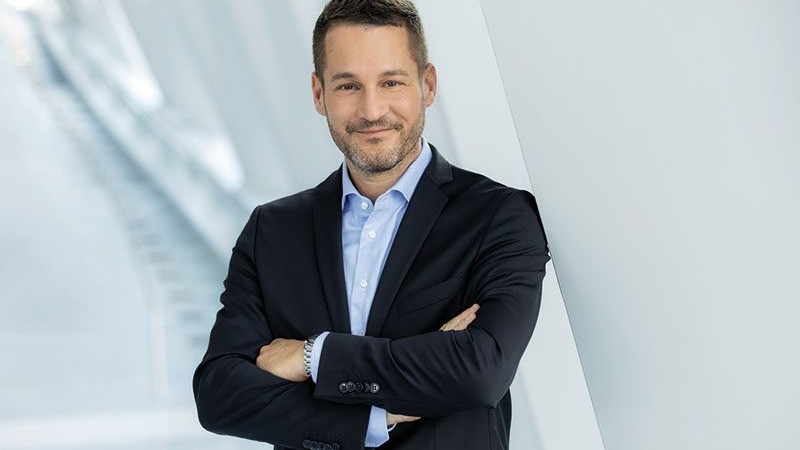
Rarely has uncertainty dominated the view from the world’s windscreen as it does today. But getting in front of people such as Daimler Truck AG’s head of truck technology, Andreas Gorbach, at IAA in Hanover last year certainly helped provide clarity from the perspective of one of the global OEM giants.
Overview
Head of truck technology at Daimler Truck AG, Andreas Gorbach, is one of those people who simply answers questions, leaving silence in their wake. Only the bravest dare go down the ‘yeah, but…’ path. He’s not unfriendly – quite the opposite – but he answers stuff with extreme clarity.
He started his round table at IAA Hanover last year with a summation of what technology meant at Daimler Truck, describing it as a “key lever” that delivers a positive outcome for customers, shareholders, and society. He then spoke about “key technology”, assigning it two fundamental attributes; first, long-term differentiation, meaning a technology that makes an ongoing difference within five to 10 years across all customers, markets, and brands; and, second, commonality – engineer once and deploy many times to create scale and therefore profit.
“What are the two most relevant technologies according to these attributes for us? The power to drive and the intelligence to drive.”
The power to drive pointed to diesel, BEV and FCEV, and intelligence to drive to electronics and software. Both are relevant technologies, differentiators today and in the future.
He says diesel has met the key technological attributes for 120 years – a propulsion technology that answers all variables of industry, application and regulation across many countries. “But the one-size-fits-all story will discontinue.
“With electronics, we’ve added it to the truck step by step. We describe functions and purchase control units from vendors, adding more and more intelligence to the truck.”
“Both of these technologies – diesel and electronics – have been the foundation of our success and the cash generators for what we do in the future.”
Decarbonisation and digitalisation are the two big frontiers moving forward, he says, expressing Daimler Truck’s commitment to decarbonisation as a signatory to the Paris Accord.
Diesel will remain in focus for the next 10 to 20 years, with BEV and FCEV forming the basis for decarbonised propulsion in the future.
Digitalisation will be key to advancing electronics with software-based architecture using centralised hardware to flash applications across the air to common operating systems.
“We need to transform the truck into a programmable device. This, in short, is our technology strategy for the next 10 to 20 years.”
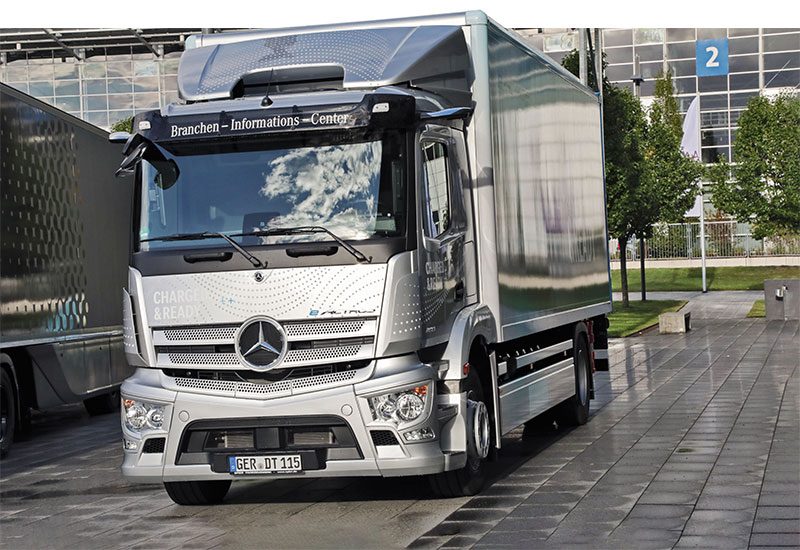
Question and answer session
(Summary of key questions asked from the floor. Answers as bullets with quoted additional comments.)
