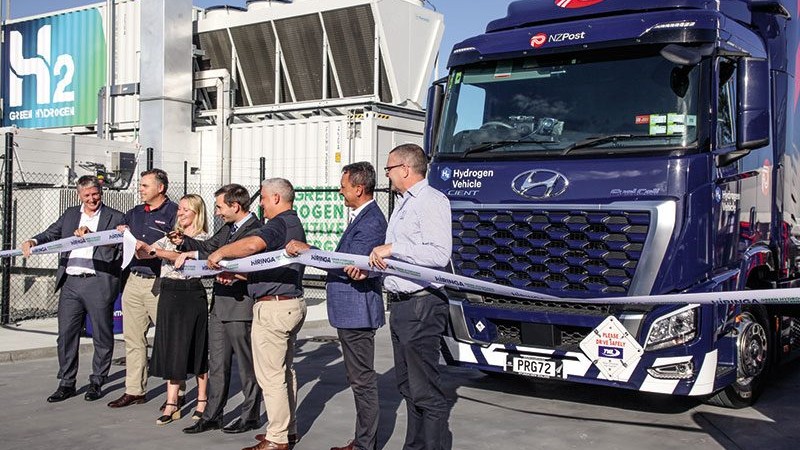
New Plymouth-based green hydrogen company Hiringa Energy has launched Australasia’s first hydrogen refuelling network, opening the taps to another alternative energy option for heavy transport and beyond.
New Zealand Trucking has been following Hiringa’s journey since the company got into its stride about four years ago. It had big plans for an alternative, green-hydrogen-powered future for heavy transport in New Zealand. Through strategic partnerships with Waitomo Group and TR Group, it would construct a network of hydrogen filling stations and offer forward-thinking operators hydrogen fuel-cell vehicles.
In April, the first phase of that refuelling network went online with the official opening of the first phase of three fuelling stations in Wiri (South Auckland), Te Rapa (Hamilton) and Palmerston North. The fourth station will be located at a new site as part of upcoming roading infrastructure developments along SH29 in Tauriko, Tauranga.
A subsidiary of Hiringa Energy, Hiringa Refuelling New Zealand is focused on deploying a nationwide high-capacity, open-access hydrogen refuelling network to service heavy road transport. In time, further stations will be rolled out at key locations on both islands, and Hiringa says the first four HRNZ stations will service 95% of heavy freight across the North Island.
While it may seem like a long time coming, it’s in fact taken around seven years to reach this point. “We’ve started a whole industry,” says Andrew Clennett, Hiringa CEO, acknowledging the hard work by all involved and adding that the chicken-or- egg conundrum of whether the vehicles or infrastructure should come first has now been answered.
The company says the heavy transport sector makes up 4% of the vehicles on the road but produces 25% of New Zealand’s transport emissions.
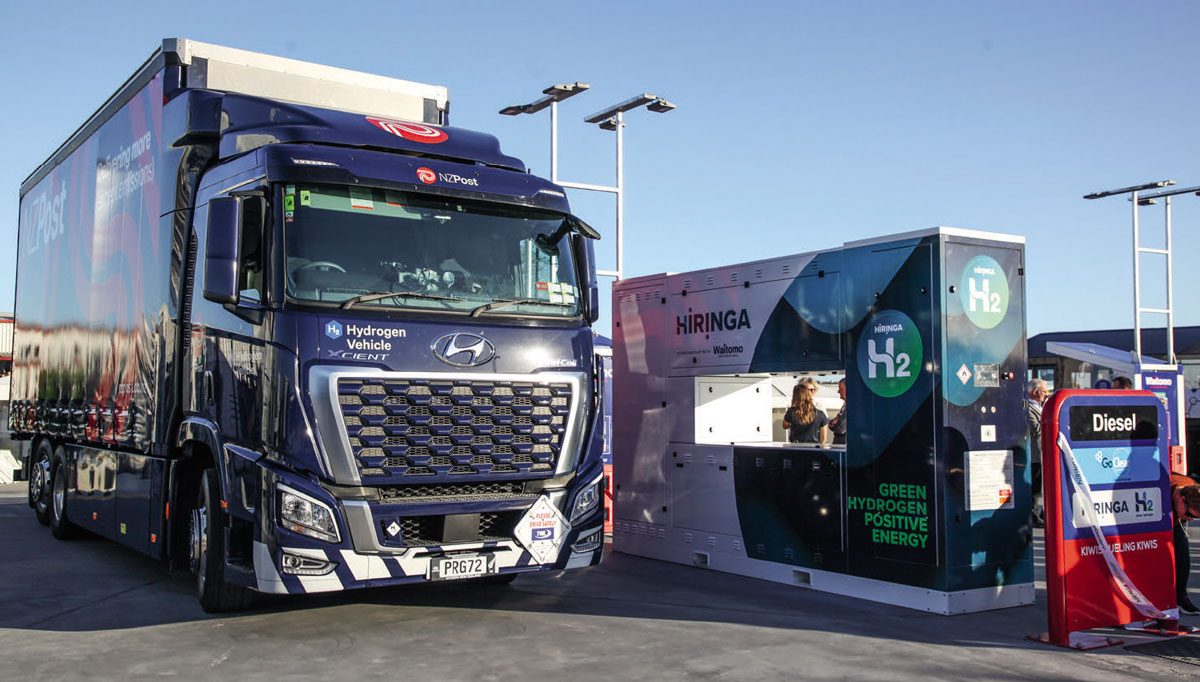
“It’s crucial we rise above the debate of ‘is it this or is it that?’ or what the silver bullet is. We need all the tools in the tool kit, including things we haven’t even thought of. You don’t play golf with one golf club,” says Andrew.
