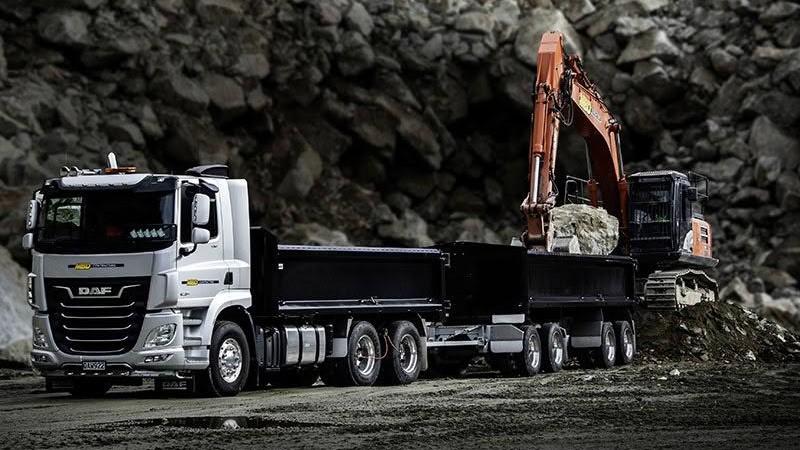
The Inca and Egyptians of past millennia will either be in awe or scoff at the way we choose to move big rocks, but there’s no doubt Greymouth’s MBD Contracting has it nailed for the needs of our time. This month, we check out one of the company’s latest DAF CF 530s, and discover the relationship between mineral, machine and management is far more nuanced than you might think. As with everything in life – approach and attitude is everything.
From the time our earliest settlers arrived, those who understood the interaction between land, sea and weather would have been acutely aware any habitation on the South Island’s West Coast was going to be a tough nut to crack. The prevailing weather arrives from some of the globe’s biggest rain and wind factories, clobbering the gigantic rock wall that is the Southern Alps – themselves a byproduct of warring tectonic plates far below the new inhabitants’ feet.
As a result of these gargantuan natural collisions, the immense volume of water careering down the majestic river valleys of Westland on its brief journey back to the sea can be all-powerful. Whether a forty-tonne boulder or a bridge the pioneers laboured tirelessly to construct, in this place, they can be dislodged like a kid kicking pebbles. The only thing to do once ‘Mother N’ has done her thing is start again and rebuild. Only better this time.
Of course, that’s where we humans come into our own. Our greatest attributes have always been desire, resilience, a big brain, an opposable thumb … and maybe a pinch of foolhardiness.
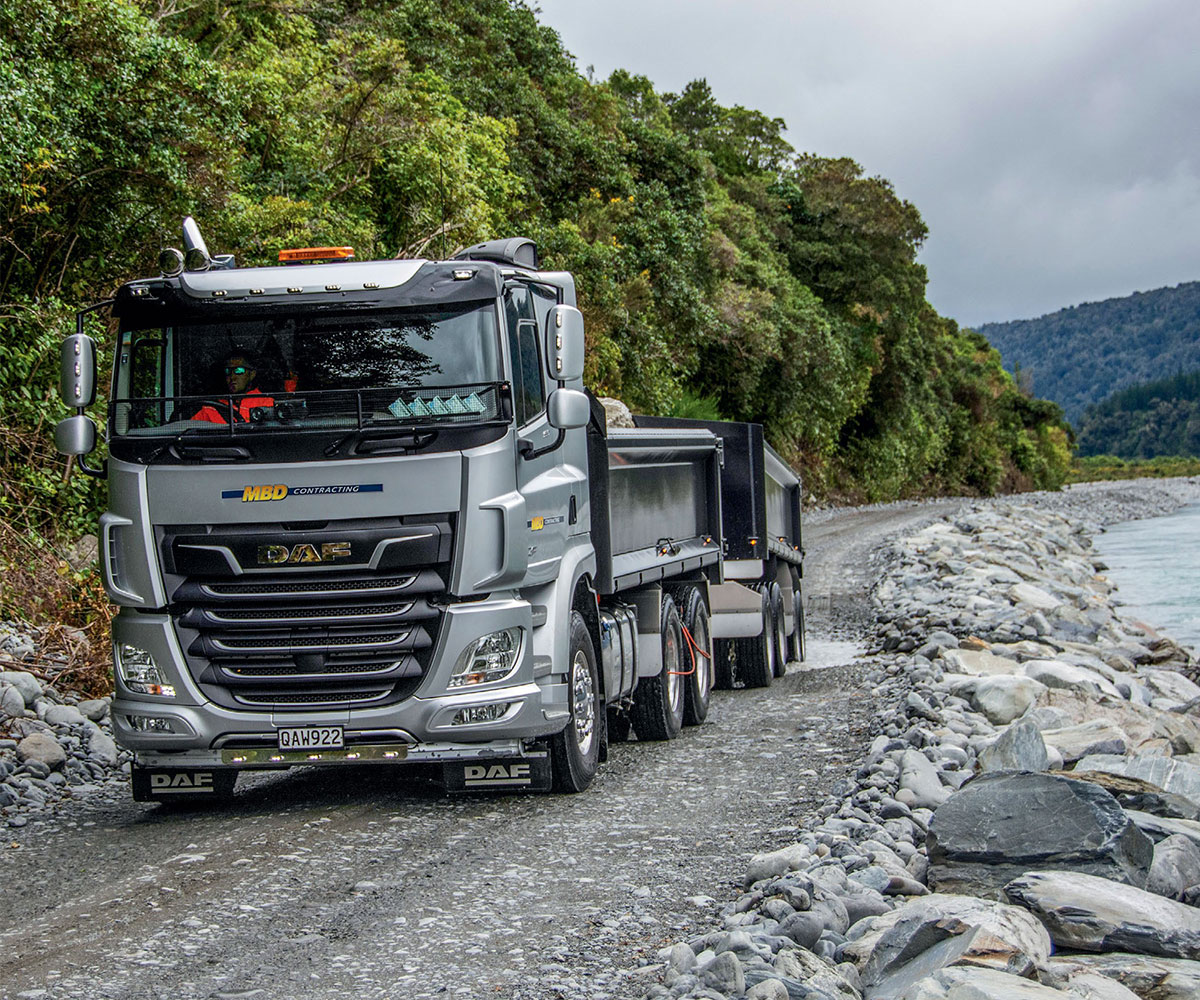
Many things trigger our desire to take on and live amid nature’s fury – but for the most part, they are riches, resource and, on occasions, the fruits of isolation, and the West Coast can certainly lay claim to all of those enticements for its migrants over the past couple of centuries.
