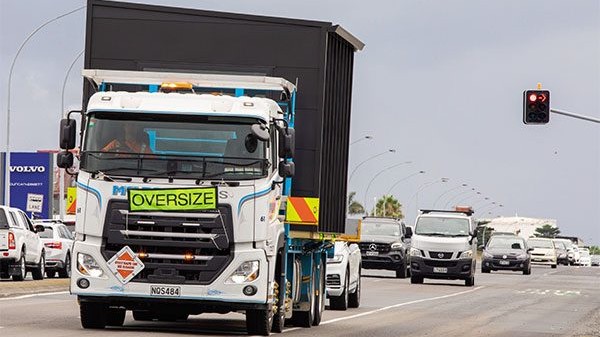
UD’s platform Quon carved out a new niche for Japanese trucks when it showed up in early 2018. UD said Quon retained the traditional attributes of trucks from the Land of the Rising Sun and combined them with safety and productivity systems once the preserve of Europe’s big names. Four years on, has Quon blazed a trail or burned some bridges?
For the average person, lifting stuff up high, especially heavy stuff, and then putting it down somewhere else is always a bit nerve-racking. Mixing Newton’s laws with lifting contraptions made of steel, tubes of pressurised oil, valves, ropes and hooks requires intelligence, education, calmness, and – let’s face it – nerve.
Hmmmm? Let’s just halt everything for a ‘mo’. Not sure about that last attribute anymore.
McLeod Cranes and Hiabs in Mt Maunganui has its roots in a company founded by local crane guru, the late Curly McLeod. For the past decade and a half, it has been owned and run by Curly’s sons Peter and Scott and their cousin Phil Hutchinson, and has grown immeasurably in their tenure. Interestingly, the growth hasn’t come from anything as tacky as rate-cutting, but rather an unwavering adherence to culture, founded on intelligence, education and calmness delivered via practical and respectful systems and processes. You’ll notice I omitted ‘health and safety’ in the list above, even though the McLeod crew tell you from the get-go it’s the cardinal pillar. I left it out because soon after arriving and interacting with the crew, you gain an awareness that it’s not there like a cheap porch on an expensive house, banged on because you had to, it’s hardwired in the double helix of the company’s broader DNA. Businesses are like cranes; get the foundation and set-up right, and you don’t have to worry as much about flying by the seat of your pants, in other words… nerve.
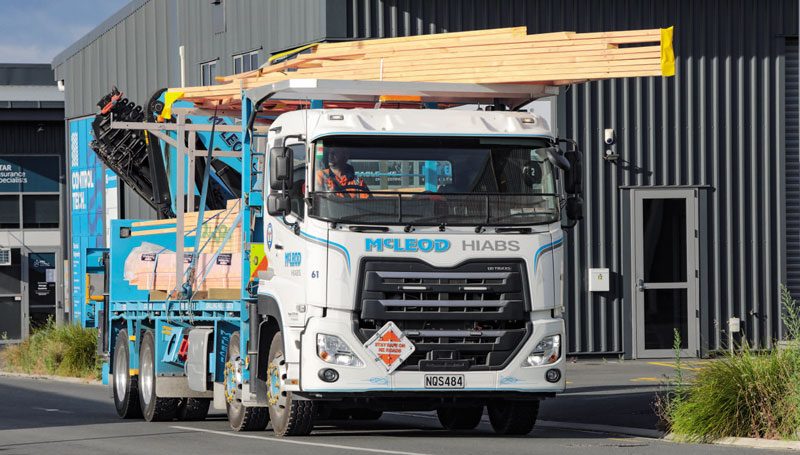
Aiming for a culture such as McLeod’s is common; delivering it is not. Too often, the intent is ankle-tapped by a perception on the ground of disrespect for grandfather IP, experience and general life skills. Not so here. An initial look at who’s pulling the levers of the McLeod business starts to give its secrets away. All three owners bring to the firm a vast practical yet systems- driven background. Scott is ex-Navy, qualified in systems and electronics. Peter is a structural engineer who has worked around the world, managing the lifts on what you might call ‘mega-crane’ operations, primarily in the oil and gas exploration industry (look up Saipem 7000). And Phil is Mr Transport, having spent his life before joining the family business in two of the nation’s culture congregations, Mainfreight and TR Group.
Interestingly, the phrase on the rear of their plant, ‘Good bastards!’ is a tip-of- the-hat to Curly, reminding one and all that relationships are paramount at all levels, and modern processes and culture are not at odds with traditional values.
With more than 200 pieces of kit across four divisions (Crane, Hiab, Transport and ATF) and five depots spread around the Bay of Plenty and Central North Island, McLeod’s is a significant and complex operation. It can furnish its customers with everything from an Iveco Daily with a crane that looks like a hydraulic toothpick, to a behemoth with a 74-tonne tare, capable of lifting 350 tonnes, requiring an entourage of ‘roadies’ to cart it’s accoutrements of trade – counter-weights, extra jibs, extra hooks, all that stuff.
