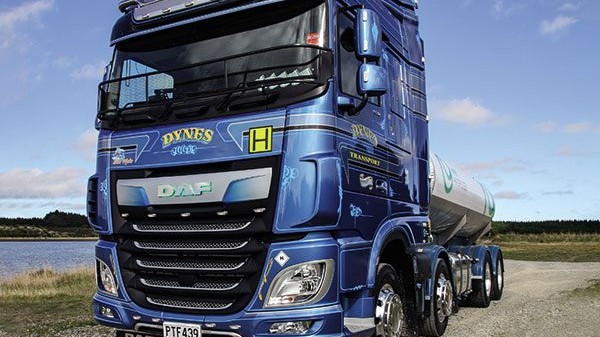
Over the past couple of years, HWR has outlined its hydrogen plan, its intention to introduce dual-fuel technology in its truck fleets and a hydrogen refuelling network for the group – and others – to utilise. Now, the first of 10 dual-fuel hydrogen trucks has arrived in HWR’s South Island fleet wearing the iconic blue livery of Dynes Transport.
As transport companies chase climate targets and grapple with the best ways to meet looming emissions regulations, the quest for reduced tailpipe emissions is centre stage in the global transport ecosystem. But as we well know, no silver bullet solution covers all transport tasks, vehicles and regions.
More so, the leading solutions are still being developed to reach commercial viability – with complete supporting infrastructure years behind still. And while the latest Euro-6e engines are the cleanest diesel burners in history, plenty more can be done in the interim to achieve further immediate emissions reductions.
Over the past two years, HWR has identified hydrogen as the fuel to power its fleet into the future and has set out to create an internal hydrogen ecosystem of supply and demand. A dedicated business unit – HWR Hydrogen – is driving its development, and the first step is employing hydrogen injection to displace diesel and thus reduce fuel consumption and emissions. Now, the first of 10 of these dual-fuel vehicles to enter trial operation this year – Blue Hydro – has hit the road and the company’s first hydrogen-gas production and refuelling facility will go online in the coming months, with a second following.
The company has put $15 million behind the project, partnered with leading local and international entities, and is willing to learn on the go.
“There were a lot of people without any skin in the industry talking on behalf of industry, not industry talking for itself. It was about putting the voice of industry into the conversation,” says Anthony Jones, HWR CEO.
Why hydrogen? “We’ve looked at EV, but the payload loss of batteries is too big. We couldn’t get past a 20-30% payload degradation. Battery just doesn’t work for the majority of the HWR fleet, most of which is heavy mass/ long distance or rural-based,” Anthony says.
“We’re not non-EV. We know EV has a place, but it’s not in our business. The recharging network is too spread out, and the infrastructure in rural towns can’t cope with rapid charging. For us, hydrogen ticks many boxes. Everything we’ve seen points to hydrogen and we’re going to test that. We’re learning as we shape the future.”
Immediate gains
Beyond its suitability to HWR’s requirements, by starting off with dual-fuel hydrogen injection, the company can prove hydrogen’s suitability to its operation while achieving real-world results – up to a 40% reduction in diesel consumption and emissions is expected.
“It’s a transitionary step,” Anthony continues. “New Zealand’s average heavy fleet age is 16 years, so it’ll take a long time to turn that fleet over. Huge numbers are needed to incentivise change [compared with light vehicles]. Alternatively, we can pragmatically look at transitionary fuels.
“If the driver runs out of hydrogen, he flips to diesel and carries on. There’s no operational penalty with this approach. But there’s a huge amount of change required with other tech.”
And when Anthony says there’s no penalty, he means it – you’ll notice the HPMV sticker proudly in place on Blue Hydro’s nose, 58-tonne permit in hand. Anthony comments that the maintenance of payload was important. The system only adds 940kg without hydrogen, 965kg fully fuelled, so the tare-weight penalty isn’t as significant as one would assume.
The ability to ‘just carry on’ points to another key consideration at this stage of the technology’s development and implementation: driver buy-in. “The overwhelming response within the group has been ‘that makes sense’. If we can avoid changing the type of truck drivers are driving, not change the driver experience, but make a 40% reduction in consumption and emissions, that’s amazing. [Dynes Transport managing director] Pete Dynes is a passionate driver himself and he absolutely sees this as a step forward for our industry, so he piled in behind it,” says Anthony.
