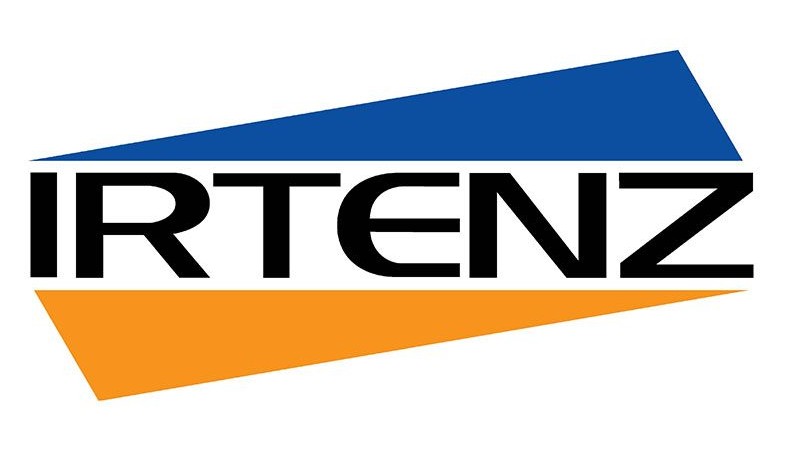
Last November, the 2023 IRTENZ 18th international conference, themed Future Highways – Future Vehicles, brought together speakers from New Zealand and throughout the world to present the latest developments on transport matters, including vehicle productivity and efficiency, road safety, legislation and policy, and infrastructure. We covered infrastructure and enforcement in the December/January issue of New Zealand Trucking. This month, we look at our workforce’s challenges, including skills shortages, immigration, education and training.
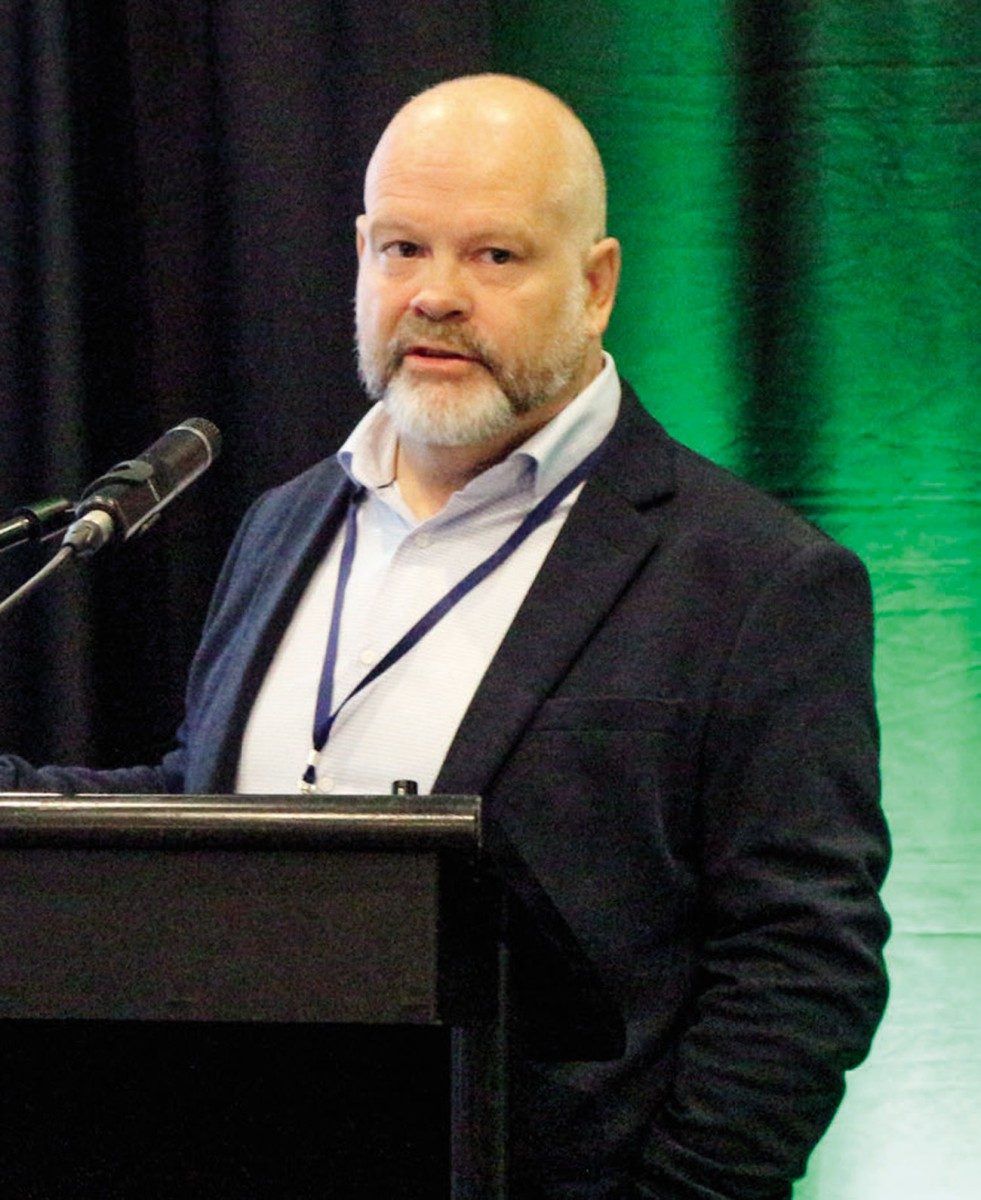
Scott Mathieson
Scott Mathieson, founding director at Working In, an organisation facilitating people to work in New Zealand, says addressing the people shortage in the transport sector is crucial.
“I’d prefer an environment where our workforce is entirely local. However, global structural dynamics necessitate finding the best talent worldwide,” he says.
“Working In has been aiding employers for over two decades in recruiting skilled individuals and integrating them into New Zealand.”
Looking ahead, Mathieson says the ageing workforce poses challenges in healthcare and social welfare. He says government spending is likely to increase in these areas, impacting the fiscal landscape.
“Migration becomes essential for economic sustenance, requiring a consistent and clear approach from the government.”
