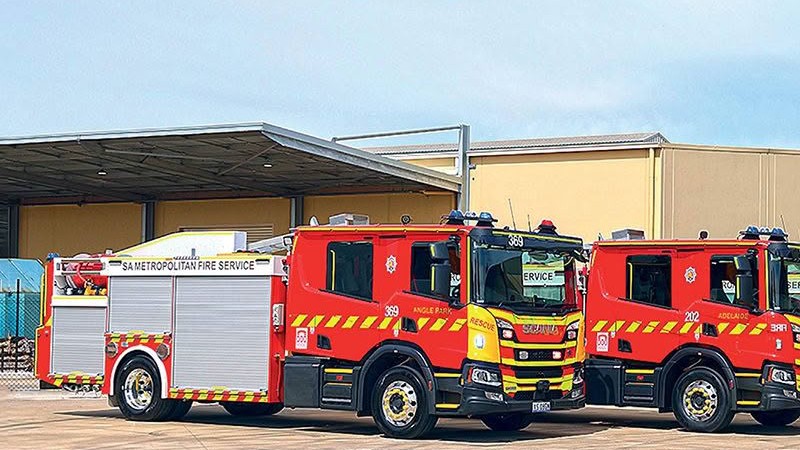
Fire appliances are a common sight on our roads, but few people are aware that most of them are built by Fraser Fire and Rescue in Lower Hutt.
John Fraser established J J Fraser Engineering as a production engineering company in the 1950s. Now known as Fraser Engineering Group (which comprises J J Fraser Engineering, Fraser Fire and Rescue, and Fraser Fire and Rescue Australia), it is one of the world’s leading providers of emergency firefighting vehicles. More than 1100 are currently in service in Australia, New Zealand and the Pacific.
Following John’s death in 2022, the company continues to be run by director and general manager Martin Simpson and company director Raewyn Fraser, John’s daughter.
Martin was an underwater weapons specialist in the Australian Navy, with plans to start up an adventure tourism operation in North Queensland, when fate brought him to New Zealand in 1987. “I came to New Zealand, and John Fraser taught me all about engineering. He taught me everything I know – but it was a small percentage of what he knew.”
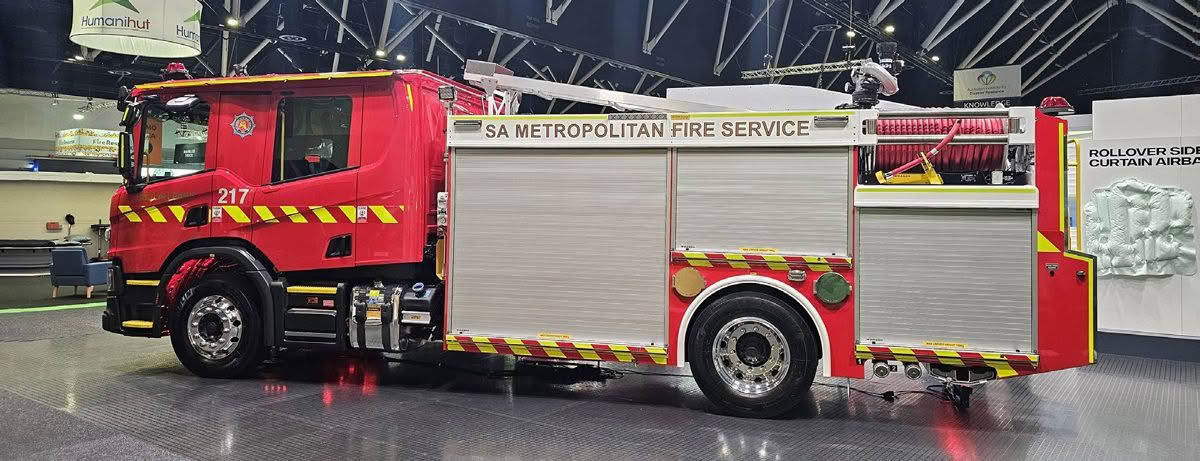
When Martin joined the company, it manufactured components for JF Hargreaves and New Zealand Railways, and undertook large jobs for Maud Kirk Couplings, Formway and Marine Air Systems.
