50% reduction in powertrain cost to drive surge in electric light commercial vehicles
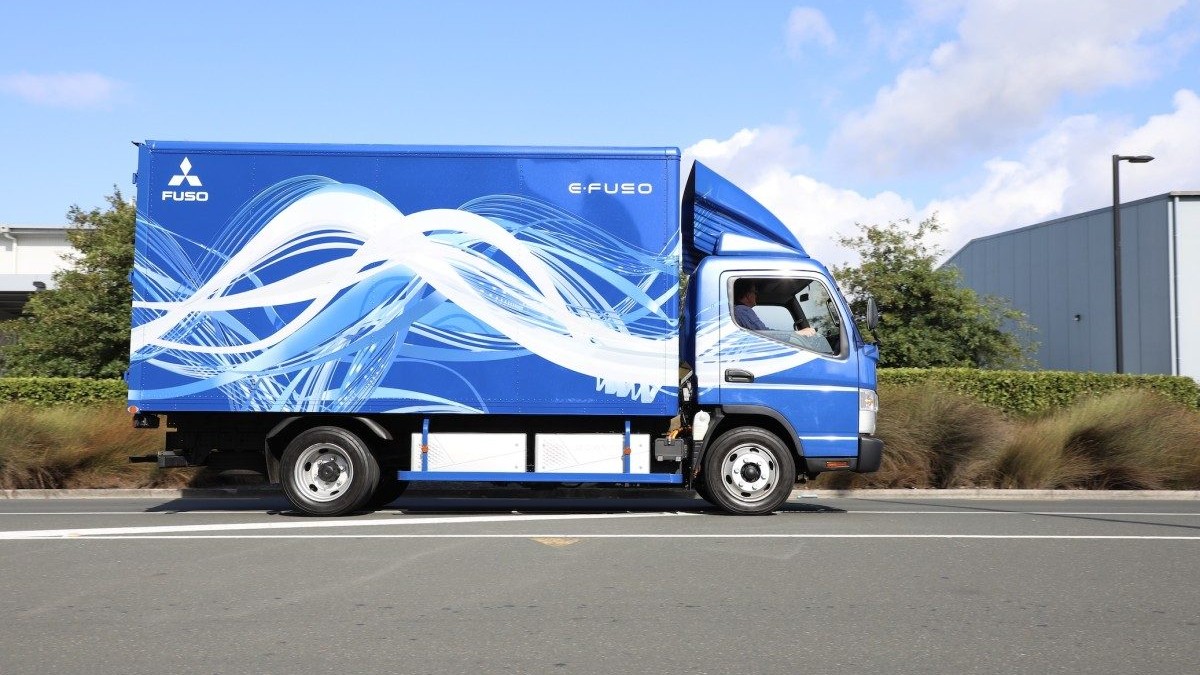
The powertrain cost per vehicle for all truck and bus vehicle types will see a significant decline over the next eight years, according to new research from Interact Analysis.
In 2021, the average cost of the powertrain for an electric light duty truck was more than US$9,000. By 2030, it will be 56% lower, at just over US$5,000.
Shirly Zhu, principal analyst at Interact Analysis, said the sale of electrified trucks and buses is forecast to maintain momentum in Asia Pacific out to 2030.
“According to our global electrified and hybrid bus and truck report, sales of electric light-duty vehicles (including utility) will register a 44% CAGR from 2021 to 2030, reaching nearly 600,000 units per year. This will drive increasing demand for powertrain components, forcing down the price of components,” she said.
Zhu said OEMs and component manufacturers are focusing on solutions that help to reduce the cost of powertrain components.
“This is crucial in order to narrow the price gap between electrified and traditional ICE vehicles,” she said.
Some of the current product trends include:
Direct drives are being replaced by indirect drives
Direct drive solutions are currently widely used for urban buses. In China, this solution used to dominate light-duty trucks because of its advantages of simple structure and easy maintenance. More recently, direct drive solutions are being replaced by indirect drive solutions with a single-speed transmission. These systems are much more reliable and economical.
Many products used in the powertrains of electric vehicles can be integrated, such as e-axles. This makes components more compact and reduces the overall number of components required. The result is reduced costs, especially as production ramps up. Integrated e-axles are particularly popular for light-duty vehicles in China, making their price highly competitive.
Market competition
As a result of booming market demand, more and more component suppliers are being drawn into the EV segment; especially suppliers of those components that have low barriers to entry. This is further intensifying downward pressure on the price of powertrain components.
“Between 2021 and 2022, in the wake of the current economic and supply chain crisis, the price of powertrain components has increased because of escalating raw material costs,” said Zhu.
“The result is that many suppliers are announcing price rises. For example, motor price per kW increased by 4% in 2021, and this will rise by another 14% in 2022. Secondly, the rapid price decline of batteries per kWh in recent years has reversed from the second half of 2021 and we expect to see a price increase in 2022 of around 8% per kWh.”
According to the research, some suppliers have higher bargaining power with relation to automobile OEMs.
“Battery and motor vendors tend to be considered as tier 1 suppliers and therefore are in a strong position to negotiate prices,” said Zhu.
“But, for suppliers of smaller components such as DC-DC’s, it is much more difficult. They have much less bargaining power and it is therefore harder for them to impose price increases whilst remaining competitive.”
Overall, the market for components within electric trucks and buses will undergo rapid change over the next eight years. By 2030, pricing will look very different because of increased demand and changes in the economic world.
Currently, light duty trucks remain the most competitive segment, and will play a significant role in forcing down component costs going forward, particularly in China.