“It’s an interesting business, there’s no doubt about that,” says Phil Hutchinson. “Not just the work either; there’s occupational cultural crossover. Crane people are not truck people and visa- versa. They’re completely different breeds. Crane people are used to one job potentially taking days by the time you include setting and breaking down the gear. In that, there’ll be spurts of intense activity and concentration, then maybe periods of not much. The truckies, on the other hand, like to keep moving – next job, next job, next job. It’s a cool place to work.”
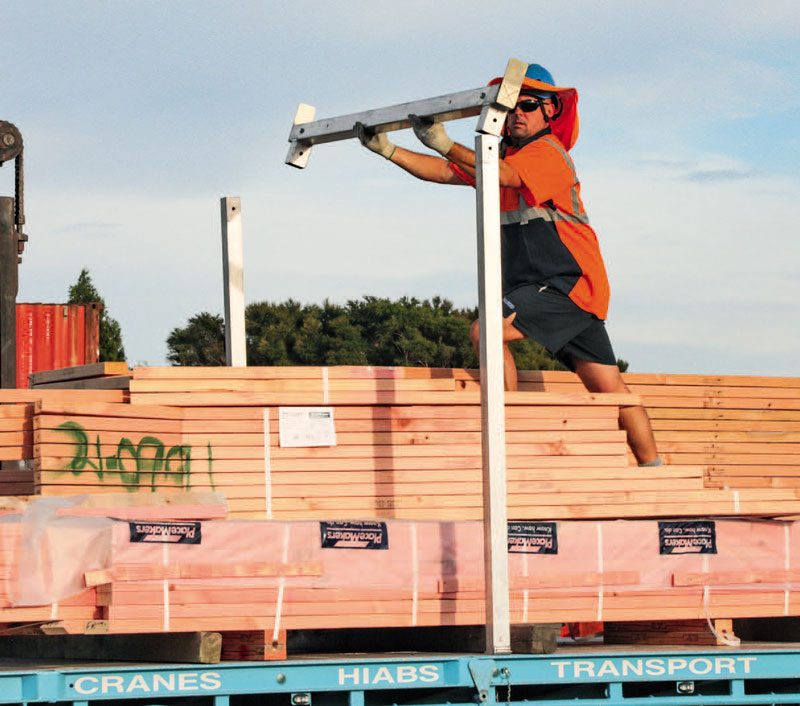
All trussed up
We meet driver Brett Meier at McLeod’s Truman Lane headquarters in Mt Maunganui right on dawn. Brett’s been with the company for almost six years and is currently transitioning into a training role. When we caught up with him, he’d been covering for staff away on annual leave, including the regular driver on the UD, Ryan Ward.
Brett had been briefed on our arrival and gave us a rundown on what we would be doing as the day progressed, as well as the dos and don’ts of life in and around the facility.
The Truman Lane depot is currently in growth mode, with expanded yards, buildings pegged out, and the first signs of earthworks. As a result, a cone path was marked out across the workings between the existing yard and partially developed fleet parking area next door. Brett gave us directions on navigating our way to the UD, currently parked over there among its fellow asset- register workmates.
On reflection, our first interaction with Brett was an interesting experience. Aside from the fact he grew up in South Africa – with all the inherent forthright pragmatism that brings – his low-key but comprehensive instruction demonstrated how effective good, well-thought-out, well-delivered health and safety systems can be. What we’d essentially had was a toolbox/tailgate/lift-plan meeting – whatever label you want to give it – yet it was barely recognisable. It wasn’t demeaning. He was engaging, simply setting the scene for what would follow, and how to accomplish the first bit – i.e. finding the truck without wandering aimlessly around a busy yard you didn’t know. You might call it epiphany No.1 (similar revelations were to happen several times throughout the day). It’s also worth noting at this point that Mr Meier is the real deal, having done things such as cart cotton in the African bush in a former army truck with no concern for GCMs. He is a genuine graduate of life’s experiences and ordeals.
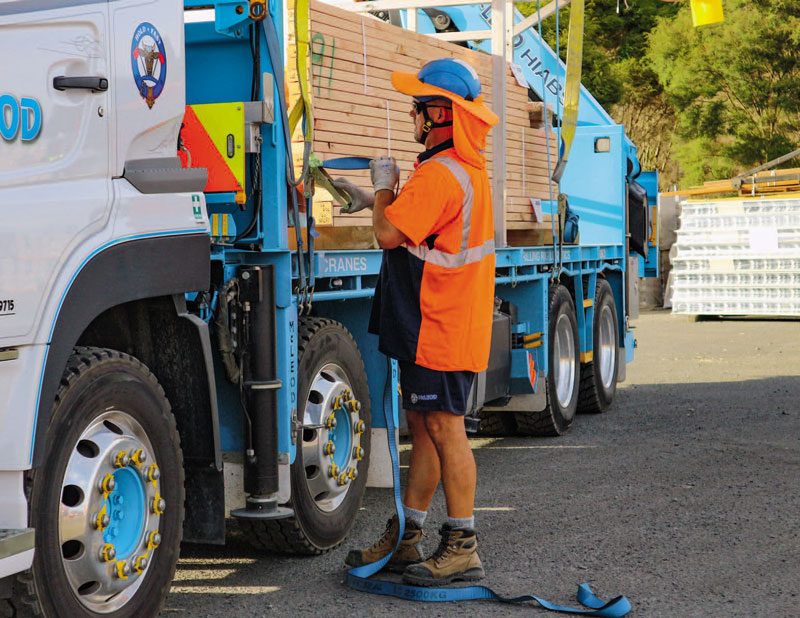
On arrival in the fleet park- up yard, we get the first look at the reason why we’re here, the company’s new UD Quon CG32.460 8×4 rigid and Palfinger knuckle-boom crane, resplendent in fleet colours – including the big ‘lifty’ thing on the arse. That level of detail alone speaks volumes. It’s one of a pair of new UDs to have driven in the gate recently, the first two of eight that are on their way. The reason McLeod’s has written the order number for the UD would surely warm the hearts of not just UD New Zealand but high offices within UD’s strategic think- tank.