Today, three road corridors breach the alpine divide connecting the South Island’s west with Canterbury and the south. To the north, SH7, the Lewis Pass, joins Westland and Tasman’s western flanks with North Canterbury, and for the most part, it is the most docile physical barrier. Some 435km to the south, SH6, the Haast Pass, joins South Westland to Otago, and then through the middle from Kumara just south of Greymouth, is the mighty Arthur’s Pass. Arthur’s not only provides the SH73 road corridor, but also the solitary vital rail link. It connects the west’s most populated and commercially active areas to the South Island’s commercial epicentre, Mid-Canterbury. Yet it also poses the greatest physical barrier, and is by far, the most difficult to keep open. ‘Sheesh! Wouldn’t you know it!’
Boulder it, and they will come
In the west, Jacksons marks the point where road and rail meet and head east, and Springfield is where things chill out and nature’s threats abate significantly, the modes running side-by-side almost the entire way across the Canterbury Plains to the Garden City. Keeping the transport infrastructure functioning on the 116km between Jacksons and Springfield requires an enormous, relentless, and expensive effort. The stretch is home to some of the globe’s engineering marvels – the Otira (rail) Tunnel and the Otira (road) Viaduct being the two standouts – the latter essentially built at the base of a scree slide. Many said it couldn’t be done, but we had a bit of No. 8 wire as we always do, and by the end of the last century – bingo! – there it was.
Greymouth-based MBD Contracting is a civil engineering and contracting firm servicing the entire West Coast and parts of Canterbury. It specialises in moderate to large-scale civil works, earthworks, quarrying, and rock protection, including a lot of infrastructural resilience projects and sub-surface roading. The plant comprises eight trucks (DAF/ Kenworth), 26 diggers (Hitachi/CAT), six articulated dump trucks (Volvo), plus assorted specialist support kit. It is a slick, immaculately presented operation and a proud West Coast homegrown brand. Formed in 2007, directors Darren Richardson and Ben Haddock are two of the original founders, and today, with staff numbering in the mid-30s, MBD’s cultural pillars point to people, quality, cleanliness and a social licence to operate in the community the team all grew up and/or live in. A large percentage of the staff who came on board when the business was formed 17 years ago are still there today.
To truck-heads observing the world of MBD Contracting from afar, they’re the guys who cart the enormous ‘goolies’ to the riverbanks, and that is largely correct in an incredibly simplified way – albeit, it’s only a part of a far wider portfolio.
A huge chunk of the firm’s work is indeed waging war against nature’s desire to wreck whatever we build for all the reasons outlined at the start. Fortifying riverbanks, road and rail embankments, bridge piers, transmission lines, and even the land itself against the next big – or even moderate – event. It’s all part of an MBD day in a constant race against the clock because you never really know if the latest bunch of dark clouds gathering far out to sea is the real deal or just another ho-hum half-metre of rain.
As well as their own account activities with the likes of KiwiRail and local councils, MBD subcontracts to companies like Fulton Hogan, holder of the West Coast NZTA NOC (Network Outcomes Contract). At the end of the day, regardless of who is working for who, it really is a massive, highly coordinated and cooperative team effort with the sole purpose of keeping vital infrastructure operating, and the daily comings and goings of people and commerce seamless. In fact, as you will read next, sometimes you don’t even know they’re there.


Southpac’ing a punch
MBD Contracting has sampled a number of truck brands in its 17-year journey to date. UD, Hino and Scania have all made an appearance, but it’s Southpac’s product offering that has found sustained favour in recent years. There are a couple of T610 Kenworths used on transporter duties, with their two three-rows-of-eight transporters. When not relocating gear, the 610s are deployed under tipulators for carting the serious stones. Six DAFs – four CF85s and two CF 530s in 6×4 and four-axle trailer trim form the backbone of the rock work, and by the time you read this cover story, two T410SAR Kenworths in the same truck and trailer configuration as the DAFs will have joined the operation, with the two oldest Dutchmen bowing out.
“The fleet is the right size for us at the moment,” says Darren. “When our workload increases beyond our capacity, we engage other local transport firms or contractors in the area of the work. Sharing the work around in this way has always worked well for us.
“It’s unusual work to spec a truck for. You have the need to be capable off-road and yet our operational area is over 800km north to south on the West Coast and inland across the Arthur’s Pass to Canterbury, so it’s no use having an entirely off-road spec. It means we mix up our plant on the jobs for best results. If it’s too rough, the highway trucks can feed the articulated dumpers. It’s just working out what’s required and playing to the equipment’s strengths.