As we inspect the truck, Kerryn Hamill, project manager HWR Hydrogen, adds: “The key is we’ve taken something the drivers are already used to and that we can support with service and operations.
“A lot of the team has been expecting something sci-fi and different, but it’s so relatable. That’s key for the drivers – to have something they’re comfortable with and familiar with and used to every day. And we can service it… Fuel cells and EVs need an entire industry to support them. Our diesel mechanics can understand the modifications we’ve made.”
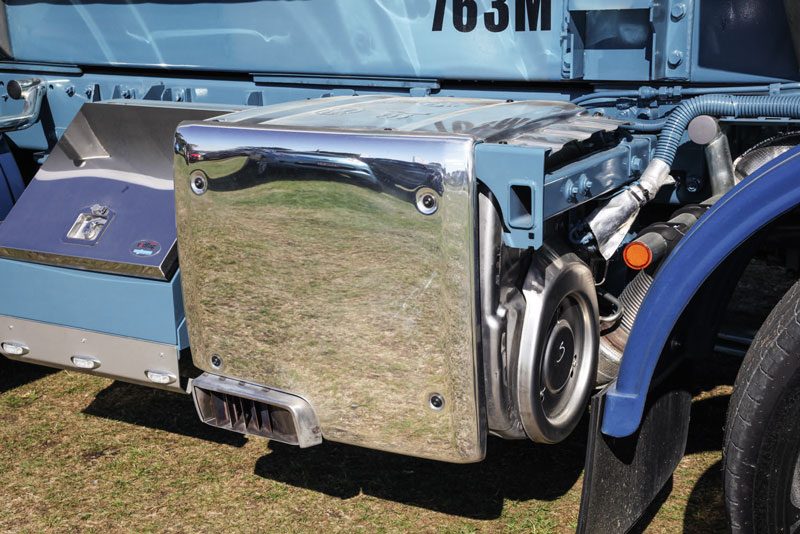
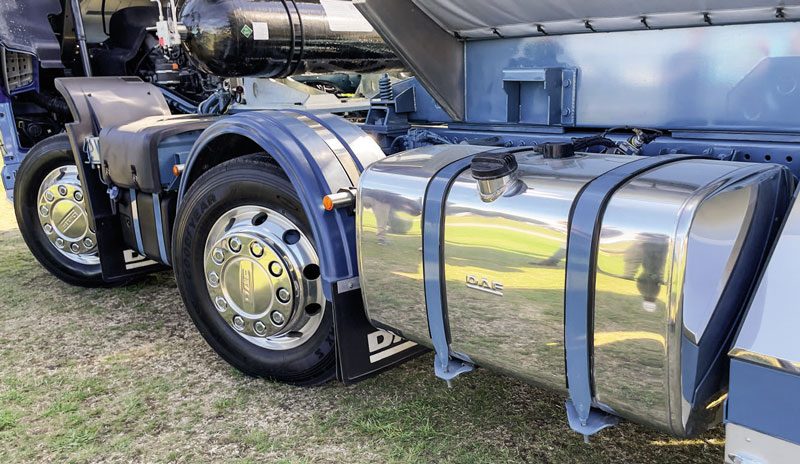
High standards
The modifications in the dual-fuel conversion are indeed not complicated or otherworldly. It’s simply a case of storing the hydrogen onboard and injecting it into the engine’s intake when required.
Five hydrogen storage tanks stacked behind the cab take care of the former. Each holds 5kg of hydrogen (so 25kg in total) at 350 bar. The tanks are rated to 420 bar, so they run well below capacity.
On that, the subject of safety… Kim Hill, commercial manager HWR Hydrogen, explains that the system features a range of safety precautions. The tanks are made (in the UK) from carbon fibre specifically for hydrogen storage and tested to EC79 – the European standard for hydrogen. They are a couple of inches thick, and subject to the likes of ballistic and fire testing.
They are mounted on a frame made of 10mm galvanised steel and FEA (Finite Element Analysis) force-modelled to withstand up to 6G.
