
In November 2022, Auckland-based Reliance Transport took delivery of two Scania 25P electric trucks. The first two electric Scanias on New Zealand’s roads, their operation with Reliance is noteworthy as they are part of the company’s usual replacement schedule – meaning they’re expected to go to work and keep working like any other truck before. Significantly, they’re also part of a much bigger company initiative to manage energy usage and leave a legacy future generations can be proud of.
Split between its two yards on Ash Road in Wiri and the Onehunga Wharf, Reliance Transport is a hive of activity. The Auckland-based company’s primary activity – comprising 70% of its revenue – is container cartage, and you don’t have to go far in Auckland to come across one of its distinctive yellow and black trucks. The other 30% of the business is flat-deck cartage.
Despite all the comings and goings and constant flow of containers, the company comes across as rather unassuming… just a mainstay of the Auckland transport scene – as it’s been for six decades – with straightforward facilities and a pragmatic pair of brothers making sure things happen. However, that pragmatism means there’s much more going on behind the scenes than first meets the eye.
Pay closer attention to the trucks as they rumble past the yards’ boom gates, and you’ll notice they’re all Euro-6 models from within the Daimler stable. A four-year replacement cycle to keep the fleet as up-to-date as possible has long been company policy to maintain ultimate uptime and efficiency, and in November last year, the last two Euro-5s were replaced. With that came the introduction of Scania to the Reliance Transport fleet. And as you’d have realised by now, the first two to don the yellow and black are not just any Scanias…
By the time the 25P had been introduced to the New Zealand market in mid-2022 (New Zealand Trucking, July 2022), Scania New Zealand had found a suitable fleet in Reliance to demonstrate the capabilities of its new electric trucks. Reliance had already explored some of the options in the market, but the company really wanted the choice of factory-backed units before taking the plunge.
“We thought, ‘Let’s just relax and wait,’” explains director Mark Darrah. “It’s not just the vehicle you need to think about. You must be able to trust the back-up and service. Scania owns their distribution, so partnering with them was a no-brainer.”
Mark and brother Grant (operations manager) dealt with Alfons Reitsma, senior product engineer of pre-sales at Scania New Zealand. With his offer, they approached EECA for co-funding. The target date to have the trucks on the road was February 2023, so achieving that three months ahead of schedule – including the stinger setup and twin-axle skele trailer by Fruehauf – created smiles all around. The whole process took 15 months.
“The thing with the Scanias is they’re OEM trucks. We wanted a real truck doing real work,” says Mark.

The energy frontier
As we were to find out, the 25P certainly is a ‘real’ truck. In fact, by the time we left the Ash Road yard bound for home, we were bowled over – not only by the truck but also by what we’d learnt about the Reliance Transport operation. Understanding what brought the company to this point and the inspiring vision behind its journey puts the 25P into clearer perspective – so let’s explore ‘Project Switch’ before getting into what the 25P is all about.
“It’s a step change,” Mark says of Project Switch, the company’s five-stage programme for achieving carbon neutrality and ultimate efficiency. The biggest challenge for an operation such as Reliance is energy consumption, and as Mark adds, that dictates the choices made when it comes to fleet replacement.
The four-year cycle might seem bafflingly short, but as Grant explains, it’s the sweet spot for Reliance. “That’s 15,000 hours on double shift, and that’s when they start having problems from all the stop-start and heavy traffic of a metro operation. Drivetrains, brakes, suspension, door handles, seats… Even though the engines are still okay, it’s the magic number for our operation.”
With such a regular replacement cycle, all the trucks in the fleet are on an operating lease. “Lease prices haven’t really changed in the past few years. If an asset’s working life is less than five years, lease it. That also allows us to keep on top of the next generation of trucks,” Grant continues.
“The good thing about off-balance-sheet stuff is it leaves on time and on budget, and you can organise your replacement trucks,” Mark adds, pulling up a slide illustrating the company’s replacement plan to 2029.
“With Euro-5, the service interval doubled and fuel was better. In Euro-6, service tripled and fuel was better still. The less diesel you burn, the cheaper it is… It’s dollars and cents – it’s efficiency. Our whole focus – as it’s been for the past 15 years – is to have the most energy-efficient trucks.
