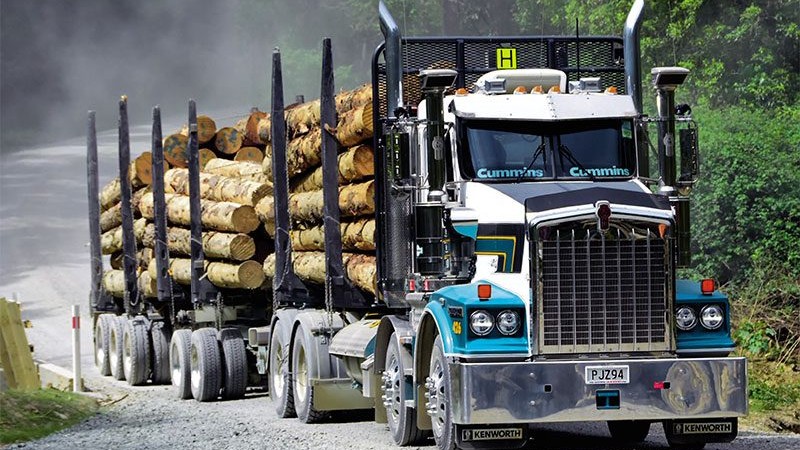
Whether physical, mental, emotional, or behavioural, barriers are there to be conquered. Walled in by physical barriers, the locals of the Tasman region have had to apply themselves to innovation, invention, and redefining the norm to keep pace in a young country that scurried to catch up with the rest of the world. As accessible and connected as we might be in 2022, that regional DNA still flourishes, finding solutions where others might see obstacles. This month we visit a company that exemplifies it all.
It’s one of those classic trucking sounds – the crunch-crunch of a pair of work boots walking across a gravel yard towards a truck patiently awaiting the arrival of its master in command. It’s normally followed by the sound of a key in a lock and the opening of the driver’s door. In this case, the release of bonnet clips comes next, then the tell-tale whine as the bonnet arcs open, almost like a good heading dog yawning at the start of a new day.
Waimea Contract Carriers fleet No.426 is a Kenworth T659 8×4 and five-axle in-house/Waimea Engineering log trailer. An aspirational log truck by anyone’s definition. A pinnacle machine designed and built for logging, the ‘five-nine’s’ success in that field is best evidenced by the number of its breed roaming the forest tracks of Aotearoa.
But like its fleet brethren in this glorious and unique part of Godzone, No.426 breaks the national mould for trucks of its make, model, and genre.
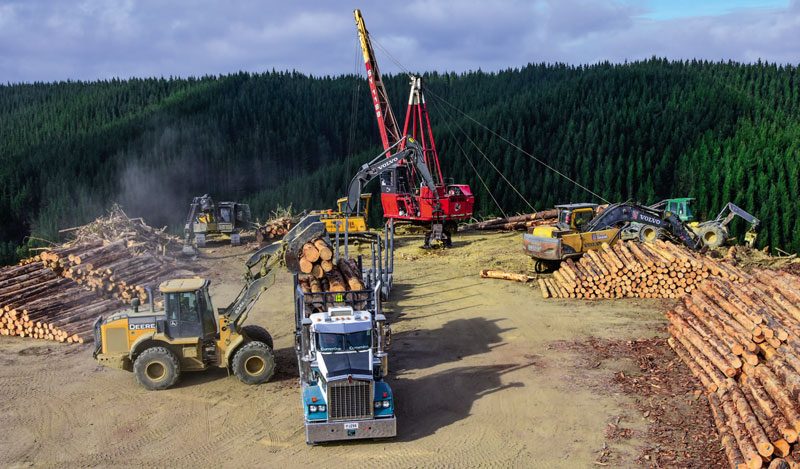
Firstly, let’s look at who is wearing those ‘gravel crunching’ boots. Tania Buschl is a 20-year veteran of the road, with eight of those years served right here at Waimea. Incidentally, she now also owns the accolade of being the first woman in charge of a cover-story machine in New Zealand Trucking magazine’s 37 years. We could do the PC thing and say that’s remiss, but it wouldn’t be right or fair on us. It’s just been the fall of the dice. But, my gosh, talk about worth the wait!
Tania is a clear sign that maybe the challenges of historical isolation help influence a redefining of normal. When hands are few, all hands are equal. There’s nothing overly special about women driving big gear in the Tasman/Golden Bay area. Waimea Contract Carriers, Stuart Drummond Transport, Sollys Contractors, Austin Transport Services, Borlase Transport and Harte Transport, just to scratch the surface, all have women on the driving roster. As company executive director – operations at Waimea Contract Carriers, Jenny McIntyre says: “It’s got nothing to do with who you are, it’s only about being able to do the job.”
Second, take a walk around this rig and you’ll soon start asking yourself the odd question, like ‘What’s that air tank do?’ ‘What the hell are they on the truck stanchions?’ ‘Crikey, that’s low!’, and ‘Air winches! Cool!’
There’s so much here your head hurts.
From whence it came
The challenges that pepper the log transport industry are relentless. Aside from the inherent risks involved in uplifting ungainly product from often awe-inspiring yet difficult-to-access locations, there’s that old Kiwi alchemy of applying first world practices and standards to a product we chose to sell in its cheapest form. Making it all happen in a way that pleases customers, compliance, and the credit side of the balance sheet is hair-pulling stuff.
What’s required is lateral thinking, innovation, collaboration, and courage. Waimea Contract Carriers was founded by the late Simon McIntyre just over 40 years ago, and he was a bloke who possessed all of the above – in buckets. As daughter Jenny says: “Dad was an incredibly intelligent and innovative man.” That’s something the company deputies of today who worked with him would second without even thinking.
Building their own trailer gear, developing log B-trains that conformed with the contours of the South Island’s mountain highways, building screens and crushers; they were all the brainchild and work of Simon, as was a sharp commercial mind. It’s been 12 years since he passed, and daughter Jenny and son Peter today hold the executive directorships of the firm their dad founded.