“We’ve traditionally bought Hino product, with a Fuso in the mix too, but UD’s latest platform Quon with the safety and productivity systems was perfectly aligned to us,” says Phil.
Brett carried out the pre-start check on an app-based system called Prestart. “Ryan’s a bloody good operator,” says Brett, “Absolute top young bloke. I can tell you there won’t be a thing out of place on this truck.” While he started checking off the list, we went for a stroll around the truck.
The first thing that was blatantly obvious is that, like the Lilburn Kenworth in the December/January issue, this completed machine was designed by crane people, with a high emphasis on procedure. The more you walked around it, the more you saw. There were process checklists for the pre-start, and no shortage of kit to help do the job as simply as possible. During our inquisitiveness, company trainer-driver auditor Kevin Scharvi walked over to see who these scoundrels wandering around the new gig were. He showed us many neat things, such as the cab protection frame that stopped something long and wayward clunking the roof – which is also fitted with pneumatic rams so mechanics could easily lift it up and out of the way for the cab to be tilted. Then he demonstrated the system for safely accessing the deck, comprising pull-out pegs that slot into the coaming rail for use as grab handles. Also, every mudguard on the truck has a wee drop step, so you can pretty much get up on the thing at any point. On the subject of gear; strops, footpads, cones, chocks, ladder, broom, chains, straps, slings, spreader bars, pallet forks, dunnage, and up-stands – they’re all there. It appeared to be a one-stop, one-person, ‘crane-it’ shop … on wheels.
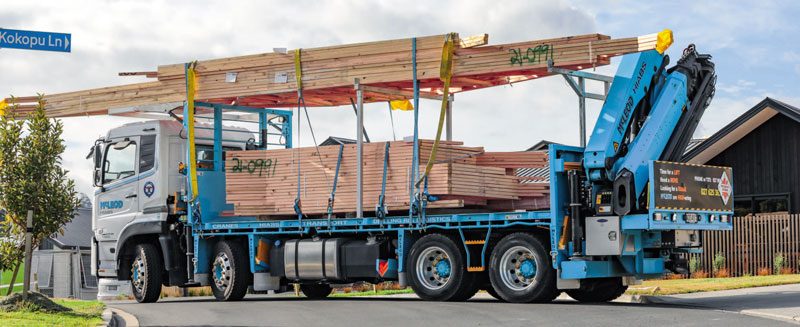
“You can lose a lot of time and waste a lot of money coming back to the depot between jobs to get the gear you need for the next,” says Phil later. “We decided to rig the trucks as best we could, so they were able to motor off in the morning and do whatever they needed. Yes, that came at a slight tare weight disadvantage, but the productivity benefits outweighed that.”
Check done, the first stop was around to the main yard to load trusses and timber for a building site in Ohauiti near Tauriko. There’s no question the additional yard space will be welcome when complete. Truman Lane is a busy place with product awaiting delivery, cranes, trucks on the wash and in for maintenance, and the company’s container transition and devanning acility humming away over in the corner.
We’re politely despatched to the safe area and given a realistic and usable boundary from which to observe and take pictures. Epiphany No.2: McLeods is not a company imposing ‘teacher’s pet’ levels of safety to prove that they’re better humans than even the best humans. No, the guys just want you to be safe, according to the mandates of their health and safety systems. We weren’t imprisoned to a spot on the ground at an impossible distance, but rather given a boundary and encouraged to use it. It looked for a moment like common sense, even though that’s not actually a thing anymore.
Brett hatched a plan with the fork hoist driver as to how the trusses and timber will best go on, and off they went.
No one at McLeod’s looks to be in a rush. There’s no haste or mayhem. The fork hoists and people idle and glide around, yet trucks arrive and leave constantly. If you’re not rushing, you always have time to stop and look both ways – surely the root of personal preservation? You get the impression if you were caught roaring around in a truck or spinning the fork hoist wheels every time you moved it, you’d be fired from a giant cannon in the general direction of Mayor Island.
“What a great place to teach young people,” I thought. The good news on that one is that they do. While kids can’t be allowed on-site, the business has an active cadet scheme, running in several divisions all the time. And just as well, it’s such specialist work that taking a level of responsibility for your own HR future is a no-brainer.
