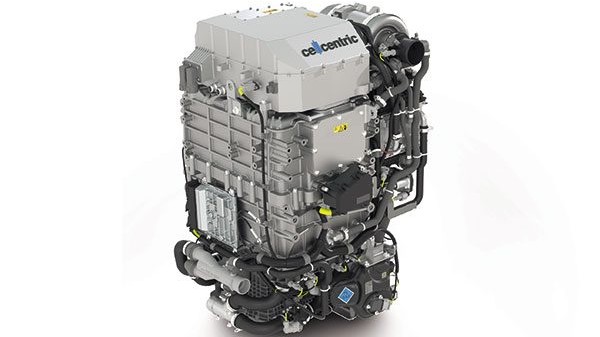
Fuel cell manufacturer cellcentric has been around for three decades, but it’s a brand few transport operators would know. That’s all about to change. The company is at the centre of a JV between archrivals, Daimler Truck and Volvo Group, and will supply both OEM giants with the fuel cells at the core of their respective hydrogen programmes.
Its stand was far from the biggest at IAA Hanover last year, but that is unlikely to remain the case for hydrogen fuel-cell manufacturer cellcentric. As chemical reactions and electrons assume their role at the forefront of global land-based transport, the name cellcentric may earn a level of familiarity akin to the companies they supply.
While pundits are still a-buzz, identifying the chinks in the armour of battery-electric and hydrogen fuel cells, those charged with delivering tomorrow’s locomotion generally take a far more pragmatic view. Theirs is one that doesn’t see the replacement of one ubiquitous, scalable power source with another, but rather, multiple options. And their reasons are far broader than a myopic view of heavy truck application, weight and range. In tomorrow’s world, regional energy availability and cost may well determine procurement decisions concerning truck purchase.
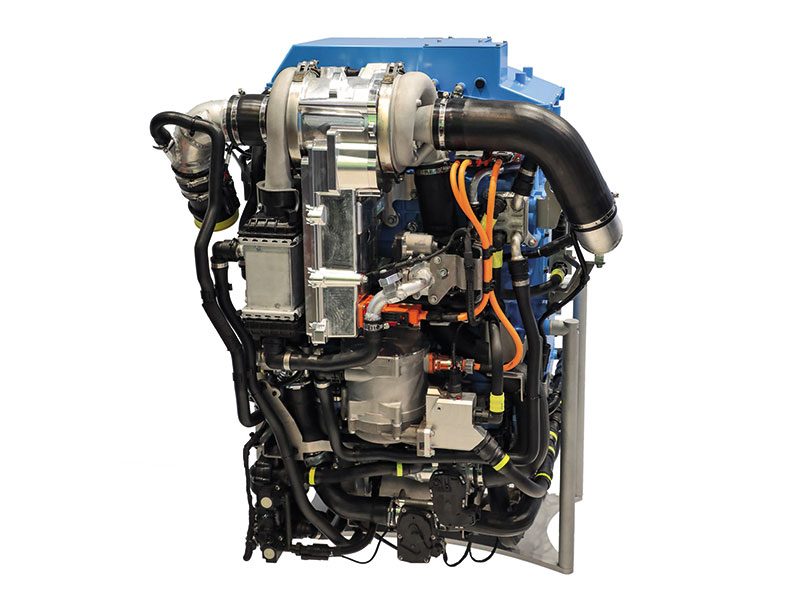
Speaking to those gathered at a forum hosted by cellcentric at Hannover, Volvo Group chief technology officer Lars Senqvist said: “At the moment, it’s like a beauty competition.”
His counterpart at Daimler Truck, head of truck technology Andreas Gorbach, added the real kicker. “In order to decarbonise the planet, we must deal in green energy on a global scale. For that to happen, we will need to transport green energy in a molecular form, as we do now with oil. Hydrogen is the best way to fulfil that requirement.”
Senqvst followed, saying hydrogen for transport would account for less than 10% of the global industrial demand. “We can piggyback on the big guys. There will be plenty of green hydrogen at the right cost level.”
Covering the bases
The scale, speed, and complexity of the global transportation revolution means even the biggest of the big are stretched trying to cover all potential bases. As such, we’re witnessing realignments in the interests of commercial protection and capital raising, the rationalisation of product portfolios, and collaborations once thought unlikely.
At the centre of one such collaboration is cellcentric, a manufacturer of fuel cells over the past three decades. Volvo Group AB and Daimler Truck AG each took a 50% stake in the company in March 2021. Cellcentric employs roughly 400 staff across four sites; Nabern, Stuttgart and Esslingen in Germany and Burnaby in Canada.
The company’s brief in the first instance is the development and manufacture of fuel cells for heavy trucks and, beyond that, general industrial applications.
Outside the fuel cell itself – fuel tanks, and the electricity produced – is the domain of the individual OEMs, and here they remain fierce competitors.