“In 1987, we had the Stock Market Crash and then the government of the day, in all its wisdom, decided to outsource most of the manufacturing,” he says. “That was the start of where the government lost its way with the importance of manufacturing, and that continues to this day.”
In 2000, he heard that fire appliance manufacturer Lowe’s Industries was in financial trouble and had been put into receivership.
“At that time we were manufacturing hose couplings and other components that went onto those fire appliances for Lowe’s, and also supplying the fire service with various components.
“I was just passing their doors one day when they were in receivership. The receivers were trying to trade out when they got into trouble. When I turned up, they had just virtually laid off all the staff and the company was going to completely disappear. I met the receiver, and then did a deal to try and turn it around. I went back to the engineering workshop and said to Raewyn that we should buy them. And to my surprise, she said, ‘What a good idea’.”
Martin, Raewyn and John retained the remaining 10 staff to ensure their knowledge wasn’t lost.
“When I took them over, we had no work. I told the staff that if they were prepared to work in Frasers and do whatever we required, we would try and pull out work and see what we could come up with.”
He says it took a good six months before he secured that work.
“I think it was for police dog-handling vehicles. That was one of the first jobs we got. Then we tried to get work with the New Zealand Fire Service but to our surprise, they were not cooperative. The first order I managed to secure was for one type 3 heavy pumper for the Australian Capital Territories.”
Martin says they had to complete and deliver the vehicle before they were paid for it. The process was complicated further because the order was for a truck that was caught up in the receivership.
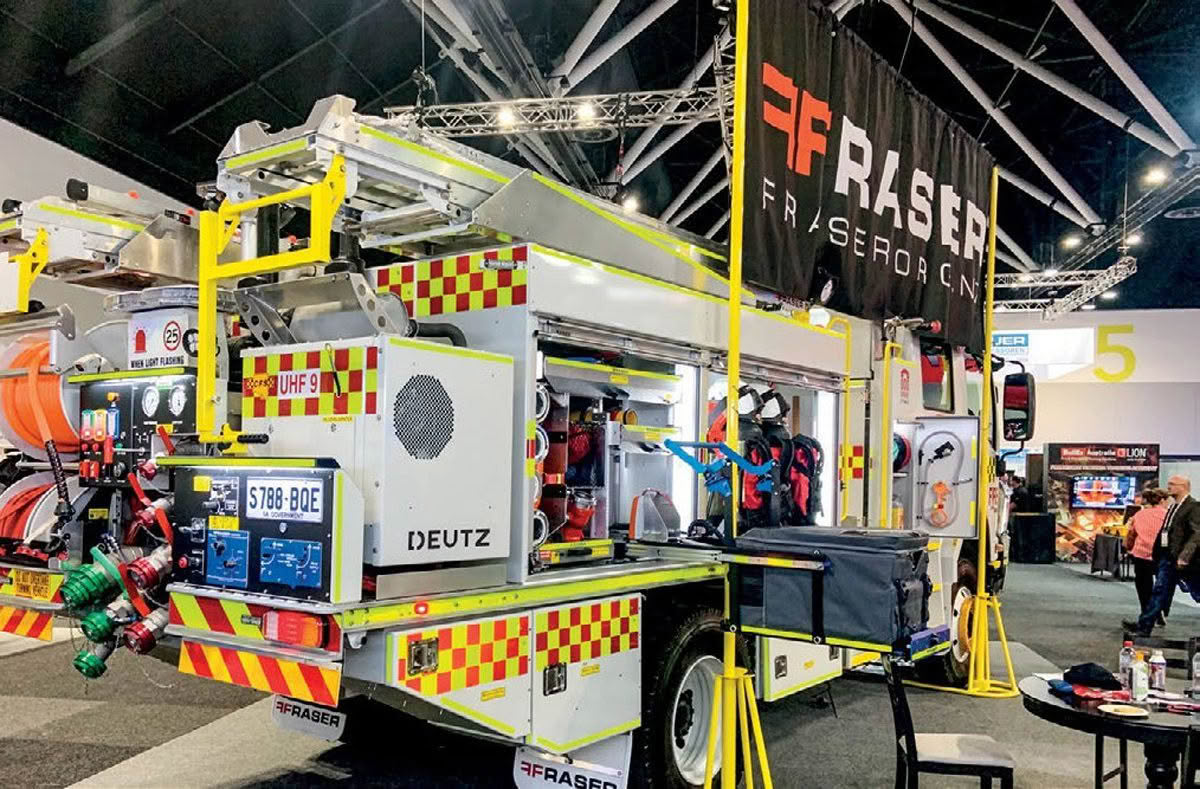
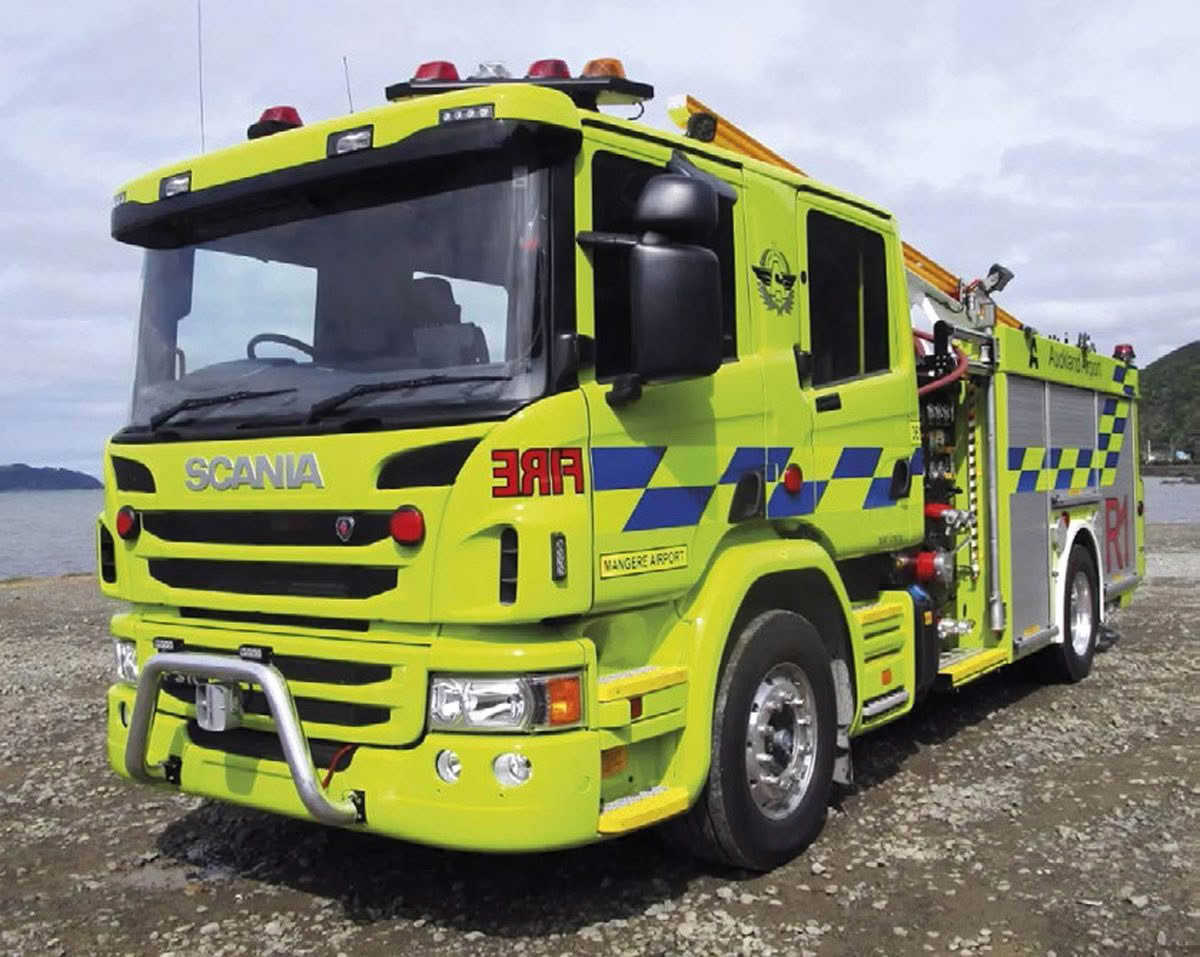
Once that order was completed, they convinced the South Australia Metropolitan Fire Service to allow them to get one of their chassis out of receivership too, and built a truck for them as well.