Once that mission was over and the fork hoist motored off, Brett ushers us over and we have a good old natter while he secures the load. Job done, he has the obligatory walk around to ensure the bits are secure and toolbox doors shut.
“I’ll drive out at walking pace with the hazard lights on, and you guys walk in behind the truck until we’re clear of the yard. I’ll see you out front.”
Too easy. There needs to be something written about this place.
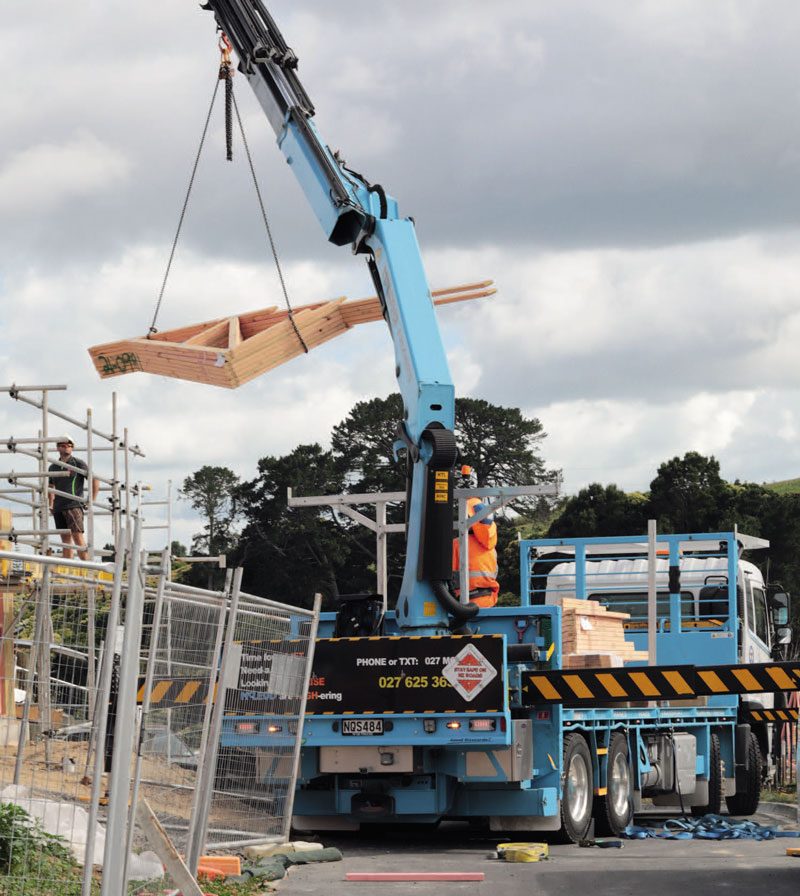
‘Oh, how easy’
Brett motors through the city, and the UD easily keeps pace with traffic. Tauranga is exploding in all directions, and the roading infrastructure is coming under immense pressure in places.
The last time we had a look at the Quon was November 2018. That was a truck owned by Charter Transport in Christchurch, bought to exploit the one-size-fits- all philosophy, working in bulk metro distribution, with the occasional line-haul blat to the far south, and even the North Island. The McLeod machine is the same in many ways. While much of its work is in and around the wider Tauranga/ Mt Maunganui metropolitan and rural hinterland, it must also be ready to hook on a trailer and head a little farther afield. For this reason, the company chose the biggest spec for the Quon, with the GH11TD 11-litre, Euro-6 motor outputting 338kW (460hp) at 1800rpm, and 2200Nm (1623lb/ft) of torque at 1200rpm. As we’ve said before, the 11-litre brigade are their own thing, and while the numbers look a little modest in today’s 3000Nm world, there’s a bit more to it. Torque does peak in the GH11, and we mean peak. However, power hangs around for a bit, roughly hovering near its peak from 1500rpm to 1800rpm, give or take 7kW (10hp). At 1600rpm, torque’s still at 2000Nm (1475lb/ft), and they pass at 1675rpm with power right on max and torque about 1850Nm (1364lb/ft). What’s that all saying? Well, it’ll be a little honey between 1500rpm and 1800rpm and tenacious back to 1200rpm, even happy to crest a hill at 1000rpm – all at weights befitting the truck, mind you. UD sent a clear message with the Quon when it binned the 13-litre, so if you’re going to put nine axles under one and head for Pegleg, the Hope Saddle, or Gentle Annie, take a thermos and have a few podcasts downloaded. In applications like this one, however, you get comments like this from Phil Hutchinson: “The UDs are already proving their worth on runs to places like the Coromandel, with significantly better trip times on account of the ‘torquiness’ of the motor, and ESCOT AMT.”