“We’re coming to the conclusion that the perfect truck and trailer is probably a bonneted truck with a simple mechanical spec, not too technical. We deal with Chris Gray at Southpac in Christchurch, and he’s been great. There’s no service agent here, and we’re certainly a hell of a long way from rescue when down at Haast, for instance. It’d be half a day for someone to get there, so simple is good.
“Bonneted? Yeah, that’s for front-axle weight distribution, traction, and central driver location. The Scanias were a good truck, although traction off road suffered because they were too heavy in the front – which sunk in the soft conditions while the rear end would spin rather than biting and driving the truck forward. They’re really nice trucks but just not right for our application. The DAFs have been markedly better certainly, but it’ll be interesting to see how the T410s work. We think they might just be the sweet spot. We’ll see.”
Lifespan for a truck at MBD will likely be around the five to seven years and 500,000km mark. “Yes, we believe in buying new, getting the best out of the gear and then moving it on. Minimal downtime in our remote areas works best for us. The first generation of T610s have been and gone – being modern and low kilometres gives the next owner a great truck.
“As I said, service agents are few and far between over here, and we currently only have two guys in our workshop based here at Greymouth. Therefore we try and operate a modern fleet to minimise the amount of breakdowns and repairs required. We’ve always looked at it from the pont of view of having two options, pay for new or pay for repairs and maintenance. The type of work we do is mainly emergency flood damage work in remote areas for varied clients. Having gear always ready to go and not breaking down is a must for us.
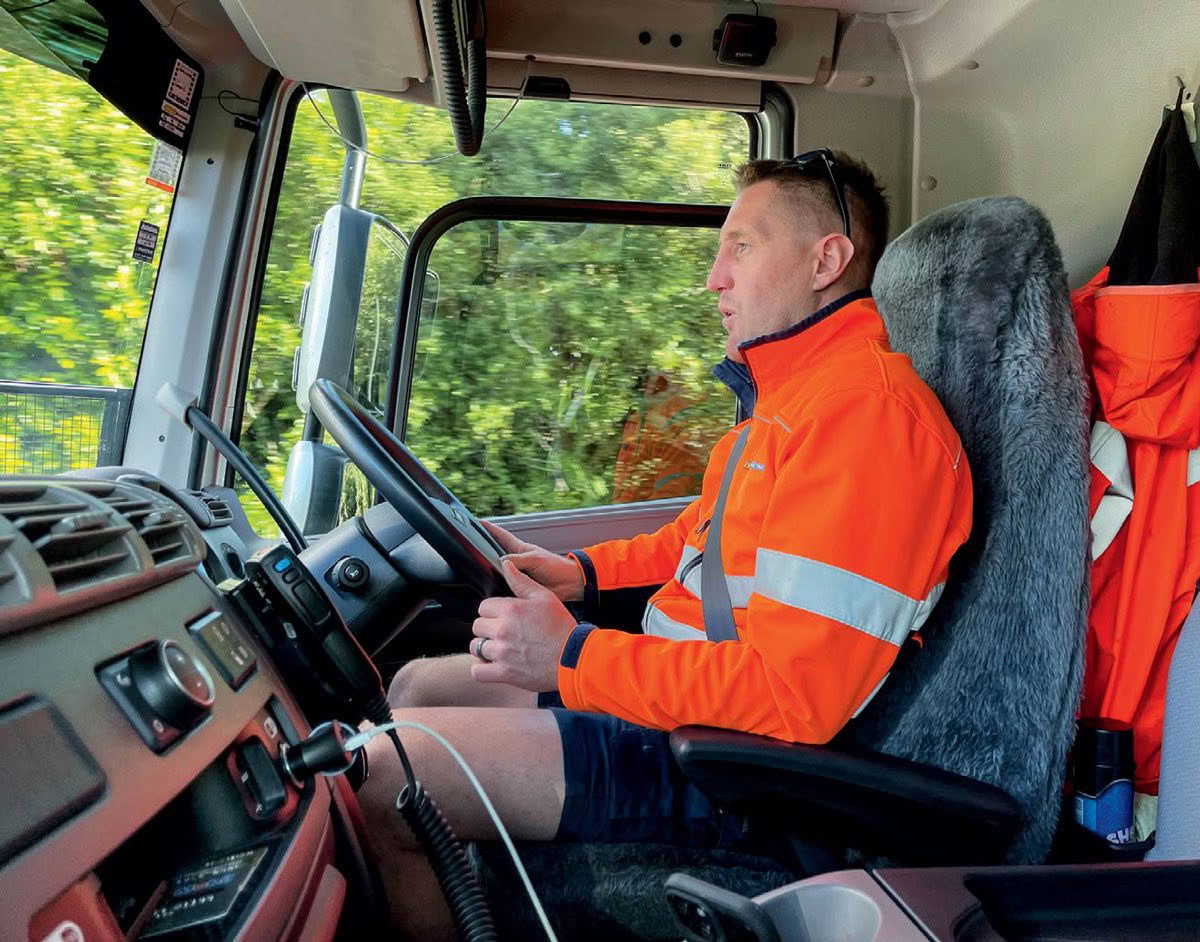
Cab party
We were here to spend two days in one of the company’s 12-month-old DAF CF 530 6x4s with Guy Norris Engineering- built Hardox body and four-axle trailer. Driver of the unit was Sean ‘Cozzy’ Costelloe. Five years at MBD to date, Cozzy is a West Coast native, and career trucker whose dad Dermot has been with local firm Aratuna Freighters for nigh on four decades. He’s typical of both the region and the multi-generational trucking breed – a grounded professional and all-round great bugger.
Rendezvous point was MBD’s Arney Street head office in Greymouth, where Cozzy was tending to some pre-start chores. Before long, we were heading to Kumara Junction, 16km to the south.