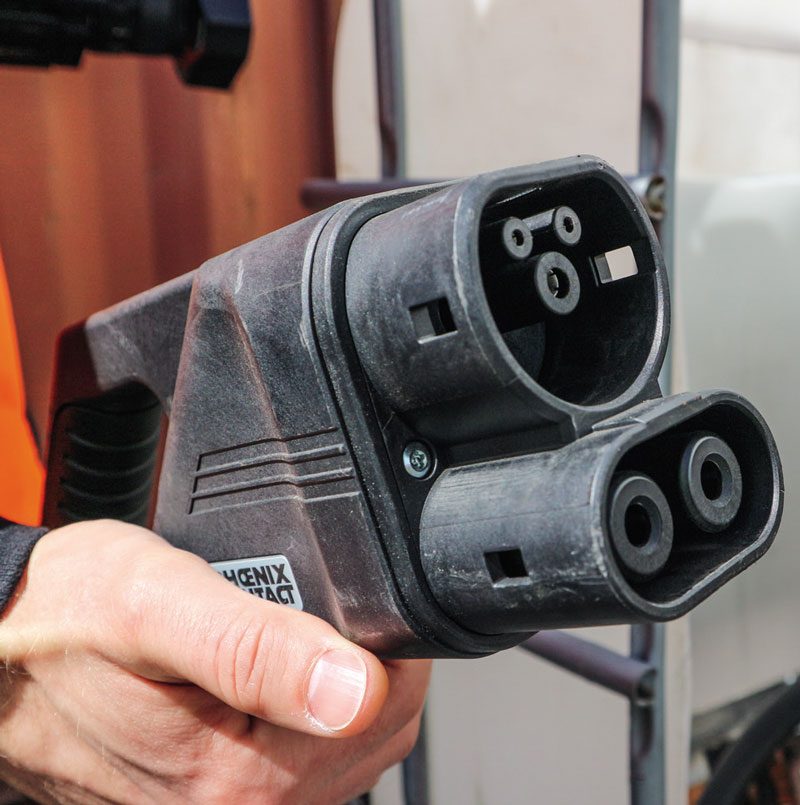
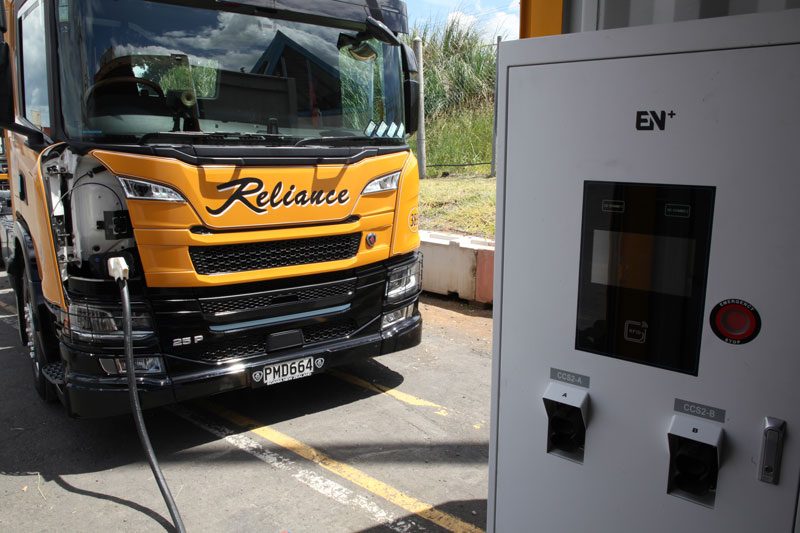
“As our Euro-6 trucks are replaced, we’ll introduce cleaner technology. Our first Scania 560 Supers are coming mid-2023, which can run on biodiesel – but that’s to be worked out. By the end of 2023, we’ll replace our 4×2 tractors. The question is, ‘What do we replace them with?’
“That’s the challenge. We set to replace the lighter trucks first because those are the BEVs available. How we’ll replace an 8×4 tractor with a quad swing lift, I don’t know. Big units like the 60-tonne B-trains… we’ll be stuck using [diesel] for a while,” Mark continues.
The company has two hydrogen trucks on order with TR Group, so there may be an answer in those. “But we’ll just transition every year. I envision about five units a year.”
In fact, introduction of battery-electric trucks is the third stage of Project Switch. Stage one was the introduction of four electric Nissan vans three years ago, followed by the first electric cars and four electric fork hoists. Stage two was getting the whole fleet of trucks to Euro-6. Stage three, as mentioned, is the introduction of electric trucks and the company’s first Sany electric reach stacker, which arrived for duty at the Onehunga Wharf last year and is already paying dividends for the company’s bottom line and social licence.
“The accommodation and residences across the road would complain about the diesel reach stacker operating at all hours of the night, but we haven’t had any complaints since the electric one went into operation,” Mark says. “I think it’s awesome – and I know what it cost!” he adds with a laugh.
Stage four of Project Switch is commissioning an on-site microgrid to power the chargers. “In reality, this is part of stage three because we can’t run the trucks without the infrastructure. You can’t run big chargers off the national grid – you need big transformers, and it costs too much money,” Mark explains.
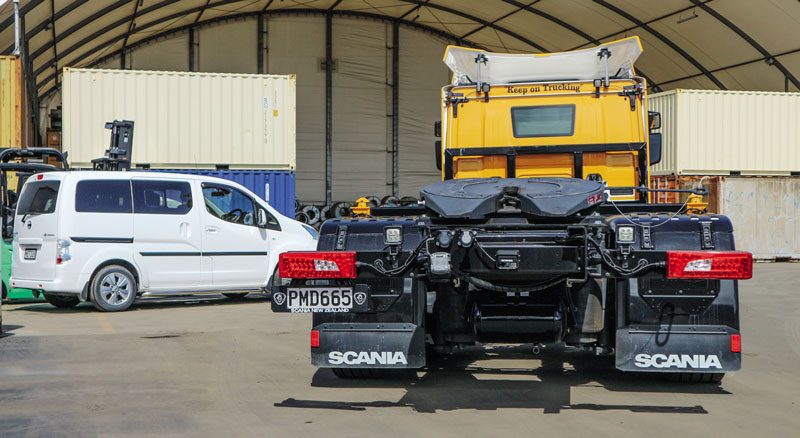
“By 2028, we’re aiming for a greenfield site, the depot of the future for us. We need 4gWh (giga- watt hours) of energy to run our business, and that site will give it to us. It’s achievable. That’s the development in the States now. Solar in the day and low-current grid connection to trickle-charge batteries at night.”
The fifth stage will be a carbon sink of native reforestation. In the meantime, the company has a carbon-zero offset in place, whereby it is audited on its and its suppliers’ CO2 production and energy use.
Carbon credits are bought to offset it. As such, Reliance Transport has achieved net carbon-zero certification by Toitu Environmental.
