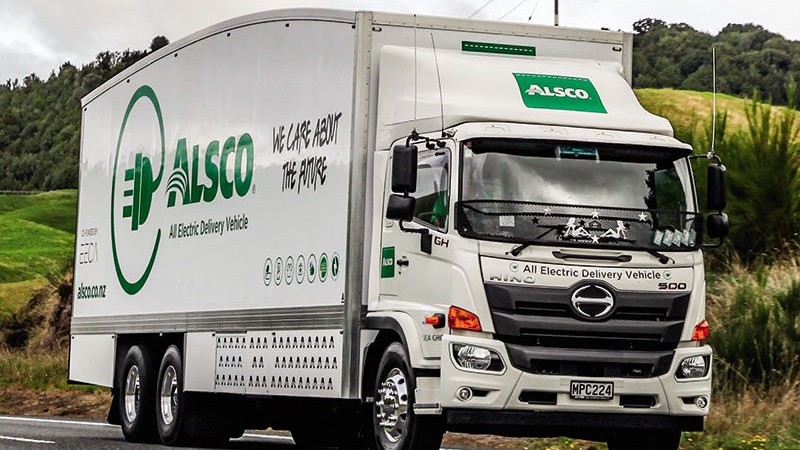
In November 2019, Alsco New Zealand and SEA Electric unveiled the country’s first heavy EV freighter, based on a Hino 500 and fitted with SEA Electric’s SEA-Drive 180b powertrain. As it would turn out, the vehicle’s next two years could be summed up in three words: steep learning curve. However, as with everything in life, such curves are necessary for success.
It’s a situation the wider automotive world is quickly coming to terms with; rapid change is taking place as the industry moves to reduce its use and reliance on fossil fuels. But when it comes to trucking, there’s not much out there yet that’s better suited to fulfilling the needs of the industry than diesel. And while the latest generation of diesel-burners is cleaner than any others before, there’s plenty of scope to start feeding in alternatives where the opportunities present.
A company such as Alsco is an ideal candidate for finding and creating those opportunities. The company has some serious goals for reducing its environmental impact, including replacing 30% of its fleet with EVs by 2030, and understands the need to start early. That’s why, in 2018, the relationship with SEA was put on the table and the call was made to find branches that might be able to make the business case for a heavy electric freight truck work, so the company could apply for partial funding via the EECA-administered Low Emissions Vehicles Contestable Fund (LEVCF). Alsco NZ runs a mixed fleet of about 270 medium- sized trucks and vans across its 20 branches and depots, and 15 three-axle freighters that run from the eight larger branches to and from the depots.
Mike Compton, Alsco NZ fleet manager and Rotorua branch manager, figured he could make an electric freighter work on the daily run from the Rotorua branch to the Taupo depot and back in the morning, and then to the Tauranga depot and return in the afternoon. Mike drove the project from an operational perspective with the support of Gavin Smith, Alsco business and product development manager, who drove it with its environmental impact in mind. Piloting it from a practical perspective was driver Craig Christensen.
“We knew the truck had a 220km theoretical range, and we needed 280km of range per day. We believed we could run it to Taupo and charge for an hour while we unloaded and reloaded, drive back to Rotorua and charge it for two hours while unloading and reloading for Tauranga, and head to Tauranga and charge it up while there for an hour or so before returning,” Mike explains.
That was the initial theory, but it would take some compromise to make it work in practise…
A partnership of early adopters
“We were sort of at a prototype level at the time of introduction. Knowing that, we sought support from the EECA LEVCF. As early adopters, we knew there would be hiccups, and we still call it a ‘trial’,” Mike says.
Indeed, Alsco was very much a guinea pig as far as running a full-size electric truck in New Zealand was concerned. More than two years later, this remains the biggest heavy EV on local roads in terms of both dimension and range. As such, it was fitted with the SEA-Drive 180b powertrain. Designed for trucks with a GVM range from 18t to 26t, it consists of a 216kWh lithium-ion battery; permanent magnet motor with 225kW continuous power, 350kW maximum power and 3500Nm maximum torque; and 32A three-phase charger with 22kW maximum charging.
On paper, everything looked like it should stack up. The truck was delivered and fitted with a lightweight, low-drag 9m body by Action Motor Bodies, and following that 2019 launch at Eden Park, it was time to hit the road and put those electrons to work.