“We wanted it to be over-engineered and account for different scenarios,” says Kim. “In the event of an incident, the tanks won’t fail first. When the system detects a loss of pressure, it shuts everything off and vents the gas in the affected tanks. Hydrogen is an incredibly small molecule, given the chance to escape, it goes up into the air.”
Back to the system… Injection of the hydrogen gas is by a ‘ring and rail’, which is exactly that: a ring of eight injection points above which is a rail of four injectors. About 30mm is machined out of the engine’s intake manifold for the ring and rail to slot into. This is the only mechanical modification to the drivetrain – nothing else is touched and the standard Euro-6 emissions gubbins remain in situ.
On safety once more… The ring and rail incorporates pressure sensors and a thermal fuse temperature sensor to cut injection when thresholds are exceeded, as well as a manual purge valve. A regulator drops the hydrogen pressure down to eight bar before it’s fed to the injectors.
Controlling it all is a supervisory ECU, which reads the engine’s revs and torque output off the truck’s CANbus. It utilises that information to inject the hydrogen optimally – the mix ratio depends on the truck’s operation. Again, plugging into the truck’s CANbus is the only electrical modification – the truck has no idea the hydrogen injection is displacing some of the diesel.
“What we want is a homogenous, even mix of air and hydrogen into the cylinders,” says Kim. “A mix up to 40% of hydrogen is about what we’re expecting to see. Ultimately, it’s the same energy mix as what’s going into the engine on 100% diesel.”
Kim says a consumption ratio of 1kg hydrogen per 3.5L of diesel is expected. In effect, 25kg of hydrogen equates to an additional 80L of diesel in the tank, or 20% extra range.
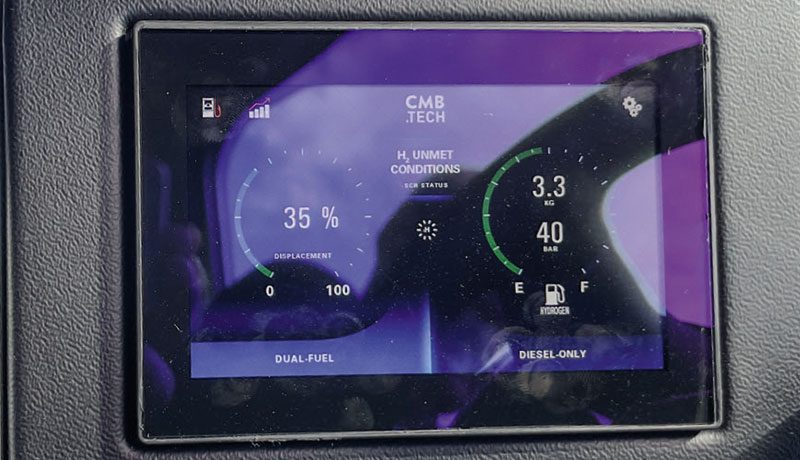
In operation
“This isn’t new tech,” says Kim. “We’ve purchased it from CMB.Tech in the UK, which has been developing dual-fuel systems for more than 17 years, and we can see they’re getting those results. But New Zealand trucks and roads are different, so it all needs to be confirmed in our trials. We’ve worked with our local partners Fabrum [gas and cryogenic specialists] and Transport Repairs [South Island heavy vehicle specialists] to adapt the tech to New Zealand and undertake the installations and training.
“We’ll continue to tune it accordingly,” she continues. “Typically, what you see in the UK and Europe is a full payload each way. We often don’t have that. That’ll change how we use the hydrogen. We need to understand those nuances and adjust the tuning for it.”
Kim adds that the secret really is in the tuning and ECU programming. Each of the 10 trucks entering the trial will run with different payloads in different operations within the various HWR companies. They’ll be new, like Blue Hydro, or less than a year old. They’ll also deliberately be different brands of trucks with different engines, which will all require different tuning.
“The beauty of it is we can install hydrogen injection on a five-year-old truck or a new truck. The challenge is having space for the tanks and payloads. Liquid hydrogen is the way forward for those trucks that can’t accommodate hydrogen gas – but there are thousands that can.”