Today’s mission was joining a swathe of the MBD team at a rail embankment fortification on the Taramakau River directly beneath the historic Jackson’s Tavern. It’s a job they’d been on for a number of weeks and had about a fortnight to run. Access was via a drop-off at the Stanley Gooseman Bridge, just off the intersection of Lake Brunner Road and SH73. From there, we travelled down a 2km road formed in the riverbed by MBD. At the end of the road was 17-year MBD veteran Rodney Thompson in his 30 tonne Hitachi digger. Interestingly, once completed, the riverbed will have to be returned to a completely natural look – all signs the road was ever there gone.
Before getting to Rodney, however, we needed a load, and that came from the Wainihinihi Quarry 14km east of Kumara Junction at Turiwhate. MBD owns a number of its own quarries as well as operating others on a royalty basis over the length of its West Coast operations, allowing access to material at any point and keeping lead distances manageable. The team does everything at these sites, including blasting and rock extraction. Ben picks up the thread for us.
“Yeah, we blast big pieces. An overshoot for us is pretty much anything under about a metre. It’s just waste for us generally. We have very limited use for it. So, blasting is a specific skillset.”
The boulders we were after fell into the one- to three-tonne range. Depending on the job, or stage of the job, the individuals in transit might get north of eight tonne. Crikey! Your big toe’s not going to look too good with that on it. (Actually, it won’t be overly flash with a one-tonner on it.)
It’s a short sharp nip off SH73, past the site office and on up to the loadout area where digger driver Bailey Hibbs was awaiting our arrival. The CF pulled its Guy Norris trolley with minimal spin on the well-matured but dew- slicked access road.
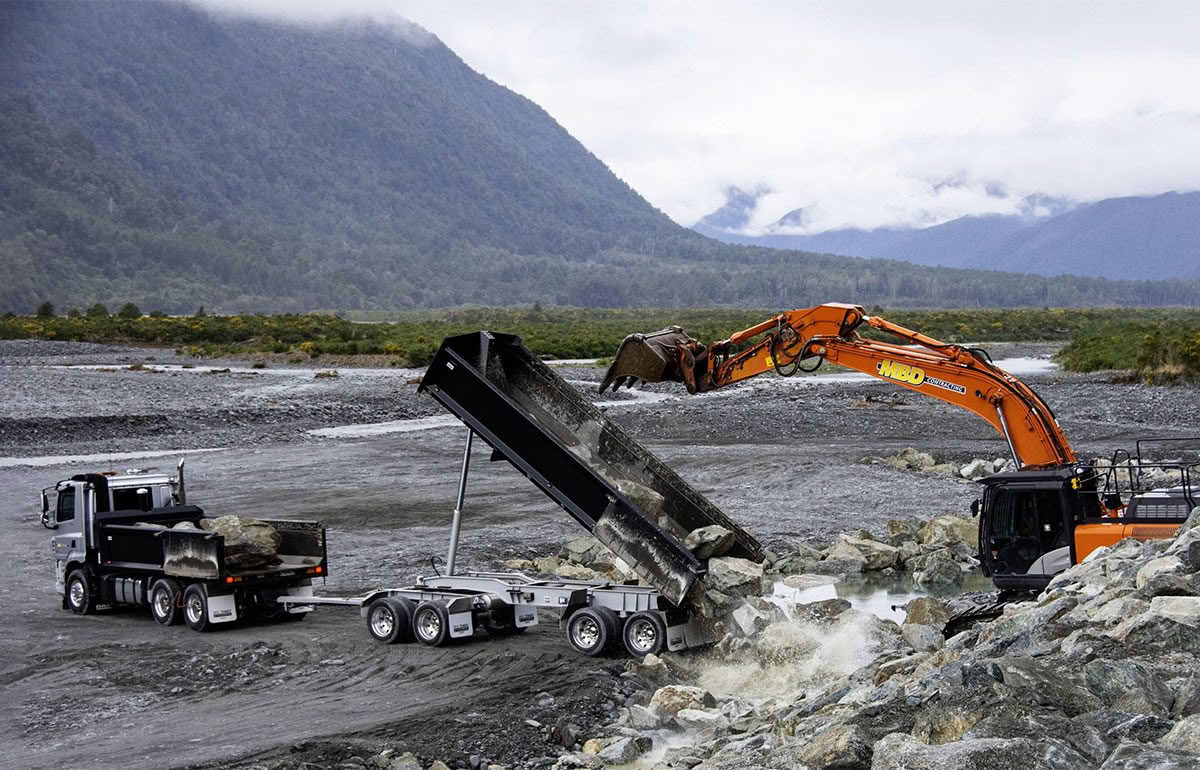
Cozzy backed up, hooking the trailer into an inside-out jackknife circa Ken Forsythe in the RMD Kenworth (New Zealand Trucking magazine Christmas 1984 issue). The DAF’s abundance of glass and great mirrors allow him to see everything effortlessly, but as you will find out, there was another reason why he was so slick at executing the famous party-trick manoeuvre.
Sitting in an MBD truck while it’s being loaded with multi-tonne boulders – I tell you, it’s a cab party! Let me make it patently clear, this is no slight in any way on Bailey’s superb prowess with his machine. This is just what happens when a rock weighing a tonne or more is placed on the deck and settles into its preferred riding position, sometimes needing a little encouragement to sit somewhere else. Cozzy just chatted to Bailey on the radio while I felt the need for a refund on every ride I’d ever paid for at Rainbow’s End. There’s probably no cab suspension test in the DAF factory that’ll vet the product quite like this does 10 times a day.
“We’ve done a bit on the DAFs just to smarten them up looks-wise,” says Cozzy. “I saw a Murlicht [Transport] one in the North Island and loved the way they’d blacked out the grille, so we did that. It transforms the look don’t you reckon?”
