Clean, green and electric future
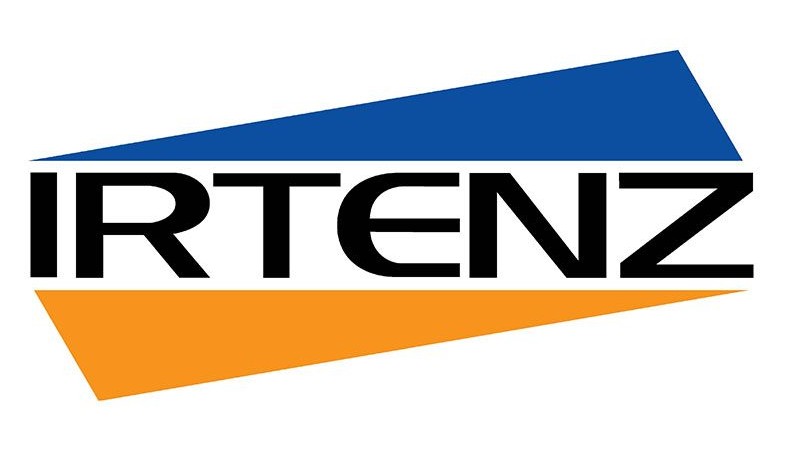
Last November, the 2023 IRTENZ 18th international conference, themed Future Highways – Future Vehicles – brought together speakers from New Zealand and the world to present the latest developments in transport matters. In this last report instalment, we look at what’s ahead for some key players in terms of decarbonisation.
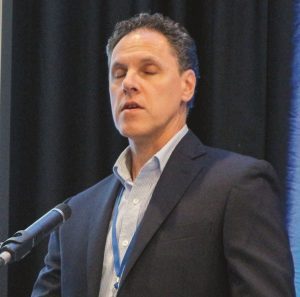
Nemanja Miletic, SAF Holland, Australia, says the future of heavy traffic will be green, quiet and electric. While there will not be one solution for everything, electrification will likely cover the last mile of urban deliveries.
Miletic says the use of electrified trailer axles is becoming increasingly important, especially for refrigerated trailers and inner-city applications. “CO 2 reduction, noise reduction and legislation to protect inner cities are the main drivers for electrified CVs,” he says.
SAF-Holland began developing its trailer electric axles in 2015. The ideal application for the TRAKr e-axle is refrigerated transport fleets in which trailer refrigeration units (TRU) can run fully electric. Purely electric operation reduces noise and will help fleets meet the new proposed zero-emissions standards.
The SAF TRAKr uses a high-voltage generator module for electric power regeneration, lowering the vehicle’s emissions and fuel consumption. SAF-Holland e-axles have been rigorously tested in real-world operation in Europe and South Africa.
SAF TRAKr for electrical recuperation
The main design principle is the centrally located high-voltage generator unit (max 20kW), which converts trailer kinetic energy to electrical energy to be used to operate electric consumers of the trailer. The generated power is stored in a lithium battery. The main applications are coolers, tanks and silos.
The SAF TRAKe for electrical recuperation and traction support
In principle, the SAF TRAKe is the same design as TRAKe but with a more powerful voltage e-machine with a higher output (max 120kW, max 320 Nm). Depending on the operation mode, the generated power can be used to operate devices or equipment within the trailer that use electricity or can be used for the drive mode to support the main engine of the truck. The generated energy is stored in a lithium battery. The main applications are the car carrier, cooler, tipper, tanker and silos.
Scania NZ’s senior product engineer e-mobility, Alfons Reitsma, touched on the latest developments in Scania’s decarbonisation journey.
“Our purpose is to drive the shift towards a more sustainable society and in our transport systems,” Reitsma says. “We work on trying to do the right thing. How can we improve the energy efficiency of our products for our customers? How do we deal with renewable fuels in the electrification journey? All while focusing on smart and safe transport.
“Every day, we get calls from our clients who ask us to give more sustainable products.”
Reitsma says good policy is essential for truck manufacturers when planning the future, regardless of who is in government. “I thought the government [transport announcement] was a little bit light on its ambition frankly,” he says.
“Of course, we’d like an ambitious government to have good policy to underpin set targets. It’s so much easier for us when we know there are set targets from a governmental policy, because we only make vehicles that comply with the legislation.
“It’s a huge challenge now globally. How many diesel engines should we make? How many gas engines should we make? How many electric trucks should we make? How many hydrogen trucks will we have to make, et cetera.
“That planning comes from good policy because good policy will indicate to us what we should create.
“But, regardless of governments and policies that are perhaps not driving the shift as quickly as we would like, we are committed to driving this change.”
Reitsma says Scania NZ Is dedicated to instigating the change towards decarbonisation by following science-based targets. “This includes targets that are in line with what is necessary to meet the goals of the Paris Accord,” he says.
“We are committed to a 50% CO₂ reduction from our operations by 2025, and a 20% CO₂ reduction from our products by 2025. By 2030, we have to have a 50% reduction of our CO₂ footprint from our products, and we have to have a 50% reduction every decade thereafter.
“The question is, how we do that? There’s a lot of investment going on behind the scenes, a tremendous amount. And that is also to ensure that we can hit that target under the Paris Accord.