Mathieson says it is important to understand and embrace cultural differences when bringing in skilled workers worldwide.
“In terms of offshore recruitment, exploring markets like India for skilled workers is a viable option. India, with its technological advancements and educated workforce, offers potential opportunities. However, cultural assimilation is crucial, and employers should be prepared to support the integration of skilled individuals,” he says.
Mathieson says being prepared for future challenges is crucial.
“Recognising the global competition for talent and understanding cultural nuances is essential for successful workforce integration. New Zealand must proactively address these dynamics to ensure sustained growth.”
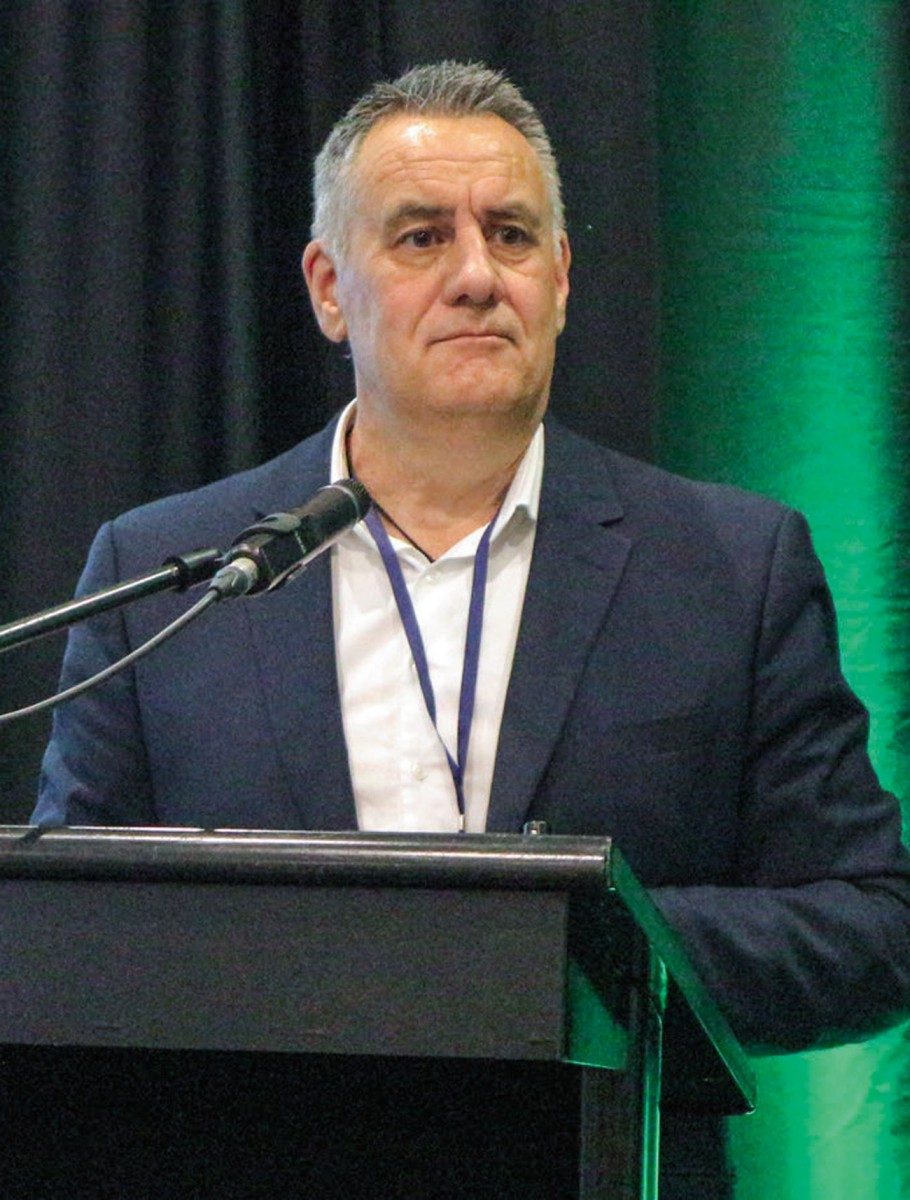
Phil Alexander-Crawford
Phil Alexander-Crawford, CEO of Hanga-Aro-Rau, the Workforce Development Council for Manufacturing, Engineering and Logistics, shared insights into the challenges and opportunities in addressing skills shortages.
He highlighted immigration as a crucial driver to fill the skills gap, and emphasised the need to explore various avenues, including tapping into the growing Pacific and Māori populations, ensuring that we try and keep as many people in New Zealand as possible.
“There’s a huge campaign on TikTok at the moment, targeting users to fly in and fly out to Australia,” Alexander-Crawford says.
“It is so clever; the campaign is designed to penetrate a youthful market. So, we are up against it in terms of retaining our existing talent – not just attracting it.”
Alexander-Crawford says it is crucial we align the education system with industry needs to ensure the availability of qualified and trained professionals.
“The education system needs to respond better to what industry needs because we don’t have the qualifications that support the training that supports what we need on the ground. And then we’re going to fail not only to retain staff but also to attract staff.”
Alexander-Crawford says the amalgamation of polytechnics will contribute significantly to workforce training. “There also needs to be a strong connection between industry and government, advocating for formal links to immigration settings.”
When looking at attracting the younger generation to the industry, Alexander-Crawford says young people currently completing NZQA credits will expect the same sort of training and recognition process when they enter the workforce.
“If we’re going to attract and retain that generation, it’s important we have qualifications in place to bring them on.
“That’s the reality. They’re expecting to go into a workplace and receive training, but also a piece of paper or digital piece of paper of recognition of what they’re doing.”
