Out of sight and out of mind doesn’t mean out of risk
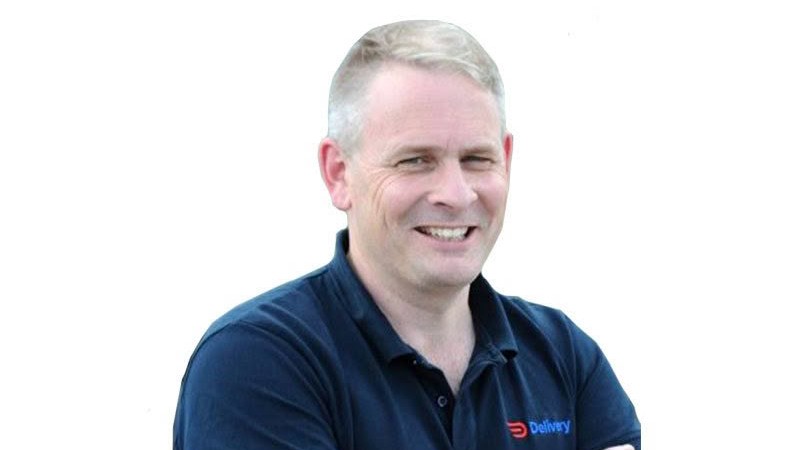
Taking the time to assess how well the risks and hazards faced by your team and subcontractors at work sites are understood is essential, writes Blake Noble.
I was overwhelmed by the response to last month’s column about subcontractors and owner-drivers, and I appreciate the time taken by those who reached out. The column seemed to strike a chord with various operators, big and small. Some of the feedback provided was definitely confronting.
It got me thinking more deeply about the entire chain we’re part of when delegating or contracting work and the full scope of our responsibilities and obligations as officers or directors – whether it’s to our team members or external subcontractors/other operators.
As much as a lot of this may sound like absolute common sense, it’s worth reviewing how well we (actually) understand the risks and hazards at work sites: that well-worn forklift needed to load/unload at a site that’s always been a bit “dodgy”, but it does the trick, or the loading zone that’s gradually becoming more of a storage area now, adding more complexity to what might’ve already been a difficult location. Perhaps it’s the length of time a task or run takes; how is it that your own team cannot do it within a shift, yet a subcontractor miraculously can?
I recently attended an event on the likely precedent-setting trial of Tony Gibson (former CEO of Port of Auckland) concerning a workplace death at the port. The insights from this case point to a strong regulatory focus; entities must clearly demonstrate and articulate that operational risks have been thoroughly addressed and stress-tested rather than just documented, delegated or assumed. There was no verdict in the case at the time of writing, but the outcome will be closely watched as a sign of coming “attractions”.
In practice, this means ensuring that the same standards and processes we apply within the boundaries of our team, equipment and facilities are mirrored by our partners – and that we can clearly validate this. Whether it’s required inductions, proper training for operating equipment or working on a site, regular drug testing or the roadworthiness and maintenance of plant machinery, these expectations must be consistently upheld.
Extrapolating this out – and it’s an issue that seems to be getting a lot more airtime lately – is the wellbeing of our teams and collaborators. There is growing awareness around mental health and wellbeing, and statistics certainly suggest the challenges aren’t going away in a hurry! A range of tools now exist that I suspect (and hope) many employers across our sector have in place to assist their teams. One is employee assistance programmes (EAPs), which provide independent counselling and support for team members with a few demons to fight. (Google “EAPs New Zealand”, and a myriad of local providers will come up.)
Worksafe has made it increasingly clear that the physical wellbeing of team members is also very much on its radar. A quick search online of this topic likewise lists a raft of companies across the country specialising in COF-type check-ups for our teams. We do it for our fleet with decent frequency; why not for our teams, too?
More simply, we are responsible for paying attention to the elements we can control and direct that we know will help the health of our teams. These include the consistency of shift patterns, the ability for team members to get a decent rest period between each working week, planning annual leave for team members to take before they’re desperate for a break, or the design and planning of runs that we know are safe and achievable, whether by our own team or a third-party.
The reality is that out of sight and out of mind isn’t out of risk; we all need to ensure we’re taking every step (and documenting/ recording/eyeballing it!) to look after our most important assets.