MAHA: Collaboration key to successful installation at Scania’s Invercargill workshop.
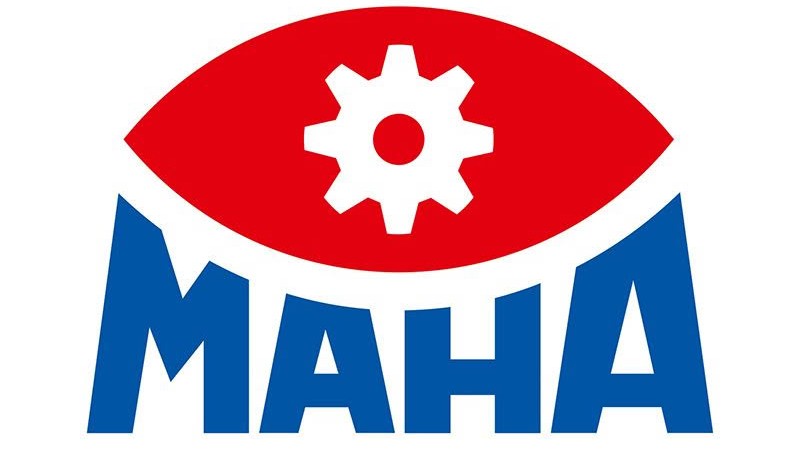
A successful collaboration between MAHA and Scania New Zealand led to the completion of a major equipment installation at Scania’s new Invercargill facility.
Scania New Zealand opened the new service centre mid-June, as it looked to support its growing southern customer base. Demand for servicing and repairing trucks in the region has increased dramatically as Scania fleet sizes have increased.
The new branch, located at 20 Wallacetown Lorneville Highway, Invercargill, has a 10-bay drive-through capacity with the ability to accommodate 15 technicians, replacing the previous four-bay drive-through workshop that housed 10 technicians.
The new workshop includes a certificate of fitness-compliant lane, full brake-roller testing and shaker-plate capabilities, along with a