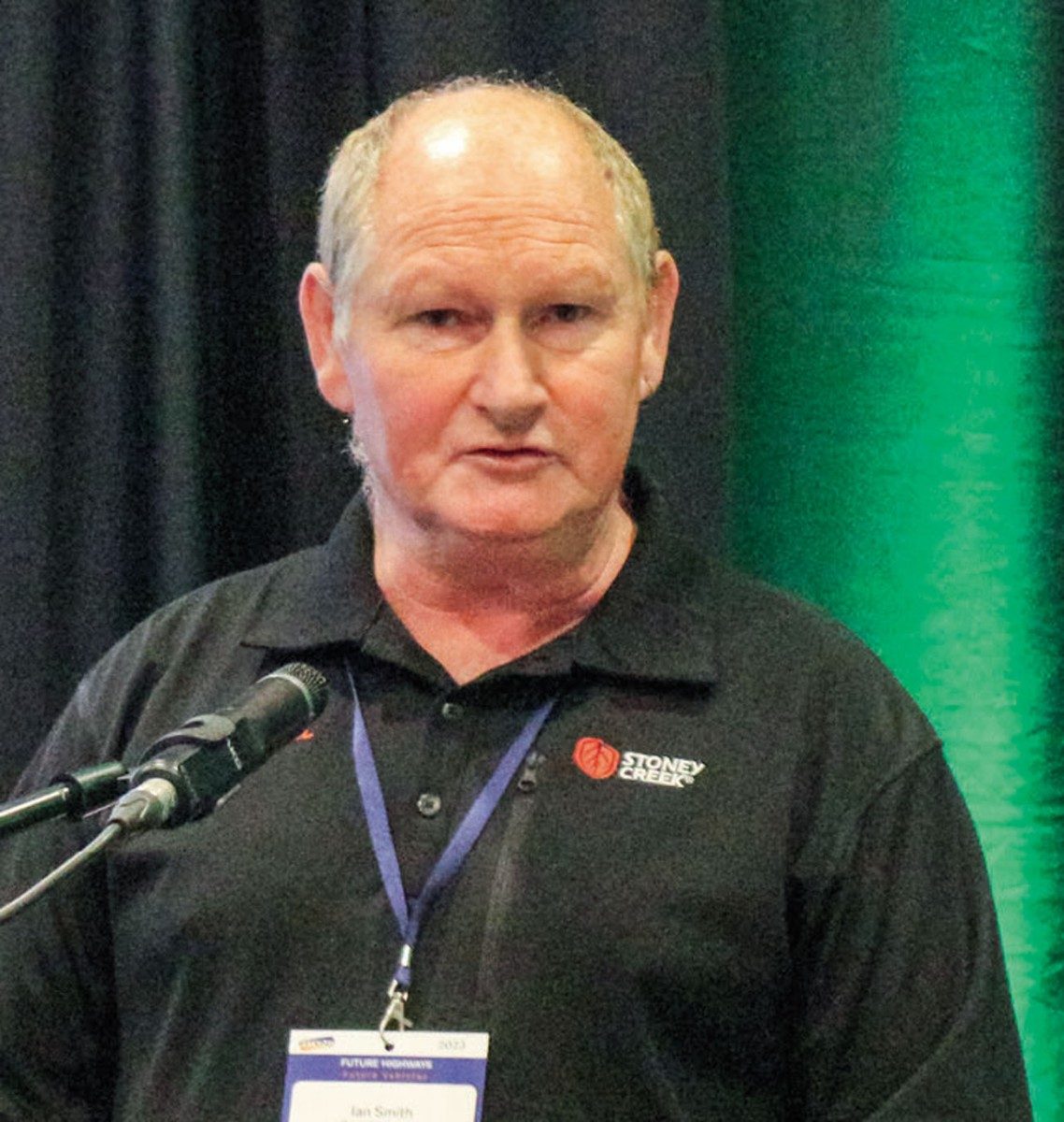
Ian Smith
Patchell Industries’ Ian Smith gave his view on training and qualifications and why the industry must be open to adapting to how we train and treat the young workforce.