“Everybody who contributes to this change is a positive step in the right direction. We are definitely not here to polarise the industry between one solution or the other,” Reitsma says.
“Many transitional steps to decarbonisation have unfortunately been taken out of the loop because of New Zealand market conditions. And that’s a shame, because all those products were developed – gas engines, ethanol engines, ethanol engines based on the ignition. They could have all contributed today to the society we live in here in New Zealand.”
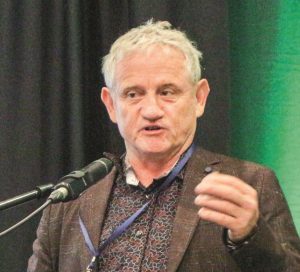
Reliance Transport general manager Mark Darrah updated delegates on the company’s Project Switch, a comprehensive, five-stage initiative to achieve carbon neutrality and unparalleled efficiency.
“We’re heading into a world where we’re going to have 450 to 500 parts per million of CO₂ in our atmosphere. While no one knows for sure, the last time we had this much CO₂ in the world, there were mass extinctions. So, we have to ask, is that where we’re heading?” Darrah says.
The core of Project Switch lies in five strategic stages:
- Convert the diesel fleet to Euro-6 and transition the light vehicle fleet to Battery Electric Vehicles (BEV), completed in 2022.
- Commit to net carbon zero, reduction, and offsets, resulting in Reliance’s certification in December 2022.
- Commission heavy-duty BEV trucks and BEV Reachstackers, completed in December 2022.
- Build a scalable MCD-capable Microgrid with Battery Energy Storage Systems (BESS) from 2023 to 2029.
- Complete the full-scale rollout of the HD BEV Fleet from 2024 to 2029.
“As a service industry, Reliance Transport recognises the necessity for a plan, driven not only by customer demand but also by legal mandates, such as COP 28 and the Climate Change Response Act. New Zealand is committed to internationally legally binding conventions to reduce its emissions,” Darrah says.
“New Zealand’s got a great opportunity because of all the renewable energy we produce. There’s enough renewable energy to replace the fossil fuel energy that we burn,” he says.
Reliance aims to transition its fleet to zero emissions, aligning with the evolving expectations of transport service buyers, who increasingly require emission reduction plans.
“We need government support to achieve this … from the Ministry of Transport/Waka Kotahi, EECA… We have had two lots of funding from EECA and we are applying for a third block. This enables us to try this technology and validate it for operation.” says Darrah.
“New Zealand is a technology follower. With commitments from Europe, the United States and China towards zero-emission heavy vehicles, we have to make moves.
“It’s going to be a hell of a ride between now and 2030. And we are really going to have to hustle if we want to change the regulatory environment and take advantage of some of the stuff that’s happening overseas and get it down here.”
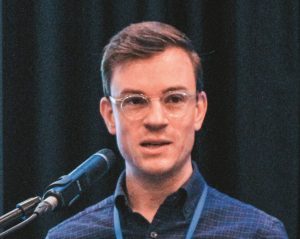
Christopher de Saxe, head of sustainability at London-based freight management start-up, Zeus, says an electric road system (ERS) is an economically attractive solution to decarbonise heavy goods vehicles.
“An electric road system is essentially a dynamic charging solution for any vehicle, but we’re mainly talking about heavy trucks,” he says.
According to de Saxe, an ERS reduces the battery capacity needed for many journeys compared with big battery trucks. This reduces vehicle cost, weight, and embodied emissions, as well as peak loading on the electricity grid. “A big drawcard for these kinds of systems is the impact that they have on reducing the battery capacity needed on vehicles,” he says.
“This has a number of implications regarding vehicle cost, weight, and efficiency, as well as the embodied emissions in those batteries, which can be significant.
“If you look across the ERS for light, medium and heavy vehicles, the impact that they have on reducing battery sizes is fairly consistent. For any of these, if you consider the price of BEVs, especially your kind of 40-, 44-tonne units, whichever way you slice it, the batteries are a huge part of the cost. A 40% or 60% reduction is going to have a big impact on the cost of that vehicle.”
A slight indirect impact is peak loading on the grid, de Saxe says.
“If you imagine an entire country’s HGB fleet transitioning to either big battery trucks with high-capacity static chargers versus smaller battery trucks with dynamic charging, the impact on the grid could be significantly more favourable,” he says.
ERS can involve in-road conductive systems, in-road inductive systems, or an overhead-cable type of conductive system.
“This is the solution we were most interested in early on,” de Saxe says. “The work that we’ve done could be applicable to any type of dynamic charging. Essentially it looks to be economically attractive based on a number of studies that have been done throughout Europe and the UK, particularly for the higher-end heavy vehicles, which in Europe is up to 44 tonnes,” he says.
“We’ve done a lot of work on electric road systems for the UK. Compared to the competing options of big battery trucks or hydrogen fuel cell vehicles, it does look to be like one of the lowest-cost economically feasible solutions.”
However, de Saxe says that doesn’t mean it’s politically attractive. “This requires centralised, big decisions from government and it’s very likely many governments wouldn’t go down this route. But that doesn’t mean it’s not potentially the best economic solution.”