“Both authorities were so happy with the vehicles that South Australia then gave me the rest of the order for about another 10. And then eventually we won a contract with the New Zealand Fire Service.”
After taking over Lowe’s Industries, they concentrated on doing as much of the manufacturing and fabrication as possible in-house.
“Now we are probably the most advanced company in the world for what they call vertical integration, where we have our own foundry, electroplating, powder coating, CNC sheet metal, CNC machine shop, and then we have aluminium fabrication, stainless steel fabrication, steel fabrication, and then a full electrical department. We also have a huge design capability utilising SolidWorks design software. This significantly reduces our carbon footprint.”
Martin constantly strives to be innovative and to improve everything they manufacture.
“For instance, we’ve developed our own compressed air foam system. Basically there are hundreds of things we make – we supply all the waterway and firefighting equipment for New Zealand, all the hose couplings and nozzles and landing valves – virtually anything that you can imagine that can be made, we can make it. There’s no limit on what we can make, the limit is on time and resource.”
While road regulations vary from country to country, the extremely harsh conditions in Australia and New Zealand must be taken into consideration when developing appliances for these markets. Martin says the bushfire vehicles they have developed in collaboration with the South Australia Country Fire Service are believed to be the most advanced and safest products on the market.
“The vehicles 20 years ago were relatively basic, whereas today they are far more complex, containing far more electrical systems, communication systems and lighting systems. They’re also required to carry as much equipment as they possibly can, so we’ve developed stowage systems that are easy to access. And of course, on all trucks, crew protection is at the forefront.