“And that’s what our customers want to know now, too. We report to one of our biggest customers on our CO2. All the biggest companies in New Zealand are part of the emissions trading scheme, and they want to know about their supply chains. Besides, it’s the right thing to do. I’ve studied all sides of the climate change debate, and it’s not bad insurance to be doing something,” Mark comments.
“I care about the customers, the staff and the owners. The best we can do for those three stakeholders is to be efficient.”
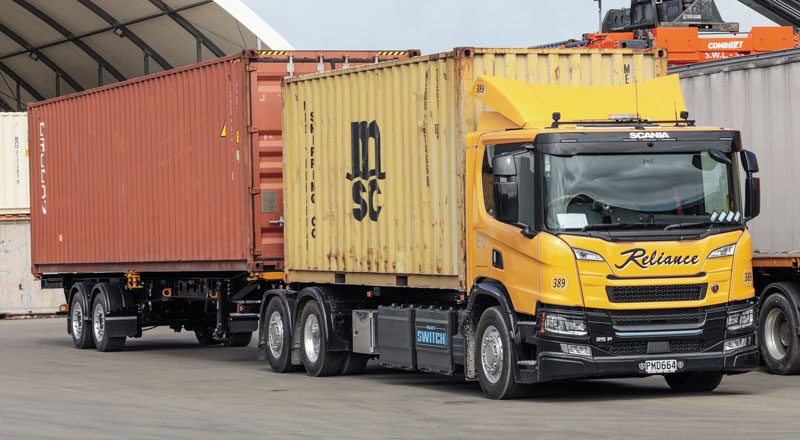
Nuance and numbers
“It’s not a science experiment or a greenwashing thing. The trucks are going to do the job the old ones did,” Mark says as we take a walk around the Wiri depot. “The trucks spend a lot of time stationary loading and unloading – we don’t need a big range.”
Grant opens the Daimler telematics app on his phone to illustrate the fleet benchmarks. “The 26 Euro-6 vehicles we can access data on are averaging 2.3km/l this week (between Sunday and Friday), over 31,000km, at an average speed of 22kph. The extremes are 1.8 and 3.3km/l.”
Mark explains the potential savings. “For diesel, we may look at 2kpl at $1.20. Fuelling an EV is four to 15 times cheaper, depending on how you source or produce your energy.”
He points to the array of solar panels on the roof of one of the buildings. On average, they produce 500kWh daily, enough to run three of the Scanias.
However, the setup is yet to be complete so, for now, the Scanias charge off a portable 40kW charger connected to the grid at Wiri and a 120kW charger (the maximum the trucks can handle) at Onehunga.
“There are all these little nuances,” Mark says. The megawatt charging standard coming in 2024 will revolutionise it, so we have to design our charging infrastructure for that. We can connect to the grid to trickle charge at night when the cost is low and have a 300kW solar setup and a 2mWh battery storage system to charge at a megawatt off- grid. That’s a couple of million dollars…
“But we’ve burnt a million litres of diesel a year for the past 15 years… so investing in the long term, we can drop energy to a fraction and fix that cost for decades with a microgrid.”
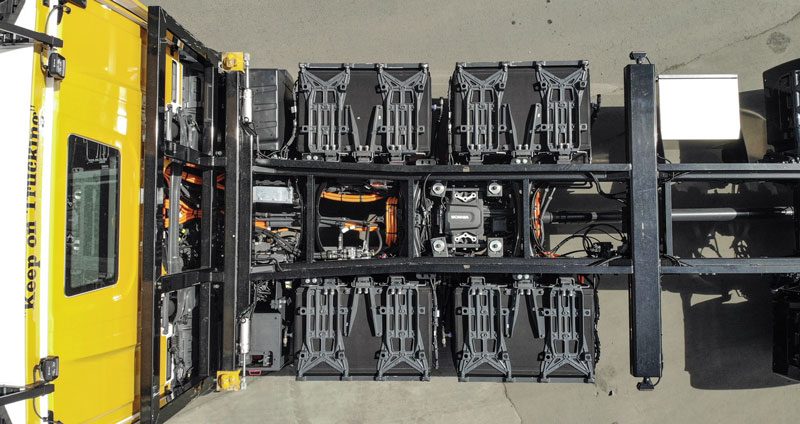
Meet the 25P
Named slightly differently from Scania’s convention for its diesel-powered trucks, 25P indicates these EVs offer a range of up to 250km and have a P-series cab. Of course, the range of an electric vehicle is more susceptible to variables, such as its operational environment, laden weight, bodywork, final drive and driver behaviour, than one would be used to with a diesel. But even then, when trucks like those in the Reliance fleet average less than 200km a day, depending on what they do, the argument about ‘range’ almost becomes moot.
The battery sets on these units are comprised of nine 33kWh units – two sets of four on either side of the chassis rails and one set under the cab – for a total output of 297kWh. A five-battery option of 165kWh is available, but that obviously won’t offer the full 250km potential. The vehicle is charged using the typical CCS type-2 switch that has become the standard for EVs.
The electric motor delivers a continuous output of 230kW (310hp), with a peak output of 295kW (395hp) and peak torque of 2200Nm. For those unfamiliar, continuous power is the maximum power the powertrain (electric motor and batteries) can deliver continuously over a long period. The peak power can be utilised in periods at full throttle. The motor unit is mounted roughly where one would expect to find a gearbox and drives through a conventional prop shaft. At about half, maybe two- thirds, the size of a gearbox, it’s surprisingly small – impressively so, especially considering its output and the fact it incorporates a two- speed transmission.