“YES! Wooo-hooo!”
Seriously though, that alone speaks volumes on the MBD approach to everything. You’d think rock carters to be rock carters, but presentation is everything here and a few extra lights, a bit of shine, a smart, tinted sun visor, it all enhances the look no end without costing the earth. It extends to the machines – in all reality, Rodney’s Hitachi is not often seen by the public, but it was crystal clean and company- branded.
“When mums are taking kids to and from school in the town [Greymouth] and our trucks are all around, they should look smart, well put together, and safe,” says Ben Haddock. “It’s all part of your social licence to operate in the community. We want to be a brand the community is proud of. Likewise, it helps with roadside checks and inspections – another reason why new gear is less hassle.”
The truck loaded, we pull forward and back the trailer in until we hear Bailey say “Yep” over the radio.
Unrelated commercially but seen as the dynamic duo for so many operators nowadays, I give you SI Lodec scales and Bigfoot Central Tyre Inflation. The MBD fleet is armed with both, and the moment 45 tonne was reached we were on our way. Such is the accuracy of the modern-day machine scale, there’s no weighbridge in the system – where would you put it in the 800km geographical work ribbon for a start?
Aside from access to the quarry and ambling up the site road, the job we’re on doesn’t tap into the utopia that is Bigfoot CTI, but rest assured, it’s called on often to keep the show rolling.
Cozzy descends the road back to SH73, the MX engine/exhaust brake combo providing due assistance in keeping any overly exuberant gravitational effect at bay.
MBD is reassessing the potential for some permitted trucks in the work envelope, but the West Coast is a tricky customer for anyone wanting to go north of standard VDAM. Based on what we’ve said, you might be forgiven for thinking there is no bridge on the coast beyond five years old. However, that’s far from the case. There are still plenty of oldies that have indeed held their ground, and while commendations must go to the planners and engineers of days past, they do dog HPMV aspirations for many in 2024.
What it means at the moment, though, is the CF 530 at 390kW (530hp) and 2600Nm (1920lb/ft) has little trouble bolting away from the quarry gates and on up the valley 14km or so to the tip-off sight at Jacksons. The 16-speed TraXon 16TX2640 OD AMT picks its way through the gears and it’s all very smooth.
Yes, we’re driving along a river valley toward the main divide so we’re going up hill, but there is no real work and the MX13 does that thing it does incredibly well, dipping to 1000rpm in 13th or 14th to crest the odd lazy rise. “It’ll go up the viaduct [Otira] in 6th,” said Cozzy. “You’ve got to set them up right at the bottom corner though. Thinking you’re going to make a bunch of shifts … yeah, na.”
Behind the TraXon is the proprietary SR1360T rear-end axle set and eight-bag ECAS suspension. Up front are parabolic springs, and the brakes are disc obviously.
The ride is fine, although understandably not like a big curtain cruiser set up for linehaul. It’s a day cab and the DAFs are shod with fat front feet to optimise loading, and of course, added to that is an incredibly dense, large, point- loaded payload sitting right behind you. It all adds up, creating its own dynamic you might say.
The CF is a lovely cab environment, spacious and open, with well put together durable materials that insulate the occupants nicely. Our trim and decor were Dark Sand and Black Rock – not that there was much darkness to any of it, ironic considering what Cozzy had to say on the way back.
As you’d imagine he’s a fanatic so the easily scrubbable surfaces, like the one cladding the engine tunnel, are a help in maintaining sanity. It should wear well, although he won’t see it do so as he’s lined up for one of the T410SARs when they arrive. Being a day cab, you’ll need to leave the kitchen sink at home, but there are door pockets, front and overhead stows, nooks around the dash console and the godsend caddy tray on the tunnel.
It’s an incredibly simple cockpit with a car-like feel and look, and ‘clean’ in terms of control clutter. DAFs seem to have it all without looking busy. Convention follows the norm with gauges and data in the binnacle; direction control, switches, entertainment, climate and brake valves in the compact wrap. There’s a Smart Wheel containing all the expected smart things, with shifter and engine brake on the right steering column wand, and all the other necessities on the left. Headlight master switch is dash-mounted on the right of the binnacle – a common convention.
Jack the Knife
Okay, attention all you wanna-be jackknife tippers. If you’re looking for a place to hone your inside-out jackknife tipping skills – take it from me, all roads lead to Arney Street, Greymouth, and MBD Contracting. To the MBD crew, a full jackknife tip is your primary tool of trade – like using a drop- saw for a chippie. It occurs at either end of the job as a rule, no wonder we were impressed how easy Cozzy effected the fab manoeuvre back at the quarry.
We roll down the access road off Lake Brunner Road, under the rail bridge and head towards Rodney, the distinctive orange stick of the Hitachi just visible in the far distance. The quality of the access road is instantly apparent, in many ways a work of art with a well-compacted surface and gravel bunds along both edges.
“Yeah, we work on the principle if we’re going to access the road trucks to the job head, then make as good a road that’s easy on them as pricing will allow,” says Cozzy. It certainly works in terms of travel time to the tip point, and must pay dividends on gear preservation.
We rolled along the Taramakau River bed and I chuckled to think tourists pay half a life’s saving to see the MBD office window. The autumnal vista toward the Alps was simply magnificent.
