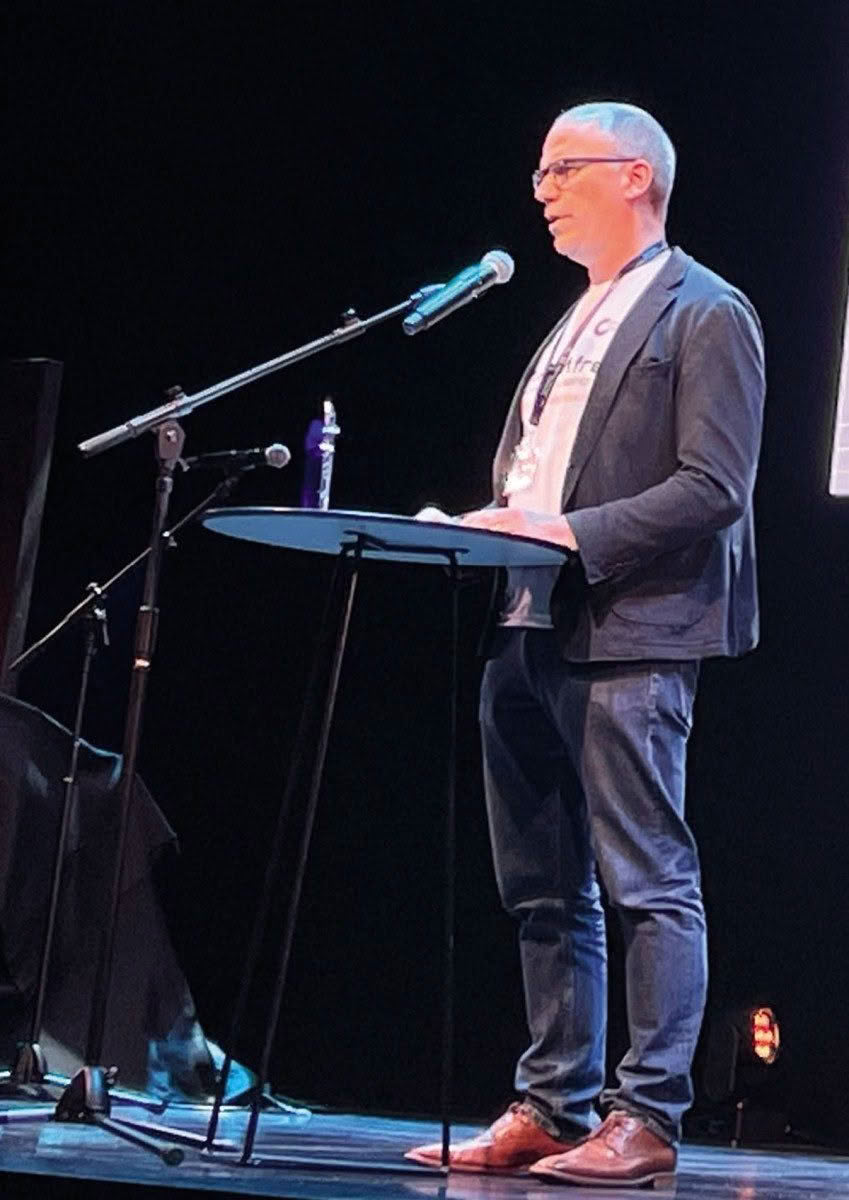
Justin Tighe-Umbers accepts the award on behalf of TDRI Solutions.