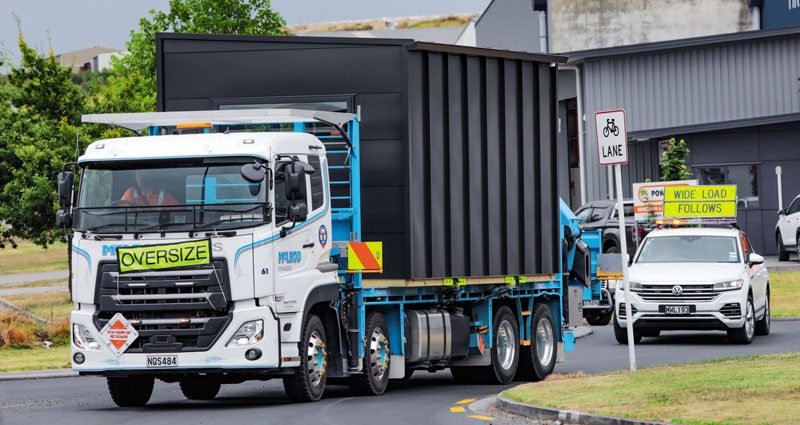
What really allows the GH11 to punch above its weight is that ESCOT-VI 12-speed AMT. Being a Volvo platform truck, we all know its breeding line, and its beautifully smooth characteristics, slick shifts, and on-point tuning set the whole driveline up for success.
Out back is UD’s 20-tonne hypoid rear end on proprietary eight-bag ECAS, and forward is UD’s 13-tonne Reverse Elliot I-beam front axle set on parabolic leaf springs.
The street where our consignment would live once constructed was the urban equivalent of the Folies Bergère dressing room, with houses everywhere in various stages of build. Of course, the streets and corners are designed for the suburb’s finished state and getting trucks and trailers in and around the joint can be a show in itself. As we were to find out later, the UDs will take a thrashing in their life, with tight lock to lock manoeuvring, kerbs, and crappy site tracks all part and parcel of a crane truck’s day.
Brett sought the clearance of the various building gangs further down the street to block it off for an hour so he could unload. Cleared, positioned, and stabilised, he gave us our boundaries again, then woke up the Palfinger crane, which made easy work of the task at hand.
“We run a job despatch system called vWorkApp,” says Brett. “We take photos of all the lifts and whatever was delivered, and then it logs the pictures against the job in the system. Often, there are boxes of fittings and things, and building sites are very open places, if you know what I mean.”
Roomoval
The next mission was an over-dimensional mini- room from The Little Village Company, just down the road in Tauriko, for relocation to its new owner’s home at Mt Maunganui. The pick-up point was tucked around the corner at the end of a commercial right-of-way flanked by other busy enterprises. Brett backed in, and after a couple of light vehicles were moved, he was all go. As anyone with a crane truck will tell you, ‘Oh, while you’re here…’ is a phrase often heard. Time was not against us as we’d had a cancellation for later in the afternoon, and so before we loaded our condo, Brett moved another small building the crew was working on.
With a slight delay while our consignment was prepped, we decided to investigate both ends of the truck, beginning at the rear.
The Palfinger PK33002-EH F Power Link Plus is very much the crane equivalent of the truck, meaning a max- utility type of arrangement. While it obviously contributes significantly to the overall tare of 18,090kg, it’s not that big a lump that it renders the rest of the truck useless. Brett’s still able to plonk around eight tonnes on the deck, which when you look at the truck’s work profile, covers a lot of jobs. Our hut, while dimensionally big, only weighed two tonnes.
Any knuckle-boom crane that can’t deal with a 20’ ‘can’ in 2022 is going to be somewhat limited in terms of utility, and the 33002 easily romps in on that one, as well as being burly enough to plop 1080kg 19m away. Pace that out and you’ll be impressed.
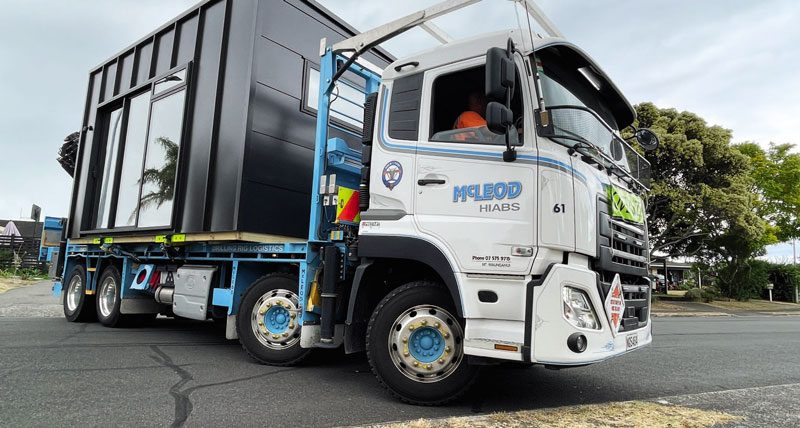
LED lights, perched out on the end of the stabiliser legs blinked away, adding another layer of awareness and safety. While we waited for the crew to put the finishing touches on our load, Brett explained there was a ‘slew’ (sorry – had to be done) of conditions on a crane’s ability at any given site; grade, substrate, arc, the load itself, even weather. “Everything has to be assessed and considered.” Thankfully, the operator is not in it alone, and the Palfinger has a plethora of failsafe cut- outs if it thinks its ability is being stretched.
“We run a mix of both Palfinger and Fassi cranes in the truck fleet,” says Phil. “Both are great products, and we have good relationships with both suppliers.