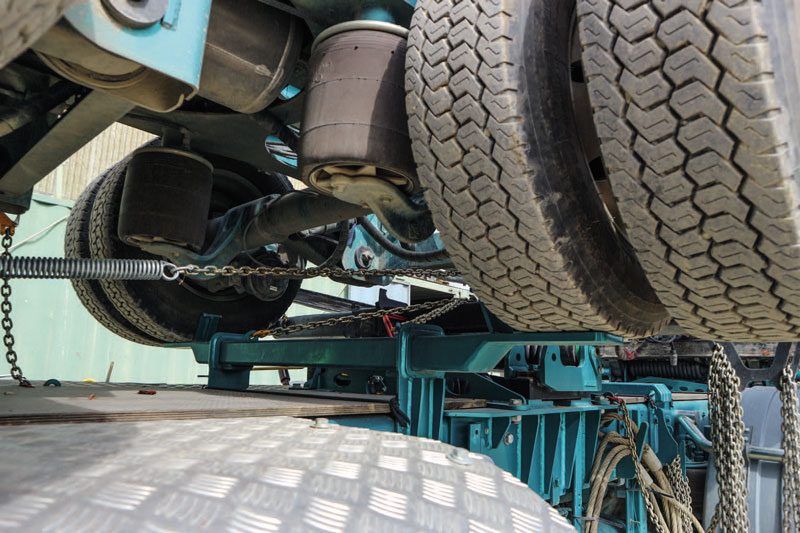
Jenny heads operations and the commercial stuff, recently winning the Teletrac Navman Outstanding Contribution by a Woman in the Road Transport Industry award at the Transporting New Zealand awards evening in Invercargill.
“The award was interesting,” says Jenny. “It’s only about competence here, that’s it. Having said that, I have certainly felt a subtle bias of opinion at times when conducting business post Dad’s passing. There are still perceptions out there.”
Peter is an engineer and his business card reads ‘executive director – engineering’. That in itself piques the interest for sure, and meeting him, you’re instantly exposed to analytical eyes and an inquisitive mind.
First, you need the pennies
Addressing the questions posed in the walk around of No.426 reveals one thing, Waimea Contract Carriers in 2022 has a tangible continuous improvement programme for the fleet, and they’re not afraid of the concept ‘try, fail, and try again’. That means there’s a real enthusiasm around projects. As you’ll read in the company sidebar, this business has been through the refiner’s fire in the past decade, resulting in a clarity of intent and direction that includes defining compliance in a way that fits with practical-thinking folk.
Take safety, for instance. It was one of the pillars they focused on when times were tough. As training and compliance manager Craig Sim says: “Yes, of course it’s always about getting everyone home safely, but nowadays it has real bottom- line advantages too.” And he’s right. In 2022, getting everyone home safely means that truck will have a driver tomorrow, without him or her, it may not.
You can only run the business you desire with the money you have. Downtime is the ultimate killer of any road transport entity, so from a commercial-welfare standpoint, keeping the drivers safe reduces downtime, not to mention allowing them to maintain the personal income stream they need/desire. It is after all the fundamental reason drivers turn up each morning.
“Plus, when something does go wrong, there’s a lot of time spent buried in paperwork and investigations. That has an opportunity cost.” When you’re a forward-facing company that must be a pain.
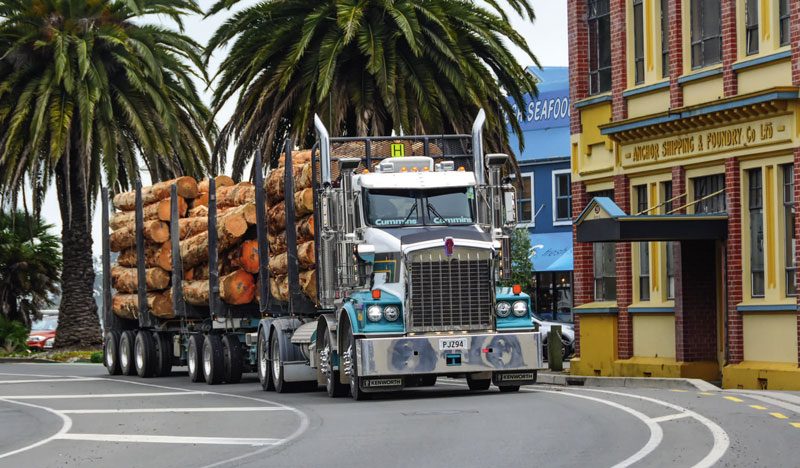
What then are some of the innovation paths that have us all here staring at fleet numbers 426 and T426? Bear in mind, not all of this is necessarily new – it’s the personal application and philosophy behind what might at times be a broader industry trend or innovation. On that note, let’s start with stanchions and trailer chassis height.
At Waimea, this issue dates back to Simon’s era and a desire to eliminate extension pins, one of the most arduous and damage- prone accoutrements on a log truck. A great move, but then the issue became retaining a productive stanchion height. To win that over, the initial enquiry concerned seating the empty trailer lower on the truck, followed by tinkering with trailer chassis heights. How timely was that?
This was the mid- to late- 1990s, and at the time, the nation’s log-truck industry had earned itself an almost pariah-like social reputation as the result of a horrific series of rollovers, particularly in the central North Island. Following an ‘if you don’t fix it, we will’ message from the law-makers, the Log Transport Safety Council (LTSC) was formed. As part of a broader suite of engineering initiatives and behavioural corrections, that body lobbied both industry and regulators for the accelerated development of lower and eventually longer trailers. Innovation in the industry was rife.
Things had settled by the end of the century’s first decade, and the LTSC had earned itself the reputation it retains to this day as one of the most effective industry representations ever.
Then along came HPMV. All of a sudden, and within the bounds of stringent design and safety criteria, the trailer’s capacity to carry increased substantially. Stanchions were needed that were now higher than ever, on trailers that pushed the boundaries of low chassis heights.
And now here we are in front of 2022’s manifestation of all that. The trailer on the back of Tania’s T659 is a masterpiece of the in-house/ Trinder & Waimea Engineering collaborative think-tank and engineering team. Headed by Peter McIntyre and Phil Kirk from the respective camps, every part of the drop-frame trailer is built and fabricated right here at the Edens Road workshops. Running gear is ROR CS9 low-mount air- suspended integrated disc brake axles with Koni shock absorbers and PSI inflation management all supplied by T.A.T.E.S. (NZ). That running gear is a considered selection also.
“I don’t want trailers with chassis that protrude over the tyre height,” says Peter.
With front tandem ride height of 250mm, and rear group of 180mm, the CS9 low-mount has one of largest SRT ratings for a dual-wheel suspension/axle system in the industry. The PSI inflation management system has the air reservoir mounted in the axle housing, which has an added benefit of being able to fit a Thermalert system if desired (ROR axles only). Say a stone gets caught in a brake caliper causing drag and heat build-up in the hub and bearing. Once it gets to 146°C, the Thermalert plug melts, draining the air reservoir and setting off a warning alarm and light in the cab.