Teletrac Navman TMS Conference
Transport Industry Technology Award,
sponsored by PartsTrader
Finalists: CCS Logistics, TDRI Solutions
TrackIT, Engage Solutions
Winner: TDRI Solutions
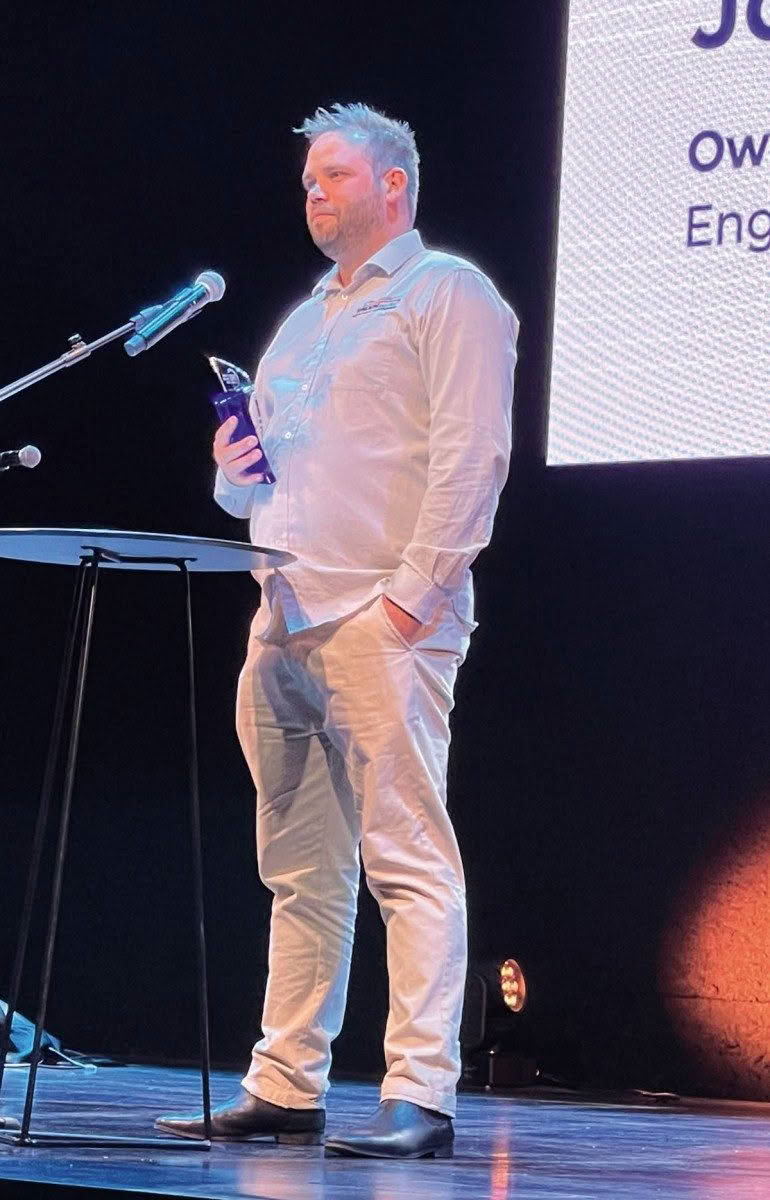