“In terms of decks and trailers, we run both Roadmaster and Domett in the semi and full trailer fleets, some new rigid units are coming fitted up with decks ex-the supplier, and we use both Truck Works Mechanical and Engineering here at the Mount and Clark Engineering. Having the builds occur right on our back doorstep allows us to project manage them much more closely.”
And now to the front…
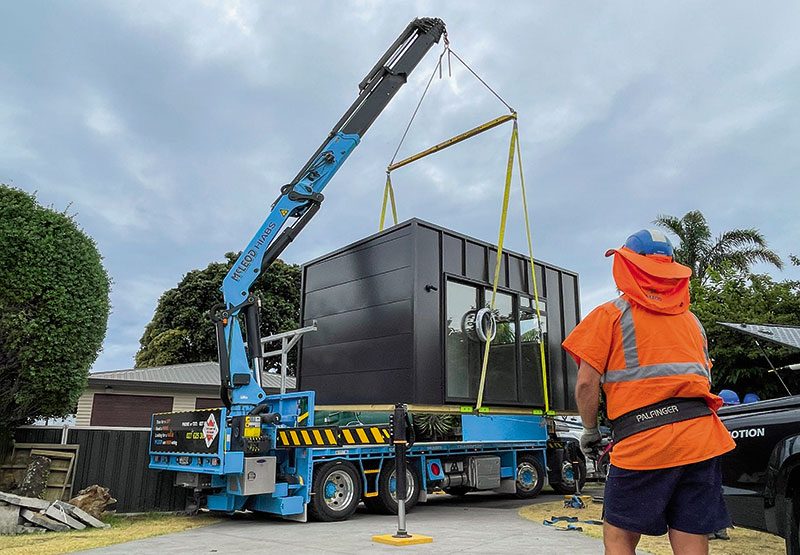
Universal Décor
Of course, the challenge cab designers face with trucks like the Quon is the breadth of application their designs will encounter. The Quon and its ilk are not pitched at certain genres of transport in the same way others are. Take Kenworth’s T659. The ringers in Bayswater’s cab design department never really had to consider how well their impending creation would cope with the rigours of last- mile metro delivery. In the event someone did hand over the rubles for a ‘five-nine’ with the intention of deploying it into such applications, it’s the customer who’d be looked on as being a wedge or two short on their artillery hub.
That’s not a luxury the poor buggers responsible for the Quon’s cab get. You can find the Quon cab in the midst of last-mile duties, delivering logs to the port, as a bath- tub tipper combination, carting cows, swinging boxes, delivering trusses to a building site, and ploughing through the night on the linehaul arteries of the nation. The point of all this is that you can’t get too nit-picky when assessing it for any one task. You have to look at it from the viewpoint of does it make the bulk of the punters happy for much of the time?
The Quon’s a classic forward-control jobby, meaning the good helmsperson’s not sitting right over the top of the front axle and engine à la K200, 9870, and the late Freightliner Argosy. There’s a good chunk of cabin (almost 1400mm) ahead of the lead- axle centre, and because having a flat floor was never in the design brief, it’s able to sit lower, similar to last month’s CF530 at Rural Transport. Being of Japanese origin and therefore unlike the DAF, there’s no desire to optimise the cab space that is left, instead filling the engine tunnel with all sorts of extraneous lockers, consoles, and caddies, that are always hard to keep pristine if you’re ‘that person’ – which many truckers are. Yes, it aids in addressing the lack of storage that made us grizzle a bit about the DAF last month, but this is not the solution either. As many of you will know, it’s my biggest beef with Japanese truck interiors.
Anyhow, let’s start by getting in, an easily effected operation. Like the DAF last month, the UD has an A-pillar grab that profiles the dash end. It’s absolutely the only way to go in our view, with a section of handle that suits the reach of every human form. There’s another wee handle on the B-pillar, but that’s a bit superfluous, maybe. Two feet on the steps and the big A-pillar handle will tick all the three-point requirements. Three nicely cascaded steps followed by an inward swing of the chuff and you’re sitting, looking out of the windscreen, ready to win at life.
It’s an encapsulated fit in the business seat, with plenty of room to move within the bounds of that confinement. In the McLeod operation, Brett or Ryan may find their driver’s door millimeters away from a fence, hedge, or brick wall requiring them to alight from the left-hand side; the inference being encapsulation may well be a pain in the arse, resulting in the odd scratch and scuff on the hard plastic surfaces of the cab’s central environ. If it were mine, I’d have a big old blanket or towel ready to lay over it all.
Focusing on the workstation and surrounds for a moment, there’s the usual form factor of a two-gauge binnacle split by vehicle and driver diagnostics. On the right of the binnacle are a pair of switch banks housing traction aids in one cluster and hill hold and idle controls on the other.
To the left there’s an integrated wrap in perfect design unity with the binnacle, with communication, infotainment, climate, and a couple more switch clusters. In the McLeod machine, there are more switches than you’d find in trucks bound for more mundane existence due to the crane hanging on the rear and all that goes with that.
There’s a smart wheel accommodating Traffic Eye cruise control and Eco-off functions on the left, and menu navigation on the right. The left-hand column wand deals to wipers, hazard lights, and the four-stage auxiliary brake, and the right lights and indicator.
