T9NO Compromises
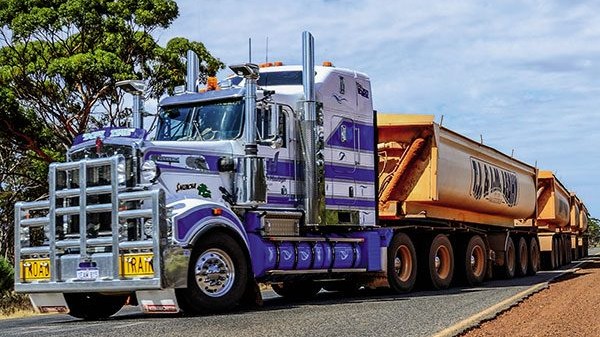
There is a fine art in specifying an extreme heavy-duty truck robust enough to endure the off-highway punishment of mine site corrugated haul roads and rough bush-exploration tracks, yet light enough to deliver a viable payload.
Kalgoorlie’s industrial hub operates in full swing 24 hours a day, seven days a week. In the small hours of the morning, fitters’ rattle guns echo through the streets while a constant parade of quad side tippers rumble through town as drivers come and go rotating on their rolling shifts.
Over the east coast of the country, most folks are still snuggly tucked up in their beds. But not here in Kalgoorlie. In the predawn greyness, the mercury in the thermometer is about to creep into the 30s.
“He’ll be down on the wash bay,” the receptionist says with a smile when I mention that I have an appointment with Gammon Haulage owner, Craig Gammon.
Craig Gammon, or ‘Gammo’, as most folks in the Goldfields know him, is passionate about keeping his truck looking new, which is no small feat given that most of the time, this T909 operates on the red dirt tracks in the remote goldfields region of Western Australia.
Sand in this pit is 98% silica, highly sought after in the nickelsmelting process.
All power dividers engaged to get moving on soft sand.
Sure enough, Craig’s T909 sat parked on the wash bay. Meantime, the man himself was busily spraying it with a homemade cocktail of truckwash detergent and kerosene.
“You found the place all right then,” Craig says with a smile, glancing in my direction as he continues waving the spray wand in an up-and-down motion. “This won’t take long.”
He explains how he sprays his detergent mix over the Kenworth, and then lets it soak for a few minutes to remove the bitumen and road grime. He uses this method during the week when the truck is busy on double shifts, like today. But he assures us that he gives it a thorough sponge wash on weekends.
Half an hour later, we were well on our way to the old abandoned Bonnie Vale townsite, roughly 14km north of Coolgardie, to load sand for the nickel smelter back in Kalgoorlie.
As Craig guides the T909 into the sandpit, it is hard to imagine that back in 1897, out here in this barren wasteland, the town of Bonnie Vale was gazetted. It was apparently named after a prospector called Bonnie, who picked up a 7oz (220g) nugget back in May 1894, which at today’s gold prices would be about $17,500.
Today, there are few remains of the township of Bonnie Vale, other than it serves as the railway station for nearby Coolgardie on the Perth to Kalgoorlie passenger service, aptly called The Prospector.
The sand in this pit is 98% silica, highly sought after in the nickel-smelting process and predominantly used as furnace flux.
Today, nickel smelting often occurs with flash smelting, when electricity and oxygen combine to quickly reach the high temperature needed to melt the nickel ore. That is an incredible 1453°C.
The nickel ore melts until it becomes a product known as liquid matte, which is usually about 45% nickel and 55% slag and other metals. After the nickel smelting is complete and cooled, it gets used for many different purposes.
Once the removal of slag occurs, the remaining product gets sold to other industries. For example, nickel is commonly used as an alloying agent with steel and other metals because it is corrosion-resistant and can be highly polished when required.
Craig pulls the road train in a straight line parallel to the pit wall then wanders over to the loader. This wheel loader has a 15-litre engine producing 350hp and 1244lbft of torque, which runs through a four-speed powershift transmission allowing operators to choose between manual or automatic shift modes. In addition, it boasts onboard scales built into the lift arms to allow on-the-go weighing of the material in the bucket. This feature allows operators to load trucks more accurately and efficiently. In addition, the bucket scoops up to 5m3 of sand at a time.
Craig said that this dry sand weighs roughly 1600kg/m3, which means he is tipping about eight tonnes of sand into the trailers with each bucketful. He wastes little time on the loader and puts four generous buckets in each of the full-length trailers and two buckets in the shorter A-trailer. All the while, he checks the weight with the loader’s onboard scales.