certified dangerous goods pit suitable for fuel tanker work and other DG vehicles, as well as full air-conditioning servicing and re-gassing.
The Invercargill site services the area between Queenstown to Dunedin and south to Bluff. It is Scania’s first purpose-built facility in New Zealand.
“We wanted to be able to check any vehicle and carry out any diagnostics on brake and suspension systems, and also we want to be COF-certified to give us the ability to do COF inspections at that facility,” says Kelly Henshaw, Scania dealer director – South.
“The goal is to be able to efficiently and accurately diagnose any braking faults, any suspension faults, and also to have the ability to do onsite COF.”
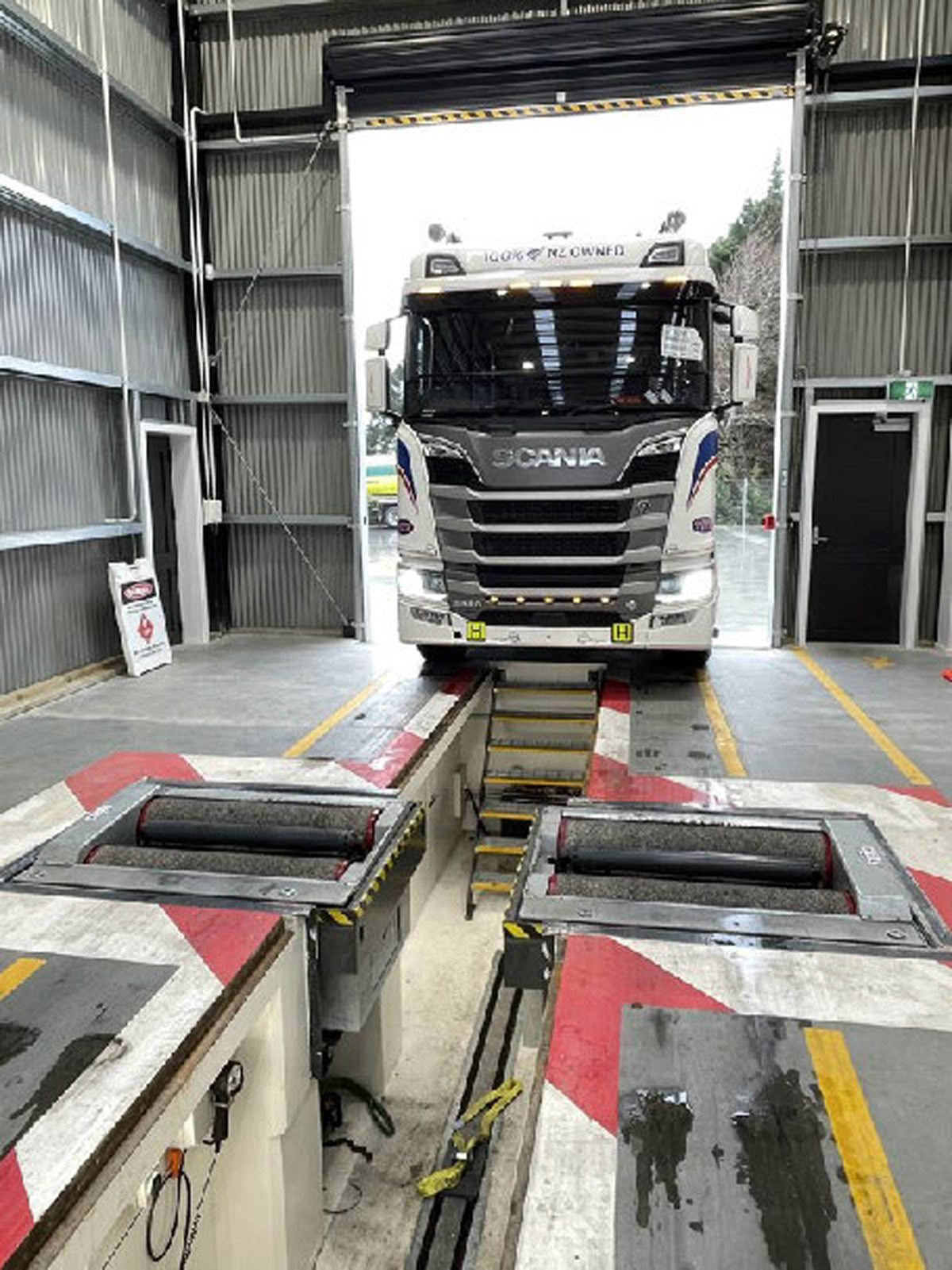
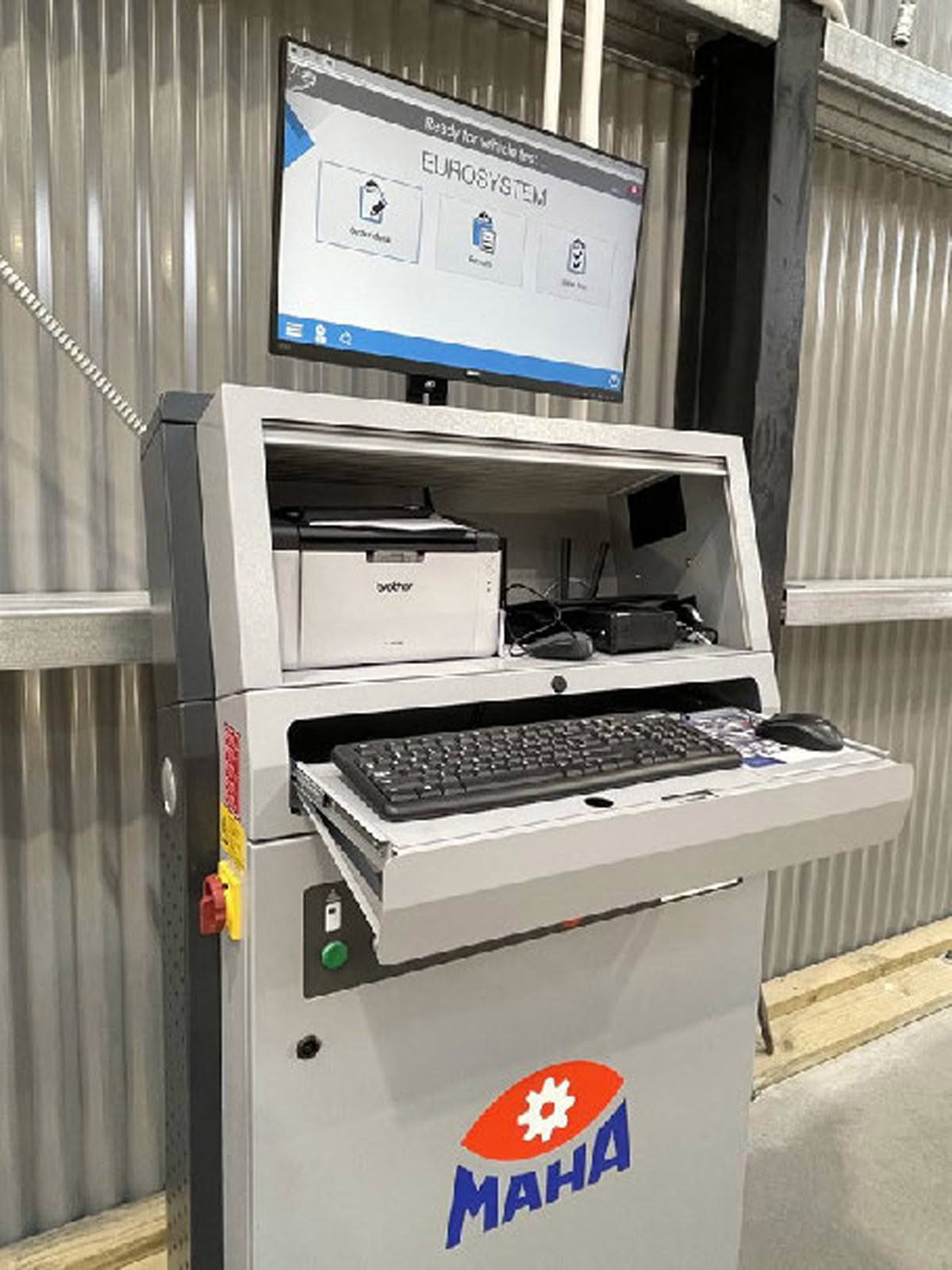
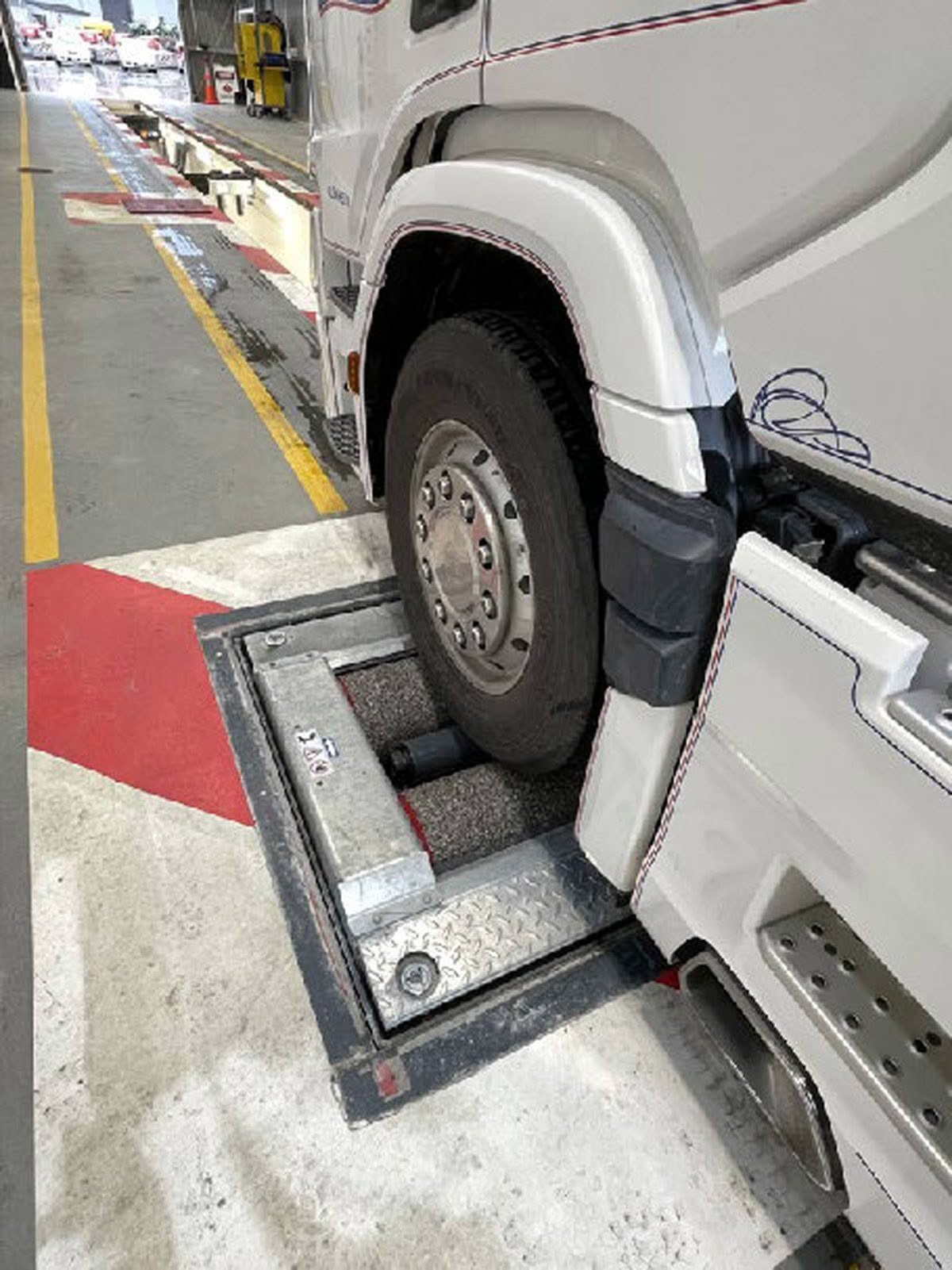
Henshaw says Scania had the option to run with any configuration and brand it wanted for the Invercargill facility.