“As a first-of-its-kind across Australasia and one of the first networks set up globally to service heavy transport, the initiative addresses this major challenge by providing operators with the infrastructure they need to switch to zero-emission transport in an efficient, scalable and commercially viable manner.
“This network allows the heavy transport industry to adopt the technology to start shifting the dial. We don’t know trucks. TR Group knows trucks, and without Brendon [King] and Andrew [Carpenter], we wouldn’t have a chance. We will build the supply as the demand is brought on. Independent analysis suggests parity with diesel can be reached by the end of this decade if we drive the scale. The investments we make now will unlock productivity gains well into the millions,” he says.
The hydrogen is produced, stored and dispensed onsite. Heavy transport vehicles such as trucks and buses will be able to refuel with green hydrogen in 10 to 20 minutes. The system can refuel multiple heavy vehicles (30-50kg tanks) back to back at a flow rate of 60g/sec. It is designed for future upgrades, including doubling daily capacity and high flow rates of 120g/sec.
The hydrogen is stored in a multiple-element gas container (MEGC), designed to safely hold up to 730kg of hydrogen gas at up to 350bar. This equates to two days of hydrogen production, enough to fill about 20 trucks. The containers hold 18 vessels in six groups (called banks) of three. Each individual vessel is made of a plastic liner with fibreglass wrap (type IV) and has a volume of 1700L, holding 41kg of hydrogen at 350bar. The vessels are corrosion-resistant, and each bank is protected by a thermally activated pressure-relief device. Each station has one MECG onsite and one mobile unit to transfer capacity.
