Roadmaster knocks it out the park for Austin
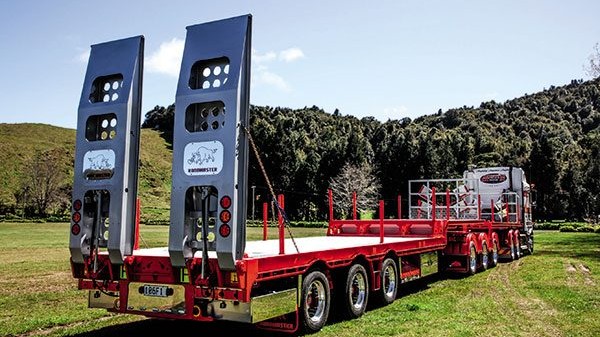
Years of experience in Australasia and the need for versatility led Austin Transport to the doorstep of Roadmaster Trailers for this ground-up, customdesigned B-train. And it’s fair to say, the trailerbuilder has knocked it out of the park.
Rotorua-based trailerbuilder Roadmaster has designed a bespoke flat-deck B-train unit for Austin Transport, and with just one look at it hooked up behind Austin’s Kenworth K200 fleet No.28, it’s clear it means business.
It is a custom, one-off build from front to back, designed and fabricated by Roadmaster to Bryan Austin’s specification. Austin drew on his experience driving trucks in Australia, picking up on some of the ways they do things there. “Like the fold-down on the step in the gooseneck,” he says. “It’s a lot of little things I’ve seen and used.”
According to Aaron Forde, Roadmaster area sales manager (lower north, upper south), the unit was designed for ultimate multifunctional use. “This particular trailer can do the vast majority of most of Austin Transport’s work now. It can cart pretty much anything,” says Forde.
The wedge ramp is just a fold-down away. Top: 3.6m-loading lift ramps have their own hydraulic Honda power pack.
“We thought we’d design it with ultimate versatility as a trial, as we cart a mix of freight nowadays, from machinery to timber. We wanted something we could load either way, no problem, ” adds Austin.
With 3mm C/10 steel decking, the lead trailer measures 6.1m, and the rear measures 12.3m and can be hooked up separately as a semi-trailer. Suspension is Hendrickson ZMD air suspension, axles are Hendrickson ZMD, and Hendrickson was also chosen for its TyreMax inflation management system. Wabco EBS controls the braking with a Wabco Smartboard unit fitted per trailer. Wheels are Alcoa alloys in 22.5 10-stud on the lead trailer and 19.5 8-stud on the rear trailer.
“The front half of the unit is set up like an Aussie unit with 22.5 tyres and rims. That matches the Kenworth, gets better tyre wear and handles better, according to Bryan,” Forde says.
‘As many tie-downs as possible’ was part of the brief.
900mm stanchions, adjustable electric wide-load boards front and rear.
He adds that one of the main requirements of the build was to have as many tie-down points as possible. The trailers feature pressed-steel coaming rails, certified rope rails with chain hooks on every cross member and twist-lock beam.
There are two in-deck chain boxes on the front trailer and four on the rear, and two removable 1200mm RHS framed headboards to fit the fronts of the trailers. ISO twist locks allow for 20’ and 40’ containers.
In-deck chain boxes, removable 1200mm headboards and robust bridge blocks for those machinery loads.
Wash and sanitisation stations are a necessity in a post-Covid-19 world
Each trailer has two 50kg alloy toolboxes and one large steel under-mount bearer box with alloy doors on the rear trailer. There’s a handwashing station on the front trailer. Lighting is LED.
The front trailer features six 900mm stanchions, the rear 10. The rear trailer step deck features a manual lift over wedge ramp, making loading vehicles easier, as do the 3.6m hydraulic loading lift ramps at the rear with their own Honda power pack.
That’s the basic spec, but Austin’s not saying much more. “It’s pretty unique for New Zealand. But I can’t tell you too many secrets to put in the book,” he laughs.
Eye-catching combo indeed.