Double-layover bolsters on both truck and trailer take care of the height when the trailer is up on the back. But the real engineering art today is accommodating a five- axle trailer on a big bonneted brute that is still able to cart three bays of 5.9m wood and comply when it’s being piggy- backed. “It’s tight,” says Peter, “but it fits.”
Frame height on the goose-neck is 1100mm, and on the lower frame 850mm with bolster bed heights of 1350mm and 1100mm respectively. In terms of advancing the discipline, the trailer can be loaded 7.8% higher than predecessors without impacting stability. ‘Advancing the discipline’. That’s the perfect segue to our next subject – keeping the load in place, and to this end, this long-standing collaborative think-tank duo may have cracked a big one.
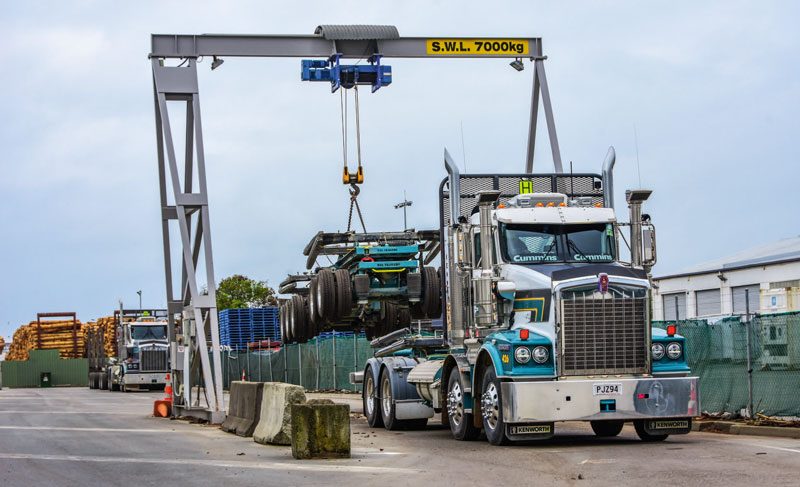
But first some numbers
“Some time back we had a staff member lose sight in one eye after he was caught with a twitch-bar, a horrible incident that no one ever wants to see happen,” says Jenny. “Securing loads in this manner was not something we wanted to continue doing.
“We moved to manual winches, with no long rack bars as the tensioning device on all new gear, and retrofitting to existing gear. But it only moved the problem.”
Move the problem indeed, and what was happening in the Tasman forests was being replicated throughout the country, meaning soft tissue injuries in the shoulder and back caused by excessive chain throwing.
Log cuts have changed as has compliance on load securing. It’s nothing for a load nowadays to require nine chassis-mounted chains, thrown over HPMV payloads. In an area like Tasman where the leads are generally short, four loads a day is quite doable. Let’s do some quick but fair maths.
If Tania does three loads, each with six to nine chains – let’s say 7.5 average for the math – and the chain coil weighs 6kg in the hand, she will throw 135kg of chain per day. Multiply that out over a conservative 224-day working year – 12 stats, holidays, all weekends off, and five randoms for sickness/funerals etc – and she’s chucking 30,240kg of chain every year. No wonder the orthopaedic surgeons in the country’s forested areas holiday in the Maldives!
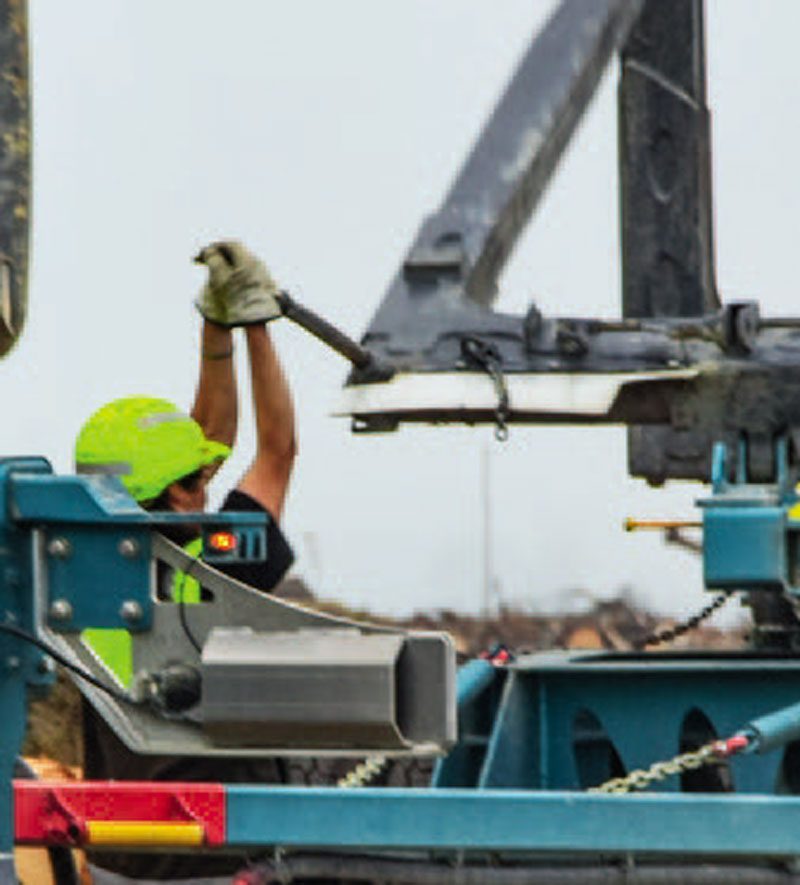
Apples and trees
“The Safety Council started running competitions to solve the problem,” says Jenny. “One of our guys came up with the ‘Gooby’ claw as we call it, a steel hook on a rope that could take three chain leaders. It was a great simple solution but not quite what the industry was after.
“So, back in 2015, Pete got to thinking and within a week he had a working ‘agricultural’ prototype of what he was mulling over, and by the end of that year it was working in the field.”
What Pete conjured up is ingenious. An air-operated rack and pinion arrangement with the output shaft from the pinion connected to a long arm with a claw that accepts a chain leader. With the leader hooked on and the chain coil laid out on the ground, a driver operates an air-release valve that charges the ram driving the rack and spinning the pinion. The output shaft on the pinion propels the arm through an arc and launches the chain.
Peter and Phil took the feasibility prototype and ‘finessed’ the concept with Trinder’s design team into an Alpha prototype. They rigged it up in the backyard at Waimea Contract Carriers, and set it going.