Teletrac Navman TMS Conference
Transport Industry Maintenance Award,
sponsored by BP
Finalists: Josh Verity, Truck Works
Mechanical and Engineering. Grant
Jefferson, MC Transport Repairs. Sam
Mason, MC Transport Repairs
Winner: Josh Verity
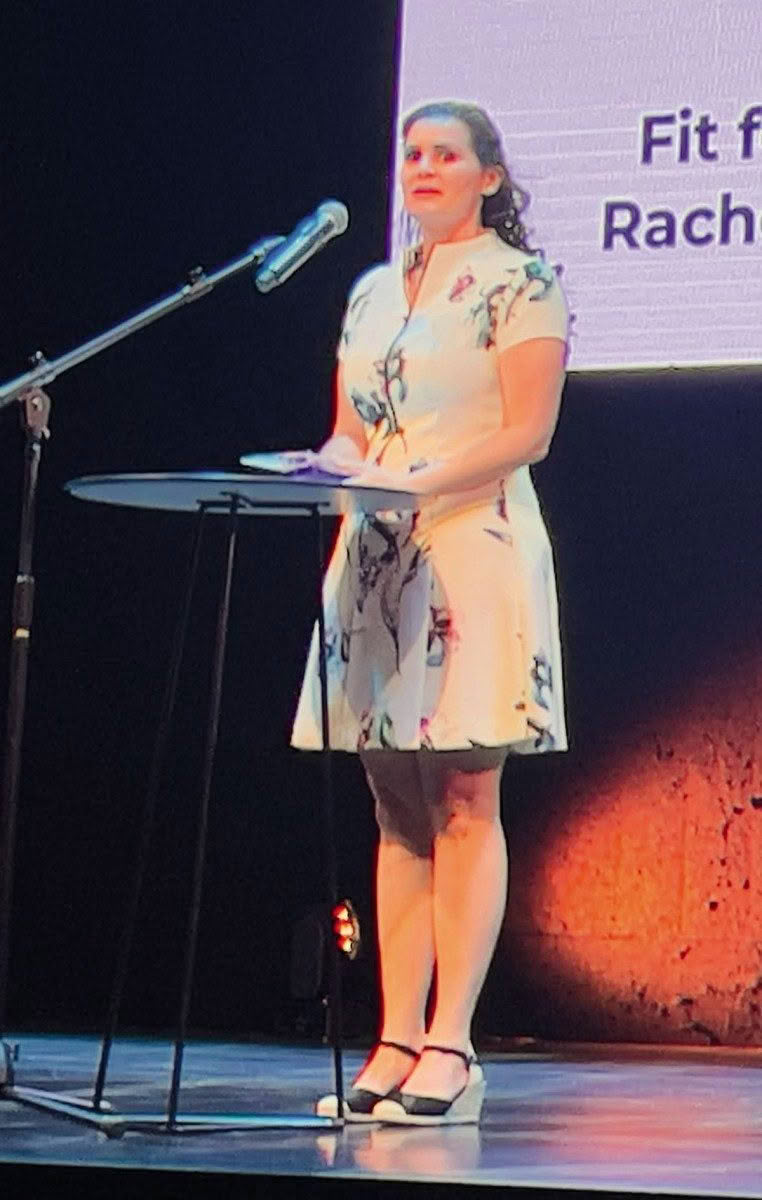
Teletrac Navman TMS Conference
Transport Industry Safety Award,
sponsored by ACC
Finalists: Waimea Engineering,
Protranz, Viewtech, Fit for Duty
Winner: Fit for Duty