But Craig and Mike soon realised their expectations would require more compromise than expected. Two main issues needed to be overcome – charging and overheating.
“We never got the charge rate that was expected – the charger was underrated for the truck. So, we had to look at the infrastructure,” Mike says. “And although range was quoted at 220km, useable range was about 190km, at which point the truck derates itself to protect the battery.”
Solving this issue was a prime example of the partnership in action. SEA added a second charging module to the truck, and Alsco picked up the bill to install four additional Wallbox chargers at Rotorua and each depot. Craig also came to the party and agreed to a split shift with a four-hour break between the runs to allow the truck to cool down fully and charge back up to 100%.
The overheating problem was one perhaps unforeseen by either party. “SEA had had success with stop-start operations, but we run the truck on the open road all the time, and that’s not great for an electric motor,” says Mike.
Action Motor Bodies adapted the skirts on the right-hand side of the body (where the cooling system is mounted) to allow more airflow, and SEA set out to boost the reliability and ensure that, if the truck was about to fail, the driver would have advance warning. Mike explains that, at first, the truck would just stop…
“That was it. We had a few failures and could hear the shake in Craig’s voice. As a responsible company, we said this cannot happen. The truck cannot just shut down. SEA acknowledged that and had to re-engineer it to give the driver more time to react in the event of a shutdown.”
A failure warning buzzer was added, and the power steering was hooked up to a failsafe mechanism. “It relied on the electric motor, so we had to retrofit a power steering unit that gives 40 seconds on the 24V systems to get to the side of the road.”
Gavin explains the difficulties encountered with a broken-down EV freighter. “It’s not a matter of getting a diesel mechanic out to the side of the road. It’s about plugging into a laptop, purely IT stuff. Twenty or 30 years ago, we could probably have gone out and got the truck running again ourselves. These days, it’s all data resolution.”
SEA understands this, and so all its builds include a data logger, which allows technicians to log in and diagnose the problem before being dispatched.
“We’ve always had the ability to remotely access the truck by connecting a laptop and talking to that. Since then, we’ve partnered with tracking and telematics company Geotab, which allows us to see information such as where the truck is, the state of the batteries, and so on. The trucks are Geotab- capable from build. The customer can have access to it if they want it, and we have engineering capability on top of that,” explains Stephen Fairweather, New Zealand general manager for SEA Electric.
“We will work with the customer’s service provider in the first instance if they have the skill base.”
Mike is full of praise for the support and commitment offered by SEA. “SEA New Zealand’s engineers, Josh Vendrig and Adam Eynon- Richards, are clever guys and a credit to their organisation. They’d be out overnight, Truckstops would loan us a bay – we have a great relationship with them as well – and they’d let the SEA techs work on the truck through the night.”
While the truck has now achieved the reliability originally expected of it, the final solution in ensuring its longevity is an upgraded electric motor. “It was offered to us out of the blue,” says Mike. “Stephen said, ‘To be honest, that truck works at 100% for too long… They’re designed for stop-start, not a 100% run to Taupo.’ So, the upgraded motor will not be maxed out, work more efficiently and not get as hot.”
Says Stephen: “It’s better to have a bigger motor running half its capacity than a smaller motor running flat out all the time. The motor will go from the current 3500Nm to 6000Nm – which wasn’t available when we built that truck. We have to change the motor MCU as well. It’s not just a case of bolting in a new motor.”
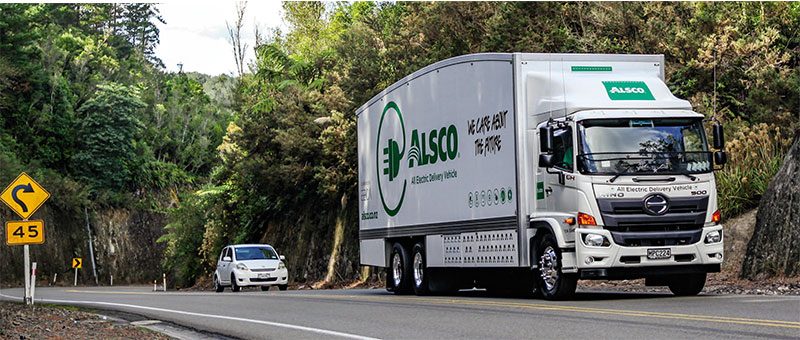
Going for a burn
While we’d be excited to get behind the wheel of a truck with 6000Nm at its disposal, to fully appreciate the impact of that we’d need to experience the truck in its original form. Craig, who last year handed off driving duties to colleague Ina Piua due to illness, came back for two days of driving and to give us a full tour of the truck. We’d run to Tauranga on day one and then to Taupo on day two.