“Our approach involves comprehensive training workshops, encompassing stock manufacturing and welding education. Emphasising the importance of certifications in our industry, we aim to equip individuals with the necessary skills to seamlessly integrate into our workshops and, ideally, pursue apprenticeships,” Smith says.
He says the current education system lacks emphasis on fundamental skills such as woodwork, metalwork and technical drawing.
“To address this, we are exploring the possibility of organising night classes, collaboratively funded by the industry, to supplement the existing training,” he says.
“Certification in areas such as electric trucks and hydrogen technology is crucial, and we’re actively working on incorporating these aspects into the qualification framework.”
Smith says the evolving nature of the industry requires the sector to adapt its training methods.
“Young individuals today may lack exposure to basic tools, necessitating a shift in our training approach. Patience is crucial in working with this generation, and acknowledging the importance of mental health is paramount,” he says.
Smith says to secure the future of our industry, we must adapt to the changing landscape, address workforce challenges and reshape the perception of trades as a viable career path.
“If we don’t adapt, we won’t have anything. I think it’s very important that in our industry – and every industry – we adapt to what we’ve got coming through.
“If we don’t learn how to, we are going to continue supporting migrants coming into New Zealand because we are not able to work with what we’ve got. So we’ve got to find ways to do it. How do we help young people getting into the trades, and hopefully also changing the schools?” he says.
“By actively engaging with schools, introducing more hands-on experiences and collaborating with industry experts, we aim to foster a positive environment for the next generation. I’m fortunate to work for a company that shares this vision and actively supports training initiatives.”
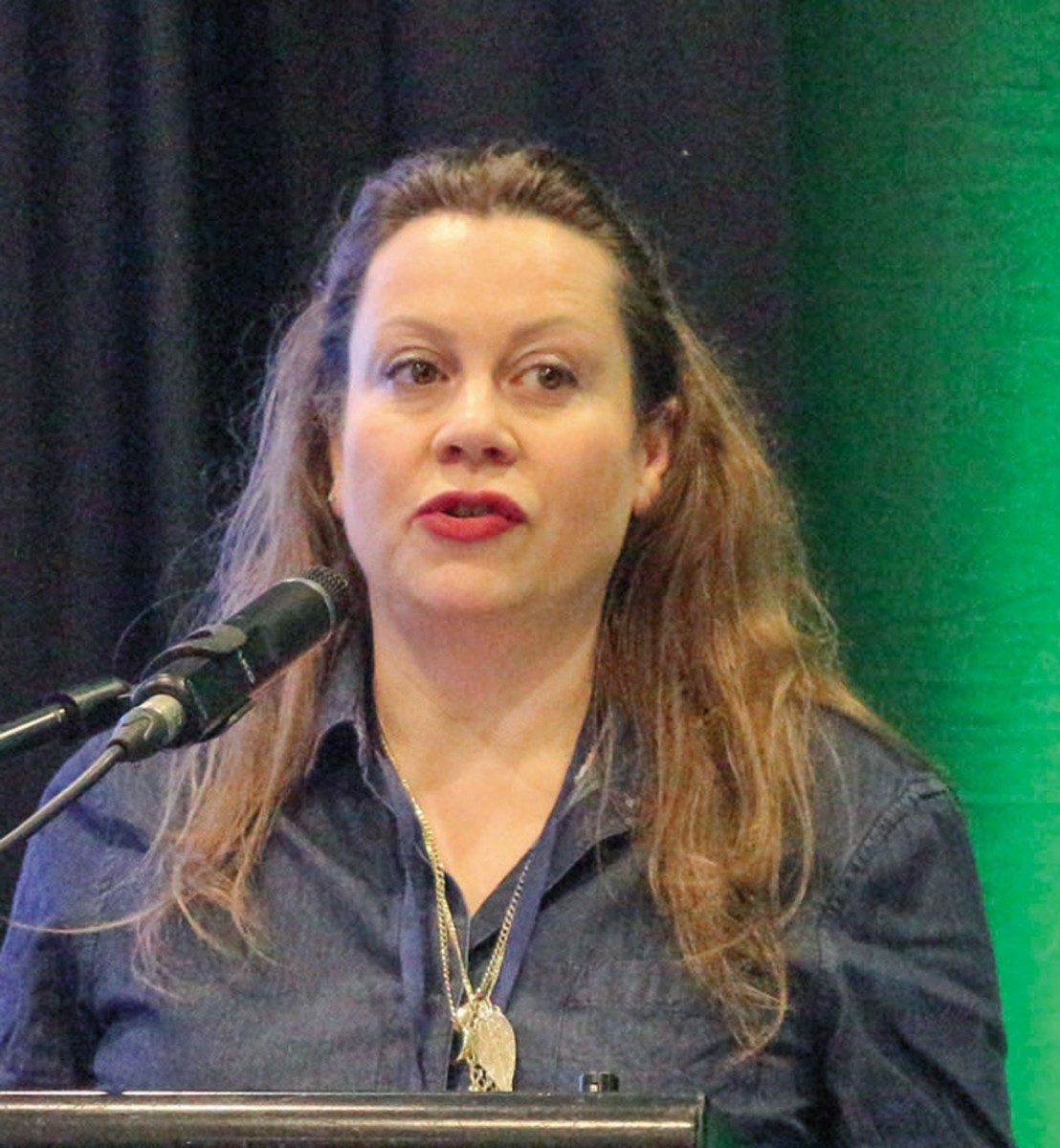
Eleanor Lavin
Eleanor Lavin from Engineering New Zealand discussed the new training and development pathway and programme for vehicle specialist certifiers.
In 2019, Waka Kotahi reset its regulatory focus, bringing vehicle inspection and certification processes into the spotlight. The focus on the heavy-vehicle certification industry revealed that there was a national shortage of engineers.
“The HVSC industry workforce is older, and in 2019, many engineers were already indicating that they would soon retire. This lack of capacity was, and still is, putting pressure on the commercial freight industry,” Lavin says.