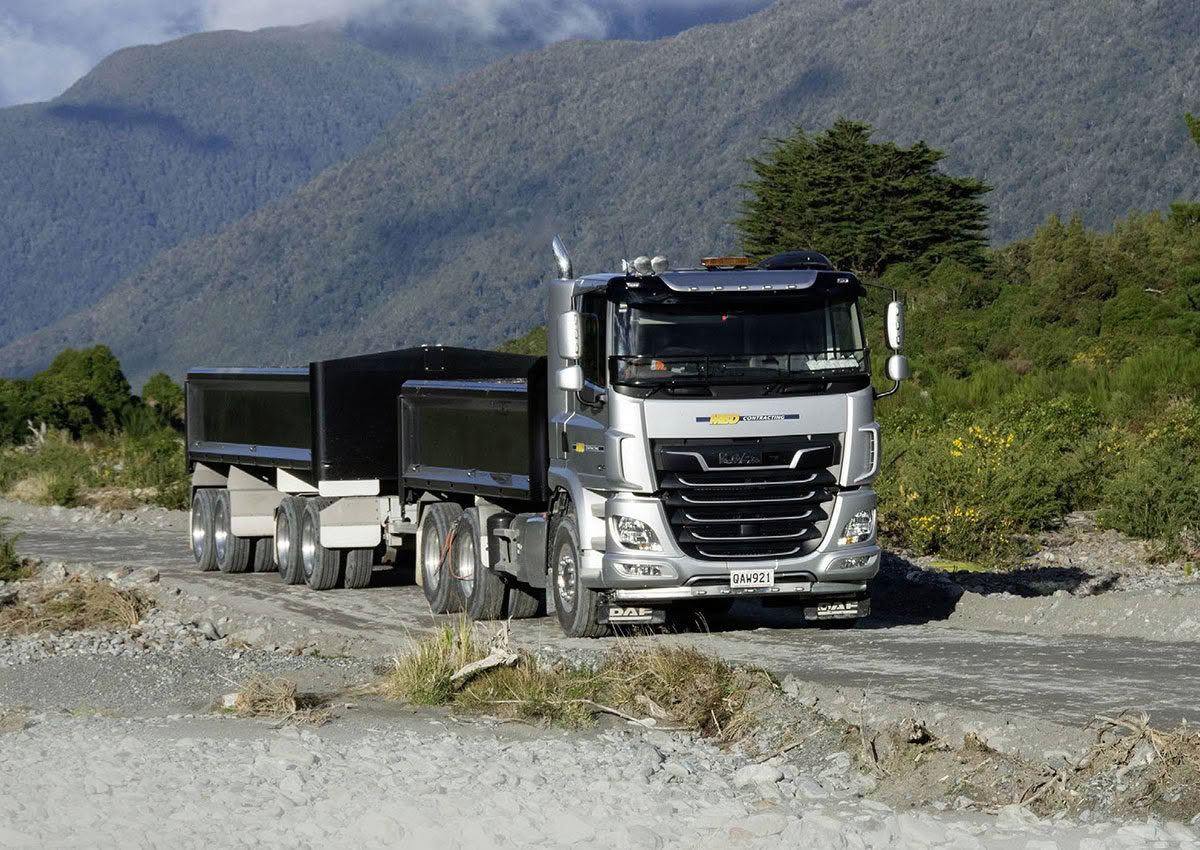
Arriving at the tip-off we waited for one of the CF85s to discharge. We were parked out on a large flat turnaround area that was itself a completed part of the project. With as many as six or seven loaded coal trains a day passing just out of sight atop the bank, the need for integrity in the lower reinforcement works is high. The MBD team had actually built a whole new subterranean rock apron and the visible rocks against the bank being worked now were merely the icing on a far bigger cake. Oh, harking back to an earlier point also, to the passing motorist or train driver, the entire operation is unseen. You wouldn’t know we were there unless you got nosy.
Watching Rodney place and key the rocks into position was nothing short of breathtaking, to be frank. If I’d had a pie, a beer and a deck chair, I’d happily sit all day watching. A 30-tonne machine and rocks that weigh tonnes each, and all you could hear was a slightly heightened idle from the Hitachi, and a ‘clunk clunk clunk’ as he placed them by eye. The finished surface you could walk across almost like cobbles – it was truly a remarkable feat of machine operation made all the more impressive by the absence of a thumb on the digger stick.
‘No, we don’t muck around too much with thumbs,” says Ben Haddock later. “You don’t need them for 95% of the work, they slow it down too much. If we’re placing rocks up under a bridge, we’ll put the thumb on, it’s obvious, but as soon as we’re clear, it comes off. If your operator is on point, you don’t need them, and Rodney’s been here a long time. He’s pretty sharp all right.”
Cozzy pulled into position and leapt out to prepare the unit. There’s just the right amount of bling on the Guy Norris Engineering gear – classy while retaining the essential practicality the job demands. There’s no ‘I damaged it a bit’, with these payload occupants. The gear’s either mint … or destroyed.
It’s a smart-looking combination and the black and grey work well with the environment – a bright yellow and red livery would clash with the serenity. LOL. It’s the little unseen things that always count too, like tapered deck stringers on the truck body keeping the lines nice and even.


He releases the locks and swings the tail doors on both units around, clipping them to their keepers on the left-hand side. There’s a heap of practical useable safety and productivity features built into the units, like side-access ladders and trip controls down the back under the decks.
“Guy has a high quality of workmanship and understands what we need. We have been continually developing and improving the product together over the years, and we haven’t had any major problems with it doing our hard rock work,” says Darren Richardson.
The bins are constructed in Hardox steel with 8mm-thick floor wear plates. (Interestingly, the same resilience is built into the digger buckets.) Hydraulic gear is Edbro and the trailers run SAF disc-brake axles and air suspension.
“Everything on MBD‘s truck and trailer bodies is beefed up and has to be strong to withstand the punishment,” said Guy Norris when we caught up with him. “If it’s not Hardox, it’s high tensile.
