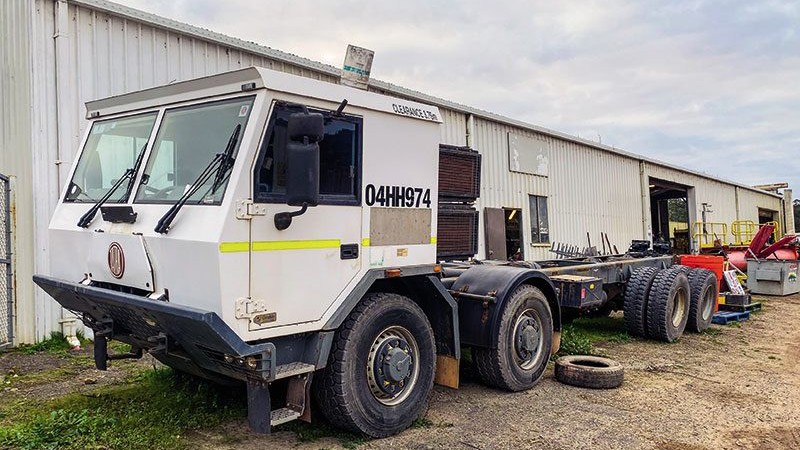
Tatra trucks disregard all conventions regarding design – and the applications they are expected to operate usually defy most conventional trucking tasks. New or used, they are sought-after pieces of equipment for specialised, unconventional applications.
According to the oil-stained papers on the passenger side floor, this Tatra T815 8×8 started life as a service truck on a mine site somewhere in Queensland’s Bowen Basin region. A little over a decade later, after toiling faultlessly at the mine site, its service body was removed, and the Tatra wound up in an auction yard. A logging contractor in Eden spotted it and thought it might suit an upcoming contract – if the price were right.
The upcoming log haulage contract exhibited some unique challenges, one of which required logs to be loaded from roadside stacks onto log trucks. This might not sound like a challenging conundrum, but the narrow bush tracks in the steep mountainous forests around Eden and Bombala often have deep gutters. Furthermore, unlike clear felling or large-scale thinning operations where logs stacks are extremely large, it’s economically feasible to transport an excavator to the site for a few weeks. However, in this new logging contract, the smaller log stacks mean a nimble road-going log loader would be more economical than the traditional excavator with a log grab.
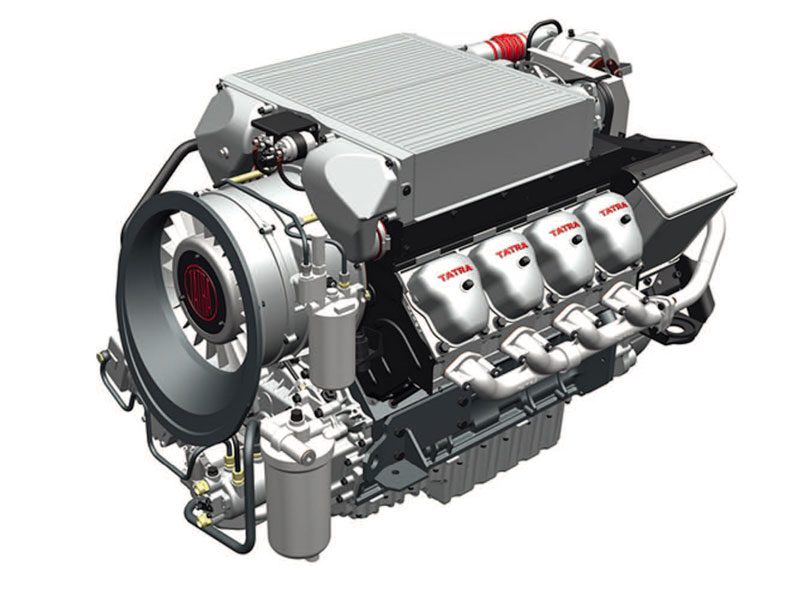
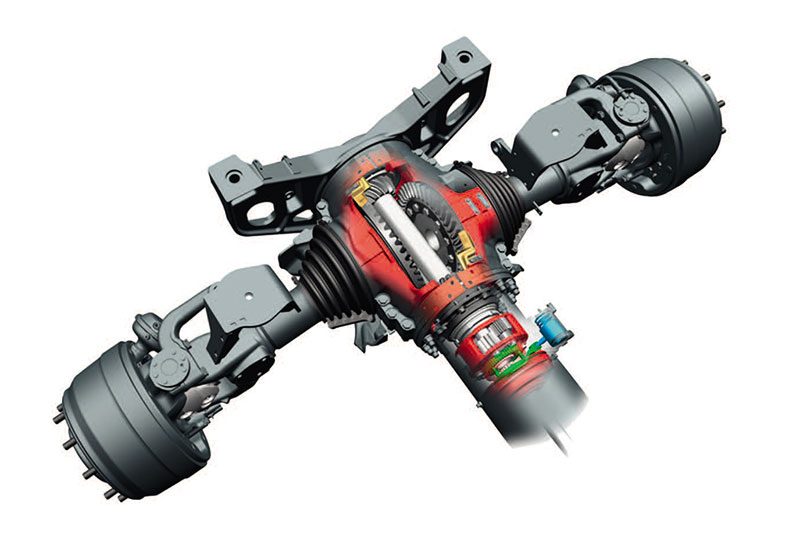
The solution is to mount a Prentice log loader onto the used Tatra T815 8×8 chassis.