According to Alfons Reitsma, the rear axle has “quite a deep reduction” to provide the gradeability and lift-off at gross combination weights. The rate of acceleration has been limited to protect the cargo and the truck’s capability – drivers would burn through electrons quite rapidly blasting away from the lights…
Should the operator wish, a 60kW electric PTO can be fitted. A separate 24V system is fitted to run the usual electronic systems.
An urban/distribution type vehicle, 25P is available as a rigid or tractor unit in 4×2, 6×2 and 6×2*4 configurations. It offers a GVW of up to 29 tonnes, and wheelbases are flexible. The Reliance units are the 6×2 with steering tag axle. They weigh in at about 11 tonnes tare, plus 3.5 tonnes for the trailer, and measure 20m.
“Comparing EV and diesel metrics is like comparing apples and pears,” Alfons comments.
“At the moment, no well-defined metrics have been settled on. It relies on the total driveline configuration, application, route conditions and energy analysis. It’s all shared and configured with the client. We were able to give Reliance an energy consumption, and that’s how they modelled their business case for this application. The calculation changes with every application. If you’re carting over the Kaimais, the cost and energy consumption will change.”
It’s a whole new world, but one we need to get to grips with. So, let’s…
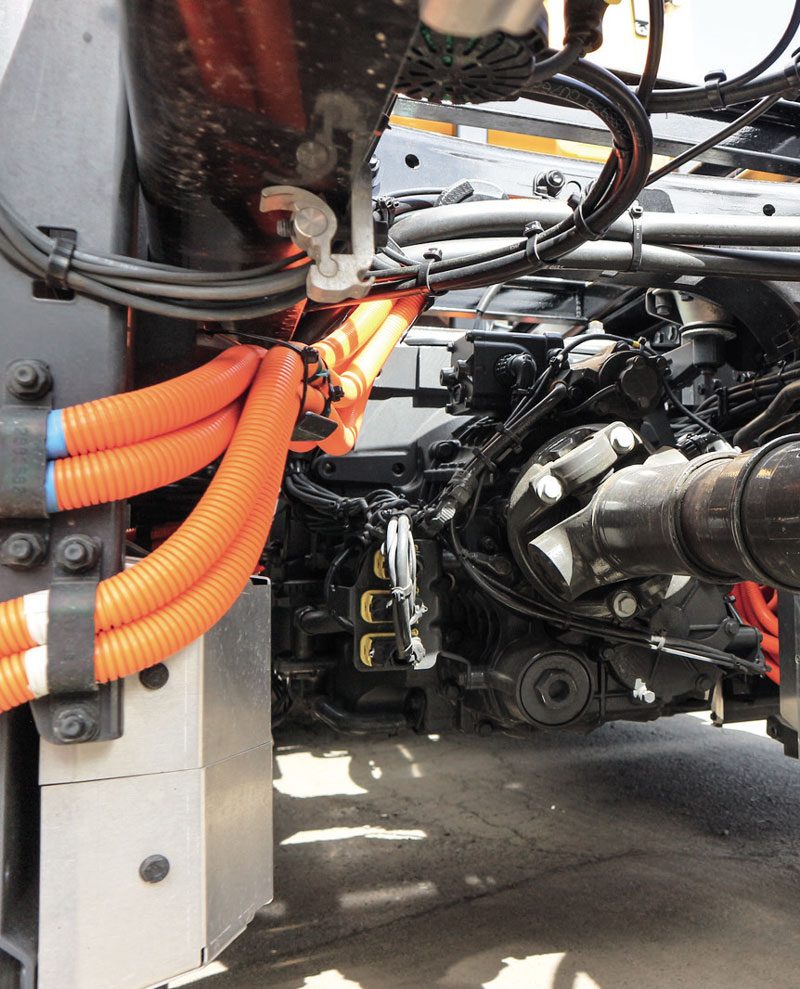
Doing the container shuffle
Our chaperone for the day is a familiar face. We first met assistant transport manager Mac Moradi when we jumped aboard one of Reliance Transport’s mirrorless Arocs models for the April 2022 issue. We couldn’t have asked for a nicer and more enthusiastic person to show us what the 25P could do. And just as well, as although he’s not the main driver on either 25P, Mac is responsible for approximately half the mileage under their wheels.
“I don’t really sit in the office looking at spreadsheets all day. I get out there and drive the trucks myself and see what the boys are actually doing,” he says as we climb aboard a familiar office space. There’s little going on in this cab to give the EV game away – in here, it’s everything you’d expect from a contemporary Scania.
Ordinarily, we’d wait for a new truck to have a fair bit of time on the road to allow both truck and driver to settle in and gel. However, the pressures of deadlines meant the 25P we’re aboard today has had only a month of operation, with much of that ‘experimentation’ – different drivers, different runs, when to charge, that sort of thing.
Nonetheless, it’s all go! Our first stop for the day is to drop off a 20-footer and a 40-footer at Container Repairs and Sales (CRS), then deliver a single 40-footer to the Onehunga depot, swapping it out for another and then back to Ash Road to collect a 20-footer so that we can deliver both to Container Co just around the corner… You get the picture – it’s a constant container shuffle, sometimes moving one, two, or three; some full, some not; from port to park to depot; and on and on it goes. As Mac quipped during our Arocs meeting, “containers are chaotic”.
But how easy the 25P makes it becomes apparent the moment we glide out of the yard. That’s what it feels like – gliding in silence. “You still hear noise from the air compressor, especially when you first start the truck. It kicks on and off with a whirr,” says Mac.
“Really? Oh yeah! I wouldn’t have noticed it if you didn’t say anything!”