When we arrive at the Rotorua branch, the truck is backed up to the loading bay with both chargers connected. “We start at 100% charge every morning,” says Craig. “To get to Tauranga will use about 40%. We’ll plug it in to about 70%, and then arrive back with 30% remaining.”
Craig lowers the Zepro tail lift and begins rolling on the trolleys of fresh linen. “A full trolley weighs about 250kg, and the truck’s set up to cart about 18 of them. At most, we’ll have about 6.5 tonne on. As the truck is spec’d for 21 tonne, we’re never going to weigh out or cube out,” he says.
We take the opportunity to have a look around the truck. Ignoring for a moment the swooping roofline of the body and the ‘electric vehicle’ branding, it appears to be nothing more than a familiar Hino 500, even retaining the OEM’s brand and model badging. Some discreet ‘SEA GHEV’ branding on the lower doors is the only other clue to the EV powertrain. Craig’s fitted a stone guard adorned with a touch of American-style bling, which tie in nicely with the Alcoa wheels. Other than that, you’d be hard-pressed to spot the differences.
Eighteen trolleys secured in place, Craig raises the tail lift and comes round to tip the cab for us. Underneath, where one would expect to find the Hino’s diesel powertrain, is a set of two stacked battery packs, with another two mounted behind in line, where the transmission would ordinarily be found. The electric motor is mounted behind those battery packs, connected directly to the standard Hino diff via a stubby propshaft.
Mounted to the left-hand side of the chassis rails are the air compressors and ancillary components such as air-conditioning and power steering pumps, with the electric powertrain control box and charge ports just behind that. At the right-hand side of the chassis sit the air tanks and, as mentioned, the cooling system.
The route to the Tauranga depot follows the gnarly SH36. With its many twists and turns and inclines and descents, it suits the characteristics of an electric vehicle better than the flat and easy run to Taupo. As Craig predicted, the truck arrives with 60% range showing. He backs up, plugs in the dual chargers, rolls off the clean laundry and rolls on the dirty, and we’re soon ready to hit the road back to Rotorua.
“Wanna take it back and see how she goes?” he asks. What a question…
There’s nothing to do but turn the key, press D on the Allison transmission selector, and go. The only gauges to take note of in the standard Hino gauge cluster are speed and air pressure, while an aftermarket battery percentage meter sits atop the dash. This being the largest, heaviest electric truck I’ve driven, my first observation is how much more throttle is required to get moving. In fact, that’ll be a recurring observation. “Just remember to keep your foot flat, mate,” Craig offers. “You’ve got to give it everything it’s got to get up those hills.”
As we wind our way out of town, I could be in any other six-wheeled Hino. It’s easy to control, place and manoeuvre. Quiet, too, as we’ve become accustomed to with electric propulsion. At town speeds, managing pace with just the accelerator pedal is easy; momentum builds smoothly and consistently up to 50kph, while easing off the pedal induces regeneration which slows down the truck effortlessly. Judge your traffic situation well enough, and you’ll barely go near the brake pedal.
On the open road and at higher speeds, it’s a bit of a different story. It takes a few minutes and a few more reminders from Craig to adjust to the ‘keep your foot flat’ mentality. With the mass onboard and a direct drive transferring the power, the truck takes a while to build up speed and carrying as much momentum as possible into an incline is essential – and a fair challenge for a first- time drive through SH36’s two steep, twisty gorges. The braking effect from lifting off the throttle is also similarly reduced and slowing from higher speeds requires assistance from the service brakes.
When I speak to Stephen, he says: “The Rotorua- Tauranga run is more gruesome, but actually it performs better there than it does on the gentle Taupo run. It gets that regen and the chance to cool down a little. The Rotorua-Taupo run is pretty hard for it in the sense that it’s a constant, 90-plus percent throttle the whole way without much respite.”
Day two, and with Craig taking us out to Taupo, I can see what Stephen was talking about. Despite not having a full load this time, Craig has his foot flat most of the way to keep up a steady 90kph. “I’m easing off so to not over- speed, but then I’m back on it to maintain speed. But, with a full load, my foot would be virtually flat to the floor. On the slight downhills here, I’ll just take the foot off, and it’ll glide down on regen.”
