A step ahead
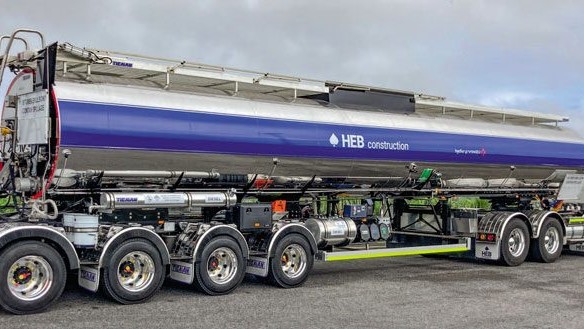
Infrastructure company HEB Construction recently took delivery of its first unit from Tieman Tankers. The quad-axle stainless bitumen tanker has been paired with an existing Mack Granite, itself having had a front-to-back refurb, to make for one of Canterbury’s most eye-catching combinations.
Tieman tankers have become increasingly common on New Zealand’s roads in recent years. Supported in New Zealand by Total Transport Engineers (TTE), the family-owned tanker- trailer builder from Victoria has found favour across the ditch due to innovative design and build techniques, quality products and personal support.
The last time New Zealand Trucking featured one was in March 2020, when Road Science put its new B-train bitumen tanker into operation. According to TTE’s Craig Gordon, about 15 Tieman bitumen tankers and one fuel tanker are in operation in New Zealand – the latest of which is this 31,350-litre, quad-axle unit for HEB Construction.
The tanker was commissioned to service the Selwyn District Council reseal contract, which had changed methodology from hot cutback to emulsion. This district is one of the three largest networks in New Zealand, with 4500km of road (about 1500km sealed), meaning the unit’s 28,700-litre safe-loading limit was a key requirement.
“Emulsion binders contain upwards of 30% water. By the time we’re spraying the road, we’re losing 30% to evaporation. That’s why the volumetric increase was critical to our ability to achieve the productivity targets,” explains Tim Clark, South Island surfacing manager at HEB Construction.
Grant Moffat, national plant manager, explains that HEB Construction has stringent environmental targets to achieve. “Our target is a carbon reduction of 40% by 2030. We need to consider things like heating, heat loss reduction, reduction in fuel burn… this all applies.”
Clark continues: “Thermal efficiency on a unit like this is a critical and an integral part of the design. Emulsion runs at about 85°C to 90°C. We burn a lot of energy keeping it hot, so we need to be able to retain the heat and reduce our carbon burn on the generators and burners. The reduction in energy burn thanks to the tanker’s thermal efficiency is a big environmental tick.”
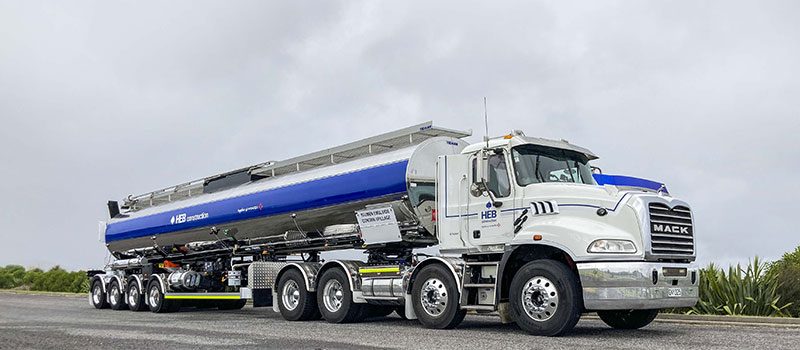
Impressive spec
The tanker is fitted with two 7kW ‘Hotco’ heating elements and one U-shaped burner tube fitted to the tank barrel and coupled to a one-stage, single-phase Riello diesel burner. Powering it all is a single-phase Yamaha 4.1KVA generator. The system is controlled by a New Zealand-made ElectriServ electrical PLC control box. Colin Tieman, director of Tieman Tankers, notes that using local suppliers where possible ensures good aftersales service.
Brendon Partridge, sealing supervisor, adds that even the generator has been incorporated with forethought. “It’s a really good unit and integrated so it’s easy to slide out for regular maintenance. They’ve made it easy for mechanics to access it.”