Interestingly the adjustment for the big and well-placed mirrors is low, on the right- hand end of the wrap. Though I’m no fan of half the dash controls on the driver’s door sill, it is the place for mirror controllers in 2022. However, Japan builds trucks aligned to the lifestyle of her native folk first and foremost, so in the Quon, you’ll find the window controller and an ashtray in that thar location. The shift controller for the ESCOT-VI is right there on a tower to the driver’s left with a definite family tie to the I-Shift’s handle. Behind that in the same well is the park brake, to the left the well is the cup holder, and fanning from there the start of the nooks, caddies, and lockers.
There’s no question UD lifted the bar on fit and finish in a Japanese truck when the new Quon arrived, something Fuso followed with its Daimler platform Shogun range. No doubt Hino’s new 700 Series – which came late last year – will fall in line as well.
The look and feel of the dash and surrounds are what you might call fleet-Euro, with quality workable, cleanable surfaces in plastic, vinyls and rubbers. The lower in the cab you go, the easier it gets to clean.
For the expanse of plastic caddies across the middle, there’s not a lot of storage, really. There’s a big overhead locker in the middle, the neat folder stow above the driver (and passenger) – an immensely practical thing for a busy driver – and door pockets. It’s interesting that a truck in 2022 doesn’t have external lockers under the bunk, something that would be an incredibly well-used facility at McLeod’s.
Colour and tone-wise, it’s all grey with the odd aluminium highlight, which sparks one of my old chestnuts of drivers enjoying a splash of colour and shine. Just because the designer might be as staid as a council AGM, the customers certainly aren’t. A flash of red or something shiny would enhance things here no end.
Daily checks are easy ‘peasy’ under the front flap. Moving on…
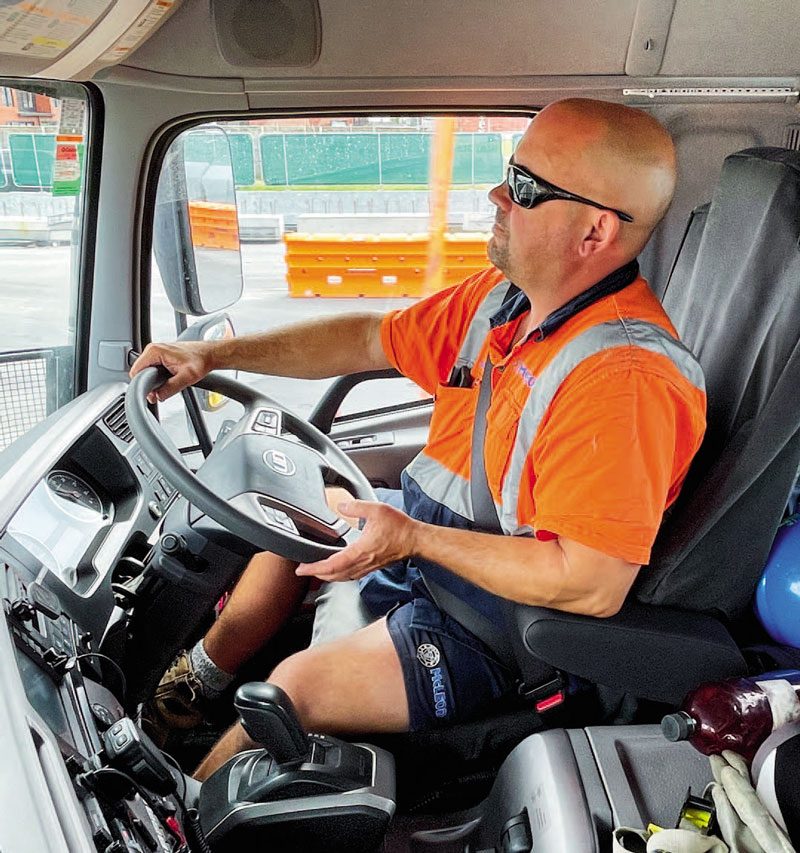
‘…as a Tiger’
At that moment our pilot, Ian Mearns, arrives. “It’s great Ian’s on the job,” says Brett. “He’s the best as far as I’m concerned. A first-class pilot and decent bloke.”
Brett eases the single room out from its possie and onto the truck. Loaded, crane packed away, secured, signs in place, walk around done, press ‘play’… Actually, select ‘D’.
The UD’s a comfy and smooth place to spend a day, a far more refined ride and workplace in the new incarnation. Visibility is great, and even though McLeods spec’d a longer than usual wheelbase at 6385mm to accommodate the crane, it’s still a nimble machine.
“I haven’t driven these new UD’s much,” says Brett. “But this AMT is head and shoulders over the ZF’s in the older Hinos. It’s bloody nice, and very smooth.
“The lane departure is one thing that we turn off regularly. We have to. So much of our work is over the fog line, and kerbs, so it’s just not a practical tool.”