Proprietary electrical engines at Daimler Truck?
• To date, the supply of all electric engines has been outsourced. However, significant resources are currently being deployed, building in-house know-how.
• There’s no definitive plan for when vertical integration will occur. But volumes over the next five to 10 years mean it doesn’t make sense yet.
Daimler’s choice to use LFP (lithium-iron phosphate) batteries in the trucks as opposed to LMC (lithium-ion) batteries? LFP is generally seen as heavier and less energy dense.
• LFP is better suited to high levels of charge cycling without impacting life. Passenger cars must last about 150,000km – a truck, 1,000,000km-plus.
• An LFP battery has no nickel and cobalt, so there are fewer costs and geopolitical issues.
• LFP batteries are slightly less energy-dense. However, trucks generally don’t have the same packaging issues as a car. “We have also found a way to compensate energy density on a cell level and on a pack level.”
• LFP batteries have better thermal propagation characteristics.
Additional comment
“We can pack 600kW/h (300km) LFP batteries sufficiently. For long ranges, we are sure hydrogen is the best solution. Packing 1MW of battery in a truck doesn’t make sense. If we were using LMC cells, I still wouldn’t push for an 800-1000km BEV truck.”
Is there a battery breakthrough that would allow over 500km? How far do you think it is?
• No. The charge comes from the electro-chemical potential between the elements. There’s a maximum electro-chemical difference between all the elements on earth.
Additional comment
“Even if you take the elements that have the biggest difference in electro-chemical potential – giving you the highest energy density, the highest voltage, highest potential energy density – you would never come close to the energy density of hydrogen. Hydrogen has 33kW/h per kg; a battery today, 0.5kW/h per kg. Even if a breakthrough battery was 1.0kW/h per kg, that’s still a factor of over 30 away. There are no elements on earth to compete with hydrogen.”
How much flexibility is there in the timeline to meet the Paris Accord? What are your milestones and dates?
• Step-by-step electrification. By 2025-26, all relevant trucks will be electrified.
Additional comment
“Some years ago, we were under pressure to get started. The product portfolio will now not be the limiting factor. The dominating factor will be the infrastructure. The price of electricity, hydrogen, and diesel impacts the TCO case for the customer.
“The products will be there, and we will have the flexibility to walk at the same pace as the infrastructure and as the TCO case for customers evolves.
“I am honestly rather scared that the speed on the infrastructure side is not fast enough to comply with the Paris Accord, which will then put us in a difficult situation at the dealership. I want to sell a BEV or FCEV, and the customer says, ‘I can’t buy it, there is no infrastructure’, and I have to tell the customer, ‘I cannot sell you the diesel truck as I cannot pay the penalty.’ And then we come to an awkward situation.
“We want to be so flexible that we will never be the bottleneck for the technology.”
Do you see engine collaboration as diesel declines?
• Yes. Captive product in the medium-duty product has already gone to Cummins.
• Heavy-duty products are best-in-class and of high enough volume to warrant continued production.
• When the time comes, partnership will be based on our technology.
• Consolidation in the diesel industry will be needed to keep volumes high enough for all parties, including suppliers.
When do you think the complete elimination of diesel will occur?
• Unsure. We are aiming for 2039 for the main markets, dependent on infrastructure and energy prices.
• Decarbonisation speed is not determined by product portfolio.
Additional comments
“If there is still one drop of oil below the surface of the planet with more than 40MJ (megajoules) of energy per litre, and the federation of states among the Paris Accord becomes unstable, then those countries will continue with diesel. We can consciously decide not to sell to those countries, but other OEMs will.