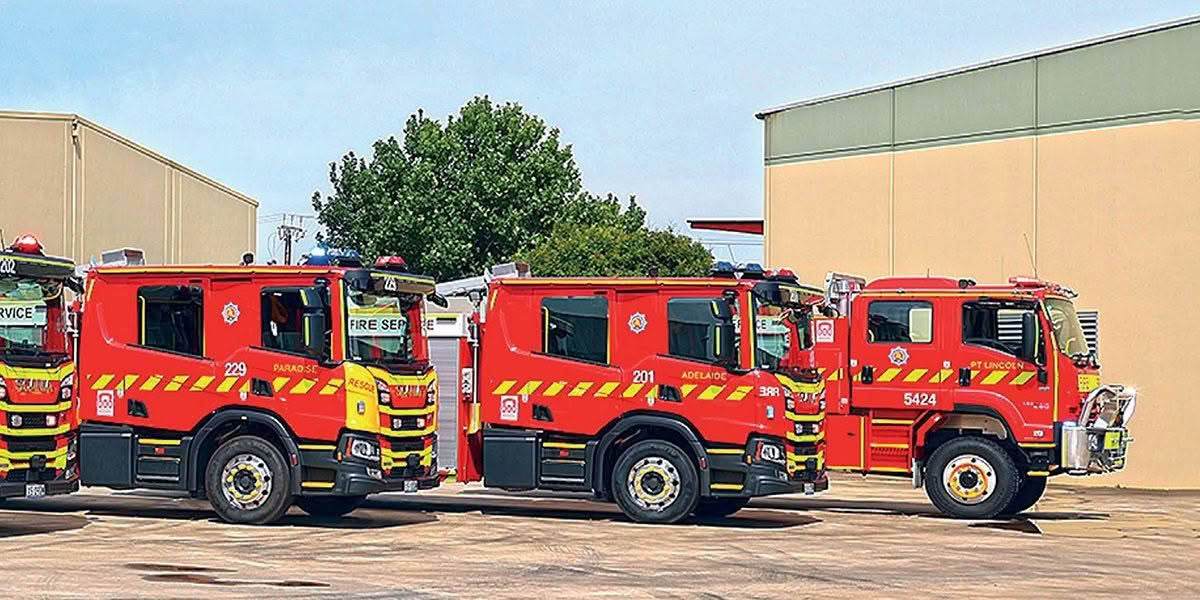
“They are fitted with a system called a deluge halo that provides full crew protection around the cab – all the tyres are protected, and all the electrical systems that can stop the truck from running are fire lagged and insulated. We’ve also developed a remote-controlled water cannon that can be operated from inside the cab. And they have thermal drop-down curtains inside the cab to stop the thermal shock, because the rapid temperature increase can cause the windows to blow out.”
He says it’s a two-way street and a lot of ongoing interaction goes on between the two countries.
“Certainly in Australia we have very technically capable teams that collaborate with our design teams and come up with new and evolving solutions to problems. We learn from all the different road conditions and we look at and monitor the life and the performance of these vehicles over time. If we find, say, components in one vehicle are not lasting as well as in another vehicle, we then re-engineer it to suit the harshest conditions. We’re constantly involved in improving the quality of the vehicles, which is to the benefit of the end user.”
Fraser Fire and Rescue is currently building three type 1 4×4 appliances for Fire and Emergency New Zealand (FENZ, which the fire service was renamed in 2017). The type 1 makes up approximately 40% of the fleet. It carries up to six crew, 1000kg of equipment, and 2000L of water. It was also installing pumps, building the lockers and installing the emergency lighting and equipment on three type 5 medium aerial appliances for FENZ.
“We all know the flow-down effects of economic and social benefits to local industry and the local supply chain. When these vehicles are damaged, we can manufacture components required and turn them around really quickly.”