“Individually, the cost of development couldn’t be justified against the volumes. However, our combined volume did,” said Senqvist. “Fuel cells are a cornerstone to decarbonise transport, and there was nothing off the shelf currently that fulfilled the tough requirement of heavy-duty trucks. This is not a ramped-up pass-car [passenger car] system. It is a heavy-truck specific design.”
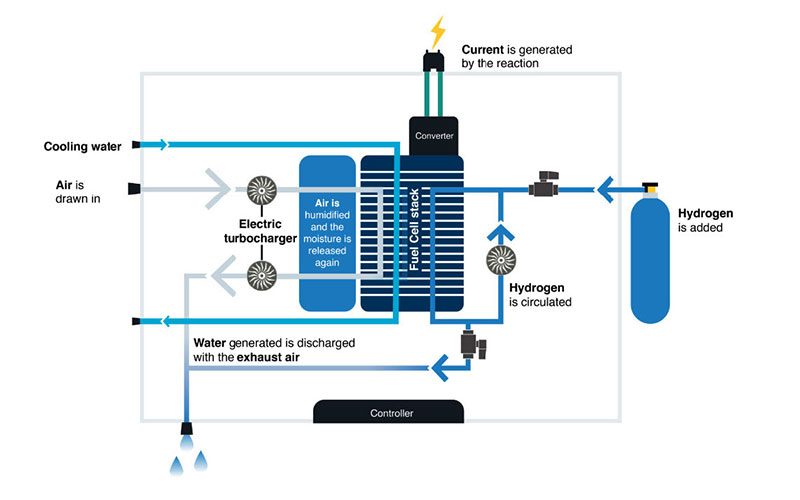
The fuel cell – form and function
Dr Florian Henkel leads external affairs at cellcentric and hosted visitors to the company’s stand at Hanover.
To the untrained eye glancing in, the fuel cells on the stand could have been mistaken for an engine of sorts – especially with their turbocharger hanging off the side. It is not a coincidence. One of the parameters in the development was a dimension envelope comparable with an IC (internal combustion) engine in what Henkel described as a ‘motor-block’ arrangement, meaning the central entity with components attached.
Robustness was a key consideration. A fuel cell must perform its delicate chemical dance amid the rigours of the shock loading found in trucking.
“In the truck, you will see 40, 60, up to 80g of acceleration in your system. Running over bumps in trucks is very different to pass-cars,” said Henkel.
“The fuel cells are subjected to ‘shaker’ test beds and in-chassis field evaluation, subjected to various terrains and extremes of temperature. The fundamental principles are the same though; harder running impacts the overall life.”
When it comes to getting your head around the fuel cell, there’s a lot in the macro-process we can all relate to. Air and fuel (hydrogen) enter and interact, and the outcome is energy. In conjunction, some level of external cooling is required, and there’s a byproduct – in this case, heat and water. No wonder it looks for all intents and purposes, like a weird little engine.
At a micro-level, however, it’s an entirely different story.
In the case of an ICE (internal combustion engine), it’s the combustion of the air and fuel (diesel or petrol, normally) that yields a release of energy. Because that combustion event is incarcerated, the energy release can be directed for use in the facilitation of mechanical work. Because of the need to combust, the whole thing yields pretty ‘yucky’ byproducts in the form of CO2 , NOx, and heavy particulates. For years, we’ve been attempting to address the latter two via the various global emissions standards. However, they don’t address the CO2 , and as we know, that’s now the elephant in the room.
In the fuel cell, the air and fuel are not combusted. Via the use of a catalyst – platinum in this case – the chemistry of the two key components is tinkered with. The electrical potential differences generated during that tinkering are captured, producing energy in the form of an electric current. (For what’s happening in the fuel cell stack, see page 102). As stated, the byproducts are heat and water.
The core cellcentric product will be the 230kg, 150kW output, 800V DC unit with a projected life of 25,000 hours. Daimler Truck and Volvo Group determined the spec with low weight, durability, a range of 1000km, and power output equal to diesel heading the list.
“The decision on the size was made around output versus weight, as well as identifying what product will pull the biggest levers commercially,” said Henkel. “Which size, in volume production, would have the most customer appeal, allowing economies of scale that will, in turn, reduce production cost. We are no longer in the R&D phase and must now focus on volume production. That will allow the OEMs to get on with their bit, as well as generate return to our shareholders.