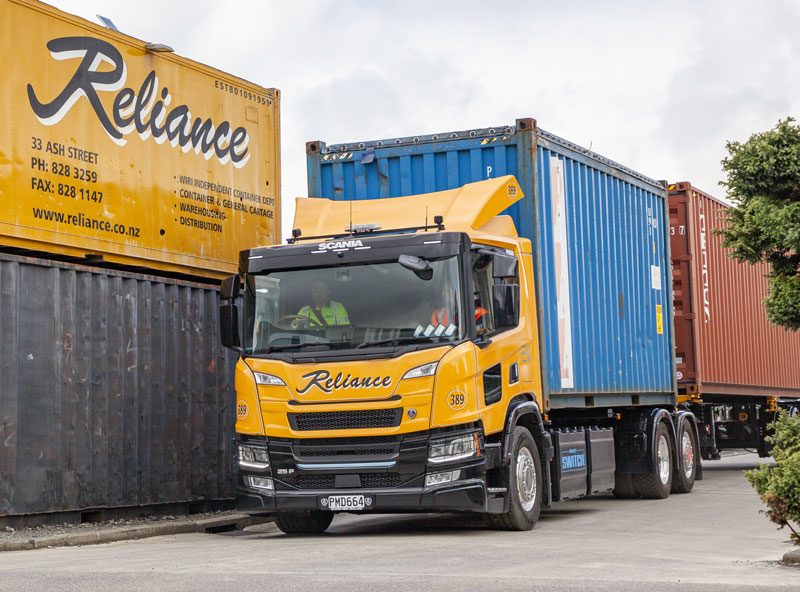
By the time we’re sitting at the lights to turn onto Wiri Station Road, it cuts out – and things get even quieter. As we make our way through the urban jungle, other trucks sound objectionably loud as they drive past. Sure, as speed rises, so do wind and tyre noise. But even at a full 90kph, the sound meter registered a 68db average. Normally, we’d expect mid-70s. Driving through town, you’re looking at 59db.
Mac interjects: “Hang on, I’ll shut off the aircon!”
Never mind, make that 56!
“The first time I drove it, I was like, ‘This is damn quiet’. You hear every single noise, the stuff you don’t normally hear with an engine running. It’s different, yeah,” Mac says approvingly and as though we’re having a normal conversation in a quiet room. Arriving at CRS, Mac explains he’d ordinarily have to shut off the engine to speak to the person at the window. “With this, it’s quite easy to sneak up on people, as they don’t hear you arriving!”
Trucks can spend a lot of time waiting around at container yards in queues to get to the gate, drop off containers and receive containers. Most often, their engines are running all the while. It’s a particular bugbear of Mark’s, but the nature of the beast.
“Mark asked me the other day what I think, and I said, ‘The beauty of these is I can leave the truck running, and it’s not idling away, not using any fuel while waiting for a hoist.’ Diesel trucks are idling all the time,” Mac says as we join the queue to offload.
Waiting allows us to discuss a nifty feature that Fruehauf built into its skele design – the pneumatic twist locks. Mark would later explain: “I approached Fruehauf with the idea of building them into our new container gear. We originally built a trailer in 2019 with Clark Engineering in Tauranga that featured automated twist locks, but together with Fruehauf, we have developed a Mk2 version, which is working well.”
Their design and operation are simple, elegant and easy, with the whole process conducted by three simple switches – two wired into the Scania’s accessory switches and the other the electronic park brake. The driver simply selects ‘unlock’ on the lock/ unlock rocker switch, and when applying the park brake, the twist locks all unlock. They automatically lock as soon as the park brake is released and the vehicle starts moving. The driver can select ‘lock’ or switch off the system to keep the locks permanently locked. The third button is a 20/40 button, which activates the respective trailer lock sets.
“Normally, I’d be jumping out to unlock the twist locks. This makes you lazy!” Mac says with a laugh. Indeed, the one physical aspect of container transport has successfully been eliminated.
“At times, the loader drivers look at the twist locks and think they’re still locked. I’ve had some get upset with me for not having them unlocked!”