As it turns out, humans aren’t that strong, because their initial pressure settings launched the chain almost into space.
“The guys would come in and sit in the the designated smoking container out the back and watch it going, critiquing each launch,” laughs Jenny. “They’d say, ‘Yep, that’s better than I could do’, or, ‘No, that’s shit’. In the end we got it to one-in-50 being a fail.”
Initially, a couple of trucks and one trailer were retrofitted with the thrower mounted outside the bolster, but No.426 and a couple of other trucks have full beta prototype, mounted integral in the stanchion. This means only the pinion drive pokes through, with the arm snug against the stanchion.
At the time we put the story together, Peter and Phil were working on the first new trailer fitted with chain throwers, and by the time you read this, you will likely have all seen the grand reveal at the TMC Trucking Industry show in Christchurch.
“We have to acknowledge the outstanding support the project has had from both ACC, and FGR (Forest Growers Research),” says Jenny. “They have both been an integral part of getting it to where we are today.”
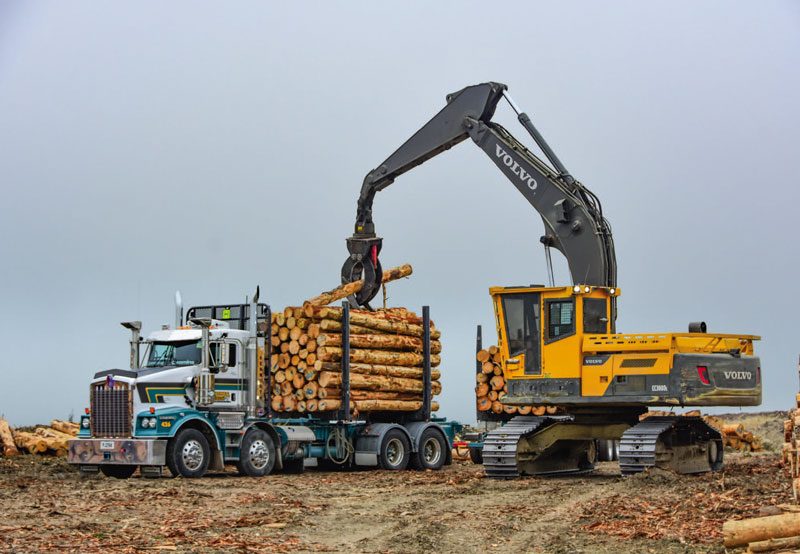
To the woods!
There isn’t much that beats a strop into the woods in a log truck. Our time with Tania would see us track her on four loads, and visit two skid sights to watch her load; one at Dovedale Summit at the head of the Pigeon Valley, and the other in the Eighty Eight Valley that runs inland South from Wakefield.
As we all know, there are regional quirks to culture whether societal or occupational. Speaking to the South Island logging scene, drivers loading out in the ‘stupid o’clock’ time slots have always loaded themselves. Although it means another whole layer to the skillsets required, it does increase load- out flexibility immeasurably.
Nowadays, things have evolved, and the self-loading drivers form a portion of the regional workpool, with some choosing not to take on the extra responsibility, and others progressing their training and unit standards to the point where they will join ranks of those that can. Like all industries in 2022, it’s about cooperation, accommodation, and aspiration. The days of ‘do it or there’s the door’ are long gone.
Tania’s background includes farming, truck driving and machine operating. The skills from those occupations meant she was a coveted resource once she decided to give log trucking a crack almost a decade ago.
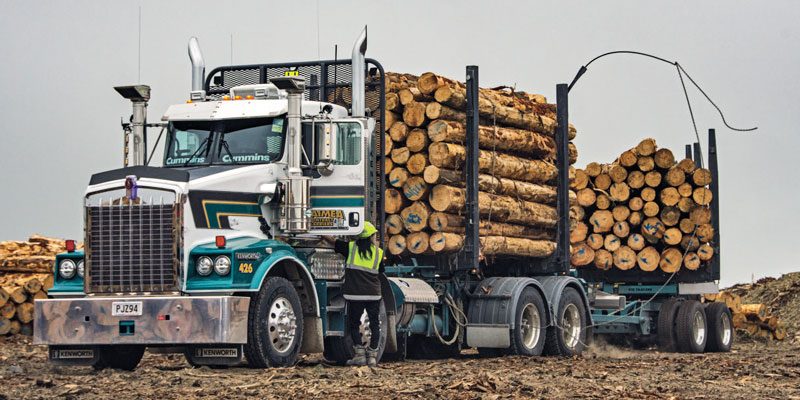

We last saw Tania as she entered the Eve’s Valley Sawmill far below with a load we’d brought in from Hira, at the foot of the Whangamoa Ranges northeast of Nelson.
With many workplaces being somewhat of an enigma in 2022, we weren’t able to see that load come off, so shot ahead to where we were now, high on a hill at the intersection where Pigeon Valley Road becomes Dovedale Road, crossed at that point by the forest road from Eve’s Valley as it transitions to Stanley Brook Road.
The tell-tale plume of dust in the distance told us a log truck was approaching and the bark of the Jacob’s shortened the odds that this would be Tania. Chaperoned by cadet Sam Phillips from Waimea Contract Carriers, we follow her into Nigel Bryant’s Logging operation.
The loading apparatus was a John Deere 624K MkII. You can’t argue Tania cuts a diminutive figure on a log skid, but her execution of the required skills is sublime. She moves about confidently, without haste, every task done in a systematic fashion. Erratic is not in this lady’s vocabulary.
“I just do my thing how I like to do it.”
The trailer off, hooked to the truck and placed, Tania has a neat bar that slots into the bolster bed, allowing amplified purchase and making the task of standing the bolsters up a piece of cake.
Back in the John Deere, she sets the bed layer before sculpting a perfectly crowned load on the truck, followed by the two bays on the trailer. There’s no revving, she just glides around, and picks, places, checks, taps-flush, and compresses the load. The SI-Lodec scales read out to her tablet, so she has no need to get out and check weights.
Once happy and out of the loader, she beckons us over. Now for the real show. Tania loves the chain throwers, and freely admits manual chain throwing is the hardest part for her.
“Sometimes I take a couple of goes. I can hardly wait to have a trailer with them.”