“We have built a number of units for MBD over the last 10 years and learnt a lot about their requirements. It’s always a path of continual improvement, they are a brilliant company to deal with.”
“Hear the buzzer?” asks Cozzy.
“Yep, why’s that?”
“A buzzer for the park brake, a buzzer for the PTO, a buzzer for the trips, a buzzer for the tailer door being open, a buzzer for the reverse … it was annoying having so many for the different warnings. We developed a buzzer system that changes its tone for the different alerts required. It’s a brilliant system and you know what’s happening by the tone you’re hearing.”
Cozzy backs up until Rodney gives him a toot. Trailer hoist up, and Barney Rubble and friends are gone. Forward, reverse into another inside out jackknife, and before you know it, the truck is empty. Their departure doesn’t quite induce the same party the arrival does.
I think to myself how the whole thing could be a wolf in sheep’s clothing to the uninitiated – if it weren’t for the culture. The skills you’re witnessing are disguised in a veil of apparent simplicity, conviviality and ease. This crew has all worked together for so long, they know each other so well, and the capability level is absurd. Anyone new, who couldn’t find their jackknife point first time, who can’t climb to a quarry load-out every single time without once shuddering to a halt, would start to cause a queue, almost immediately. You’d wonder why you were having trouble when no one else was. It wouldn’t be a case of not being 95% on your game, in most other places you be bang on, but to work here, the requirement is 99.5%. The good news is twofold. First, practice makes perfect and my goodness you’ll get practice; and second, once you have nothing to prove you accommodate those who genuinely aspire, helping them get to where you want them. That’s culture, and that’s Darren and Ben from those we chatted to.
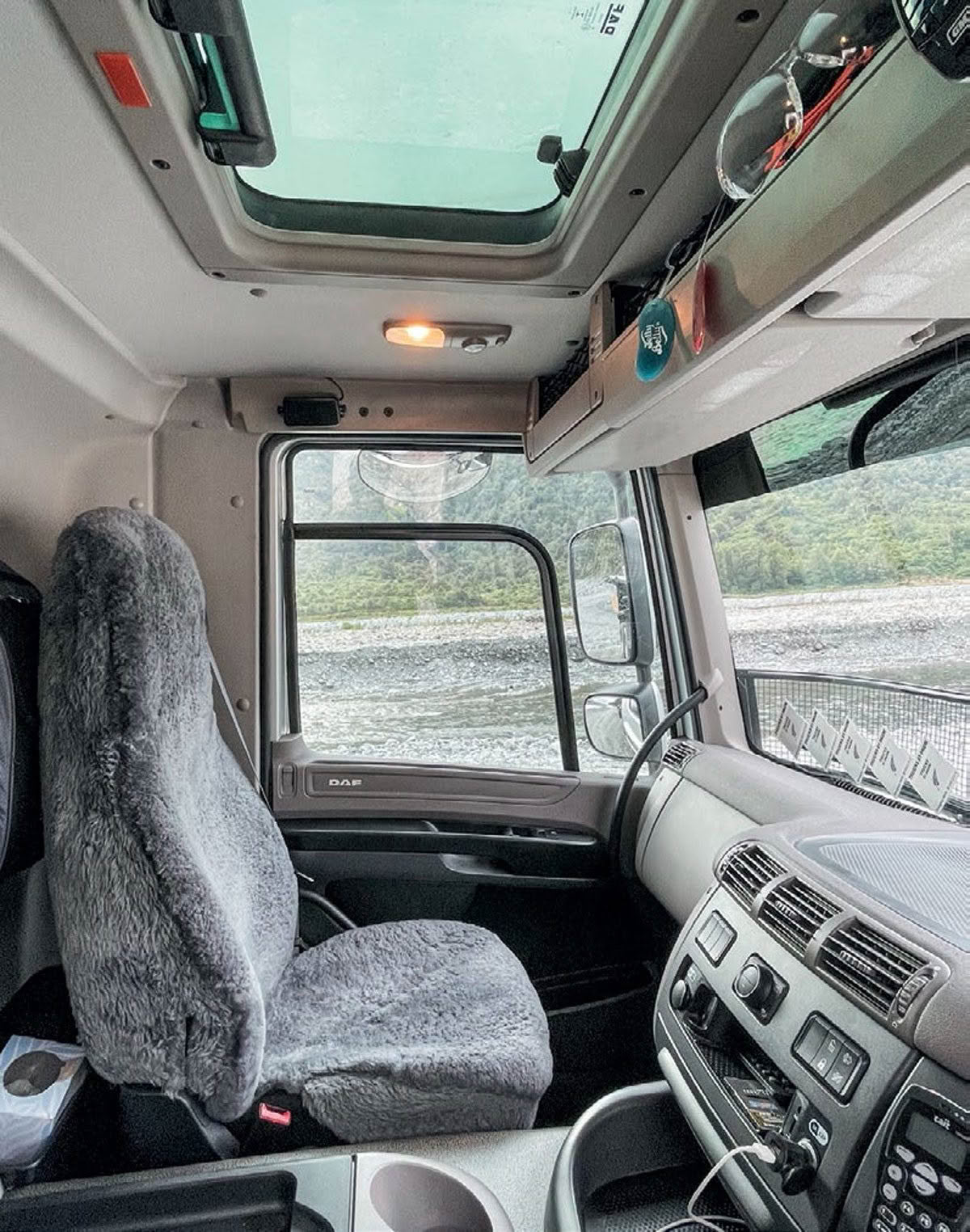
Tailgates swung shut, and we’re on our way back to Wainihinihi. The CF DAF is so easy to get in and out of, an aspect that certainly lends them to this type of work. However, the tech encompassed within the CF may have just outreached the application. Cozzy explains.