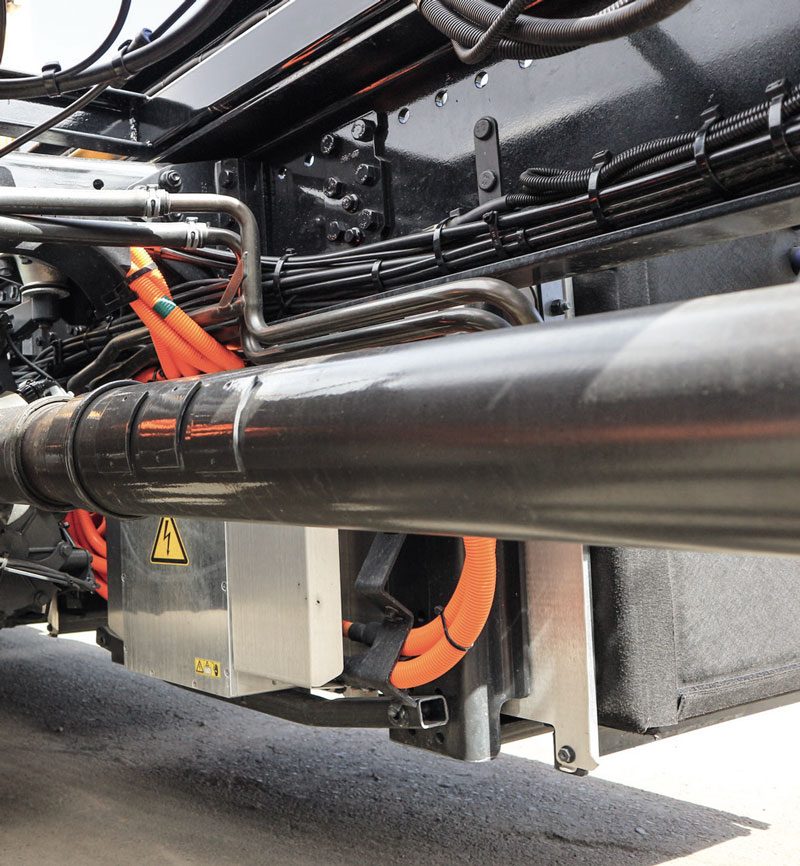
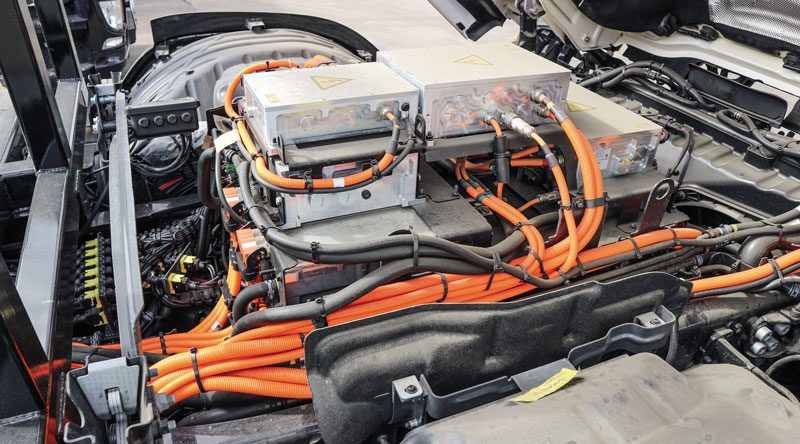
Go, stop, charge, repeat
Saying there’s no better place in New Zealand than Auckland to prove the merits of a vehicle in a metro operation might be stating the obvious, but that’s precisely where you want to do it – in the most intense environment available. And so far, the 25P hasn’t put a foot wrong.
The ride and handling are like any other Scania on full air suspension – sublime. The unit manoeuvres around the city streets and tight confines of container parks and depots like any other in the Reliance fleet. By all accounts, it took a bit of doing to get the configuration right within the confines of VDAM (see, The proof is in the pudding, page 33), something that will need to be done on a case-by-case basis until legislation catches up.
It’s handy too that it features Scania’s Blind Spot Warning that indicates, via lights in the A-pillars, passing vehicles when changing lanes or vehicles in the blind spot when turning corners. The feature is part of Scania’s Advanced Driver Assistance System (ADAS), which also includes the likes of lane-keep assist and automatic emergency braking.
With Mac behind the wheel, the 25P zips around the city streets. It’s quick off the line despite the restricted acceleration, accelerating up to 50kph in one fell swoop with the set gear change – barely perceptible – at 30kph. Even building speed to merge onto the motorway requires only a three-quarter application of the throttle pedal… The energy metre in the instrument binnacle – in place of a conventional tacho – is barely fussed. It’s truly impressive and belies the quoted output figures. Apples and pears, remember – you can’t base it off what you know with diesel.
If the driver needs to get going in a tricky situation or without weight on the drive axles, they can engage the diff lock and load transfer (tag-axle lift).
Slowing down is aided by five-stage regeneration, which works just like a conventional retarder via the left- hand wand on the steering column. Stage one applies the regeneration with a light press of the brake pedal before the service brakes start to bite. Mac suggests stages two and three are strong enough for most slowing situations and briefly demonstrates stage five, which strongly retards the 25P’s progress. As for the effectiveness of regeneration, with sensible anticipation of traffic flow you can see the battery charge percentage ticking up.
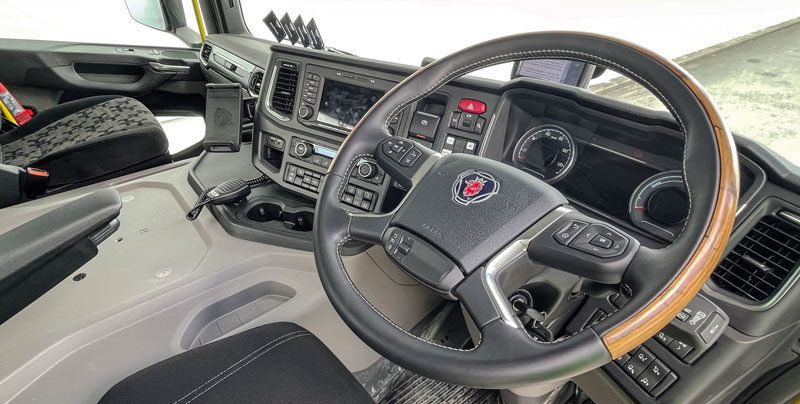
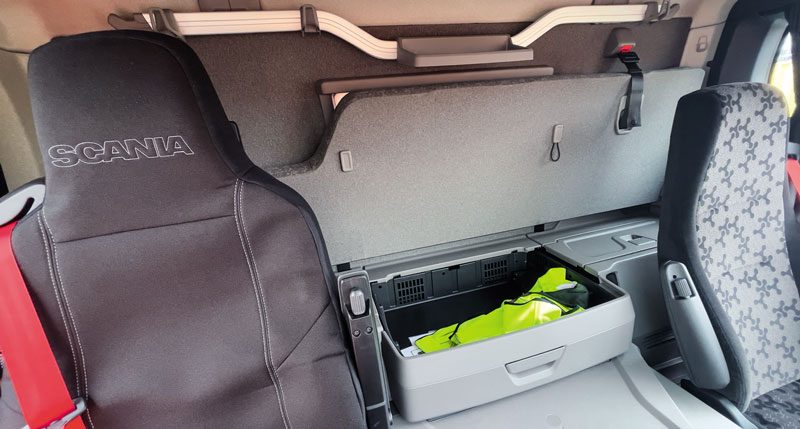
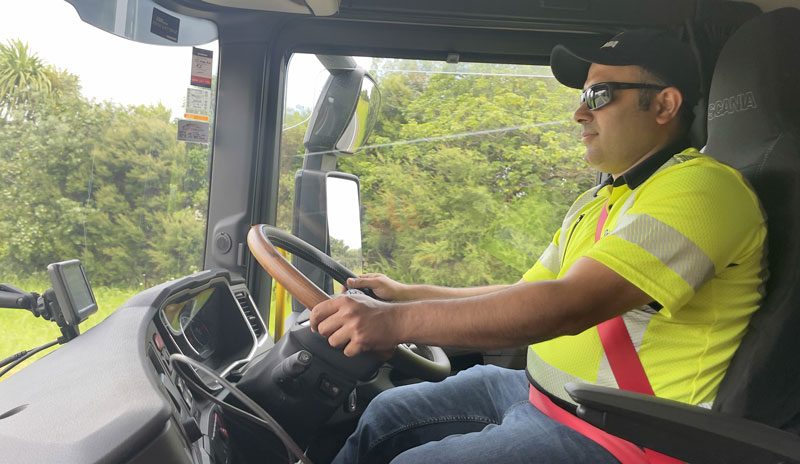