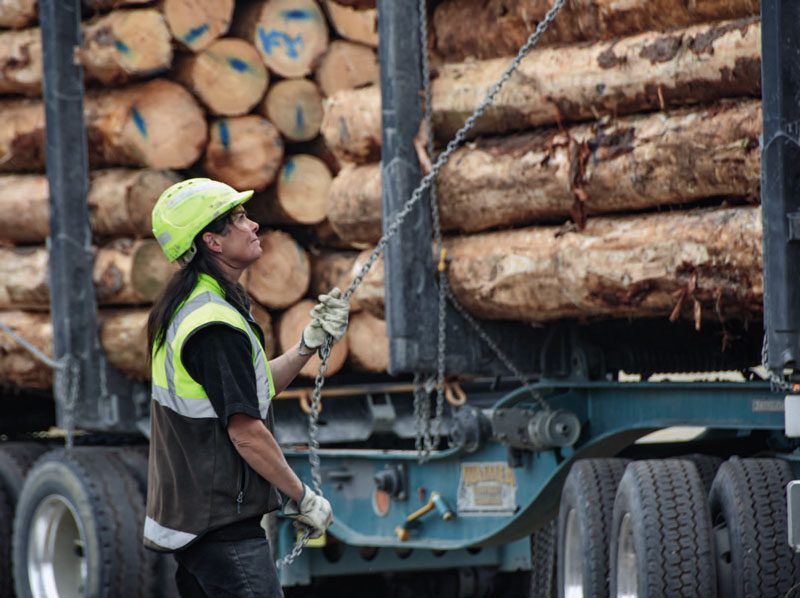
Jenny says general acceptance of the technology has been great, and even the squinty-eyed cynics now buy in totally.
Tania pulls the chains off the carry hooks, and lets them drop on the ground. She unclips the rubber lock that secures the arm to the stanchion when travelling, and hooks the chain leader in the claw.
Often when something new comes along, there’s a value-add you either never really thought about at concept, or just evolved as the discovery process continued. The throwers are operated from a valve under the passenger seat, ensuring the driver is nowhere near the flailing arms. Better than that though, a camera showing the right-hand side of the truck outputs to a screen mounted in the same place, meaning Tania can see the entire right- hand side of the truck prior to releasing the thrower on the left-hand side. This is workplace safety – platinum!
“Count me down,” she
laughs.
“Three, two, one, go!”
There’s a hiss and the arm arcs over the load, releasing the chain.
“Wow! How cool is that?”
“Oh shit!” she says. “Bugger it! It’s not gone right over. It hardly ever does this!”
“Hell no, that’s epic!” All that had happened was the chain had slipped off the crown, a daily log thing, and she could still easily grab the leader from the right-hand side and give it the ‘logger’s’ flick’. All good. She’s a ripper.
The back chain flew over and landed perfecto!
“There! That’s it. That’s how they go,” she says.
You know an invention has it nailed when the old way instantly looks archaic. And that is exactly what we felt watching Tania throw the chains for the trailer. Something utterly familiar three minutes prior… yet it looked a cumbersome historic act.
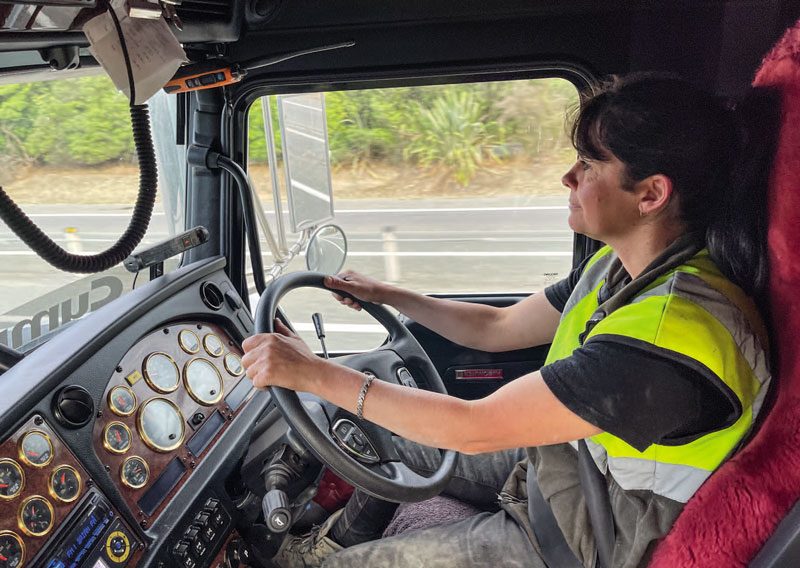
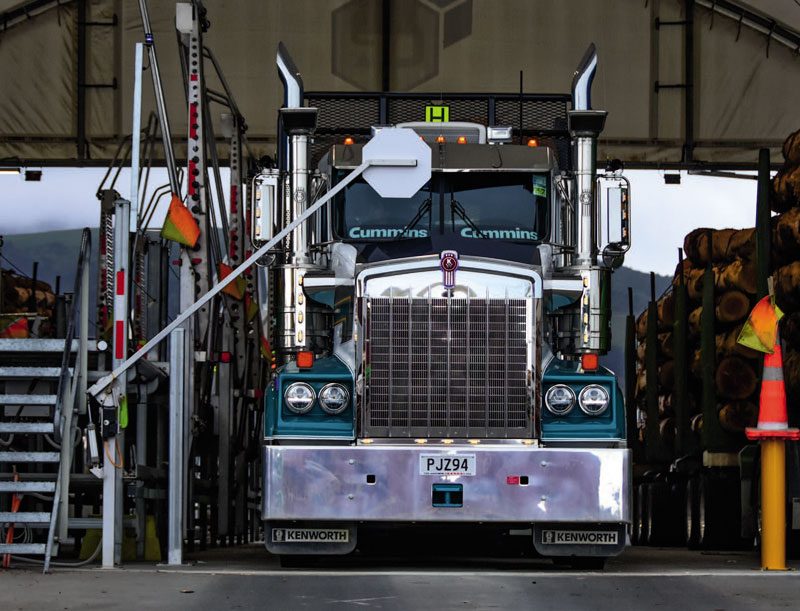
When calm prevails
Loaded, Tania hooks the dog of the chain-tensioner onto the load chain. She flicks the switch and the tensioner spits its rhythmic squirts of air and the chain comes tight. “Easy, eh? And they keep tightening as I’m travelling if the logs settle a bit. You can hear them ticking.”