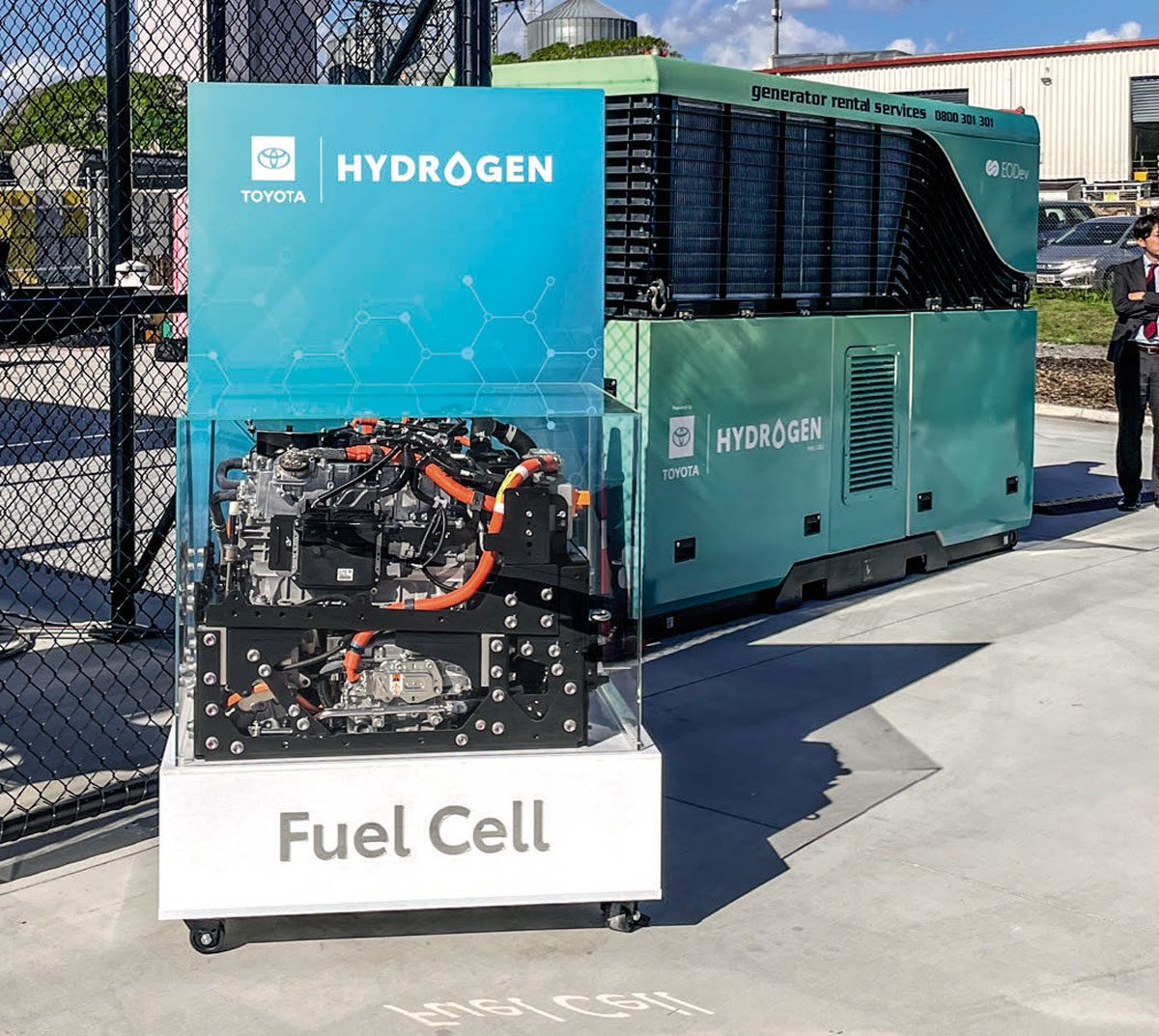
(See More About Hydrogen below to learn how the hydrogen is produced.)
“What we’ve done here isn’t just a demonstration – we’re not talking about one station but four, not kilogrammes but tonnes, not kilowatts but megawatts. To make an impact, we had to think big and that takes an entirely different engineering and technological strategy. We’ve thought about redundancy, backups and fail-safes – this network is about commerciality. It’s a go-big or go-home moment,” says Dan Kahn, co-founder and CTO.
“Waitomo believes in a just transition and that’s why we’ve joined the journey and invested in this network. We’ve long said hydrocarbons would fund the transition, and we can see that in this multi-use site,” says Simon Parham, CEO Waitomo Group.
“It’s about maintaining a viable operation while investing in a sustainable future. That’s why this network isn’t just infrastructure; it’s a gateway to a hydrogen fleet. One hydrogen truck equals a hydrogen reduction equal to up to 150 EVs. This is where the decarbonisation prize exists.”
As for the trucks, they are expected to arrive later in 2024. Brendan King, general manager of TR Group, says that when it comes to climate change, taking a leading position is important.
“There are currently 20 Hyzon trucks in Melbourne headed for our market. We couldn’t commit to these trucks without the likes of Hiringa and the customers who are committed to this cause.”