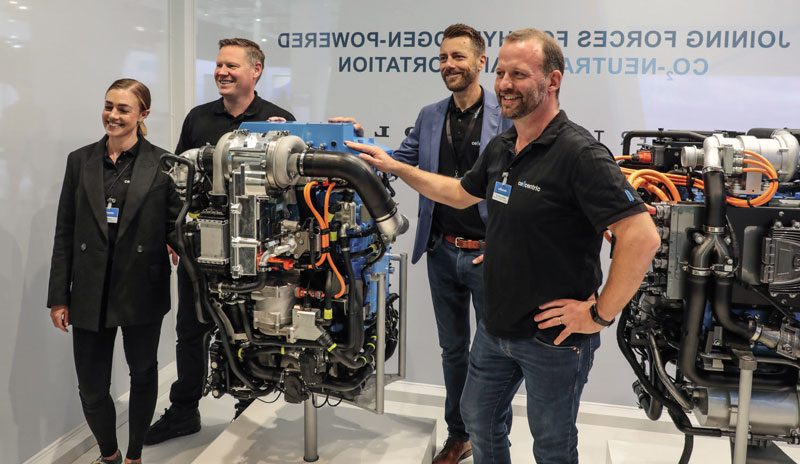
“The unit is a fantastic building block and can be paired with other units, meaning you could have two 150kW units in a truck produce 300kW, ideal for the standard European 41-tonne gross weight limits.”
The electrically driven turbines on the unit, which look like turbochargers, but are more comparable to a supercharger in reality, increase the volume of air being taken in on one side, and expell it on the other.
The output current generated goes to a power distribution unit, and from there, the OEMs can direct it as they see fit, whether that’s into a battery buffer or to some other end use.
“We are only responsible for the fuel cell. How the hydrogen is stored on the truck – whether liquid or in a gaseous state – is up to them. Likewise, what they do with the electrical current produced,” said Henkel.
“We don’t need pure hydrogen. We can take it from commercial refuelling stations. However, tank quality is always the question. Prefilters on the intake system is possible. But again, it comes down to price.
“The transition to hydrogen as part of the green-energy solution is a two-step process. There’s the fuel cell itself, but also the infrastructure. The latter is made up of the physical network, the standards, and regulatory framework. We know which impurities we can take and which ones we can’t, and we are working with authorities in the development of the standards.”
Anyone building anything today must consider ‘what happens next, looking to their product’s end-of-life journey. In that context, the fuel cell also comes up trumps with cellcentric stating a reuse factor of over 90% for the precious metals alone.
We may live in times of upheaval but, with luck we might end up with a better world out the other side.
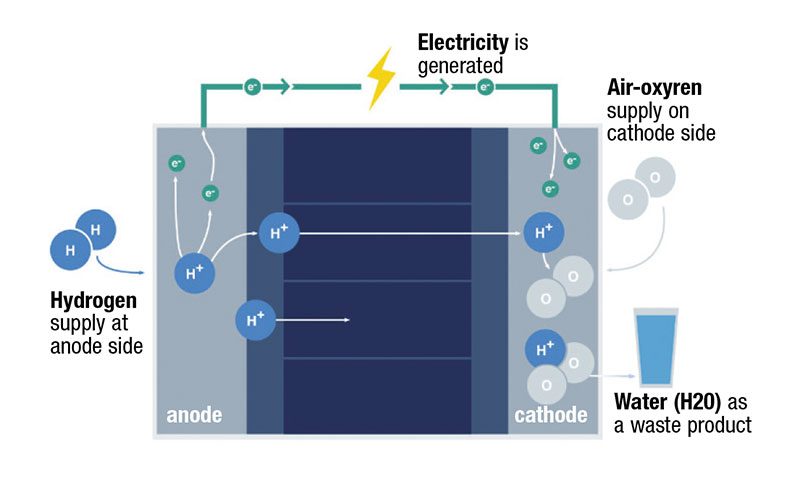
WHAT IS A FUEL CELL?
A fuel cell propagates a chemical reaction between hydrogen and water that yields electricity, heat and pure water. The systems developed by cellcentric are based on PEM (Proton Exchange Membrane) fuel cells, operated using hydrogen and oxygen from the air.
For the propeller heads among you, here’s how it goes:
1) Hydrogen is supplied to the anode side, atmospheric oxygen from the cathode side.
2) The hydrogen molecule H2 is split into two protons and two electrons via a platinum catalyst.
3) Electrons flow as electrical current through various electrical consumers, while protons diffuse through the membrane.
4) The potential difference between the anode and the cathode generates electrical voltage. By stacking several cells, their voltage can be combined.
5) The oxygen molecule is split catalytically at the cathode into two oxygen ions through the acceptance of four electrons. Every oxygen ion connects with two protons to form a water molecule.
6) The water is carried out of the fuel cell by airflow.
That’s a PEM fuel cell. But what about combusting hydrogen? Dr Henkel explains this best. “If you have a combustion hydrogen combustion vehicle, you bring hydrogen and oxygen together, but you also bring in atmospheric nitrogen. This means the hydrogen combustion vehicle is carbon-free but not emissions-free. You still produce NOx [nitrogen oxides], which has to be dealt with. In the fuel cell, you only produce heat, electricity and pure water.”
Read more
Road to Zero Isuzu styles
0 Comments6 Minutes
Ready for the harvest
0 Comments12 Minutes
VGA introduces electric
0 Comments8 Minutes
The fondest farewell
0 Comments36 Minutes