But he’s quick to point out that driving the 25P requires a different approach to a conventional diesel. “It’s not like a diesel truck that you can just gun around. But you learn quickly, and once you have some time behind the wheel, your mindset changes and you start to get the best out of it.” To ensure that, the drivers get their own information via the Scania Connected Vehicles Portal Fleet Management System so that Scania and Grant can monitor how they’re getting on and build data on the new trucks’ performance. Drivers can also check the trucks’ vitals, such as range and charge status, via the Scania app on their phones.
Speaking of which, let’s address the elephant in the room – charging. Grant explains that the drivers are required to head to the Onehunga depot and plug into the 120kW charger during their half- hour break. “On the 40kW charger, we can add about 15% in half an hour [it takes three to 3.5 hours to charge from empty to full]. The 120kW charger adds 40%.
“A 120kW charger at both depots means we can start double-shifting it. Perhaps the day driver finishes at 5pm, plugs in and the next driver starts at 6.30pm with a fully charged truck. He’d knock off at 4am, and it’ll be fully charged by 6am. Perhaps it might only be two nine-hour shifts. We won’t know until we get up and running and do it,” he says.
By the end of day two (in all the excitement, we forgot to reset the trip computer on day one), we return to Ash Road with 33% battery capacity, or 90km, remaining.
“When we first drove the truck, I wasn’t sure, watching the range drop and drop. But when you’re out and working, it does okay,” Grant says.
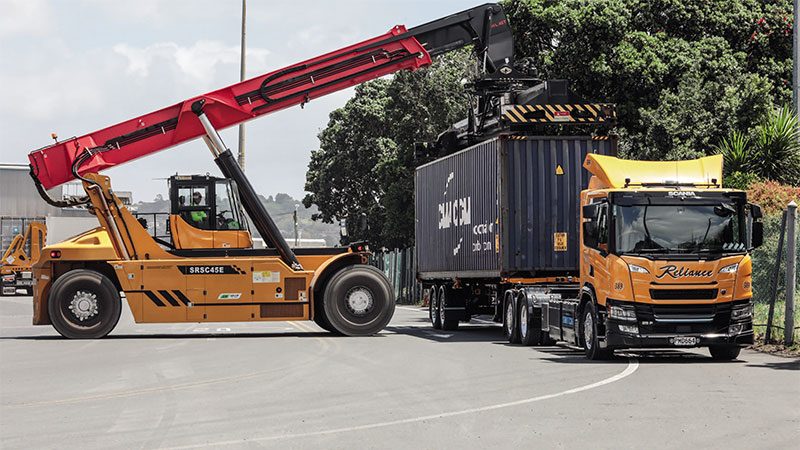
Setting the example
The biggest privilege we get from producing this magazine each month is being granted access to the offices, yards and cabs of the companies that keep New Zealand moving. We never fail to learn something new, meet some brilliant people, and admire what it is that really makes the road transport industry of New Zealand. It is the same with Reliance Transport – it’s a company putting its money where its mouth is and diving into the most sustainable, efficient future it can create for itself.
“There’s risk, but that’s where you need your customers to buy in for the ride. And now that the trucks are here, those conversations are starting,” says Mark.
“Up-time and maintenance are great. CPK in operation is better. Yes, there’s a capital cost – but there’s co-funding from EECA, specific finance from some of the banks, and RUC exemption. We’re not driving to Wellington – we’re a ‘last-mile’ metro company just like the majority of the trucks in Auckland. A big part of the market can access that and get these trucks on the road. It’s not a hard process – the opportunity is there. The cup is half full,” Mark says.
“I expect we’d get more than the four years out of these trucks, maybe eight. That changes the economics again, too,” Grant adds.
“Competing against another metro container business with electric trucks would keep me awake at night,” says Mark. “I think there are others in the industry going, ‘Ooh, shit. What are those f@&kers up to?’”