Nathan Wingate, technical support (plant) at HEB, adds: “There’s a thought process behind it all. For example, the safety shower system, or the trailer brakes interlock so it can’t be moved with the hoses connected.”
At the centre of it all is Tieman’s ringed stainless- steel tanker construction, an innovation led by the company in 2001. As a unique design of the barrel construction, the ‘Hat’ section structural stainless steel rings are fully welded to the barrel. This offers numerous benefits, among which is a reduced barrel thickness from 4mm to 3mm because of increased strength, resulting in lower tare weight and higher payloads.
The rollover coaming, barrel mounts to chassis, and the chimney are also stainless steel. The barrel mounts are huck-bolted to the suspension subframe, which reduces the risk of cracking due to the high temperatures required for the product, compared with welding.
The tank benefits from an additional automatic pneumatic vent designed by Tieman Tankers, which means climbing on top of the tanker to open the top hatch when discharging is no longer required. Extra maintenance hatches have been fitted so future internal cleaning can be done safely in confined spaces, and an added bottom cleaning port has allows easy removal of decoking residue. An air-purge system fitted to the rear discharge line allows the operator to check for any blockages before pumping out.
In the case of emergency, E Stops to shut down the hydraulics are included.Should there be a failure in a product hose when pumping, the driver can run to a safe area at the front of the tankers, away from the outlets, to shut down the pumping. Finally, the 45-litre pressurised shower, with shower heads located on both sides of tanker, is in place should an emergency burn accident require immediate and easy water treatment.
“Tieman’s solution means there are no future maintenance costs to barrels or loss of revenue through downtime of assets,” comments Colin Tieman.
“While capital cost on stainless-steel ringed tankers is higher, the design has proven over 20 years that it offers the lowest lifetime operational costs, which quickly pay back the investment.”
For New Zealand
TTE’s Craig Gordon says the fact Tiemans works to New Zealand regulations means getting the unit onto the road is as quick and simple as possible. “The EBS brake kit is sourced in Australia but set up to be New Zealand-compliant, the same with the electrics and DG spec. The paperwork is sent to a certifying engineer in Auckland, and when we get it here, it’s inspected for any remedial work or signed off. Then it’s just a case of taking it for a COF, RUCs, compliance, and grooming it for handover.”
The Mack Granite at the head of the combination came out of the HEB heavy- haulage fleet – not that you’d know by looking at it now. “We stripped it all down, gave it a full sandblast and repaint, straightened the bumpers, polished the wheels, fitted a new Holland Kompensator fifth wheel, and cleaned up the upholstery inside,” Gordon says.
The truck is fully DG-compliant and runs the likes of Eroad and Guardian Seeing Machine. “Refurbishing it to a new standard makes an impact on the driver. The drivers really own them, are proud and take care of them,” says Moffat.
Behind the wheel is Steve Young, who’s been working with HEB’s surfacing operation team for about eight years.
“He’s very passionate about it. We have the right guy in the right bit of kit, which is awesome. It is quite a big barrel, so he plans his routes carefully. But he says the rear steering axle helps heaps, and he doesn’t really notice the size, saying it tows great and it sits behind the truck nicely,” Partridge says.
Collaboration and partnership
From the ground up, the build has been a collaborative effort to create what the team wanted. Daryl Holden, now retired, kicked off the groundwork and build process. “He was integral from the start – his initial phone call with me about where we were going, what we were doing and what was needed. He got all the technical things right to make sure it could get down the road legally and with as much capacity as possible,” Clark says.
“Darryl saw there would be a need for something of superior quality than what we’ve seen in the business before,” comments Wingate.
Moffat adds that the collaboration includes the team at Tiemans and TTE. “We can’t overstate the impact they had opening our eyes to other opportunities.”
Partridge adds: “You start with a vision in mind, and it was good to have Tiemans show us what they had to offer and what they’d done with Road Science. They have some cool, cool stuff. It’s simple, but for safety, it’s huge.”
Clark concludes: “As a family business, Tieman’s ethics and values align with our own. Collaboration and honesty are all part of that – to make sure we get to where we need to be. That made the whole relationship easy.”