Blue Hydro will be based in Dunedin and will alternate between running as a milk tanker and curtainsider. It’s also configurable as a logging truck; it was designed to be diverse and suit the needs of the job within Dynes Transport. For those wondering, the curtain body comes within 100mm of the tanks, and the log frame is “slightly shorter” and features a curved headache bar.
The way forward
Impressively, Blue Hydro has hit the road after only a nine-month turnaround – especially so, considering there were no set standards HWR Hydrogen could follow for hydrogen in New Zealand.
“There was a lot of work to do for the New Zealand configuration. It’s quite different to the rest of the world,” comments Kerryn. “NZTA has no legislation we could go through, so we’ve relied on the LT400 process [for heavy vehicle repair or modification work] to sign off this truck.”
Kim adds: “It hasn’t been super challenging, but there is a process involved. The challenge is that it’s new. Someone has to deliver it first and show that the systems meet different standards – but there’s no local standard for hydrogen, so we have to use European standards and show what our partners have done. There’s a lot of learning for everyone – every step of the way we’re educating people on what we need and what we can do.
“The government’s hydrogen roadmap won’t be available before the end of 2024, and that’s too late for us. To move forward, we need to do what we’re doing. Government has put a lot of focus on EVs and yes, they have their place, but we don’t believe they’re the answer for full-size trucks in the next 20 years.”
Ultimately, HWR would like to move to liquid hydrogen. “We can absolutely see that liquid hydrogen is the way forward. We need to prove it with this tech first,” says Kim.
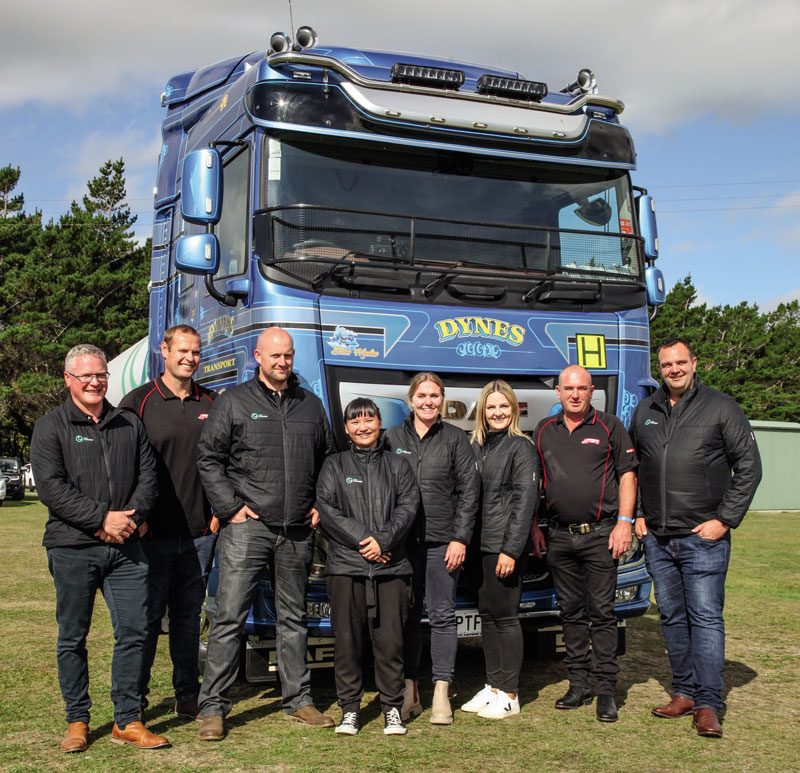
Kerryn adds hydrogen fuel cells are also in the picture, and the HWR Hydrogen team is following the work being done by Cummins on hydrogen combustion.
“We absolutely see the ability to adopt these technologies when it becomes economically viable for us,” she says. “A big focus is making this all commercially viable.”
Commercial viability also applies to the Gore hydrogen production and refuelling facility. Kerryn says that, once more, there is little to go on by way of legislation or certification.
“We’ve done a lot of work to educate WorkSafe NZ and the communities that hydrogen is a safe fuel, more so than LPG.”
For now, though, all eyes are on Blue Hydro as it leads the way in the group’s dual-fuel hydrogen injection trials. As Kerryn says, the dual-fuel approach isn’t common or obvious, but it deserves to be championed.