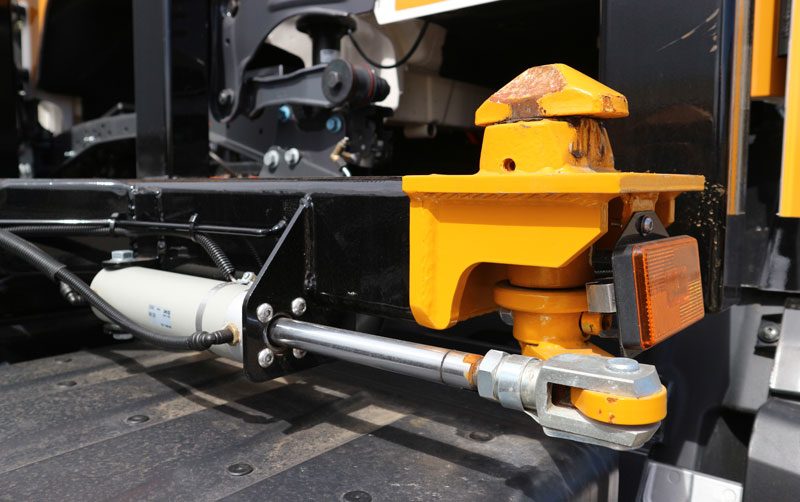
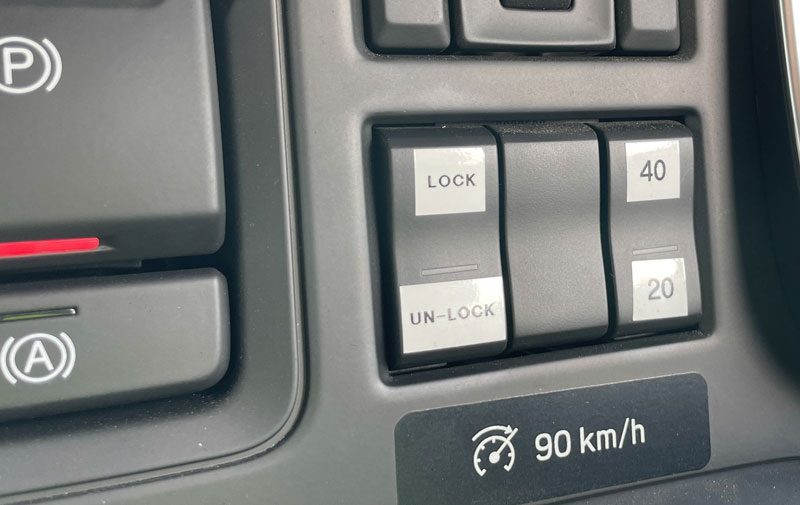
Mark and Grant have put absolute faith in Scania. “By now, all these first-generation electric trucks have had a long and intensive development since they first appeared half a decade ago. It’s the same as the cars. We bought Nissans because we know they made a ‘million’ of them. We know Scania will have mitigated any issues.” So far, the 25P is living up to that expectation, and we’re excited to see more of these find a place in the market and begin to do ‘real work’, as Mark put it.
With OEMs suggesting cost parity with diesel in the second half of this decade – just a couple of years away – investigating how these alternatives could fit into one’s business is undoubtedly good due diligence. What Mark and Grant have decided to do with Project Switch goes beyond; it is a commitment, pure dedication.
Good on you, men. We can’t wait to see what returns come from Project Switch and can only look on with admiration.
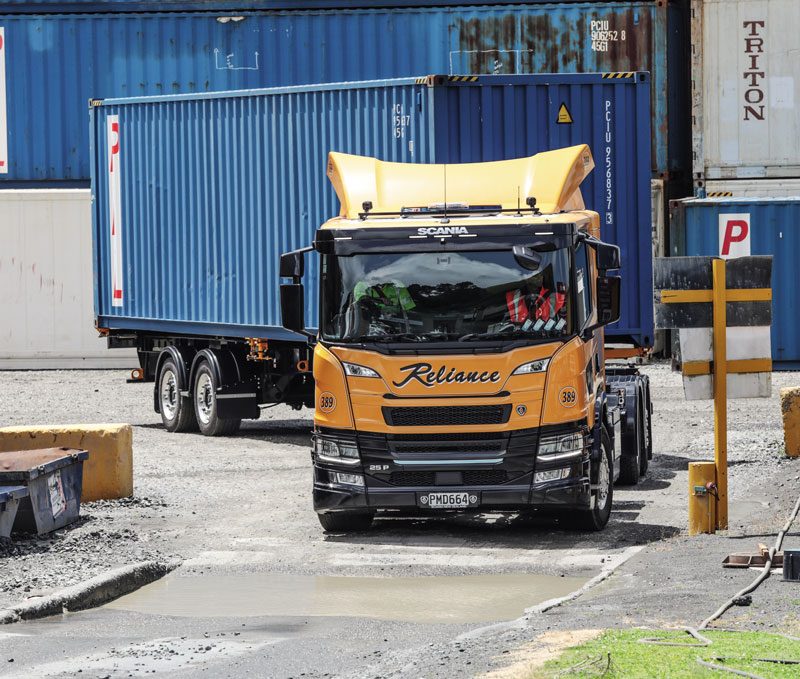
Quick reads from Test
Read more
The right man for the job
0 Comments29 Minutes
Legendary ambition
0 Comments36 Minutes
Hard Fought!
0 Comments40 Minutes
Postal Trifecta
0 Comments29 Minutes