As we said at the outset, the UDs safety suite was key in the decision-making process around McLeod’s next-generation fleet. Being a true platform machine, the new Quon takes full advantage of Mother Volvo’s box of safety tricks and so comes off the shelf standard with Traffic Eye cruise control and braking (intelligent cruise and autonomous emergency braking), lane departure, and electronic stability control. Obviously, there are ABS and EBS, but the truck is also a full disc-brake set-up. Nice, and that’s all non-negotiable, too, speaking to the OEM, not the customer.
There’s also useful productivity kit like the ESCOT-Roll function, brake blending – handy when crossing the Kaimai Ranges is a part of your regular life – and extended service intervals, which being a crane truck and all, UD schedules at 400 hours.
Our destination was one of those places where sharp, well-trained, experienced crane operators earn their keep. Innocuous it may have looked, the building had to go down the end of a long concrete drive flanked by fences and trees, and then negotiate a hook in the drive so the rear of the truck was in a position where the crane could reach the footings with the new room.
Brett goes for the obligatory walk and assessment with James and pilot Ian, who had decided to hang around, realising the more eyes here, the better. All told, we were probably looking at 120-plus years’ experience in both building and relocating ungainly stuff.
With the plan made and communicated to all, it was time to get the brand- new – unmarked – truck into position. Yikes.
Brett checks the trees on the drive for big hidden branches or extraneous flotsam that might like a mirror to munch on, and with everyone on point and in radio comms with Ian, back he goes. Even the initial line-up takes a bit of jiggling. The UD has great front-bumper clearance, but the dunnage bin located right down under the crane is something that’s going to have to be watched.
Inch by inch, he eventually reaches the kink in the drive and commences a series of forward and back manoeuvres, working the tail around without damaging the front left of the cab on the fence.
It is this chain of events that demonstrates just how easy linehaul is on drivelines, and just how hard so many other things are. Kilometres may not feature heavily in this machine’s life, but the steering, suspension components and clutch are not in for an easy trot. With all the back and forth, there was not a hint of issue from the clutch or ESCOT-VI, and when Brett is finally at a point where he can go no further on account of fences and other obstacles, he alights and says, “That was bloody impressive. If there’s one thing that we’ve found the AMTs aren’t that hot on, it’s low- speed manoeuvring. They tend to get a bit hot, and jittery after a while, but that thing was smooth all the way with no hint of heat. It’s only new, so we’ll see, but that’s a good first sign, I must say.”
Once in place, the easy bit came next, and by now, we were well used to seeing big things up high.
Ian leaves and Russell and team stand ready for the arrival. Brett has one of his chats with the customers and when he was done, they had no idea they’d just been ‘toolboxed’. We got our boundaries laid out to us, and off, out, over, and down, came the wee hut, just like that!
Summary – Talk about the right truck at the right time
McLeod’s is just the customer the boffins at UD must have been thinking about when they raised the bar on what defines a truck from Japan. In the UD Quon, McLeod’s has a truck that’s affordable in times of meteoric expansion yet slots beautifully into the cultural mandates set by this generation of company owners. It’s a market sector that’s only going to grow as expansion comes to many firms in times of ever more stringent compliance.
“Since the launch of the new UD Trucks Quon 8×4 range in 2018 we have been very pleased with the performance of these models in terms of product specification, in service performance and customer acceptance,” said UD Trucks New Zealand general manager John Gerbich.
“After a five-year absence of an 8×4 chassis in our model line-up, UD Trucks developed three new models specifically for the New Zealand market, with suspension and horsepower options, and some of the most advanced technology available. UD Trucks have continued to make small changes to the model specification to improve driveability and driver comfort, with further enhancements planned for the near future.” At the end of the day, everything is about application – whether it’s trucks to a task or your principles in business. Process is something rarely understood, and although it’s permeated in every square inch of commerce, health and safety is still something many struggle to do well – and there are a plethora of reasons for that, most of which lay with central government.
McLeod’s success in both these areas is rooted differently than most. Two of the owners come from backgrounds where the aim is keeping people safe in unavoidably dangerous situations; war and oil and gas exploration. The other was born of two companies, noted in New Zealand as being successful through unwavering adherence to culture.
What you end up with is an entity that creates a framework whereby dignity and respect allow intelligent people to execute difficult tasks in as safe an environment as possible. We had a great chaperone, and when we left, we’d found a new friend, even though we’d been ‘toolboxed’ all day.
Build a company with values like that and you’ll grow like billy-o in 2022, at which point you’ll need an affordable, productive truck that meets your cultural fit. Epiphany No.3: In the end, those guys and gals at UD were the trailblazers!
ACKNOWLEDGEMENTS
Another rich experience for us adding an invaluable insight to a company’s philosophy that only serves to enrich your own life-book. Thanks to Phil, Scott, and Peter for access to the McLeod operation, and Phil, for the time we were given in a business that’s so busy. Thanks to Brett Meier for a great day, and a truly amazing personal back story. Unbelievable. I worry about elephants on the road at night now. Thanks to John Gerbich and Marvin Fynn at UD Trucks NZ for your always enthusiastic help.
Quick reads from the Test
Read more
The right man for the job
0 Comments29 Minutes
Legendary ambition
0 Comments36 Minutes
Hard Fought!
0 Comments40 Minutes