“The 85s were a good simple truck, manual transmissions, and not too much tech. These are beautiful machines, don’t get me wrong, but there might be just a bit much going on for our work. When we’re on the road, the emergency braking, adaptive cruise, lane departure, is all great – but off-road, when coming into the site, it can’t cope. Likewise, the AMT isn’t quite flexible enough, sometimes we need to grab four or five gears in a single hit to maintain momentum and with the AMT, two at a time is it. They’ll bog down if you’re not careful. The off-road control turns the traction control off, giving more power, but that makes it worse. With the AMT, you’re better leaving the traction control on so metering the power better. I’ve talked to stock carting guys with them and they don’t have any issues, it fits their work fine, it’s just the nature of this specialist role and some of the places we go. Simple is best for us.”
Out on the road back to the quarry and Cozzy points out a quirk of geography and astronomy that’s a real issue on the coast. “We put bigger sun visors on the trucks as a rule, not to look cool but to counteract the low sun – especially this time of year and what’s ahead. We’re nearly always heading west at some point, and the low afternoon sun beams straight into the cab at mid-windscreen height. You simply can’t see at times. The DAF has a bit too much glass and light and the sunroof needs blacking out. There’s just so much reflection coming back to you – look how clearly you can see our own reflections in the windscreen with hi-vis gear. You need a dark cab, and in that sense, I’m looking forward to the T410. A big visor, darker tones, and less glass, no sunroof, it should be better.”
Hard decisions made simple
Before you could say ‘Bob’s your uncle’, we were back under Bailey’s bucket for another round of rubble.
I’m yet to have a bad DAF experience. They’re an easy, uncomplicated machine and a testament to good design. Their popularity both in Continental Europe and half a world away here in New Zealand, as well as repeated success at IToY (International Truck of the Year), point to the product’s quality and adaptability. They are a truly global product.
Every model lineage has a sweet model in the eyes of specific customers, and maybe the CF85 was it in MBD’s rocky old world. There’s no doubt the CF 530 can do the job, and will serve MBD well, we had a great couple of days. However, does the relentless call from the global customer base for more technically capable machines mean in some niche applications a vehicle might out-evolve itself – like sending Sheldon Cooper to do a job Richie Cunningham could happily complete?
In the T410SARs on their way, MBD is able to still spec a truck that fits its precise requirement, an engineering chromosome core to that brand’s DNA. It will be interesting to see which of PACCAR’s products ends up rocking MBD’s world. At some point the evolution in technology will mean techy trucks will be able to move the oldest payload known to man without any compromise. The rocks will certainly be waiting; time is not ‘a thing’ for them.
SPECIFICATIONS
DAF CF 530 FAT 6×4 Rigid day cab
Tare: | 11,800kg (Load certificate) |
GVM: | 25,600kg |
GCM: | 70,000kg |
Wheelbase: | 4550mm |
Engine: | PACCAR MX-13 |
Capacity: | 12.9L |
Power: | 390kW (530hp) at 1675rpm |
Torque: | 2600Nm (1920lb/ft) at 1000rpm – 1400rpm |
Emissions: | Euro-6d |
Transmission: | TraXon 16TX2640 OD 16-speed |
Clutch: | Sachs (ZF) with ZF ConAct pneumatic actuator |
Chassis: | 260mm (side height) x 6mm |
Front axle: | 167N |
Front-axle rating: | 7.5 tonne |
Front suspension: | Parabolic, shock absorbers and stabiliser |
Rear axle: | SR1360T x 2 single reduction with inter-axle and cross locks |
Rear-axle rating: | 18 tonne |
Rear suspension: | Eight-bag ECAS with shock absorbers and stabiliser. ECAS remote control |
Brakes: | Disc. EBS |
Auxiliary braking: | MX simultaneous engine exhaust/brake |
Additional safety: | ACC, FCW, AEBS-3, LDW, VSC |
Additional productivity: | Eco performance, ASR, DPA (Driver Performance Assistant) |
Fuel: | 430L |
DEF tank: | 75L |
Wheels: | Alcoa polished alloy wheels |
Tyres: | Front: 385/65 R22.5 / Rear: 11R 22.5 |
Electrical: | 24V |
Cab exterior: | Day cab 2300mm-wide with side cab skirts. Galvanised steel bumper. Translucent sun visor. Heated remote mirrors. Bi-reflector halogen headlights with impact-resistant Lexan lens and integrated LED day running lights. Headlight beam for left-hand traffic. Bumper-mounted fog lights. Central door lock with exterior light-check function. |
Cab interior: | Cab trim Dark Sand, interior decoration Black Rock. Textile wall lining with sound absorption. Glass roof hatch. Air- suspended high-back driver’s seat and fixed passenger. Storage box on engine tunnel. Automatic temperature control and air conditioning. Pollen filter with activated carbon. Electric windows. |
Special thanks
What a wonderful experience delving into a company that’s always intrigued me, and a huge thanks to Darren and Ben for the welcome and fantastic yarn. So many takeaways. Of course, Sean Costelloe, a huge thank you for being our man on the front line, a wonderful company ambassador, and another from trucking’s incubator of real people.
Guy Norris, the short-notice catch-up was hugely appreciated – thank you.
Richard Smart and Chris Gray from Southpac – the constant support of our business is never taken for granted, and your enthusiasm for your product is inspiring. Thank you.
Quick reads from Test
Read more
HVYD0G off the leash
0 Comments23 Minutes
Remember where you come from
0 Comments35 Minutes
The right man for the job
0 Comments29 Minutes
Legendary ambition
0 Comments36 Minutes