Incidentally and unsurprisingly, Peter and Phil, the dynamic engineering duo, saw potential in building the tensioners, and have an in-house unit on trial on one of the other trucks, capable of bigger chains and increased tensions. In time, the final safety product offering constant tension will be integrated into the auto-tensioner. However, as it stands, it has a load- monitoring system able to be retrofitted via a D-shackle, alerting the driver in-cab if a chain comes loose.
Tania sets the Big Foot central tyre inflation to the required traction setting and pulls off the skid. The big X-15 gives a snarl as she pokes it at the gnarly little climb up to the ridgeline. Second high- split is the chosen cog, giving the motor plenty of wiggle room as she winds away from the skid. A seasoned operator, there’s no confusing the truck’s ambition with its abilities, meaning no hastily grabbed gears on account of a gradient that’s got your measure. Only as the big motor starts to sound its ‘knocked the bugger off’ howl do we hear Tania summon the next few sprockets to duty as the combination disappears into the dust.
In the cab, she’s completely at home, with the left foot idle most of the time as gears are picked off on the way up, or gathered back in on the way down.
“This is my second 659. The last one I got off the previous driver, but this one’s new. I really like them, they’re a great truck.”
We know this drive-line better than our own children by now. In the Waimea Contract Carriers deployment, power in the Euro-5 X-15 sits at 410kW (550hp) and torque 2508Nm (1850lb/ft). It’s perfectly pitched at the short lead, high stop-start nature of the work. There really is nothing to be gained in this region by ‘tapping-it-out’, either in output or the way you drive it. Backing off the output stresses may well engender improved service life also.
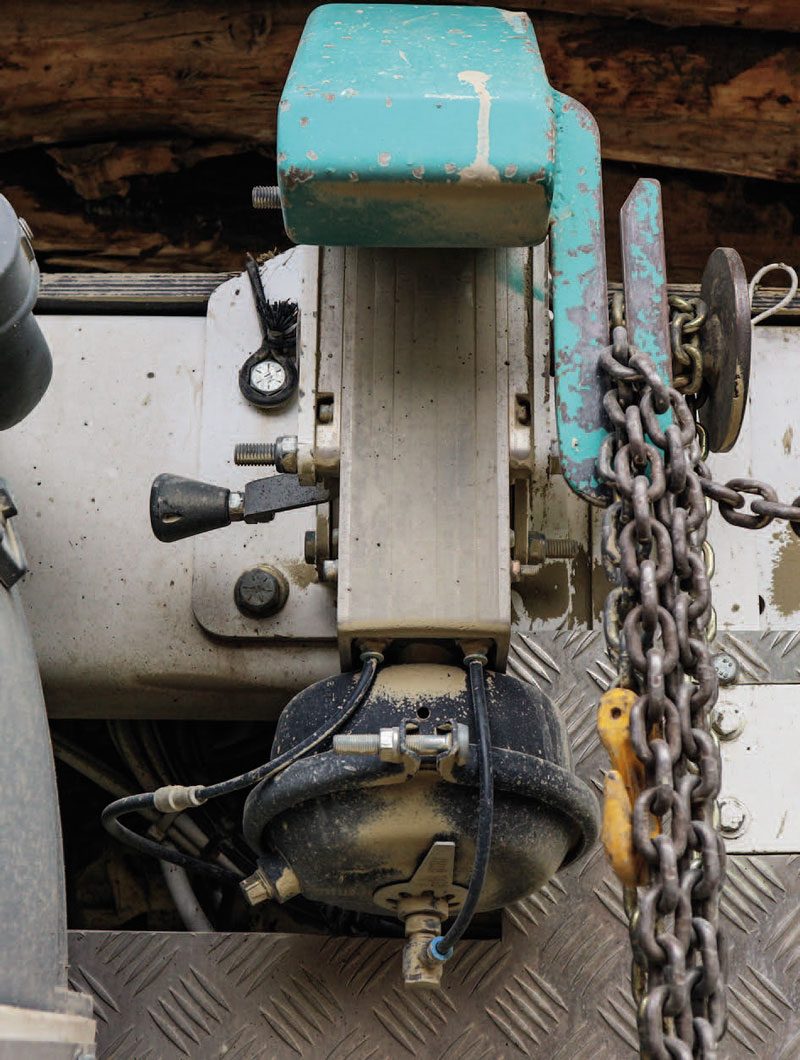
Behind the big red motor is the venerable Eaton Roadranger RTLO20918B 18-speed manual transmission, and sitting out back are Meritor RT46-160GP rears at 4.30:1, with dual diff-locks and cross-locks on both axles. Up front Meritor dual MFS66 at 13.2 tonne combined capacity sit on taper-leaf suspension without load-share, and holding up the after-guard is Kenworth Airglide 460 eight-bag air suspension at 20.9 tonne capacity. Brakes are drum. Now if that’s not a spec you’d bet your Shane van Gisbergen memorabilia collection on, what would be?
Interestingly, those who’ve been around a while will remember Waimea as a Scania stronghold for many years, with Freightliners entering the fray in the early part of the last decade. In recent history, Kenworths have arrived en masse. Today Waimea is most definitely a Kenworth stronghold.
“The Scania’s are a good truck, we’ve got one of the new generation in the fleet,” says Peter McIntyre. “It’s 18 months old and hasn’t put a foot wrong. The cabs are second to none in the way they’re constructed, and the drivers loved driving them. The problem was the availability of parts and the proprietary nature of individual machines. We found too much variance in third-party systems on the trucks – things like fuel and injection systems. You might have 10 trucks, all identical models, but under the skin there were differences. Plus, being proprietary drivelines, there were no options where parts were sourced from. About 10 years ago, we were taken to Aussie to look at the Kenworth option. Big basic trucks, third-party componentry in the driveline meaning parts from multiple suppliers. We were also shown a timeline for the current power train, so knew everything wasn’t going to change tomorrow. And Southpac’s support is fantastic. Their agent here, Commercial Vehicle Centre, are just fantastic. It’s been a great decision, and worked well for us.”
The port in Nelson is on the northern side of town, with SH6, Whakatu Drive, and Rocks and Haven Roads the heavy-truck route in from the south and west. It really is one of the more horrid port accesses for trucks in the country, with no real bypass options, short of spending half of Elon Musk’s net worth and enraging every environmentalist this side of the equator. As it stands, you pass through industrial Richmond along the motorway deviation, past the airport, then a chain of commercial and residential zones broken by Tahunanui Beach, no less. It’s people, cars, mayhem, families and cyclists, with at least half of it dual carriageway only. Once you arrive, the port feels like a sanctuary, relatively speaking. For Tania and the hundreds of truckers in the region, it’s home sweet home. To us outsiders, it’s ‘Crikey! that’s a pain in the arse’.