It takes roughly half an hour to load three trailers and roll out the tarps. Then it is time to get down to the business side of the operation. We are here to investigate how the big-bore Cummins handled getting 170 tonnes and 86 wheels rolling in soft sand.
The soft sandy road base in the pit makes it hard for any truck to get rolling. But Craig has all the power dividers engaged to ensure each axle is getting power. In no time at all, the engine is working at 100% capacity.
The turbo boost gauge needle hovers up at 260kPa. In the cabin, you can hear the air getting sucked down the high-rise air intakes as the big 15-litre Cummins gobbles up to 45,000 litres of air per minute when Craig has the throttle fully opened up.
It’s well worth checking out the gauges in the dash of this unique T909 because you don’t often see such a welloptioned and practical dash package like this these days.
Located in the top row of the centre binnacle are the axle oil-temperature gauges for all three axles. Below is the all-important turbo boost gauge. Then the engine oil temperature and the main transmission temperature gauges. For remote Outback road-train operators such as Craigs, monitoring component oil temperature is vital.
A sudden spike in temperature is a sure earlydetection tell-tale that something requires attention. For instance, in the middle of summer, when the ambient temperature is hovering at about 40°C, it could simply be a matter of dropping down a gear and slowing the road train down a few kilometres to lower the temperatures.
There are two Murphy switch gauges with black bezels on the main centre dash panel. They are paramount for operators such as Craig, and it’s worth spending a moment investigating how they work and why they reside prominently in the main dash panel.
The Murphy switch gauges first appeared in the late 1930s, and their popularity quickly ensued due to their robust, simple design, ease of adjustment and simplicity for operators to test.
What makes the Murphy switch gauges so reliable is their full mechanical operation. They don’t require temperamental sensors or electrical wizardry to function.
The pressure and temperature models are diaphragm-actuated, with built-in electrical switches that can trip alarms or shut down equipment if required.
These vapour-actuated gauges feature a sealed capillary tube and a sensing bulb. When subjected to heat, the liquid in the sensing bulb changes to vapour, creating pressure against the diaphragm mechanism.
The diaphragm translates this vapour pressure into a mechanical gauge reading. Meantime, the gauge pointer acts as a pressure or temperature indicator (depending on the gauge) and as one switch pole which completes a circuit when it touches the adjustable limit contact.
As a result, the contact gets grounded through the gauge case. A corrosion-resistant coated steel case encloses the gauge’s mechanism. The lens is constructed from break-resistant polycarbonate for added protection, and the gauge is available with a polished, stainless steel or black bezel. Importantly, these gauges have a self-cleaning motion to enhance electrical continuity.
Thankfully, today, even with the mercury nudging 44oC, the Murphy gauges didn’t sound any alarms. Still, with all this weight, the coolant temperature sat comfortably at 97°C.
Also, it’s worth looking at how the transmission radiatorcooler mount is concealed into the construction of the front of the rear mudguard bracket. The extra thought that Craig meticulously put into this truck’s detailed specification is what makes it so unique, productive and durable.
“It’s all about keeping the running gear cool,” Craig says. “It’s certainly not your average run-of-the-mill Kenworth. There are some good engineering outfits here in the west that really know how to fine-tune these trucks to survive in our conditions. The cooler we can keep the components, the longer they live out here.”
Keeping an eye on all the temps is critical when operating in 40+°C heat.
He deliberated for some time on the decision to specify traditional hypoid drive rear axles over the heavierduty hub-reduction rears.
“There are two big disadvantages for me with hub-reduction rear axles in my operation. Firstly, in a tri-drive configuration, they add a lot to your tare weight. If we operated solely off-road on mine sites, then the hub-reduction rears might be the better option. Secondly, the hub-reduction rears get extremely hot and will prematurely destroy the outer planetary drive if they are driven over 80kph for extended periods, such as with on-highway driving.
“These Meritor drive axles, on the other hand, have more than proven their worth in this country. That’s why I chose the Meritor rear axles – for a tare weight advantage and on-road productivity gain,” says Craig.
“It certainly wasn’t a cheap exercise – that’s why it’s got the ‘Money Muncher’ written in the side of the bonnet. But I’m expecting to get 20 years out of this truck, with a scheduled major overhaul at 10 years.
“I’m looking at the big picture. That’s why it’s worth investing in premium gear like the Murphy gauges to help protect my investment.”
Read more
The sale is on!
0 Comments7 Minutes
Running north
0 Comments13 Minutes
Changing the Game
0 Comments10 Minutes