Waka Kotahi was then tasked with addressing a lack of consistency across the inspection and certification industries.
“What we had here with this was an ageing work workforce who often worked reasonably in isolation, and they were very protective of their work and their IP, and how they go about their engineering and their certification practice.
“From a regulatory viewpoint, transparency about what good practice looks like sets up an industry for success. It’s impossible to do that when the knowledge is contained in individuals and in their heads.
“So the most effective thing we could do for the workforce alongside the agency was to extract that knowledge. And the most constructive thing we could do then with that knowledge is to develop an inter-vocational pathway and training.”
Lavin says the lack of visible, documented practise knowledge in the heavy vehicle specialist certifier (HVSC) space created barriers to industry entry.
“This scenario prompted the creation of our project with the key goals of establishing a vocational pathway, enhancing ongoing professional development for certifiers, and improving the effectiveness of the mentoring system,” she says.
The project’s benefits include an increased number of certified heavy-vehicle specialists (HVS) through promotional activities, improved certifier retention, production of well-trained and competent certifiers, and a focus on continuous training and learning development for established HVS. These outcomes are expected to lead to improved road safety by expediting the competency development of engineers.
“While it takes time for HPCs to become competent, we believe that the training programme will help engineers reach competencies sooner,” Lavin says.
“This, in turn, helps alleviate pressure on the commercial freight industry through greater capacity of certifiers and increased certification procedure knowledge.
“That will help increase efficiencies while meeting compliance and get some real consistency across the board.”
The fundamental skill sets cover a range of modules, each focusing on critical aspects such as regulations, proper inspection, welding and fatigue requirements. These modules use real-life scenarios, online training, webinars and practical sessions to ensure a comprehensive learning experience.
Lavin says the programme’s success hinges on the collaborative efforts of all involved parties. In the coming months, Waka Kotahi plans to launch the training programme, and Engineering New Zealand will develop a learning management system to host the modules and record training progress. Fees for the training will be set in line with government requirements for cost recovery.
Read more
IRTENZ Conference 2023 – PBS
0 Comments12 Minutes
Ready for the harvest
0 Comments12 Minutes