In addition to New Zealand, Fraser Fire and Rescue builds vehicles for South Australia, the Northern Territory and ACT, as well as various agencies and mines throughout Australia. It has also supplied fire appliances to the New Zealand Defence Force, and airports in the Pacific Islands.
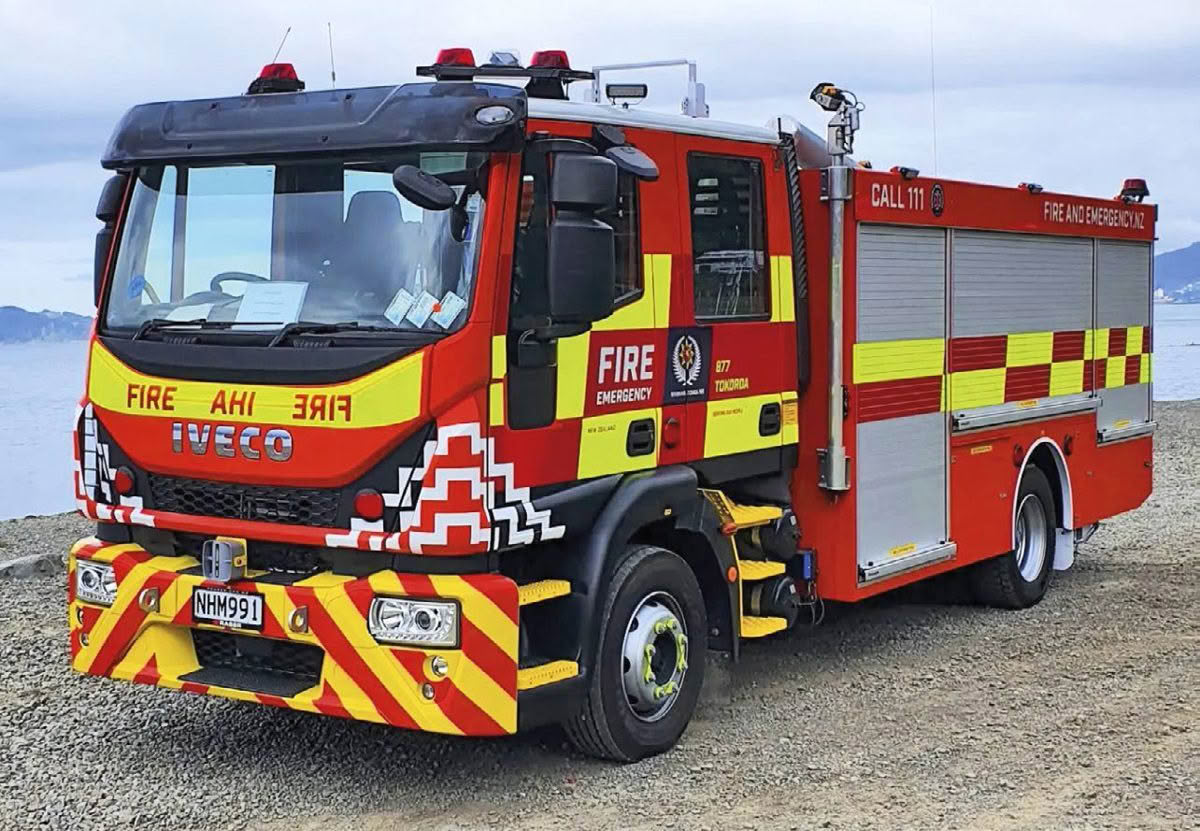
Fraser Engineering’s main site is in Wingate, Lower Hutt, and there is a large manufacturing operation in Adelaide that also does warranty support and servicing of the vehicles in Australia. Across the whole company there are about 140 staff, the majority in New Zealand. Some staff have been employed via a Ministry of Social Development programme.
“They give us people who are in the social welfare system with no engineering experience whatsoever. Currently we have about a 50% success rate with training them and finding out what they’re good at, giving them a purpose, and then giving them full employment. All of the people we’ve taken on add significant value into this company.”
Martin says with the current change in the economy, he is finding it a lot easier to find quality staff in New Zealand.
“I think the attraction of working for us is our stability. People now realise there’s more of an advantage to having your wages guaranteed for years into the future. With the contracts we have now, we’re flat out for at least the next three years.”
Martin says he has been waiting since 1987 for a government that embraces manufacturing and recognises its value to the economy and the flow-down effects to all of society.
“We are a major exporter, and have the potential to create not just millions, but billions of dollars worth of exports – yet we don’t have the government’s full support. How could that even be possible in an economy that is so dependent upon export dollars? It’s just because we’re not trending; we’re not the movie industry, we’re not the wine industry. It’s not seen as a growth industry, and it’s not seen as something that provides heaps of jobs and heaps of money.”