But what makes the Tatra 8×8 the best truck platform for the Prentice log loader? For starters, these are the preferred trucks by many modern NATO armies today because of their go-anywhere, low-maintenance attributes.
Tatra commenced automobile manufacture in 1850 when it began building vehicles in Czechoslovakia. Originally specialising in cars and carriages, Tatra branched out into truck manufacturing in 1898 and hasn’t looked back since. The Danish army recently ordered dozens of self-propelled Caesar howitzers built on the Tatra Force 8×8 chassis. At the beginning of last year, Tatra trucks, together with the DAF Trucks and Czech Tatra Defence Vehicle companies, announced it had received a contract for almost 900 logistics trucks on a Tatra chassis for the Belgian army.
Then, in the middle of last year, Tatra trucks with Rosenbauer, an Austrian manufacturer of special fire vehicles, won a contract for more than 70 Tatra Force military fire trucks for the Bundeswehr. These commercial successes indicate that the capabilities and parameters of Tatra trucks are increasingly appreciated in the armies west of the Czech border. Most recently, Tatra trucks will also serve the US army with military training, which has bases in Germany.
All about the T815
The T815 cabin might not be the prettiest looking, but it is very functional and comes standard with an inbuilt ROPS and FOPS canopy, ideal for mining operations and certainly a bonus for forestry vehicles. There is a noticeable lack of plush creature comforts inside the cabin that are often taken for granted in many modern trucks today. But, considering the environment this truck is destined to work in, the plain steel dash is undoubtedly a more sensible approach.
The dashboards warning lights are large and bright, as are the switches. One feature not found in many other trucks is the large handrail for passengers to hold onto when the Tatra 8×8 gets into off-road severe going.
The Tatra T815 8×8 utilises the company’s 12.7-litres T3D-928 Euro-5 air-cooled V8 diesel engine, producing 325kW (435hp) and 2100Nm (1550lb/ft) torque. The engine uses a turbocharger and charge-air cooler positioned directly above the engine. In addition, it is equipped with a mechanically controlled direct in-line injection pump. With a cylinder spacing angle of 90°, it features other unique technical solutions, including a ‘rollable’ mounted crankshaft bolted from the individual segments.
The advantage of the Tatra engines is the absence of complex electronic control and easy maintenance and serviceability.
The Tatra V8 draws external air via the front of the cabin through a shrouded multi-blade fan, which is then split to flow between the finned cylinders and the centre of the block valley. As a result, almost two-thirds of the air exits from the top of the engine compartment. Meanwhile, the rest of the air gets forced down around the cylinders. The system keeps the engine in its most efficient combustion zone and minimises heat soak when the truck is at rest. As a result, the cabs are cooler and air-conditioning units more effective.
The engine drives through an Allison 4500 six-speed automatic transmission with double PTO outlets. Tatra’s own 2.30TRK two-speed static shift auxiliary gearbox provides the deep reduction. Instead of the usual engine retarder, a Telma electric FN83-00 retarding unit is located at the rear of the chassis and provides a staggering 3000Nm (2212lb/ft) of retardation.
According to the manufacturer, Tatra trucks employ a unique chassis concept that originated in the early 1920s and has not yet been rivalled. The main principle uses a central load-carrying tube and axles with independently suspended swinging half-axles bolted into a single unit.
The Tatra’s chassis is an enclosed box section that houses most wiring and airlines. The chassis is then solidly mounted to a central tubular core, containing a straight tail shaft. As the chassis is modular, sections can be added or removed without the usual metal cutting. You can add a drive, a lazy or a drive/steer, building the capability and capacity of your Tatra to suit your load profile. All drive axles are swinging half axles with air bellows and springs added on the rear axle sets. Telescopic dampers and stabiliser bars are standard on the T815.
The Tatra-designed independent half-axle suspension is simple but effective. Each axle gets cushioned by a coil spring enclosed in air bellows, mounted on the top of the axle housing and secured to the centrally mounted tubular chassis. In addition, this T815 has the optional multi-leaf steel spring, which is used on a bogie axle arrangement when the application demands ultra-heavy-duty use.
The bellow air supply is mechanically controlled by the load and axle position, maintaining spring frequency no matter the load on the individual wheel. Consequently, as a result, when the truck moves over rough terrain and a wheel drops into a pothole, it does not affect the wheel on the opposite side of the truck. The chassis is insulated against twisting moments, and the load is protected. Additionally, both wheels are in complete contact with the surface, maximising traction. Axle differentials, inter-axle differentials and reduction hubs complete a formidable traction formula.
Tatra axles are constantly driven and equipped with locks in their basic version. A pair of driven crown wheels (one per half-axle) and a pair of pinions transmitting torque from the differential are placed in the axle housing. The differential is placed outside the axle in the central load-carrying tube. Unlike classic axle solutions with a bevel differential, it is a so-called crown or cylinder-type differential. The inner space of the housing is adapted for the swinging motion of the half-axles.
It’s indeed easy to understand why the Tatra T815 8×8 is sought after by forestry and mining operators with its purpose-built off-road design features. Some might say the Tatra T815 is a bulletproof truck, and we hope to find that out when we head up the bush to see this one working in its new forestry operation roll.
Read more
The sale is on!
0 Comments7 Minutes
Running north
0 Comments13 Minutes
Changing the Game
0 Comments10 Minutes