“We’ve got a number of different companies we can deal with, but we like to deal with MAHA because of the quality of the equipment and the reputation that it has in the industry,” he says.
Henshaw says the relationship with MAHA goes back a long way.
“I’ve had a lot of dealings with the local MAHA team, and also the Australian team, and the communication is good, the feedback loop is good, the pricing is accurate. I think they’re a great bunch of people to deal with.”
He says MAHA was involved in the build of the equipment every step of the way.
“They checked everything was correct before the floor was laid. Then they came back when the equipment was up and running, and then carried out the training as well.
“They didn’t just sell the equipment and wish us all the best. They were there throughout the journey to advise on any issues the builders and the developers had. They were integral with that communication loop, and they were physically on site to make sure that the equipment was in the right location and correctly installed.”
Mick Lauster, managing director of MAHA, says the collaborative nature of the project was evident from the outset.
“It’s a really collaborative operation between us and Scania. We are heavily involved right from the planning stage,” he says.
“We consulted on the architectural plans, ensuring that the design accommodated the sophisticated equipment required for Scania’s operations. We continued to provide support as construction progressed, overseeing the implementation of their equipment into the building’s infrastructure.
“Once the physical construction was completed, our role transitioned to equipment installation and staff training, ensuring that Scania’s team was fully equipped to utilise the new technology effectively.”