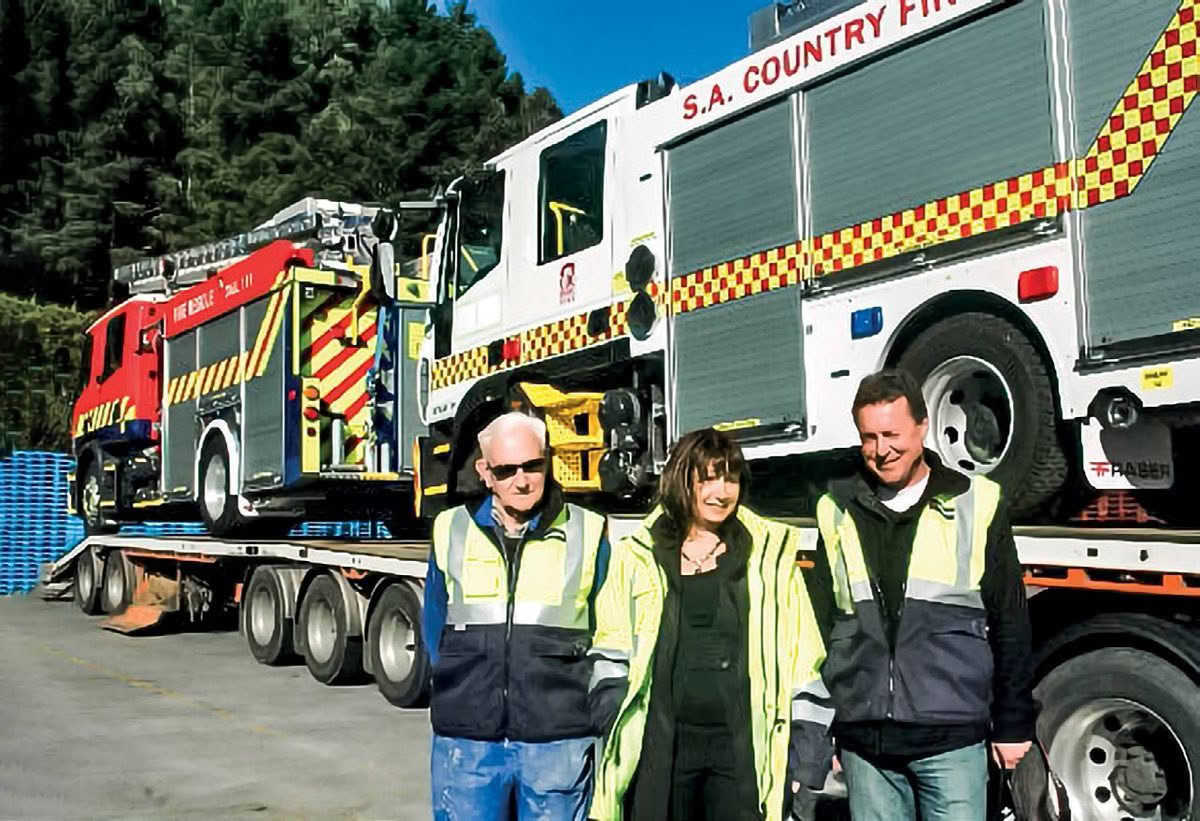
He says there is a symbiotic relationship between the transport industry and the manufacturing industry.
“The flow-down effect from manufacturing is so massive, but it is not understood because our people in government often don’t have the fundamental experience of manufacturing or product development. In Australia it’s very, very different, and it appears that their politicians are far more in tune with the manufacturing side of things now than they’ve ever been before. There’s been a huge change, and they’re far more advanced than us.
“We have $30 million worth of the latest manufacturing technology and we can make anything here, but it can be a lot easier if you’ve got the will of your government.”
Martin says they have the potential to double their current output by streamlining and increasing their technology base. At present they are building a significant number of appliances for South Australia, both the Country Fire Service and the Metropolitan Fire Service, and also supplying some vehicles for the Northern Territory.
“We believe that our quality is second to none, and we are currently exploring the opportunity to set up a manufacturing facility in Brisbane and expanding our manufacturing facility in Adelaide. I believe that we’re in a very good position because of our reputation and our quality is now being noticed throughout the other states. We certainly hope to be working with some of those states in the very near future.
“It’s all about partnerships and we believe that developing our partnerships in the Australian market will open up significant growth opportunities for us, and that is driven by being able to deliver vehicles on time to the specification required and meeting their budgetary requirements.”