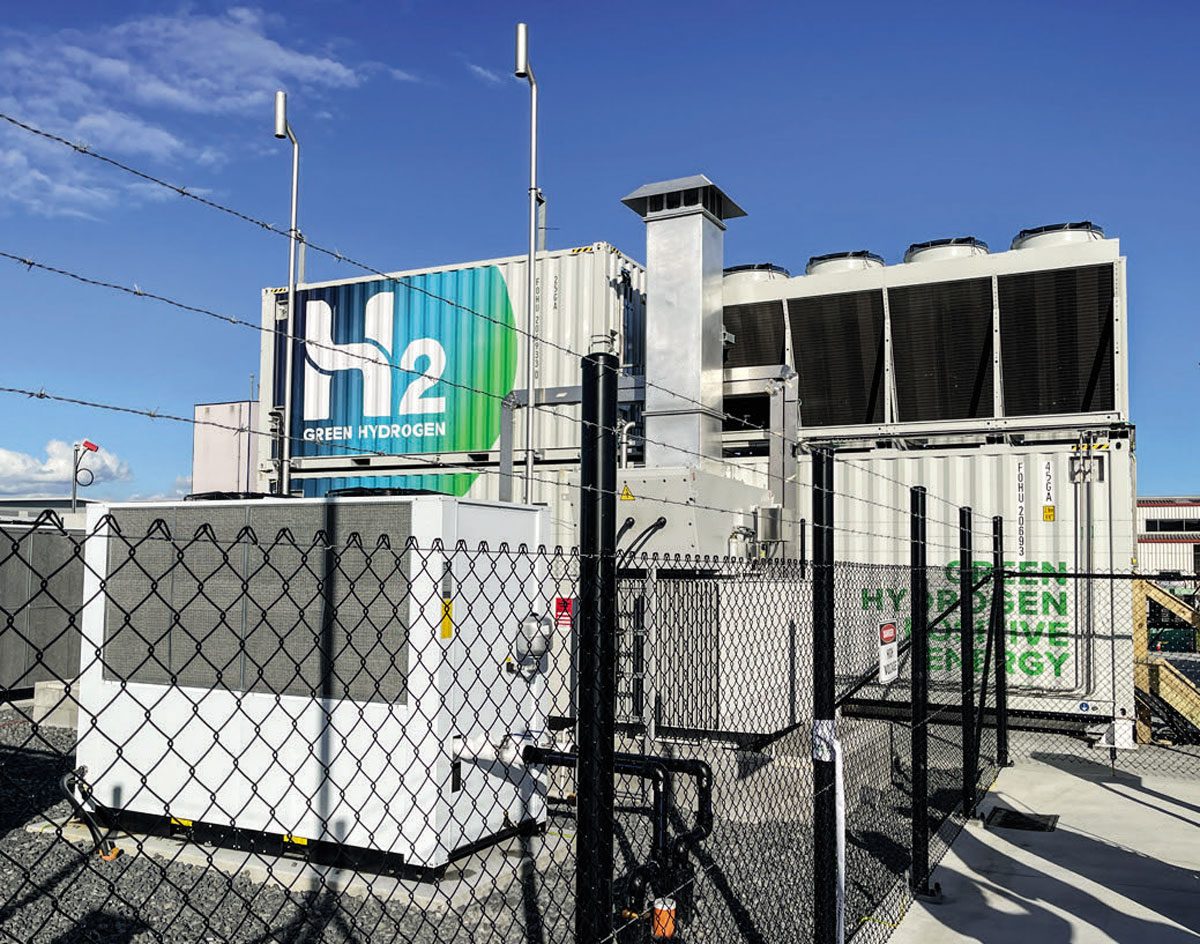
More about hydrogen
Technically, hydrogen is an energy carrier (like electricity) and not an energy source. It is produced at the HRNZ sites through electrolysis (passing electricity through water to separate the hydrogen and oxygen molecules). As this process makes use of renewable energy sources like solar or wind power, it is termed ‘green hydrogen’. The onsite electrolyser has a capacity of 440kg per day.
The only by-product is pure oxygen, released into the atmosphere. Electrolysis requires a surprisingly small amount of water compared with other existing industrial and agricultural processes. Technology is being developed to create hydrogen from seawater to ensure hydrogen production at very large scale will not compromise access to fresh water for other uses.
Once produced, the hydrogen is then compressed and stored onsite, ready to be dispensed. To create the power it needs, a fuel-cell electric vehicle (FCEV) essentially reverses the electrolysis process (and, as such, its only emission is water vapour). The onboard fuel cell combines the hydrogen with atmospheric oxygen in a chemical reaction to release energy in the form of electricity, which is stored in the vehicle’s battery packs and powers its electric motor.
As an alternative to battery electric vehicles (BEVs), hydrogen fuel cells provide longer distances, faster refuelling times, and should therefore be better suited to heavy- duty vehicles and long-haul transport.
In addition to transport, Hiringa aims to accelerate the adoption of green hydrogen applications across multiple sectors, including aviation, construction, rail, marine, materials handling, off-highway and remote- use stationary power. Hiringa has a strategic alliance agreement with Air New Zealand, along with being a partner in the Hydrogen Consortium, to pioneer New Zealand’s commercial deployment of green-hydrogen- powered aircraft.
The launch event was silently powered by a hydrogen fuel-cell generator to demonstrate this particular use case.
Read more
Truckloads of support
0 Comments5 Minutes
Leo van der Weerd
0 Comments2 Minutes