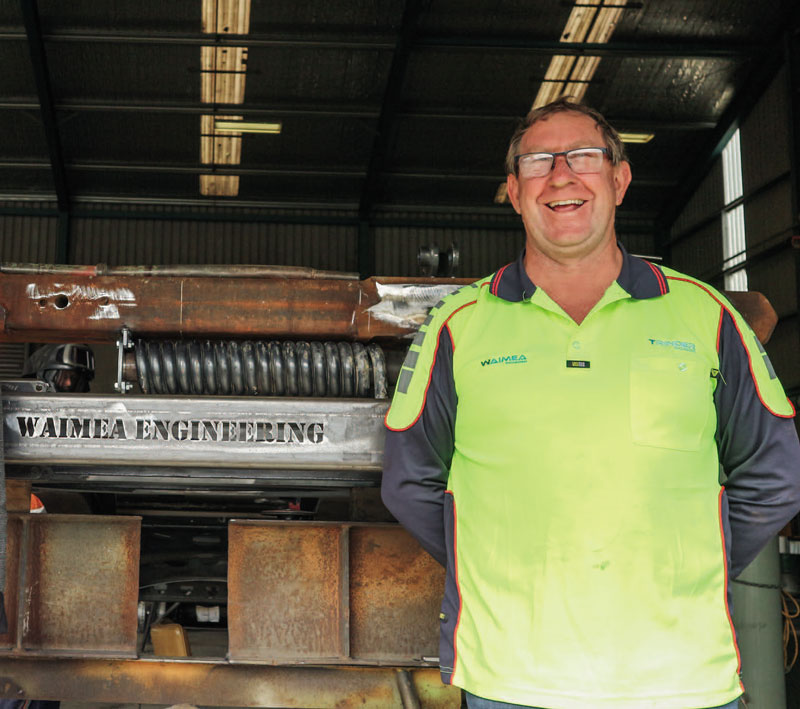
The normal port-side process of tagging, unchaining and unloading takes place, and then it’s around to the gantry for trailer-up. Nelson has a great setup. The weighbridge and gantry are right alongside each other, both on concrete or bitumen, and the gateway in and out of C3 is just over the road. It’s really fast and compact, almost making up for the trauma of getting there. Our next rendezvous with this uber-cool log-truck lady is the following day up the Eighty Eight Valley to Raku Logging’s operation. A lovely drive out through Hope, Brightwater and then into Wakefield to the southwest of Nelson, where we turn left and head up the valley. About 15km in, we turn into a farm gate and drive up the race to the forest access road. It’s a windy old trot up the gully but the Kenworth and pilot are completely unfazed.
The access to the log skids generally appears first rate, considering the mountainous and hilly terrain of the region. Likewise, the load-out pads on the skids were all user-friendly. This was no coincidence. The forest companies, harvest crews and carriers have established an effective working tripartite in Tasman. Whenever a new road and skid is coming on stream, representatives from each visit the access roads and load-out site to discuss potential pitfalls. In Waimea’s case, Craig Sim and health and safety manager Margaret Klink comprise the company’s representatives.
“The forest companies are fantastic,” says Craig. “If we want a corner opened out, a bit more turnaround space on a landing, or hard material on the load-out, it’s never a problem.”
This level of dialogue and cooperation has its roots in the nature of the work here, with the self-loading drivers in the wee-small hours. “It’s no use having someone stuck on skid and having to send a ute up at 2am to get them.”
The communication extends far beyond the gnarly bits. Local community needs concerning noise and traffic flows, school bus runs, even forest exits where the sightlines to the first corner are a bit tight, are all taken into account. “We can install flashing lights on roads that the drivers activate via their RTs to warn traffic approaching that a log truck might be pulling out just around the corner. It grabs their attention far more than just a sign. All we’re trying to do is ensure that by the time the trucks arrive at a new location, no one’s set up for failure.”
High on a foggy old hill in the Eighty Eight, Tania spins the rig around and lines it up with the exit ramp.
This time, there’s a Volvo EC300DL tracked grapple loader for the payload- deploying honours. Thirty- tonne is certainly at the higher end for log-truck load-out duties and it takes up a fair old footprint. The Kenworth’s ego must be feeling slightly dinted as it can’t lay claim to dominating the picture on this occasion.
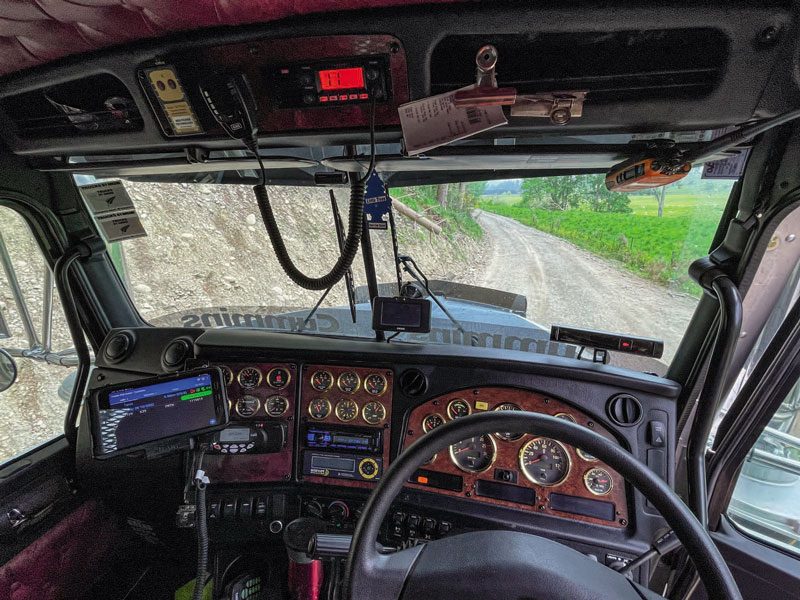
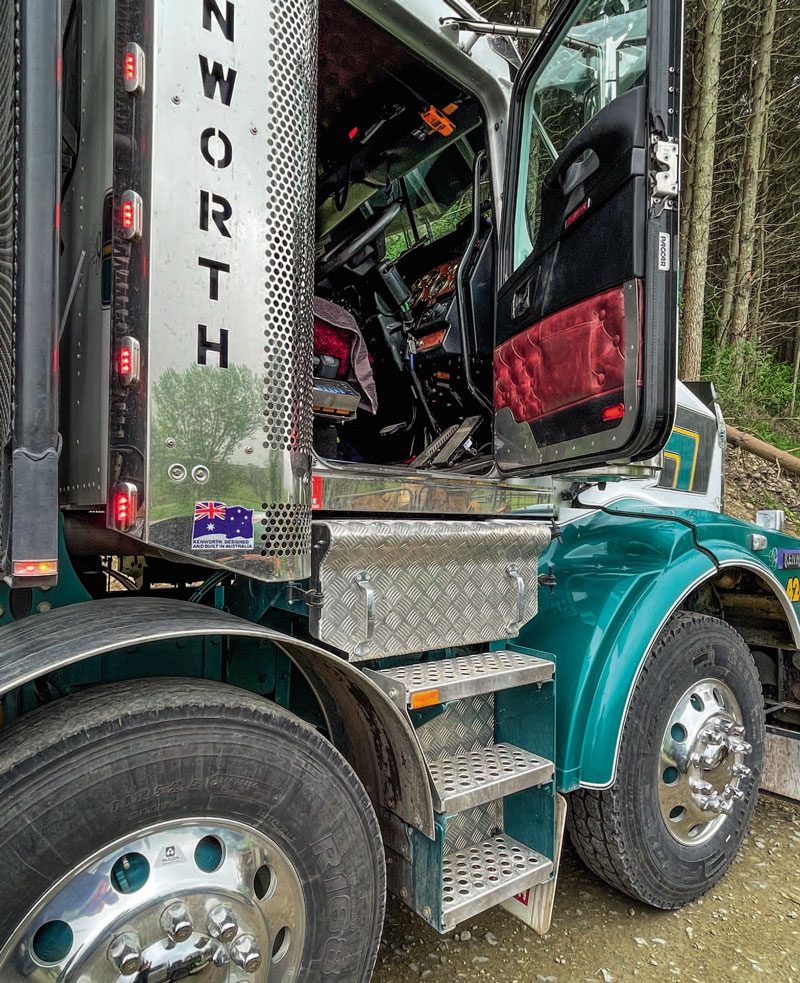
Tania climbs up and soon that familiar hum, the digger’s key life sign, fills the air. Like a huge pet insect, she wakes it from its slumber, gently lifts the trailer off the Kenworth’s back and sets the rig up for loading.
Like the motion of the machine itself, erratic moves in the cab as you try to keep tabs on exactly where everything is are always a hint of nervousness. But Tania’s silhouette sat comfortably in the seat, her head largely motionless but for the occasional glance at the log stack or truck in the act of building her load. The grapple was always doing exactly what she wanted – close and press, or the gentle end tap to keep all passengers vertically aligned.