Normally the truck consumes about 50% of its battery power to get to Taupo, where a half an hour on the charger will put it back up to approximately 60%, which allows a small buffer to get back to base with. With a lighter load, we consume 47%.
“All I concentrate on is making sure those percentages are what I need to get home. Weight, weather and wind all have an effect,” Craig says.
“I’ve run it right down to 1% getting back to the branch … it derates itself, and you crawl in,” he says.
Achieving the goal?
With a little over 66,000km and two years of trial and error behind it, this truck is still a testbed for both Alsco and SEA Electric. It’s all a matter of getting it right for Alsco’s particular use and this market. After all, when diesel is truly done and what we now consider alternative propulsion has become the norm, cherry-picking routes, drivers, schedules or loads to suit the truck won’t be an option. They’ll have to work all the time, every time – just like diesel. Working on perfecting that now is paramount.
“It’s a new way of operating, as opposed to ‘she’ll be right’,” says Gavin as he explains Alsco’s steps to track the truck’s performance. “The data management side of it is something we didn’t even think about initially. It’s not range anxiety – it’s about the knowledge at your fingertips.”
While the Wallbox chargers installed by TransNet provide data and record daily electricity usage, Alsco has also hired an energy graduate to stimulate energy savings across the company. He handles the data analytics and validates the energy and emissions savings. (See A Year of Operation.)
“The sustainability angle of EVs was important to us. We want to be a good corporate citizen and desire to be seen at the pointy end of innovation. If we need to spend some money to make the business better, we’ll consider it. Our initial estimates on diesel savings and emissions reductions were damn close. On each journey we take there’s an offset that we can materialise, and the actual monetary savings have proved to be pretty close,” Gavin says.
Mike adds that the electricity costs were originally estimated to be about 20% of diesel costs. “Of course, that was three years ago, and diesel is a completely different animal now…” he quips. R&M has been negligible, with Truckstops taking care of the service items such as diff oil, brakes and bearings. The only R&M money spent so far has been on a set of steer and drive tyres.
“We saw the benefits of being early adopters and jumped at the chance, but in hindsight asking an electric truck to drive constantly under load probably wasn’t ideal,” Gavin says. “Three years in, would we make the same decision? At this point, yes, at the end of 2020, perhaps not. We’re early adopters and aware there will be issues – but we think they’re all surmountable.”
That said, Gavin and Mike note it’s unlikely they’ll put another heavy EV freighter to work in New Zealand until range increases and the trucks can operate without a split shift. In the meantime, Alsco Australia has ordered two new, smaller SEA 500 EVs to trial.
“We remain committed, and when the technology is there, we’ll accelerate it,” says Mike, adding that the three SEA E4V electric vans that joined the fleet at the same time as the Hino SEA-Drive 180b have been running successfully. Gavin says that as vans make up the bulk of the Alsco NZ fleet, they are now the immediate focus.
“SEA is kicking some pretty big goals at the moment, and while our journey with them hasn’t been perfect, it’s been very well supported,” says Gavin.
“It’s been a real partnership,” says Stephen. “It was always a big ask to do what they wanted to do, and we’ve overcome some of that. Alsco’s been very patient as early adopters; great to work with all the way and very supportive of us, even in the earlier days with the issues. We’ll continue to work with them to improve the truck.”
As a truckie dealing with people who see the truck on the road each day, Craig probably sums up the venture best: “People ask how it’s going, and we’ll tell them straight up. We could’ve waited two or three years for others to go through the process of getting it right, but Alsco wanted to be at the forefront. The thing is, you’ve got to start.
“It’s also about getting people in for a drive, letting them see how it feels, and the first thing they say is, ‘Wow, this is different!’ You’ve still got old-schoolers, sticklers… ‘nah nah nah, I’ll have a gearstick, blah blah’ … but I’ve had to embrace it and take it on because this is what the company’s decided. I’ve been pleased to be a part of the journey with this truck.
“This is it; this is the future. So, I say, sit back and relax.”
Read more
The right man for the job
0 Comments29 Minutes
Legendary ambition
0 Comments36 Minutes
Hard Fought!
0 Comments40 Minutes
Postal Trifecta
0 Comments29 Minutes