“We need strong collaboration between the states that signed the Paris Accord, and they need to invest in infrastructure and provide cheap, green energy. It’s a fragile situation on the planet at the moment; who has the power and political willingness to go down that path and continuously reinvest in cheap, clean energy?” Hydrogen combustion engines?
• We are closely monitoring, as are all players. “Too sexy to look away from, too immature to bet your house on.”
• Efficiency is significantly better than it was.
• Fuel cells are at their best under low load, e.g. a 40-tonne combination on the motorway at 80kph requiring only 100kW of the 300kW available. With a construction vehicle under full load, the hydrogen combustion engine would be better.
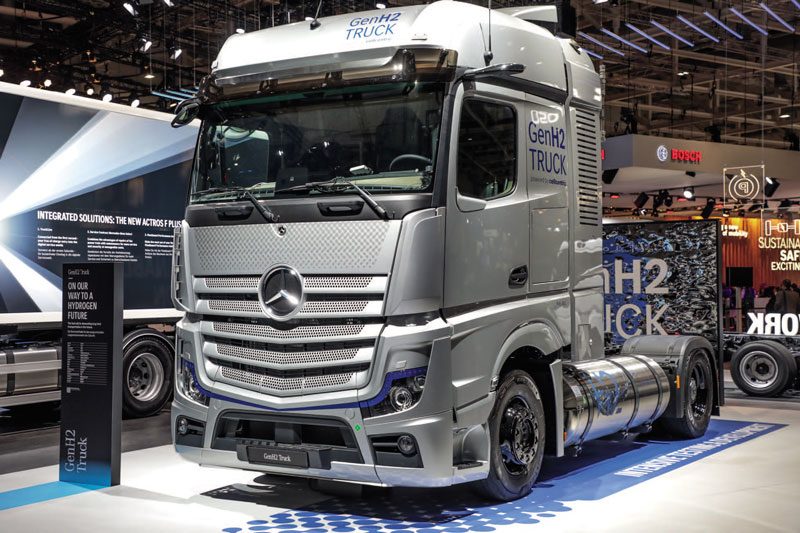
Hydrogen in what form? Gaseous or liquid?
• My personal preference is liquid. It is:
• easier to produce
• easier to transport
• better for us [Daimler] – lower cost
• better for the customer – wider range
• lower investment at the filling station.
• Everyone in the supply chain has an advantage with liquid. However, today, grey-compressed – at 350- 700 bar – has a greater infrastructure.
• Grey today, green tomorrow, with gas a transitioning to liquid-dominant long term.
Additional comments
“Irrespective of road transport requirements, we must transport green energy as a molecule. The world trades heavily in energy. Take Germany. We import 70% of our energy requirements. To decarbonise, we have three options: first, reduce consumption by 70%; second, produce 70% ourselves – and in that, we don’t have enough wind or solar, so we would need 30 of the largest nuclear power stations; and third, import green energy. We can’t trade electricity on a global scale, so it needs to be a molecule.
“Australia, the Middle East and Africa could all produce green hydrogen, transported as a molecule.”
Electrolisers? Use a lot of electricity and water.
(Qualified as commentary only, Daimler Truck not directly involved)
• Today, some regions can produce green hydrogen at 1c per kW/h.
• Need to use electrolyser and transport as a liquid or pipeline.
• Water can come from seawater with the salt extracted.
• 12 hours of flow of the Rhine would make enough hydrogen to run 20% of our global truck fleet for a year – so the volumes required are not as great as people think.
• Oil and gas production consumes more water per year than hydrogen production would.
Will there be a collaborative hydrogen infrastructure like you’ve done with Traton and Volvo on the MCS charges?
• The MCS project is only the start of what’s needed.
• There will only be micro-projects with hydrogen on specific routes, working with Shell and Total.
• The right political signals are needed. All OEMs together don’t have the resources to address the infrastructure issue. It’s not their role – “We don’t build bridges and roads.”
Read more
Road to Zero Isuzu styles
0 Comments6 Minutes
Ready for the harvest
0 Comments12 Minutes
VGA introduces electric
0 Comments8 Minutes
Celling’ the future
0 Comments14 Minutes