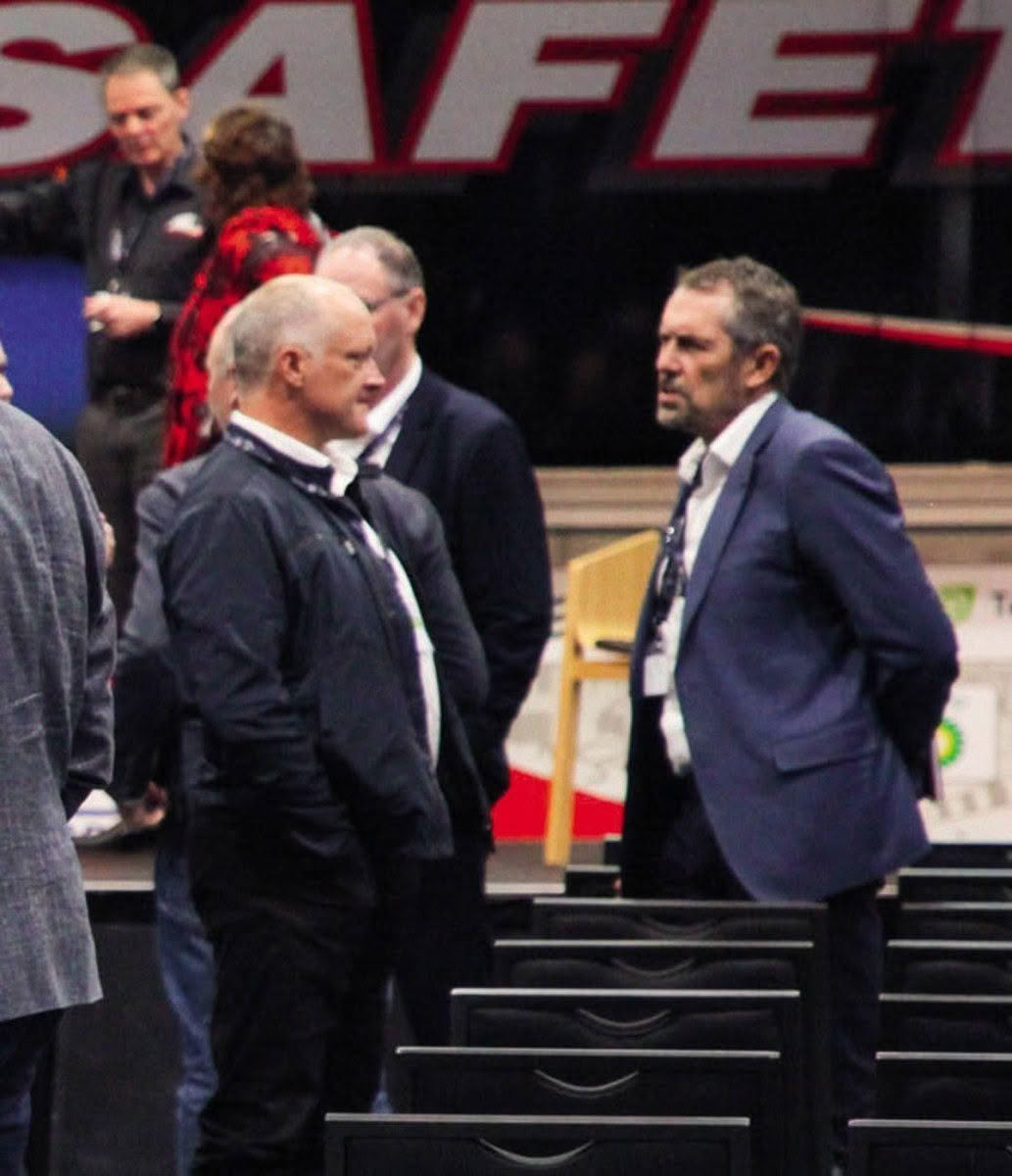
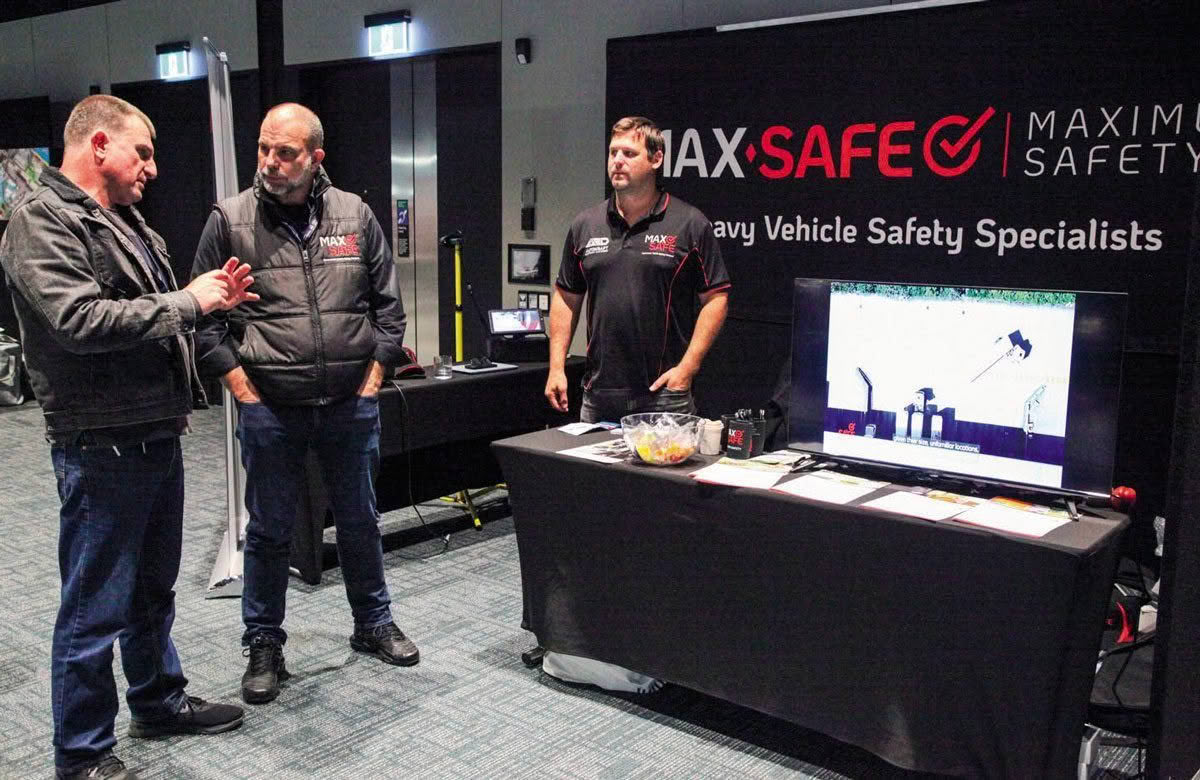
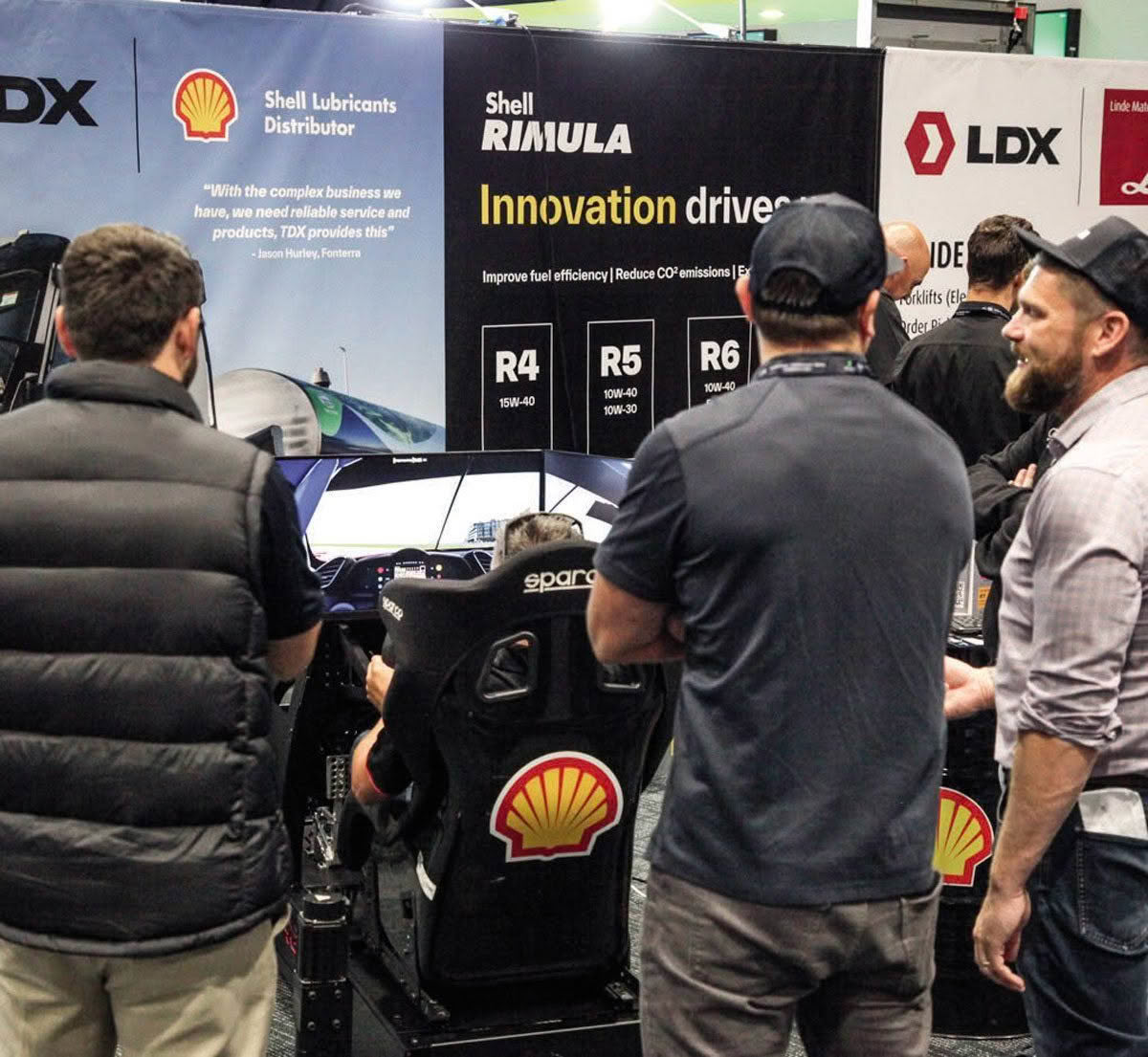
Read more
Red-tape resilience
0 Comments12 Minutes
An apple a day
0 Comments2 Minutes
The Wingman
0 Comments3 Minutes