Job done! Chain demo No.2, and this time a 100% strike rate.
The pull away from the skid was easy up onto the ridge and then a long winding descent all the way to the road. The Jacobs did what they’ve done for 61 years and kept proceedings in check as Tania guided her charge out of the woods.
The 659’s cab is a snug office, small by today’s standards and looking more and more full with the addition of so many of today’s essentials, things like job tablets, Seeing Machine, bush radios, EROAD screens, etc. It’s your classic Kenworth setup – wood grain and gauges, big buttons, lots of hardy scrubbable surfaces, and crimson buttoned upholstery. There’s no real commentary to be had – fans are fans, those who aren’t, aren’t. In terms of somewhere to execute your task when things get busy in the act of dragging wood from the bowels of a gully, or off the top of a ridge, there are few places that are its equal, hence its prevalence.
As high as it is, there’s plenty of steps and grab handles so Tania has no problem ascending to one of the world’s more famous vehicle cockpits.
“Driver acceptance of the Kenworths has been great,” says Peter. “Initially, there were a number of people who were ‘Scania hard’. Most have been surprised by the Kenworths, and a couple who were offered the chance to go back, have chosen to stay with their trucks.”
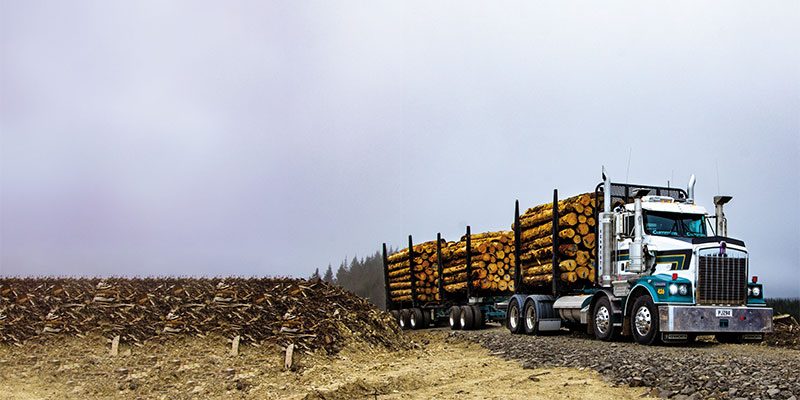
Giants come in all sizes
We stop for a yarn with Tania out on the access track to the Valley road. It’s all in a day’s work, for this lady of the land turned machine operator and log truck driver. She’s at the top of her game. You can tell by the way she carries herself and how the other drivers interact with her. The respect is mutual. As slight as she might be, she’s not intimidated by anything, or anyone, and like the best, she’s humble and friendly. It’s the old chestnut, the good ones never regale you with how good they are. She’s a fantastic role model.
The truck? We know the truck inside out. This machine’s proved itself beyond the need for critiquing and finding pedantic nuances that speak to not much. Yes, there are better trucks nowadays in terms of visibility, space, comfort, safety tech, and power. Like I’ve always said, the most effective safety feature on a truck still sits in the driver’s seat and to this end, fleet 426 is as safe as houses.
If you are a log-truck operator and signing the sale and purchase for something that will be the family breadwinner, the 659 would have to be on the shortest of shortlists.
Waimea Contract Carriers – an epic family story where ambition meets innovation, meets perseverance, meets identity. Hailing from a region whose historical isolation has proved to be its greatest gift. The business’ challenging journey of late has instilled a clarity, ethos, and value proposition not often seen in the second generation. Their collaborative success with suppliers, customers, and staff is redefining the relationship between safety, productivity, and prosperity. Long may it all continue.
Quick reads from Test
Read more
The right man for the job
0 Comments29 Minutes
Legendary ambition
0 Comments36 Minutes
Hard Fought!
0 Comments40 Minutes
Postal Trifecta
0 Comments29 Minutes